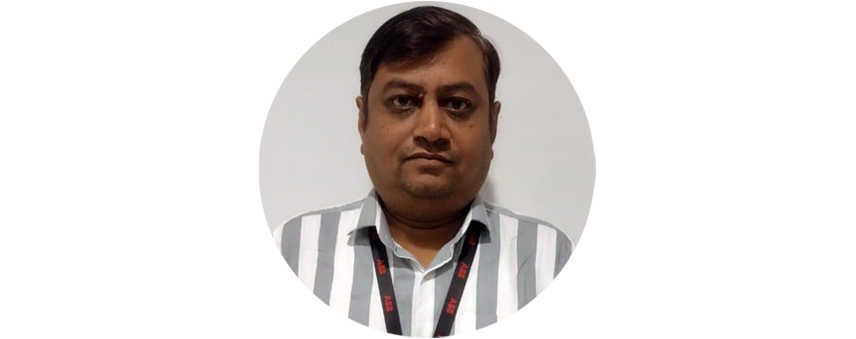
Introduction
In the intricate landscape of paper manufacturing, efficient production planning and scheduling play a pivotal role. Paper machine order scheduling, capacity utilization, and on-time order deliveries cause significant impacts on profitability. Achieving high efficiency in machine scheduling is difficult due to widely varying parameters and complexity.
ABB, a global technology leader, offers a robust solution tailored specifically for the pulp and paper industry. The Production Planning and Scheduling (PPS) module within ABB Ability™ Manufacturing Execution System (MES) for Pulp and Paper empowers mills to optimize resources, meet customer demands, and ensure timely delivery. Within the PPS module, the trim optimization function plays a critical role in production planning and scheduling addressing the optimization of trim loss during the paper manufacturing process.
During production, paper rolls are cut into smaller rolls or sheets based on customer orders. While the trim algorithm analyzes various factors, including roll width, order specifications, machine constraints (e.g., blade width, cutting speed), and existing trim patterns (in case of retrim). Leveraging ABB algorithms, the system determines the optimal cutting patterns to minimize trim loss. It dynamically adjusts the cutting plan based on real-time data (e.g., machine breakdowns, order changes) and considering multi-stage trim problems.
The PPS module provides real-time information for optimal trim decisions to minimize waste during the paper trimming process. By optimizing cutting patterns, PPS reduces trim loss, leading to cost savings in raw materials. Through efficient trimming, organizations can ensure that the maximum usable area of the paper is utilized.
Tailored for the pulp and paper industry, the PPS module provides key capabilities including:
1. Optimal Real-Time Planning:
- Simplifies real-time planning and scheduling of production blocks, runs, and orders.
- Streamlines the allocation of machine time for single or multiple machines/mills.
2. Profitable-to-Promise Function:
- Instantly checks real-time machine availability, capacity, and projected profitability of potential orders.
- Ensures production plans align with profitability goals.
3. Accurate Timing Information:
- Full reports on order backlog, late orders, and other critical metrics are available.
- Dynamic visual interfaces display clear pulp balance curve graphs, helping find the optimal balance between production and consumption.
4. Efficient Allocation:
- The finishing machine optimizer assists in allocating orders more efficiently.
- Factors considered include changeover times, capacity constraints, and other relevant parameters.
5. Efficient Resource Utilization:
- Ensures that available resources (such as raw materials, machinery, and energy) are optimally utilized.
- Aligns production activities with resource availability, minimizing idle time and maximizing productivity.
6. Meeting Customer Demands:
- Timely production and delivery of paper products.
- Improves customer satisfaction and maintains business relationships.
- Produce and deliver orders on time, enhancing customer satisfaction.
7. Cost Optimization:
- Reduce waste, minimizes downtime, and streamlines processes
- Avoid overproduction or underproduction.
- Precise timing and cost information are incorporated into the planning process.
- Reduce complexity and streamline production planning and scheduling.
8. Quality Control:
- Well-planned production schedules allow for quality checks at each stage.
- Ensures consistent quality and maintains the reputation of the paper mill.
9. Inventory Management:
- Maintain optimal inventory levels.
- Ensure timely replenishment, avoiding stockouts or excess inventory.
10. Waste Reduction:
- The system minimizes trim waste at winder as well as on downstream finishing machine like Sheeter, coater and rewinders.
- Reduced Waste: By optimizing trim patterns, retrimming minimizes material waste.
- Cost Savings: Less waste translates to cost savings in raw materials.
- Improved Efficiency: Efficient retrimming ensures smooth production flow and reduces downtime.
- Higher Yield: Maximizing usable paper area leads to higher yield per roll.
11. Minimizing Changeovers:
- Effective scheduling minimizes changeover times between different paper grades or products.
- Reduced changeovers enhance overall efficiency.
12. Adaptability to Market Changes:
- Dynamic planning and scheduling allow quick adjustments to changing market demands.
- Flexibility ensures the paper mill can respond to unforeseen events or shifts in customer preferences.
13. Rapid Production Plans:
- ABB’s solution enables planners to create optimum production plans swiftly.
- Tool generates the multiple solution faster for complex trim problems.
14. Resource Allocation for Maintenance:
- Scheduled maintenance downtime can be planned to minimize production disruptions.
- Proper allocation of resources ensures smooth maintenance activities.
15. What-If Scenario Analysis
Users can explore ‘What-If’ scenarios within the system:
- Assess the impact of planning and scheduling changes on production times.
- Evaluate profitability implications.
- Anticipate potential order delays.
16. Integration with Other ABB MES Applications
The Production Planning module seamlessly integrates with other ABB MES applications for pulp and paper like Order Management, Production tracking. Quality data Management, Warehouse Management, Recipe Management and Diary.
17. Scalability and Modular Design:
- Highly scalable and modular, it caters to the advanced needs of the pulp and paper industry.
- From production allocation to trim scheduling, it provides world-class tools for planners.
18. Integration with ERP Systems:
- Integrating trimming software with ERP (Enterprise Resource Planning) systems enhances overall process management.
- ERP systems provide real-time data exchange between suppliers, customers, and internal departments.
- Effective supply chain management complements trimming efficiency.
Conclusion
In summary, planning and scheduling play a crucial role in optimizing production, reducing costs, and maintaining competitiveness in the paper industry. ABB’s modular and flexible PPS MES applications cater specifically to the pulp and paper industry from last 3 decades. By leveraging ABB Ability MES for Pulp an Paper, mills can achieve new levels of operational efficiency and transform their production processes.