Morten Stakkeland, Data Scientist, ABB Marine & Ports
With eight ABB Ability™ Collaborative Operations Centers, ABB Marine & Ports delivers world-class support to customers worldwide. Now, its artificial intelligence (AI) training is combining data and machine learning with skills that only experienced engineers can pass on.
From locations in Europe, Asia and the Americas, ABB experts monitor shipboard systems, coordinate equipment diagnostics and offer maintenance services around the clock. In addition to providing a single point of contact through ‘24/7 care’ approach, ABB’s international centers share data so that staff can access the same information – and provide the same level of support – regardless of their location. Moreover, engineers can retrieve real-time data to help with resolving onboard issues or identifying anomalies before they become faults.
Artificial intelligence at sea
There are significant benefits in using AI in marine diagnostics and maintenance. The technology optimizes condition monitoring and, as a consequence, reduces the burden on crew members and engineers. The resulting increase in system reliability – and therefore also vessel performance – also improves safety.
It is clear, then, why shipping is ready to adopt AI on a larger scale – and its progress in the industry is being driven by several key factors.
For instance, machine learning techniques have advanced considerably in recent years, and software allowing these novel methods to be applied to industrial datasets is now more widely available. Just as significant are the wider availability of historical data and the presence of a digital infrastructure that allows information to be collected from vessels and stored in the cloud at a relatively low cost.
ABB is playing a key part in this development. Its ‘Electric. Digital. Connected.’ strategy encompasses every element in the digital ecosystem, facilitating the collection of data from connected machines and devices onboard ship as well as its secure storage in the cloud.
Learning from the past
Using past data to prepare algorithms for a specific purpose is fundamental to modern machine learning methods. An example of this practice in the maritime sector is predictive maintenance, in which past maintenance data combined with operational and failure data is used to develop a condition-based approach able to predict malfunctions ahead of time.
Yet while historical data is undoubtedly crucial to machine learning, human input is equally important. Engineers – who for the past decade have been using the data to provide services like diagnostics, fault detection and troubleshooting – possess insight into customer equipment and systems that cannot be gleaned from data alone.
Against this background, ABB is developing interfaces to enable engineers to ‘train’ machine-learning algorithms. Enhanced by the unique insight of experienced professionals, the resultant AI systems will provide faster, more reliable service to customers throughout the sector.
Labelling data for supervised machine learning
Support engineers spend much of their time assisting customers whose operations have been disrupted by system or component failure. In such cases, the engineer assigned to the task will often manually download and inspect measurements and data from the relevant systems or subsystems to pinpoint the root cause and propose an appropriate solution.
As part of this process, he or she classifies the incident or fault. The dataset concerning a fault may consist of categorical data in the form of alarm lists, measurements from shipboard sensors and text-based information in the form of service reports or communication between the support team and crew.
Unlike unsupervised machine learning, in which little or nothing is known about the data, supervised machine learning relies on the data being clearly and accurately labelled. Figure 1 provides an overview of the process.
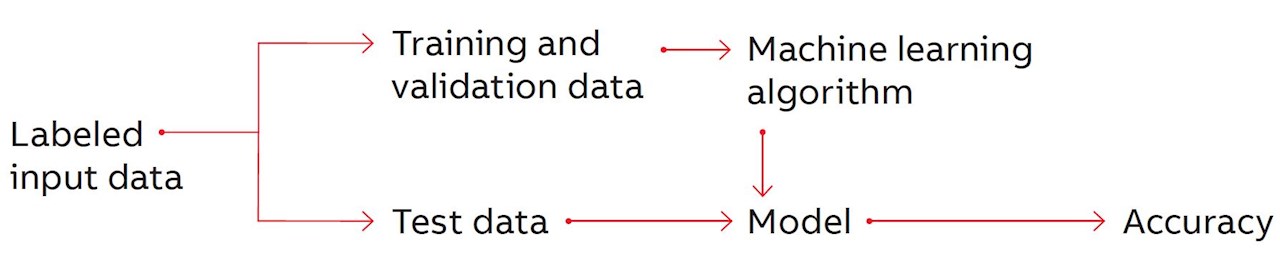
The labelled input data is frequently divided into training/validation datasets and test datasets, which are used to prepare and verify the machine-learning algorithm. The algorithm selected depends on the application and the available dataset.
In the case of fault diagnostics in complex marine systems, a classification algorithm is employed. The underlying engine used to train the classifier varies depending on the dataset, but the training and testing process, as well as the deployment of the trained model into a production system, can all be integrated into the ABB Ability™ ecosystem.
Interaction with algorithms
Unsupervised algorithms cannot learn structure from labelled data, and instead have to identify that structure independently.
In cooperation with researchers from the University of Oslo, Norway, and as part of the BigInsight research project where ABB is a funding and contributing partner, ABB has developed an unsupervised system that takes output from marine systems and finds structure or clusters in the unlabeled dataset. The algorithm is based on advanced Bayesian statistical methods, accounting for the fact that datasets collected from marine applications do not constitute ‘big data’ on the scale of other industries such as the consumer applications market.
Each of the structures corresponds to a mode of operation of the equipment, including fault or failure modes. However, for these results to be useful, domain knowledge is needed to accurately recognize and name the various clusters or operational modes. An overview of the methodology is shown in Figure 2.
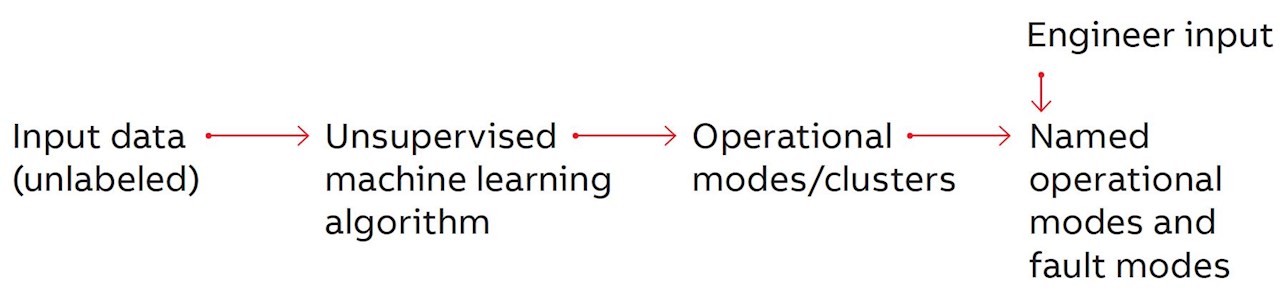
The developed model allows engineers to manually edit the cluster. For example, for a given fault class, an engineer may decide that a certain alarm or message delivered by the system is irrelevant and should not be considered as an indication by the algorithm.
The methodology will be applied to automated diagnostics and fault detection for complex marine systems. It will be integrated into the digital service offering and support onsite engineers in their maintenance work.
Combined power of human and machine
ABB is augmenting its support and troubleshooting services not by replacing human staff with AI, but by developing systems that combine the benefits of data and machine learning with skills and knowledge that only experienced engineers can offer. The more input the experts provide, the more intelligent the systems will become. This will ultimately improve the level of service provided to the customer, increase vessel efficiency, and make maintenance work easier and safer for the engineer.
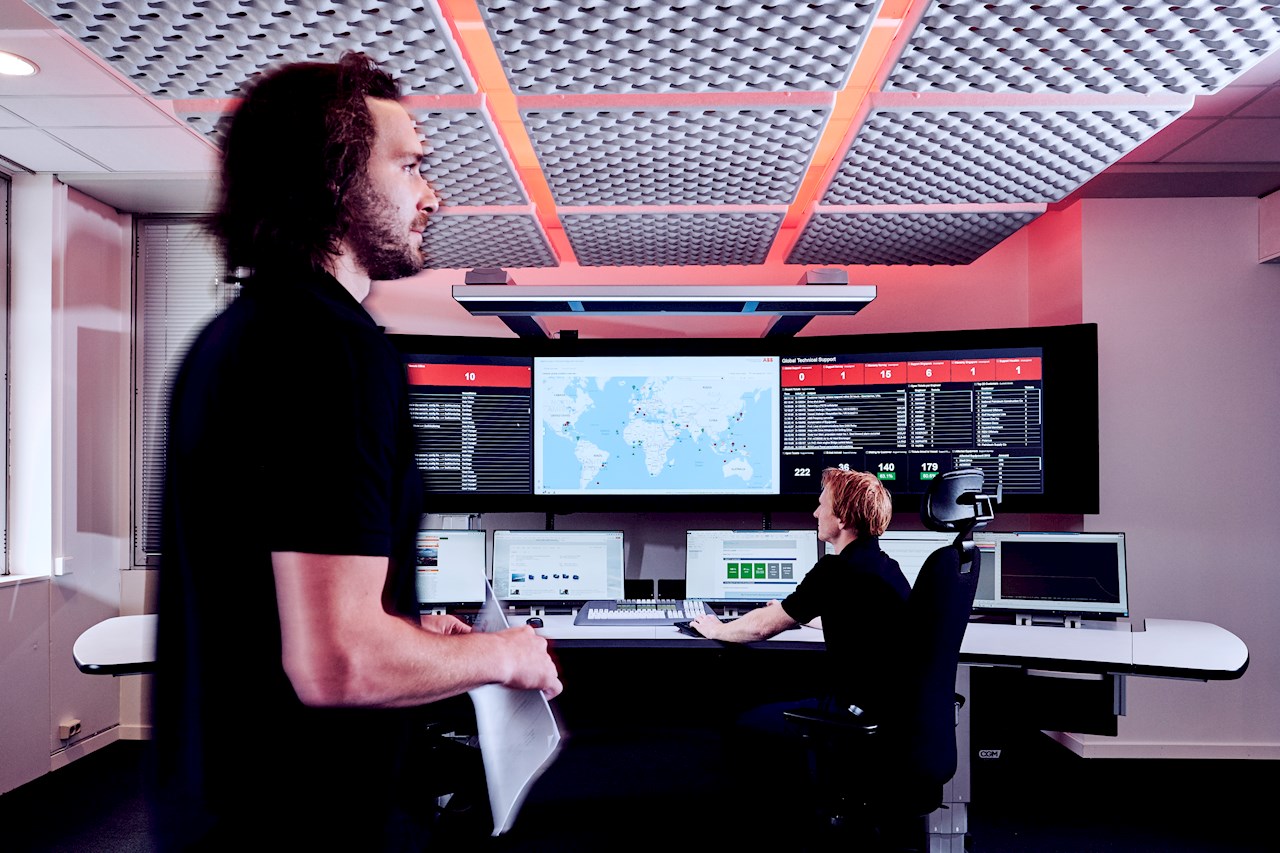