Overcoming energy management challenges
This manufacturer is already a global leader in sustainable stainless, low-CO
2 steel, and because sustainability is a core priority for them, the corporate headquarters challenged this US-based site to reduce energy consumption further by 10% within two years. But the US team had a problem: how could they reduce energy use if they did not have full visibility over their current energy consumption? They had the basic information like which processes were their main consumers, but they wanted a deeper understanding of energy patterns. They needed more data, and they needed to be able to visualize and analyze that data to make intelligent decisions.
When the energy reduction mandate came down from corporate, this site already had an energy management system from a third-party vendor in place. However, instead of just solving their problems, this system introduced additional challenges for the team. For example, any time the client wanted to create a custom report on their energy data, they had to contact the vendor’s support team to build a new report, which meant they were charged support hours for every custom report. Additionally, the system could not report on KPIs like CO
2 produced per ton of steel. They needed a flexible, intuitive solution that they could manipulate to make custom reports easily on their own and that would also go beyond typical energy management by monitoring emissions and production data.
So, the US manufacturing site knew they needed a new energy management system, and they wanted more capabilities than their current solution could offer. The site leaders turned to a sister plant in Europe – one of the company’s sites in Europe had been using the ABB Ability
Energy Management System for many years and recommended the system to their American counterparts. The Americans decided to enlist ABB for their energy management needs. Not only would this allow them to leverage the pre-existing relationships and expertise of the European team, but also, choosing ABB would allow the company to start benchmarking energy performance across the sites globally from one platform.
Benefits of a flexible, intuitive Energy Management solution
Thus, ABB was contracted to deliver the Monitoring and Reporting module of the ABB Ability Energy Management System at the US site, which not only monitors traditional energy data, such as electricity and gas, but can also track environmental data points like production-derived carbon emissions. By reading flow meters and energy meters on circuit breakers, ABB Ability Energy Management System is able to provide visibility over hundreds of process areas, sub-areas, and pieces of equipment to get a granular view of electricity and natural gas consumption.
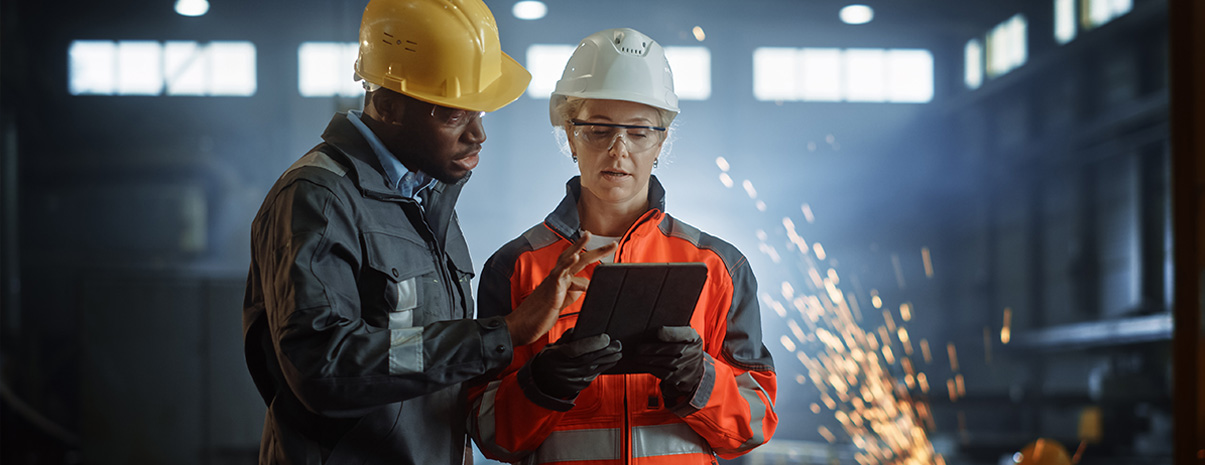
And do you want to know this manufacturer’s favorite feature of the ABB Ability Energy Management System? When integrated with production data, the ABB Ability Energy Management System tracks MWh per ton of steel and CO
2 per ton of steel which allows them to decipher which product grades are most energy and emissions intensive. They now have a richer understanding of their energy consumption patterns and how energy use corresponds to production.
This steel manufacturer has high expectations for the solution. Of the 10% energy reduction target, they expect 1-1.5% of energy savings to be attributed to the ABB Ability Energy Management System alone – they anticipate improved efficiency simply by virtue of the fact that the energy management system can help with better decision-making. The rest of the 10% will come from other improvements such as upgrading to more efficient motors and lighting systems.
Expanding the solution for enhanced efficiency
Looking to the future, this steel manufacturer is already implementing the ABB Ability Energy Management System at another site in North America, which will be online later in 2024. Additionally, now that the ABB Ability Energy Management System has revealed when their production is most energy and emissions intensive, they are beginning to explore next steps with the ABB team such as adding Forecasting, Planning, and Optimization capabilities, which would help them to design and optimize production schedules to minimize energy consumption, carbon emissions, and total energy cost.