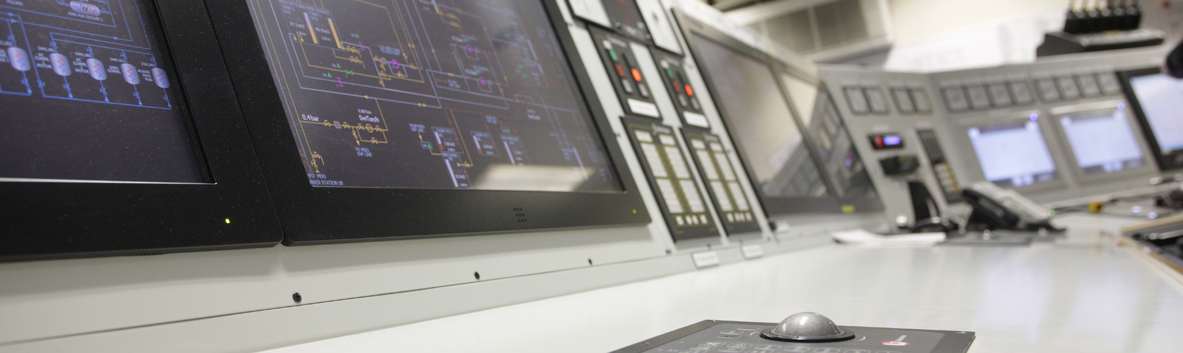
Many cost and operational benefits – such as reduced footprint, better use of space, lower product costs, as well as a more efficient engineering, commissioning and operation of the ship – could be found in a more efficient integration of the systems. However, these benefits are often lost due to the complex engineering needed to integrate the different systems and components.
Complexity is due to the various communication protocols, fieldbuses, speed requirements and unconnected tools used to manage the information. Information is therefore typically mostly exchanged via hardwired signals or through slow serial lines – and often limited to the signals absolutely necessary for the operation.
Another reason for the slow introduction of totally integrated systems is conservative class rules that have favored traditional technology. With an increasing understanding of the reliability benefits, and with new technologies securing a segmented and autonomous operation, recent additions to the class rules now allow systems to reap the benefits of total integration.
Some of the challenges, as well as the benefits and opportunities of a totally integrated solution will be discussed below. In addition, some solutions from ABB that provide total integration possibilities from the intelligent device level all the way up to the operator in the control room will be presented.
Horizontal and vertical integration
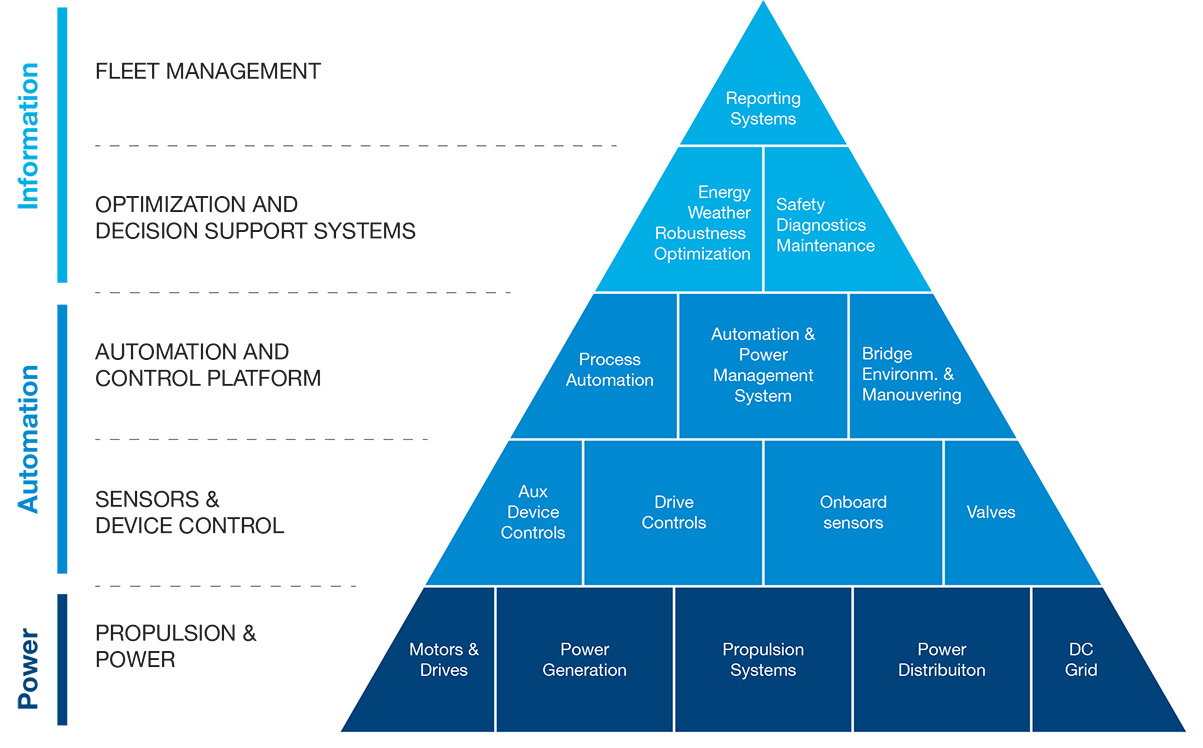
The complete power and automation solutions in a ship are depicted in Figure 1. The various systems, from propulsion and power systems up to fleet management systems, form a hierarchical structure. The main and most important parts are related to power generation, distribution and consumption (in the form of, for example, pumps, fans and propulsion motors) that all are essential systems for ship operation. Automation, found on the next level of the hierarchy, is used to manage the power systems. Automation systems with monitoring and control functionalities, as well as associated sensors, actuators and drive controls, operate the power systems in a safe and efficient way. Finally, at the highest level of the hierarchy, information, optimization and various fleet management functions can be found. These systems provide help and advise personnel on board and on shore on the best and most efficient ways to operate, service and manage the ship.
Today, what is commonly considered an integrated system on a ship is often the Integrated Automation System (IAS), which in practice is only one part of the automation layer in Figure 1. Typically, IAS solutions are based on so-called Distributed Control Systems (DCS) that are suitable for large and distributed automation applications. While originating from the process industry, a number of manufacturers have entered the marine market with DCS based IAS solutions, and today DCS technology is a mainstream solution for large ship installation.
An IAS system does, however, only address the so-called horizontal integration within the automation and control layer. That alone does not offer many cost benefits. For this, deeper and wider integration is needed. A higher and more profound degree of integration means using vertical integration between the layers – this implies the use of intelligent devices and embedded controls to achieve cost efficiency.
ABB is a global actor and forerunner in the development of vertically integrated solutions. Research and development activities in many industries with a high demand on reliability, transparency and diagnostics have built a wide portfolio of vertically integrated products and solutions. This allows us to illustrate the possibilities with some real-world examples of total integration.
From integrated automation to total integration
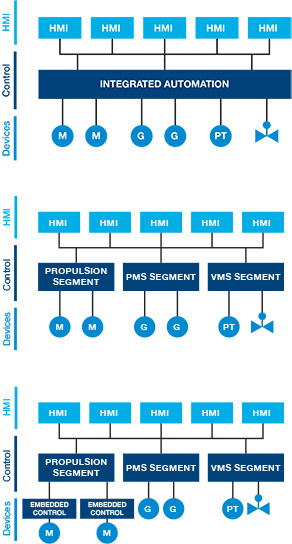
In a totally integrated solution, bus communication and embedding of intelligence are key elements in achieving higher cost efficiency. The main difference, when compared with integrated automation systems, is that in totally integrated systems, the integration of intelligence is not limited to the automation layer alone but distributed on all levels in the system hierarchy. In the ABB Totally Integrated Solution, information is also transparently transferred between all system layers, and the system interfaces at all levels are well defined to ensure compatibility, efficient engineering and optimal utilization of information.
Integration can also be done in several ways. While hypothetically total integration, as in Figure 2, could be the most cost efficient solution, several drawbacks limit its applicability. Instead, modularization and requirements on an autonomous operation favor a segmented integration model. A segmented integration model allows a high redundancy, independent and autonomous operation and secures high availability. In addition, there is more flexibility in scope from a stand-alone product to a totally integrated system. More embedded solutions are also being used and developed, allowing for an even higher reduction in footprint and installation time. Significant cost savings can be gained from integrated system architecture, modern fieldbus technology, distributed intelligence and system-wide configuration tools.
In the fully integrated architecture, redundancy ensures the automation system has high availability, and all signals and systems are connected to the integrated system. It is:
- Cost efficient
- Transparent
- Non-autonomous
- Difficult to modularize
- Characterized by complex engineering
In a segmented integration, similar integration as in a fully integrated architecture can be achieved, but with the difference that various functionalities can be separated to different segments. It is:
- Cost efficient
- Autonomous
- Modular
- With a slightly higher hardware cost
Segmented integration can also be extended with intelligent devices – embedded controls that further reduce the complexity on the automation level. It offers:
- Same benefits as segmented automation
- Reduced footprint
- Reduced hardwired IO
- Increased factory test coverage
Figures 3 and 4, of traditional and total integration clearly show their differences. Some of the most significant technologies in Figure 4 will be explained below.
Image currently unavailable
Image currently unavailable
Image currently unavailable
Image currently unavailable
Image currently unavailable
Image currently unavailable
Figure 3 Traditional "integration" Figure 4 Total integration
The ABB 800xA extended automation system
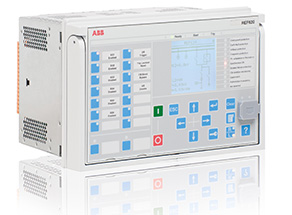
One of the cornerstones of the ABB Totally Integrated Solution is the ABB 800xA extended automation system. The 800xA system is a true and proven DCS solution that not only provides DCS control, but is highly flexible and capable of consolidating, monitoring and controlling all aspects of the Totally Integrated Solution. This is largely due to the high extendibility of the 800xA system, which seamlessly integrates the electrical systems with its IEC 61850 communication, drives and field devices, but also allows embedding segments of the system to, for example, propulsion controls. The 800xA system also integrates with regard to asset management, remote diagnostic and ERP systems.
A smart segmented architecture allows the control hardware to be optimally allocated in order to reduce the footprint, to optimize functionality and to meet requirements on redundancy and autonomous operation in a reliable and cost efficient way.
The 800xA system also supports transparent time stamping and time synchronization across the whole vertically integrated system. The transparent time synchronization avoids typical problems where different integrated systems may independently support accurate time stamping, but where a lack of transparent and accurate time synchronization cancels out the benefits of the time stamping.
As the space on the bridge and in the ECR is limited, other 800xA system features are also useful for multi-function displays and, for example, video integration capabilities, allowing a reduction in number of stand-alone workstations, monitors and dedicated equipment and access to total system information from any connected workstation.
The 800xA based ABB IAS libraries also provide core VMS, PMS, ESD, as well as HVAC control functionality, seamlessly integrating to power distribution, propulsion, remote control and asset management functions as needed.
Benefits of the 800xA system include:
- Platform with native support for vertical integration
- Reduced footprint for hardware and cabinets through optimal use of controllers and reduced hardwired IO
- Supports space efficient PMS integration in switchboards
- Reduced bridge and control room footprint through multi-functional workstations with access to all system information
- Easy and cost efficient commissioning with access to total system from any one workstation
- Reduced ECR footprint, with multi-functional video walls replacing expensive mosaic walls, CCTV integration, etc
- Improved functionality for, for example, black-out prevention, with full system information available
ABB MNS iS bus-based low voltage switchboards and motor controllers
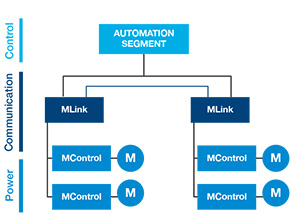
As in medium voltage switchboards, where intelligent protection relays have drastically reduced the need for hardwired interconnections and simplified the integrations to automation and PMS systems, similar vertical integration solutions exist for low voltage distribution. With a fully embedded intelligence at breaker and motor controller level, and transparent communication with the higher-level automation systems, substantial benefits can be achieved.
ABB’s innovative MNS iS concept combines the long-term experience, energy efficiency, grid reliability and industrial productivity of the well-known MNS system with advanced design in hardware and software technologies. Compared with non-native bus-based integration of the LV distribution and motor control, where significant delays may be introduced, the MNS iS solution allows for fast control, interlocking and time stamping at the device level.
The MNS iS solution also provides exceptional operational safety with physical separation of the power and control parts of the switchgear.
The MNS iS system is widely scalable and flexible, as standard power modules cover a wide range of motor starter and energy distribution applications. The associated control module is scalable from basic to complex motor starter types, protection functions and field input/output signal requirements, depending on the application. All starter level interlocking schemes between control and power modules are built in. No hardwiring or input/output assignment required. The control schematic is reduced to assigning field I/O signal contacts only.
The typical hardwired control interfaces between the IAS system and single starters are replaced by an interface module MLink, which serves as the gateway between the IAS system and individual feeders/starters via the internal bus of the MNS iS switchgear. The MLink solution not only supports IAS integration, but also time synchronization, accurate time stamping of events and alarms, integrated alarm handling as well as asset monitoring.
Benefits of the ABB MNS iS low voltage switchboards and motor controllers include:
- Reduced footprint with less physical IO
- Increased flexibility during commissioning and the life cycle
- Improved diagnostics and preventive maintenance
- Fast fault tracing
- Reduced cabling and engineering
Drives integration
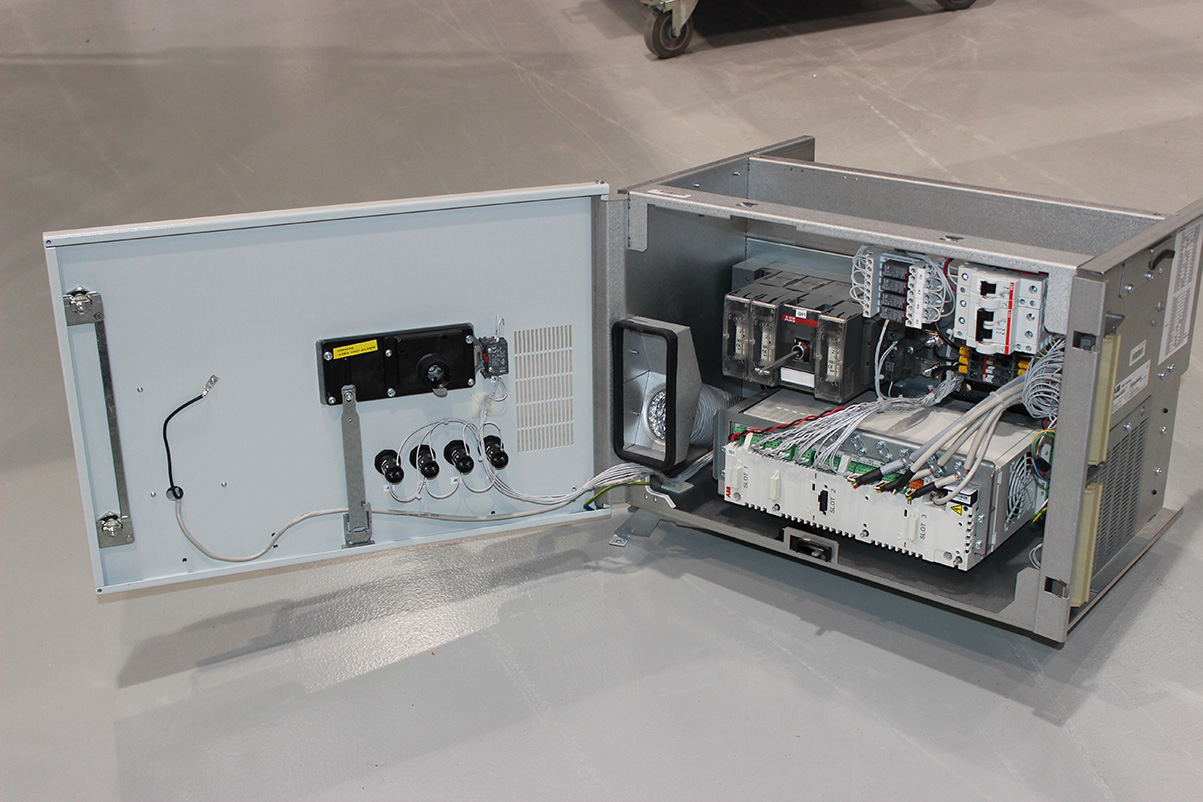
The use of variable speed drives (VSD), which are frequency converters, instead of single-speed motors with throttle control is an increasing trend in shipboard installations, as the cost of energy has become a major factor in the economic planning of shipping companies.
The most common engineering approach is to simply place a VSD between the supplying switchboard and electric motor. Typically, this causes disadvantages and challenges, such as:
– VSD are wall mounted as loose units or floor mounted in drive cabinets, which increases the installation footprint.
– Power cables and cabling accessories are required for interconnecting the switchgear and the VSD.
– The solution requires extensive coordination among vendors.
Instead of additional cabling and interfaces of separate VSD installations, the integration of drives into either switchgear or driven equipment brings the benefits of the smart motor control centers combined with the energy saving potential of the VSD.
ABB ACS 800/850/880 drives can be integrated into the MNS low voltage switchboard. Lower power units may be built into a withdrawable module, while higher power units are installed as fixed units into the MNS switchboard. This solution ensures the following savings at every stage of the product lifecycle:
– No more field wiring between feeder and VSD.
– No more wall mounted or standalone VSD panels, which is more flexible and optimizes of the room layout.
– One vendor handles the complete solutions, which saves hours in the design engineering and project management.
– The standardized design enables shorter engineering and delivery times.
– The integrated solution can be routinely tested at the factory prior to delivery.
– The standardized design saves on the spare parts inventory.
– Energy savings due to variable speed operation of pumps, fans, etc.
ABB Embedded Azipod® controls
While the Azipod propulsion system represents the ultimate solution in flexibility and energy efficiency, new control solutions aiming for a more optimized fit bring further space and cost benefits. With a design based on the 800xA platform, the new Azipod solutions are introducing products fully adapted to the segmented integration model. The new design allows for a reduction of control electronics by approximately 30 to 50 percent, and a reduction of footprint for the control cabinets of up to 70 percent. In addition, seamless integration into the 800xA IAS system, with a minimum of interfaces, allows for full monitoring and control of the propulsion system from the IAS system multifunctional displays. Full autonomous and stand-alone operation is still possible where needed.
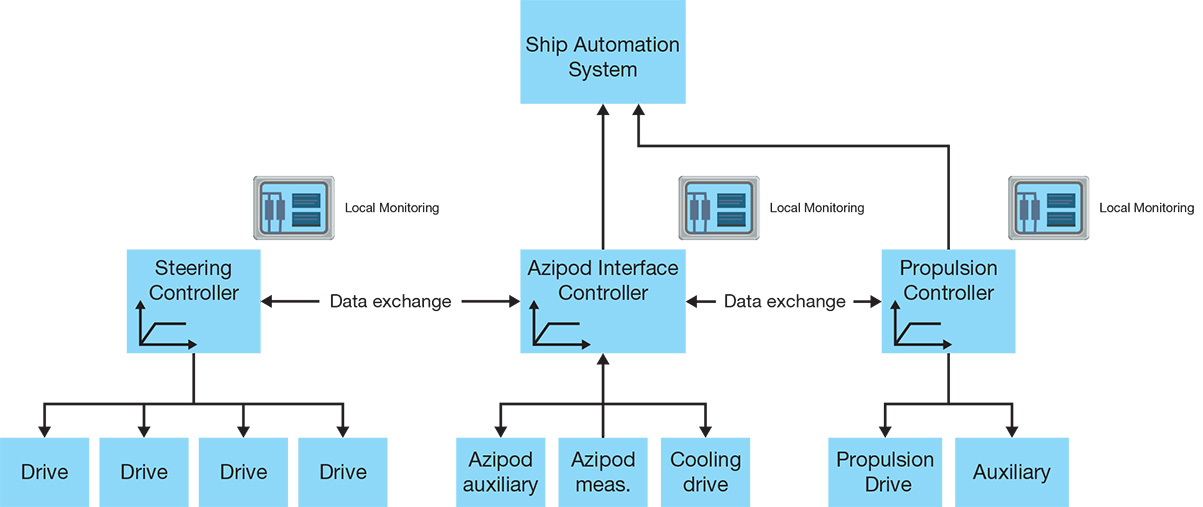
The differences in design between the traditional and new Azipod topology are illustrated in Figure 7 and Figure 8. In the traditional topology, the Azipod controls are separate, with largely hardwired connections between each system. While providing independence between the systems, the new segmented solution provides even higher reliability and full autonomy as it reduces the number of potential system damages and failures.
In the new topology, vertical integration with smart VFDs and starters is also deployed within the Azipod segment, creating a large standardized hybrid component. It seamlessly integrates into the IAS system, provides accurate time stamping and transparent diagnostics and improved network stability.With a reduced number of interconnections between the different Azipod controllers, full factory testing of the complete propulsion system is possible, reducing installation and commissioning work on site.
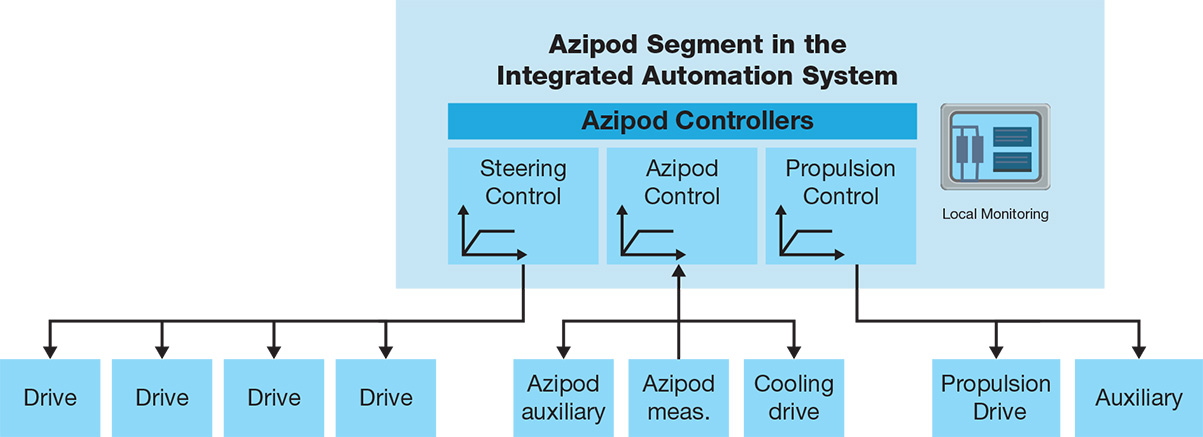
ABB Information Solutions
Due to the increasing costs of fuel and crew, decision support solutions are becoming more mainstream in shipbuilding. While it is possible to build an extensive decision support system based on components available on the market, the cost of integration, and the cost of potentially doubling hardware easily increases the overall price factor. With the ABB Information Solutions, the same hardware platform, sensors, workstations and information are used throughout the system, and correct information is provided in the right place at the right time. With the information available in the integrated system, no additional monitors or workstations are needed. Instead, the advice is available directly from the same multifunction displays, in affected process mimics – providing the best efficiency and user experience. As all information in the system is also available for fleet management, transparency down to the lowest level is provided for onshore personnel.
Benefits of the new topology include:
– Significantly reduced footprint, both for control hardware and in the control room
– Sequence of events and millisecond time stamping of all essential events on board
– Improved blackout prevention and load shedding
– Simplified commissioning and full system validation before installation
– Improved diagnostics, preventive maintenance
Benefits of ABB Information Solutions include:
– Less integration costs
– Reduced hardware and footprint
– Simplified commissioning and full system validation before installation
– Improved diagnostics, preventive maintenance
ABB Extended Operator Workplace
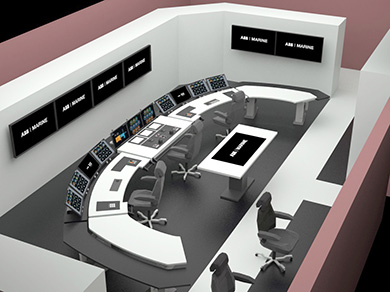
While with the concept of integration is often conceived as the interconnection of various devices through hardwired or bus-based signals, an aspect of integration not often considered is the interaction between the automation system and human operator. With the focus on operator efficiency and safe operation, ABB has recently introduced the Extended Operator Workplace (EOW) concept. The ABB EOW concept involves an ergonomic and performance-enhancing environment that facilitates safe, fast and correct operator decision making. This leads to measurable improvements in operator efficiency, safety, information exchange and operator job satisfaction.
With ready-made solutions for efficient control and bridge environments, ABB can provide cost-efficient solutions that make best of the Totally Integrated Solution. Technologies such as video integration in with separate CCTV systems, large-screen support instead of mosaic walls and integrated communication, are highly cost efficient.
The ABB Project Management and System Integration
The individual ABB products, when deployed in a coordinated and integrated fashion, provide clear cost benefits. However, there is another benefit to the ABB Totally Integrated Solution related to the engineering and commissioning activities required during ship design and manufacturing. Using one system supplier for the central parts of the ship systems – the power generation, distribution, propulsion, automation and control – reduces the burden on the yard in the following ways:
– Less need for system integration will not only introduce savings during the engineering phase, but also reduce risks during commissioning, because the integration is thoroughly validated by the system supplier. A single system supplier will also reduce the need for integration meetings, allowing yard engineers to focus on customer requirements and project control.
– There will be less need for FAT testing as larger units and systems can be tested and validated together, for example, validation of the main switchboard and the PMS system at the same time.
– As the total solution and all its interfaces will have been verified by the manufacturer, the testing time during commissioning will be minimized, and the number of required modifications and corrections during commissioning reduced.
– Transparent access to full ship information from the multifunctional displays will ensure faster and easier system testing.
– One ABB site manager coordinating all essential systems on site will ensure efficient commissioning and communication.
– Common competences and parts allow the flexible use of resources and spares during commissioning and operation.
Providing the customer with better and more cost efficient solutions is the ultimate goal of a totally integrated solution. However, there are challenges in achieving higher cost efficiency with a purely horizontal integration, while as the real-world examples in this article show, vertical integration provides tangible cost savings.
Benefits of the EOW include:
– Increased safety and operator efficiency
– Cost efficient solutions for the entire control room
– Optimum integration of the ABB 800xA operator efficiency features
Notes
[1] ABB review, Special report on IEC 61850