Marcus Martelin, VP Service Product Group Manager for Electric Systems, ABB Marine & Ports
In a ‘smart port’, when a ship docks, it is also plugged into an onshore energy supply, allowing electrical onboard functions to run while the diesel engine is shut off. This cuts out harmful emissions and reduces noise pollution in sensitive, often densely populated harborside areas. In some circumstances, landside power supply can be used as ‘charge’ to replenish a shipboard energy storage system, with the resulting battery power available for short distance operations, whether for end-to-end ferries or for emissions-free propulsion in port or in protected waterways, for example.
To understand the value of shore connection in more tangible terms, it is helpful to compare the fuel consumption of a typical diesel-powered commuter ferry with that of a vessel modernized to draw on shore supply. If a conventional ferry consumed 84 liters of diesel fuel per hour, its battery-powered equivalent would, of course, consume zero. However, a ferry adapted to run on hybrid power could consume as little as 17l/h, depending on the operational profile.
As a leader in electric shipping and smart port technology, ABB Marine & Ports offers comprehensive shore connection solutions comprising state-of-the-art infrastructure both on shore and on board. Systems are compliant with international regulations and includes high- and medium-voltage switchgears, transformers, frequency converters, control and protection systems and more.
In conjunction with these solutions, ABB provides a wide range of services, such as remote monitoring, planned maintenance for ABB installed base and third-party systems, system studies, project management and training, as well as round-the clock access to its global support network.
Shoreside installation
With an important role to play in reducing the enivironmental impact of global shipping, shore connection has received backing from organiations such as the European Union. For example, EU Recommendation 2006/339/EU promotes the implementation of shoreside electrical facilities, while EU Recommendation 2003/96/EC proposes the subsidisation of shoreside power supply for ships through the cancellation of electricity taxes.
At the same time, discrepancies in frequency between ship and shore are driving demand for more intelligent landside solutions.
ABB’s onshore offering comprises transformers and frequency converters to synchronise shoreside power, voltage and frequency with those of the vessel’s onboard system. Also included are connecting cables and berth terminals with capacity for several ships. The solutions are suitable for container terminals and city harbours, with power ratings to suit even the largest ports.
They cover the entire chain from the substation receiving electricity from the local network to the power outlet at the dock. Furthermore, all major components can be accommodated within compact buildings or containers designed to blend into the surrounding environment.
ABB delivered the world’s first shore power supply system to the Swedish port of Gothenburg in 2000. Other ports to have implemented high voltage shore power supply systems include Karlskrona, Gothenburg and Ystad, Sweden; Antwerp and Zeebrugge, Belgium; Rotterdam, The Netherlands; Lübeck, Germany; Oulu, Finland; Delimara, Malta; Duqm, Oman; Los Angeles and Seattle, United States; Vancouver, Canada; Jurong Singapore; and Dalian, China. It is currently engaged in projects to equip the ports of Incheon, South Korea and Tallinn, Estonia with shore power systems.
Shipside installation
ABB’s shore power supply solutions allow a vessel’s energy load to be transferred to the shore-side source in a secure, automated manner, without disruption to onboard services. This means that the ship’s auxiliary engines can be shut down for the duration of its harbor stay. Emissions into the local surroundings are thereby eliminated, enabling compliance with environmental regulations set by authorities such as the International Maritime Organization, California Air Resources Board, the EU and individual governments.
In addition, ABB shore connection solutions cover all necessary electrical and automation infrastructure on board and can be used for retrofits and newbuilds. They are delivered on a turnkey basis, with support in procurement, project management, system studies and calculations, engineering, installation, commissioning and testing.
Installation and connection in depth
Onboard shore connection is available in the power range 0–20 MW. Smaller vessels such as ferries typically use low-voltage solutions, while larger vessels such as cruise and container ships require higher voltages. ABB offers shore connection solutions in low voltage (less than one kilovolt in alternating current power and less than 1.5kW in direct current power) in accordance with IEC/IEEE 80005-3 LVSC general requirements – and high voltage (between 6.6 and 11kW) in accordance with IEC/IEEE 80005-1 HVSC general requirements. Sockets and plugs are standardized for roll-on/roll-off vessels and passenger ferries (11kW), container ships (6.6kW) and cruise ships (6.6kW, 11kW). Standardized cable management systems are available for these vessel types.
Installations vary depending on the kind of solution being deployed and on which type of vessel. For Azipod® electric propulsion systems on cruise ships, for example, cable sockets are mounted in the front part of the cabinet. A shaft line system on a container vessel involves an onboard cable drum lowering the cable down to the quay for onshore termination. Meanwhile, the shaft line system for ro-ro and ro-pax vessels entails an onboard transformer converting the power from high to low voltage.
In general, the sequence for connecting and disconnecting a vessel to shore power is as follows: the ship arrives in port, power and control cables are connected, and the last running engine is synchronized with the landside power grid. After the shore connection circuit breaker is closed, the generator is offloaded, and the engine is stopped. Before the vessel departs, the first engine is restarted and synchronized with the onshore power grid. Once the load has been transferred to the generator, the shore connection reopens, power and control cables are disconnected, and the vessel is ready for departure.

Shore connection system components
Essential components of a high-voltage shore connection system include a high-voltage shore connection panel, an automation interface between shore and ship, a main switchboard feeder panel, control and protection equipment, safety circuits and an incomer panel.
The high-voltage shore connection panel is developed in accordance with the rules of major classification societies. It features a finished cabinet solution with power and control modules. This may come equipped with either cable sockets in the front or openings for cable entry through the cabinet floor.
Automation interfaces are standardized based on the ABB platform and also comply with guidelines laid out by major classification societies.
Installation of the main switchboard is carried out on a case-by-case basis. It may be fitted as part of the vessel’s existing main switchboard with an additional cubicle and circuit breaker including control and protection devices. Alternatively, a ‘generator panel’ can be connected to the ship’s main switchboard via fixed cables or bus bars.
Optional components include:
- Power management system with integrated shore power system
- Step-down transformer to match shore voltage with ship voltage
- Human-machine interface to operate the shore power system
- Cable management system (typical for container vessels)
- Automatic voltage regulator, i.e. Unitrol® 1020
- Governor system, i.e. DEGO IV
- Protection coordination study upgrade
Shore charging for electric vessel operations
As noted earlier, shore charging solutions are a vital component in the smart-port environment – allowing emissions-free propulsion in protected areas – and need to be designed and delivered in conjunction with the rest of the system. They can take one of two basic forms depending on requirements: manual cable connection and automatic connection.
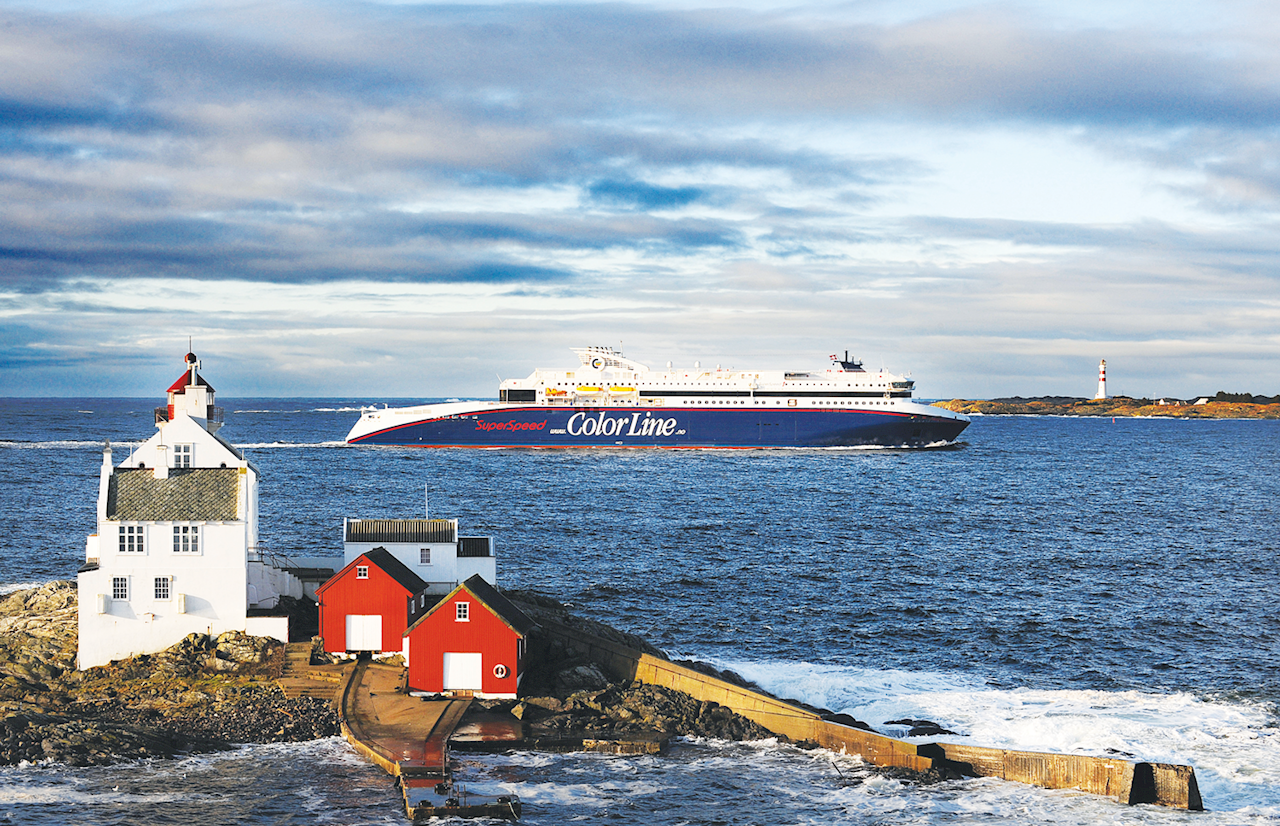
Manual cable connection
Manual cable connection is appropriate when normal operations do not require fast battery charging. Low-voltage, manual plug-in solutions are available up to 600 amperes, which typically allows a transfer power of up to 450 kilowatts. It is divided between night-time and daytime charging.
Night-time charging is when the battery is connected to the power supply overnight, leaving it fully replenished ahead of daily operations. In daytime charging, the battery receives power in shorter intervals throughout the day. How the two methods are combined influences the dimensions of the battery and transfer line.
Maximizing the daytime charging current often means deploying longer transfer lines, components and batteries (batteries are oversized to account for cyclic charge/discharge current). Meanwhile, placing more emphasis on overnight charging increases total battery capacity requirements or calls for hybrid operations, with batteries used in parallel to the generators.

Automatic connection
Available in both low- and medium-voltage solutions, automatic connection provides a power range of up to 20 MW, making it preferable for fast charging. It allows vessel operators to maximize charge during short harbor stays. It also keeps crew involvement to a minimum. However, automatic connection can be significantly more expensive and careful analysis is required to determine whether a connection is really feasible.
Conclusions
With environmental regulations becoming ever-more stringent, shore connection is garnering wider attention – and with good reason: synergy between shore and ship improves the efficiency of vessels but also, crucially, helps to protect harborside environments.
ABB Marine & Ports offers landside and onboard solutions encompassing every step in the shore-to-ship chain. These enable vessels to run auxiliary functions wholly on shore power while berthed, negating the need for bunker fuel in shoreside operations. They also optimize the battery-charging process so that electric and hybrid ferries can comply with regulations while operating in sensitive areas.
A considerable number of smart ports are already active around the world, and many more are in the planning or development stages. As the technology becomes more widely established, ships will become more efficient and ports will become cleaner, benefiting everyone from shipowners and electricity suppliers to dock workers and harborside residents.