Samuli Hanninen, Key Account Director, ABB Marine & Ports
Matko Barisic, Technology Manager, Marine Software Development Center, ABB Marine & Ports
Torsten Heideman, ABB Marine & Ports
Krzysztof Goldon, R&D Senior Engineer, Marine Software Development Center, ABB Marine & Ports
Sampo Viherialehto, Sales Manager, ABB Marine & Ports
Pirjo Maattanen, Senior engineer, structural mechanics, ABB Marine & Ports
Since 2007, traffic volumes in the arctic seas have increased substantially, especially in the North-East Passage following the development of major oil and gas projects. In development of icebreaking liquefied natural gas (LNG) tankers, the selection of propulsion system plays a major role determining vessel performance, safety and icebreaking capability.
The recent success of the Yamal LNG project has led to accelerated development of new arctic LNG projects, such as Arctic LNG2. This paper will introduce selected operational results from the revolutionary icebreaking LNG carriers with modern azimuth propulsion systems.
This paper describes the methodology for using remote diagnostics systems (RDS) onboard ice-going LNG carriers to continually record, consolidate, upload, and analyze ice-breaking propulsion performance. We will further describe how vessel operational experience and RDS data can be used in development of icebreaking LNG carrier propulsion design and product development.
Special attention will be given to the propulsion system of a large Arctic LNG carrier equipped with three 15,000 kW azimuth thruster units. These propulsion devices help shipowners to access opportunities in the Arctic region by providing safe and reliable operation. The paper will highlight some of the key findings from ship machinery using data collected with RDS and further analyzed by an engineer specializing in ice loading on machinery systems and components.
Podded propulsion solutions have played a major role on Arctic ship projects, making these challenging projects technically and economically feasible. The latest findings and unique results from Arctic LNG carriers represent valuable information in the development of future Arctic energy transportation in the Northern hemisphere.
Hydrocarbon transportation in ice infested waters
Historically, most oil shipments in ice conditions were to supply communities in the North or the Antarctic research stations. These operations were normally executed during the summer months with or without the assistance of icebreakers. Shipping companies generally used the tankers they had on hand, and hardly any purpose-built vessels were constructed.
The first Arctic oil was discovered on the North Slope of Alaska in the late 1950s. This large deposit sparked rapid development in many sectors of the oil industry, and two different oil export schemes were investigated. One was the pipeline across Alaska from Prudhoe Bay on the North Slope to Valdez in the south of Alaska. The other was tanker shipment along the North West passage through the Canadian Arctic.
The shipping alternative was thoroughly investigated by the converting of an existing tanker, the SS Manhattan, the largest commercial vessel under the US flag at that time, into a highly sophisticated icebreaking tanker, and by ice model tests in Finland. The old bow was removed and replaced by an extreme icebreaking bow. The remaining hull and propulsion system were extensively strengthened for ice operations. The modified vessel was delivered in 1969.
In the summer of 1969, SS Manhattan made its way through the North West passage from the east and reached Prudhoe Bay to receive one symbolic barrel of oil to bring back to the US east coast, escorted by US and Canadian icebreakers. The following summer the vessel made a second experimental voyage along the same passage.
The main lesson learned from these voyages was that Arctic navigation was feasible with a good icebreaking bow and high power. However, the oil company decided in favor of the pipeline option and the Trans-Alaska Pipeline was built.
Despite promising discoveries in the Canadian Beaufort Sea, no further commercially viable Arctic oil export has taken place in North America. Focus shifted to the Soviet Union when oil was discovered first on offshore Sakhalin and later in the Pechora Sea. These events actually meant the launch of Arctic oil and gas shipping, and were soon followed by shipment systems for the Novi Port oil and LNG from the Bay of Ob.
Ice class and icebreaking performance
All major classification societies have adopted IACS UR for Arctic vessels. The IACS rules focus on the structural integrity of the vessel, both hull and propulsion, but leave the questions of power and icebreaking performance to the discretion of the owners and designers. Not all those involved in Arctic shipping are aware of this fact. When relating ice class to ice performance, the question is often, “Which ice class do we need to go to go there?” This is only half the truth, in the sense that a certain location or route will require a certain ice class at a certain time of the year, but the ice class will certainly not guarantee that the ship can reach that location or sail that route. It is up to the owner or operator to specify performance requirements, allowing the vessel designer to determine the appropriate power level. The Russian Register, RMRS, and the Finnish-Swedish Ice Class Rules are the only regimes with requirements for vessel power.
Lessons learned from SS Manhattan showed that required icebreaking performance can be obtained with a good icebreaking bow and sufficient propulsion power, at least to a certain extent. As vessel size and performance requirements increase, traditional thinking eventually comes up short.
The Double Acting principle
In the history of icebreaking, the effectiveness of having at least one propeller in the bow has long been recognized. In 1888, the railroad ferry SS St Ignace commenced service on the Mackinac strait between the Upper and Lower Michigan peninsulas. The wooden vessel had one propeller in the aft and one in the bow. It operated for more than a decade and served as an example for designers of icebreakers in Europe. In fact, the sub-arctic Baltic icebreakers stem from SS St Ignace, after Finnish designers visited the vessel around the turn of the century.
Icebreaking tests with Baltic icebreakers in the 1970s revealed that ice resistance decreased when more power was distributed to the bow propellers. In theory the ultimate icebreaker would have 100 percent power in the bow. In practice this is not feasible since such a vessel would be difficult to steer in the desired direction and it would be very inefficient in open water transit.
The advent of the azimuth thruster with pulling propeller was a true game changer for icebreaking technology. Now it was possible to fully utilize the combination of full power at the stern when running astern, with good performance going ahead. This method of operation is called Double Acting (DA). The main idea behind DA is to optimize the stern for icebreaking in difficult ice conditions, and the bow for various other conditions. This might mean a bulbous bow for good open water performance, or an extreme icebreaking bow for breaking multi-year ice.
The podded propulsion prototype with 1.3 MW of power was retrofitted to the fairway service vessel Seili in 1990, which first entered service in 1991. The first commercial applications included the retrofitting of two Finnish 1A Super tankers, MT Uikku and MT Lunni in the early 1990s. These vessels were extensively tested in both Northern Baltic and Arctic conditions, and they fully revealed the superior icebreaking performance of DA vessels running astern in difficult ice conditions.
The improved performance can perhaps best be illustrated by a trial where MT Lunni had penetrated through a grounded ridge field in the Northern Baltic running astern. The vessel was not able to return through the broken track running bow first, despite having a very good icebreaking bow. (Heideman, 1996).
Considerations on selecting a propulsion system for Arctic hydrocarbon transportation
Icebreaking projects vary greatly according to environmental requirements and operational demands. When evaluating and comparing alternative propulsion systems for a ship project, the total operation of the fleet should be taken into consideration. The performance of an individual ship in the given ice conditions is naturally the basis for such an evaluation. The following topics should be included as part of the Arctic fleet evaluation:
- Icebreaker assistance requirements for the fleet
- Icebreaker availability
- Operational aspects of low load operation of the machinery
- Hull form performance in both open water and ice conditions
The following topics relate to an individual Arctic vessel and fleet from the point of power plant and propulsion system selection.
Maneuvering in ice
The maneuverability of the vessel with azimuthing propulsion is superior compared to normal rudder and shaft line vessel. This makes tactical ice navigation, following leads, and other ship duties in ice safer and more efficient.
Harbor maneuvering in ice covered waters
Azimuth thrust can be used to clear ice between the pier and the ship, allowing considerably faster berthing of a vessel. The time saved can be used to increase the transportation capacity of a vessel, or to achieve fuel savings through slower vessel speed.
Ice management
There are several ice management tasks that can be efficiently performed using the wake from azimuth propulsion, for example:
- Clearing hummocked ice and breaking ice ridges
- Freeing a beset vessel without external icebreaker assistance by manipulating vectored thrust, enabling autonomous operations
- Breaking and clearing moving pack ice
- Clearing an ice channel behind a vessel
- Clearing ice from around hull of the vessel
- Clearing ice from between the vessel and a secondary object
- Widening the ice channel behind the vessel
Auxiliary icebreakers
Vessels with azimuth thrusters have proven to be capable of navigating independently in difficult ice conditions. This reduces or eliminates the need for auxiliary icebreakers, resulting in savings on both investment and operating cost of the fleet. The use of auxiliary icebreakers should be evaluated against the project’s operational requirements. Feasibility varies between projects. For example, if port operations are significant, and the port facility is by nature prone to difficult ice concentrations, a port icebreaker should be considered. In other cases, overall investment and operating costs are optimized with purpose-built vessels able to operate independently in all conditions without icebreakers. It should be noted that for vessels with more than 40m of beam, two icebreakers per vessel are typically required for successful assistance. The rate for one medium size icebreaker can be in the order of USD 30,000/day, meaning investment in a more ice-capable vessel design may well be justified.
Fuel consumption and exhaust emissions
Due to a reduced need for installed power, the fuel consumption of an azimuth thruster vessel is considerably lower than with shaft-line propulsion. Depending on vessel design and propulsion configuration, fuel consumption with podded drive can be reduced by up to 20 percent. With the electric power plant principle, diesel engine loading can be kept closer to optimum. This will lead to reduced specific fuel consumption by the diesel engines, resulting in lower emissions.
Cargo capacity per vessel
Podded propulsion and its auxiliary equipment arrangement have a smaller footprint than shaft line propulsion vessels. Therefore the same size ship can be designed for more cargo capacity, increasing transportation capacity and making it feasible to reduce speed during the voyage.
Ship hull form performance
Icebreakers have traditionally been designed to strike a balance between icebreaking performance and open water seakeeping ability. The requirement for open water operations is weighed against time used in icebreaking. As an example, some icebreakers designed solely for Baltic icebreaking are unable to safely make sea voyages even with moderate wind conditions of +15m/s. On the other hand, some multipurpose icebreakers are designed mostly for operation in open water, but with limited icebreaking capability. Azimuth propeller thrust gives the vessel designer the possibility to incorporate both excellent icebreaking capabilities and seakeeping in open water into the design. This is the DAS or Double Acting Ship concept.
DAT – Double Acting Tanker
The DAT concept is a design principle for icebreaking vessels where the vessel bow and hull shape are optimized to meet operational requirements. DAT design allows for the bow of the vessel to be optimized for open water operations and very good sea keeping, while the aft of the ship is optimized for icebreaking. The vessel normally moves bow first in open water and easy ice conditions. When the ice becomes more difficult to force, the vessel is turned around and proceeds astern. Azimuth propulsion has the unique capability of having the greatest icebreaking efficiency when the pod units are pulling the ship. The propulsor wake flushes the hull and greatly enhances icebreaking performance. At the same time the rotating pods allow for precise control of the vessel when moving astern. The podded propulsion configuration also allows the aft to be designed specifically for icebreaking. These operational features are not achievable with conventional shaftline propulsion.
Efficiency and seaworthiness in open water
With azimuth thrusters and the DAT concept, the bow shape can be optimized for open water operation, leading to reduced resistance and improved seakeeping characteristics. An extreme icebreaking bow, long with a small stem angle, can be highly vulnerable in open water conditions due to slamming loads in heavy weather. The benefit of reduced resistance can be used for a higher open water speed or reduced fuel consumption.
When designing the icebreaking capacity of a ship, the following criteria should be considered:
- Operational profile determining how much of the time a vessel is expected to operate in ice
- Prevailing ice conditions
- Maximum ice conditions that may be reasonably expected
- Availability of icebreaking assistance
- Required open water transits
- Cargo carrying capacity and vessel dimensions
- Geographical and climate requirements, such as polar service temperature
- Maritime treaty obligations like Polar Code, ISM and SOLAS
- Classification society selection and requirements
Power requirement
Due to more efficient ice and open water hull characteristics for DAT with azimuth propulsion, the comparative power requirement in some cases can be 50 percent of the shaftline version. This will lead to considerable cost and space savings on machinery, as total installed power and auxiliaries are significantly reduced.
Ridge and rubble performance
Ridge and ice rubble penetration capacity is far better for DAT than for traditional bow-first operation, since the ice resistance can be up to 50 percent less when going astern. Penetrating hummocks and ridges in difficult ice conditions places great demands on ship design. When a vessel is breaking ice, it uses both the hull shape and thrust to force the ice. When the resistance of a ridge formation exceeds the power output, the vessels comes to a stop. If the ridge must be forced, traditional icebreakers reverse to create a path used to accelerate and ram the ice features bow first. This operation is violent and offers only one option for the bow shape. With DAT, the vessel enters the ridge aft first and manipulates the pods repeatedly. In this way the vessel enters the ridge without the need for ramming.
Novel fuels and carbon emission targets
Many shipowners have decided to build their new vessels to work with dual fuel, and this it is of course a natural choice for an icebreaking LNG carrier. The combination of marine diesel and LNG gas brings together long endurance and low emissions. LNG dual fuel engines emit methane, or methane slip. This occurs mostly in high dynamic load variations of power. Icebreaking is good example of this. Load bank or battery energy storage can greatly reduce methane slip and enhance icebreaking capability. In the following, the results of Ice Mode control and load bank enhancing performance of Arctic LNG Carriers are introduced.
Double Acting Tanker references and operational experience
The international breakthrough for the DA concept came in 2006, when the mining company Norilsk Nickel took delivery of the first of five ordered containerized bulk DA carriers for the transport of ore from Dudinka on the Yenisey River. The company was aiming for independent navigation along the Western Part of the Northern Sea Route, without the assistance of icebreakers. The ice trial results, Wilkman G. (2007) and 15 years operational experience have proven the concept. The transport system was a success, largely due to the DA concept, and paved the way for the concept in the development of the hydrocarbon transportation in the Russian Arctic.
As mentioned earlier, in 1993 and 1994 the Finnish Neste tankers MT Uikku and MT Lunni were retrofitted with azimuth thrusters providing 11.4 MW of power. Since they were retrofits, the propulsion units were the pushing type, meaning that the propeller was situated behind the propulsion motor inside the pod. The vessels have been operating until recently in the Arctic Ocean for the Murmansk Shipping company. In 2001 and 2002 Fortum (formerly Neste) took delivery of two Aframax 1A Super ice class tankers, MT Tempera and MT Mastera. The vessels were equipped with a single, pulling type azimuth propeller with 16 MW of power. These two vessels were the first tankers to fully utilize the DAT concept.
Three 70,000 dwt twin podded propulsion DA tankers with propulsion power of 2 x 10 MW were delivered to Sovcomflot between 2007 and 2009 for Lukoil’s Varandey offloading terminal in the Pechora Sea. They were soon followed by two 70,000 dwt twin podded propulsion DA tankers for Prirazlomnoye project in the Pechora Sea in 2009 and 2010, with 2 x 8.5 MW of propulsion power.
Varandey Tanker MT Vasily Dinkov
In 2011 Norilsk Nickel took delivery of an 18,500 dwt DA tanker based on the same hull and propulsion as the bulk carriers. During 2016 and 2017, Sovcomflot received six 42,000 dwt twin DA tankers for the Noviy Port oil export terminal, 2 x 11 MW of power.
The Yamal LNG consortium led by Novatek started to produce LNG in Sabetta located on the Bay of Ob in 2017. Several shipping companies have acquired a total of 15 LNG carriers of the same design for shipment. The 170,000 cbm DA tankers each have three 15 MW azimuth propulsion units. In 2019 the consortium added two 50,000 dwt twin thruster DA condensate carriers with 2 x 11 MW pods to the fleet. In 2020, ALNG2, also led by Novatek, placed an order for six optional LNG carriers with a somewhat improved design. A discussion of operational results of these Arctic LNG Carriers follows.50
Arctic tankers for the Yamal LNG project
Arctic tankers and LNG carriers have been in the forefront of adopting new propulsion technology over the last decade. The driver for change has been the difficult environmental conditions present in the area of operation. In this chapter we discuss the propulsion solutions used in the fleet of tankers and LNG carriers operating along the Northern Sea Route (NSR).
Arctic waters present unique ice condition characteristics. Sea ice conditions vary greatly, with ever-changing environments. For icebreaking, this offers unique challenges. Sea ice in the Arctic is also a mix of drift ice and multiyear inclusions. Ice on the open sea is always moving. Experience shows that ice movement ranges from 0.1 knots to 1.3 knots, Vainio J. (2002). When the ice is packed against a land mass or fast-ice pack, the combination of wind and ice movement creates ice pressure. This pressure in turn forms different ice features. In a level ice field, the pressure begins to crack and bend the ice, creating ridges and hummocks. If the ambient air temperature is well below freezing, the hummocks consolidate and become very difficult to force. Where swell and wind work against the ice edge, the result is different. Here drift ice is ground into shuga by wave energy, creating brash ice barriers. If the temperatures are well below freezing, the brash ice barrier eventually consolidates into floes that are very difficult to force.
The NSR presents an environment where the prevalent ice is moderate to heavy first year ice. The NSR is also very shallow, with a dynamic river output producing characteristic river ice intrusion. However, the NSR also typically offers large ice features of multi-year-ice (MYI), Chai, W (2020). It is this combination that requires vessels operating along the NSR to be equipped with sufficient power and dimensions to operate in difficult brash ice and shuga conditions with inclusions of MYI features.
It can be argued that without thruster technology, the LNG operations in these ice conditions might not have been economically feasible. Azimuth propulsion is able to direct the thrust vector, and combined with the DAT principle, to flush the vessel hull when moving astern in difficult ice conditions. The advent of DAT and podded propulsion were key enablers in independent vessel operations along the NSR. With conventional propulsion, the fleet would be required to rely on external icebreaking assistance to a large degree. The operational requirements for this solution lead to both increased investment and operating costs (CAPEX and OPEX).
Arctic countries provide line icebreaking as a public payable or free service for all commercial cargo transport. As such, government icebreakers are not well suited to support single operations on a continuous basis. By contrast, icebreaking services provided by nation states require commercial tonnage to be of sufficiently high ice class. Freeriding is a tempting path for managers chartering tonnage for their company’s operations. However, the strict requirements for operating vessels along the NSR have been designed to prevent this, and to create a level playing field. Tanker and LNG operations along the NSR represented a departure from this, in that the operators chose to invest in tonnage able to operate independently.
Christophe de Margerie, was the first of Yamal LNG fleet’s LNG carriers, total 15 vessels. The first vessel was delivered in 2017. The entire fleet was in operation by 2019. As of February 2020, they have delivered 30 million tons of LNG from Sabetta to Europe and Asia, Figure 1.
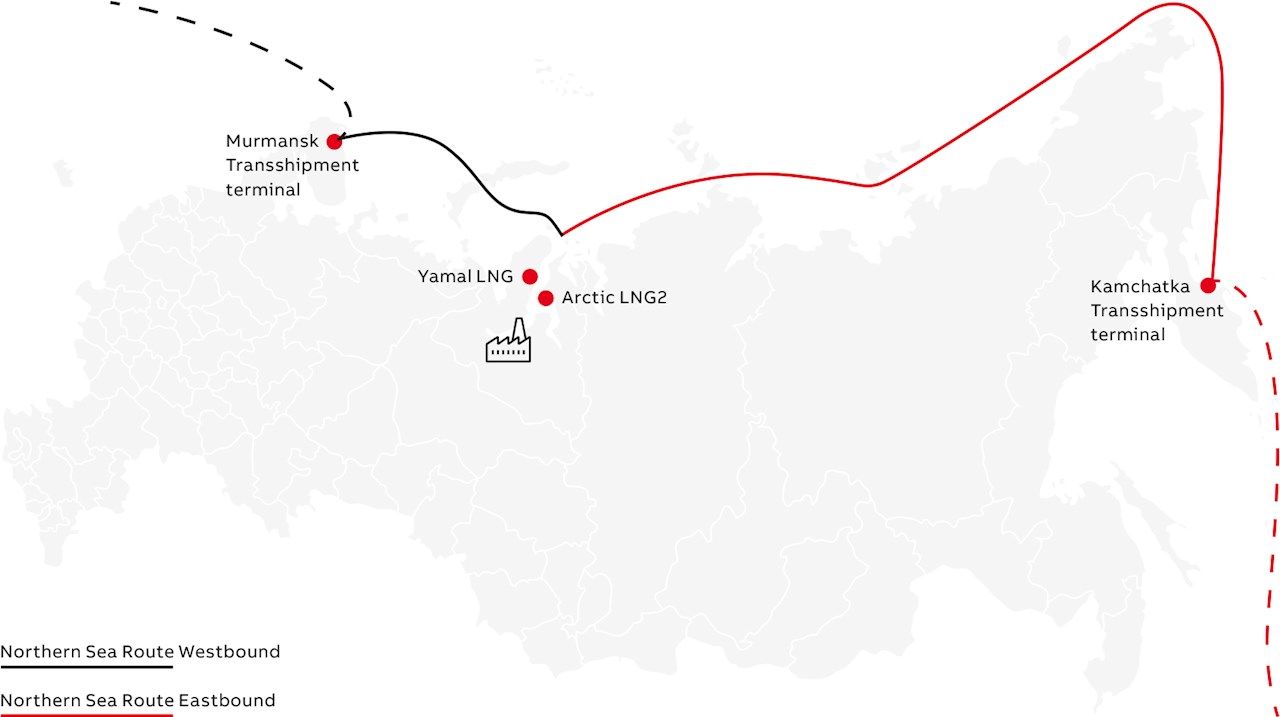
Some cargoes from Arctic tankers are transferred ship-to-ship in the Barents Sea, near Murmansk, to open water LNG tankers. This optimizes the transfer operation, where a high ice class arctic tanker operates in demanding conditions, and the open water voyage can be made with lighter vessels.
The Yamal LNG fleet has operated continuously since 2017 from Sabetta to Europe, and in the summer months, via the NSR to Asia. Previously it was possible to operate the NSR only for four summer months using icebreaker assistance. Ships employing new technology have now enabled operation for a longer period. In addition, ice conditions in recent years have been lighter than usual.
Yamal Arctic LNG Carriers have made few voyages on the NSR Eastbound, the latest in May 2020 and January 2021. In May 2020 a Russian nuclear icebreaker provided assistance. In January 2021, one of the vessels sailed independently from Sabetta to Asia. The voyage from Sabetta to the Bering Strait took 11 days, with an average speed of 9.5 kn. The ship was operating stern first for most of the voyage in ice. Parallel to this, two other Yamal LNG tankers were sailing the NSR. All three were sailing independently without icebreaker assistance. One purpose of the voyages was to study year-round operation or at least extending the sailing period for the Eastern NSR route.
Arctic LNG Carrier operating stern first in ice (courtesy of SCF)
The following is a description of some of Arctic LNG carrier technical features that secure safe and successful operation along the NSR.
Ice Mode as a control technology for making gas-fueled ice-breaking performance more robust
In addition to the previously mentioned advantages of podded electrical propulsion in ice-breaking conditions, the control of propulsion on such systems is achieved by controlling fast-acting electrical quantities and flows of electrical power. The fast-acting nature of such control loops, and the proper dimensioning of solid-state and rotating electrical machinery through which the electrical power flows for mechanical effect, provides further benefits that are impossible to achieve with purely mechanical propulsion. One such benefit is Ice Mode functionality. This is a networked, decentralized control function that performs synchronization of electrical power flows across multiple propulsion line-ups, i.e. in cases where there is more than one electrical drive onboard. In the case of the Yamal LNG project, this function acts to unify power flow control over the three line-ups for the central and side propulsion units. This function increases the robustness of the total electrical propulsion system when acting in a closed bus-bars regime, against stall-outs of electrical motors with rigid connection to the ice-milling propellers, which otherwise can cause serious power imbalances. Such power imbalances are caused momentarily on the electrical side of the electrical propulsion system by a near-instantaneous drop in the amount of electrical power that an electrical motor used for ship propulsion via rigid coupling to a propeller can consume. This is caused by the mechanical obstruction of the propeller by ice too thick to mill in heavy ice-breaking conditions, when pods are used for active ice-milling in the front-facing, pulling configuration. As a result of the rigid coupling of the propeller to the rotor, the motor’s function is reduced to that of a transformer, and the effective impedance. Therefore the ability to dissipate power by incoming currents fed by the electrical drive is reduced to negligible amounts.
In legacy and competitive solutions to the one delivered in the Yamal LNG project, the resolution of such power imbalance is relegated to the governors supplied by the manufacturer of the prime mover, the internal combustion engine (ICE). Since impedance on the electrical load-side of the generation sets in question is reduced, this is reflected on the gen-set’s mechanical side as a precipitous decrease of the loading torque on the mechanical axle linking the generator and the ICE. When this happens, given steady-state throttle opening of the ICE effective for the conditions on the electrical propulsion network for the immediately preceding conditions, the rpm of the axle increases precipitously. As a result the governors will decrease the throttle opening, eventually bringing the system back into balance.
The issue is the fast-acting nature of the electrical load change, which can be a liability in boiloff gas-fueled prime mover ICEs. In such dual-fed ICEs, governors operate in two distinct modes, with the gas-fed mode featuring constrained throttle-up and throttle-down curves, due to boiloff gas having lower specific energies than marine diesel oil (MDO). Lower specific energy of fuel means in turn that the ICE fed with such fuel will stall out and shut down if the throttle is operated as dynamically as with MDO feeding. Therefore, if the governors detect the need to reduce the throttle more intensely than allowed by the gas-fed throttle-down curves, they will in dual-fueled configurations automatically switch to the more energetic fuel, MDO, and proceed on the more liberal curves. Since such events, consisting of rapid intermittent reductions in the power load of the electrical power system, are common in heavy-duty ice-breaking, in classical installations this would mean very common surreptitious switch-over to MDO, rather than proceeding to break ice while consuming boil-off gas, which would ruin the economy of an ice-breaking LNG carrier’s High Arctic transit.
In the case of the Yamal LNG project, ABB has installed further safeguards and followed the “Swiss Cheese” safety model approach in order to greatly improve the ability to perform heavy ice breaking while the ICEs continue in gas-fed regime. The first safeguard is the rating of the installed ACS6000 heavy-duty medium voltage drives for intermittent 180 percent nominal torque delivery. A fast-acting control loop, acting on electrical and digital quantities (indirect torque measurement through current measurement, acting on pulse widths for individual thyristor firing), upon detecting rpm reduction in the motor, will increase the amount of torque provided to the motor, with the goal of matching the increased loading torque on the propeller by the ice stalling its rotation. If the loading torque provided by the ice that the propeller is biting into while ice-milling is greater than 180 percent nominal, Ice Mode functionality kicks in.
Classical layers of safety for ice-breaking with gas-powered prime movers and electrical propulsion
Introduction of Ice Mode for increased safety, robustness, and performance
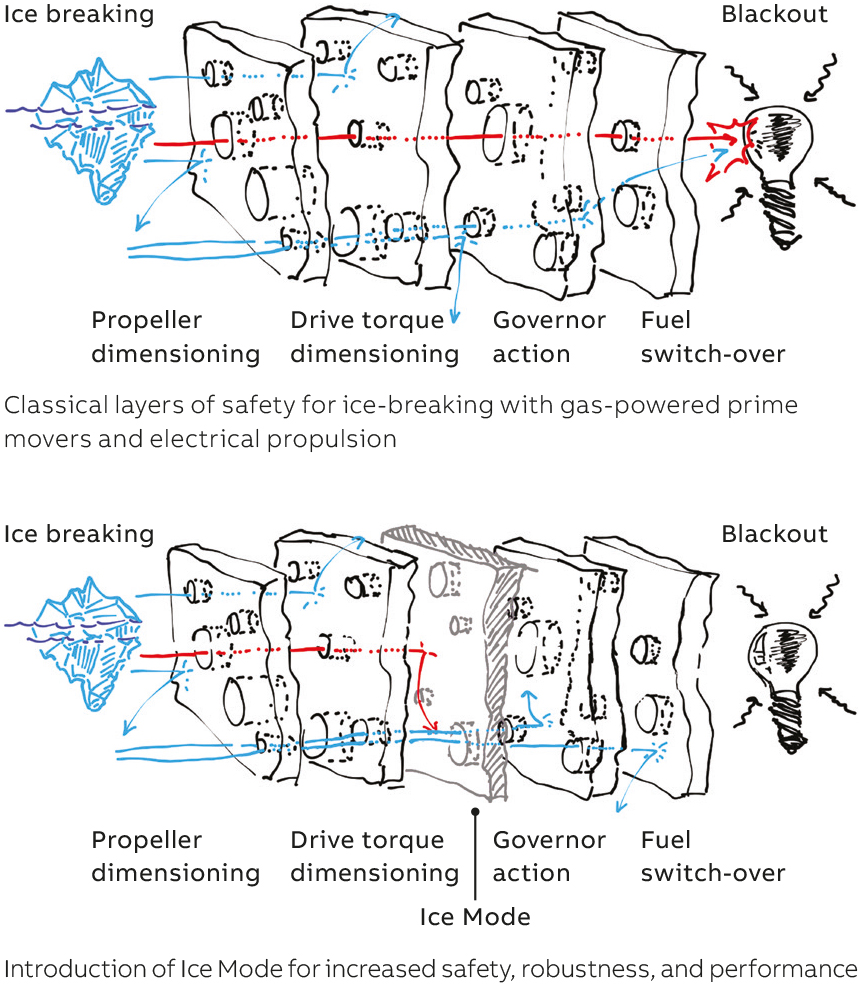
Ice Mode can be conceived as the “middle” barrier in the Swiss Cheese model in Figure 2. Its purpose is to provide further robustness of the electrical system, before relying on the ICE governors, to level out the load-side power consumption. It is enabled by installation of additional DC chopper modules in the electrical propulsion main drives on the line intended to “bleed” counter-direction currents into a braking resistors bank. These allow the control of currents in the DC link of the electrical drives, in effect allowing the fine control, rather than safety through passive proper dimensioning, of the loads dissipated on individual braking resistor banks. Ice Mode function, implemented as a coordinated, decentralized function of the three separate propulsion control solutions in charge of their own electrical propulsion line-up in Figure 3, therefore has access to a total of six electrical quantities that it can use to balance the electrical load of the total system.
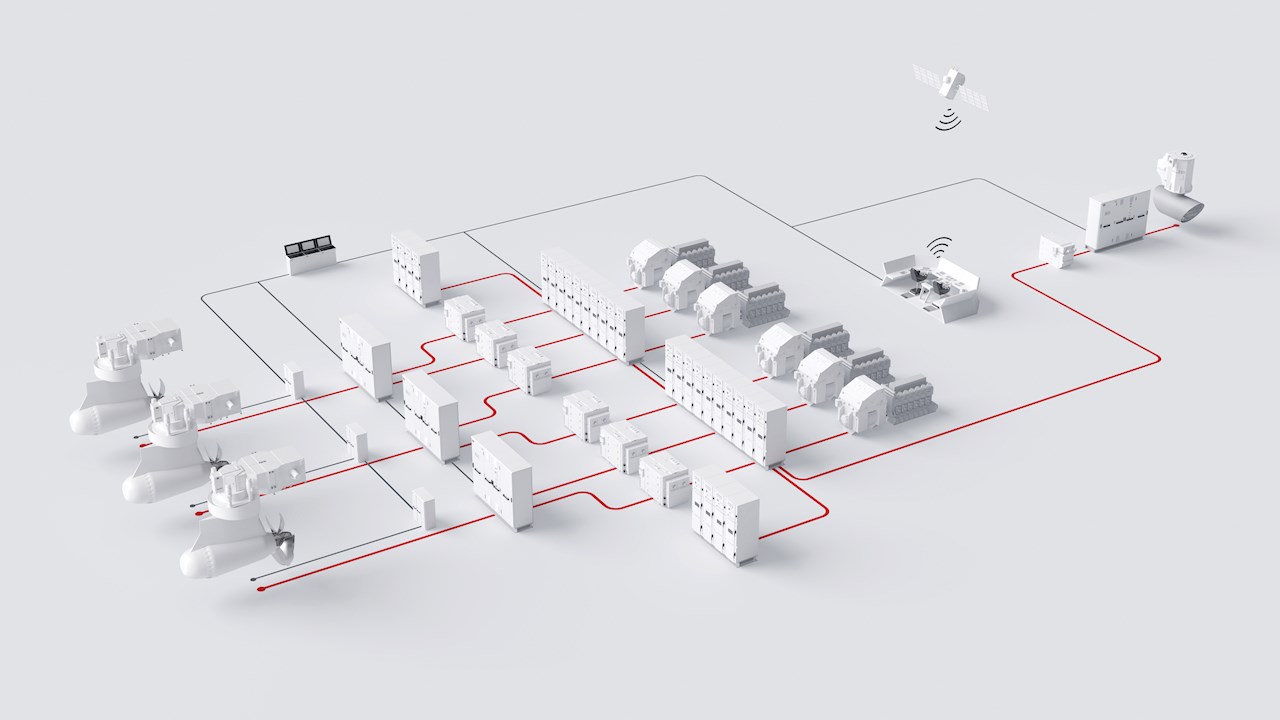
For each line-up, the Ice Mode function can command both the power shunted to the braking resistor bank, or inject an excess power (power boost) signal to the requested power to be loaded onto each of the pods. Since these six channels of action are all electrical quantities, they outpace the dynamics with which the imbalance is ordinarily converted to the mechanical side of the gen-sets as increase in generator axle rotation (which is what the ICE governors will act on). Ice Mode effectively combines the three braking resistor banks, one in each line-up of the Yamal LNG carriers, into one virtual power “pool” that can be used to offset the imbalance, and all non-stalling propellers (either two in the case of one pod stalling during ice-milling, or one if two are stalling simultaneously) as another such “pool”. The action of Ice Mode vs. the action of only governors when stalling events due to ice are encountered is presented conceptually in Figure 4.
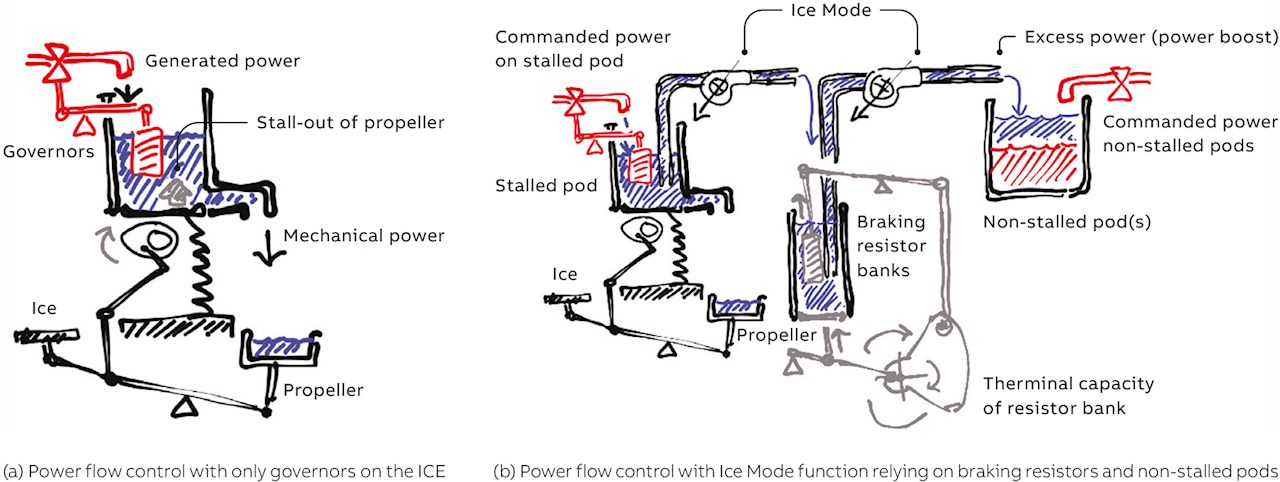
The power of the Ice Mode function comes from the interplay of the two available pools of load that are managed and coordinated in order to stabilize conditions on the electrical propulsion network. The braking resistor banks are solid-state devices that can quickly act to stabilize the load conditions, by consuming appreciable currents and dissipating the electrical energy as heat. However, they are limited in the amount of power they can instantaneously consume compared to the large electrical motors of the podded propulsion units.
Additionally, resistors are further limited in the total amount of energy (power consumption integrated over time) that is converted to heat and manifests as temperature increase. If they are over-used in this load balancing strategy, they are soon interlocked on grounds of overheating, for safety reasons. To avoid this scenario, the Ice Mode function starts commanding the propulsion control units in parallel on all the pods that are not experiencing stall-out events to load up more power than commanded by control levers on the bridge. In use cases where Ice Mode is typically active, the exact amount of power with which each pod is loaded, especially in the short term, is not particularly important, as the vessel is moving slowly while ice-breaking, and already experiencing a highly dynamic power regime on the propellers.
While this is ongoing, Ice Mode is aware of the amount of power by which the generation can be reduced following the safe throttle-down slope for the ICE prime movers burning boiloff gas, and will leave the safe amount of excess generated power unconsumed on the network, such that the governors will, following their standard functionality, ramp the prime movers down safely and appropriately.
A pronounced example of Ice Mode action in the case of stall-out of two out of the three propellers available to Yamal LNG carriers is provided in Figure 5. These events are rare, even during intense icebreaking activity, characterized by cumulative statistics of overtorque spikes on the propulsion drives provided in Figure 6, and identified in the datasets by the blue high kurtosis component probability distribution function provided in Figure 7. Nonetheless, such events are not exceedingly rare, so for prolonged High Arctic operation in winter months it is highly beneficial to both over-dimension the torque capacity of the drives, allowing for operation in the area denoted by the red ellipse on Figure 6, and have recourse to use Ice Mode functionality able to allow ride-through of ice-milling stall-out events while continuing to operate prime mover ICEs on boiloff gas from the transported LNG cargo.
Image currently unavailable
Image currently unavailable
Image currently unavailable
Image currently unavailable
Image currently unavailable
Image currently unavailable
Image currently unavailable
Image currently unavailable
Image currently unavailable
Figure 5. An intense ice-milling stall-out event featuring parallel stall-out of 2 out of 3 pods Figure 6. Statistics (event histogram) of overtorque events during ice-milling. Columns in the area above 150 percent nominal overtorque are indicative of stall-out ride-through on LNG when redimensioning ACS6000 drives to 180 percent overtorque rating. Figure 7. Statistics of torque (mechanical loading of the propeller) dynamics: a Gaussian mixture with most prominent component in low ratings for unconstrained sailing; prominent peaks also in medium ratings for light ice navigation; one trailing peak in high ratings for heavy ice navigation.
Trends in Arctic shipping and future development
Ongoing changes in Arctic sea ice are significant. The last twenty years have seen many record lows broken for extent of summer ice in the Arctic, Figure 8, Lindsey, R. (2006). Sea ice extent during the Arctic winter has, however, remained constant despite global warming. The notable change has been in ice thickness and the ratio of multi-year ice (MYI) versus first year ice. Ice conditions in the Arctic are such that shipping is predominantly focused on the summer and fall months of each year. The diminishing summer and MYI ice conditions have opened up possibilities for economic activity not previously feasible. For example, LNG and oil exploration activities are expanding in the Arctic. Also Arctic mining projects that have not previously been feasible are on the rise. Predicting according to what we have seen taking place in the Arctic in general, we can extrapolate that there will be growth in economic activity in the region. This will drive the change in Arctic shipping.
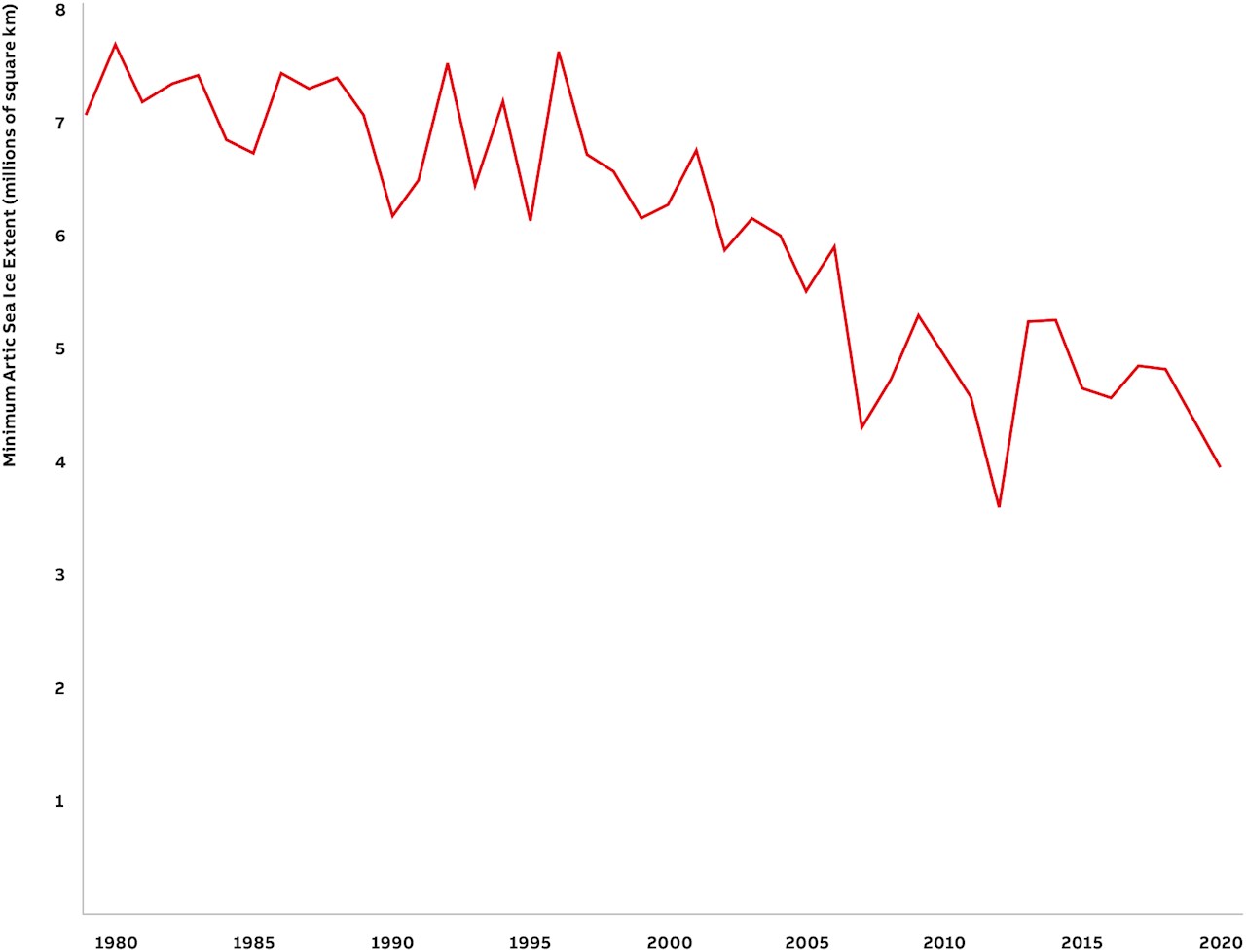
There are three distinctive sectors where growth can take place in response to the change in ice conditions in the Arctic. First, as discussed above, is Arctic exploration for hydrocarbons. The growth in this sector is however, subject to changes in the global efforts to reduce greenhouse gas emissions. New regimes and treaty obligations are to be expected, Henderson, J. (2014). It can be argued that this sector will remain difficult to predict.
Secondly, Arctic mining has been increasing in volume for the past years. New projects are also on the way, Sharman, H. (2011). Arctic mining has been under somewhat similar pressures as hydrocarbon exploration regarding environmental aspects. However, the technology needed to shift towards zero-emission transport will require the extraction of minerals. In this respect, Arctic mining can be expected to be on a growth track in the future.
Thirdly, we can expect to see major new projects in telecommunications infrastructure in the Arctic, Saunavaara, J. (2018). Global demand for ever-faster data transfer is bound to bring the transpolar cable route to fruition. This endeavor will require specialized shipping solutions, but is nevertheless becoming more feasible as the climate change advances.
In December 2020, six newbuild Arctic LNG carriers were contracted featuring a trio of the largest and most powerful azimuth propulsion units ever supplied for ships operating in ice. Together, the giant 17 MW propulsion units will provide total power of 51 MW, enabling the vessels to navigate safely through ice up to 2.1 meters thick. In similar conditions, conventional comparable ships would require icebreaker assistance.
In summary, the need for icebreaking vessels in shipping will be on the rise as climate change increases. This may seem counter-intuitive to some extent, but ice conditions in the Arctic will nonetheless remain challenging for shipping for decades to come.
Conclusions
The development of podded azimuth thrusters for icebreakers started with small units 30 years ago. Over the years, high power units of up to 17 MW have been realized. Most new icebreaking ships have been built for trade and traffic in the Russian north, serving mainly the oil and gas industry.
This paper has addressed the selection criteria of propulsion system for icebreaking tankers, and presented recent results collected from Arctic LNG carriers. The largest icebreaking vessels ever built, these ships have further demonstrated the possibilities of year-round Arctic shipping. Ice Mode propulsion control system was specially developed to provide operational safety and efficiency for the dual fuel LNG fired engines powering these vessels. Ice Mode control principles have been demonstrated with full-scale machinery load data during harsh icebreaking operation.
References
Heidenman, T, Salmi, P, Uuskallio, A, Wilkman, G, Full-scale ice trials in ridges with Azipod® (Azimuthing Podded Drive) Tanker Lunni in Bay of Bothnia 1996, Polartech 1996, St. Petersburg, Russian Federation
Vainio, J. (2002). Sea Ice Nomenclature. Helsinki: Merenkulkulaitos.
NOAA; Climate Change: Arctic sea ice summer minimum
Author: Rebecca LindseyMichon Scott
Sharman Haley, Matthew Klick, Nick Szymoniak & Andrew Crow (2011) Observing trends and assessing data for Arctic mining, Polar Geography, 34:1-2, 37-61, DOI: 10.1080/1088937X.2011.584449
The Oxford institute for energy studies; The Prospects and Challenges for Arctic Oil Development; James Henderson , Julia Loe https://www.oxfordenergy.org/publications/the-prospects-and-challenges-for-arctic-oil-development/
AU – Saunavaara, Juha
Arctic subsea communication cables and the regional development of northern peripheries
ISSN 2221-2698.2018.32.63
Chai, W., Leira, B.J., Høyland, K.V. et al. Statistics of thickness and strength of first-year ice along the Northern Sea Route. J Mar Sci Technol (2020). https://doi.org/10.1007/s00773-020-00742-5
Wilkman G., Elo, M., Lonberg L., Kunnari, J. Ice Trials of MV Norilskiy Nickel in March 2006. 19th International Conference on Port and Ocean Engineering under Arctic Conditions (POAC'07).
Abbreviations
ACS6000 – Type of Medium Voltage electric AC Drive
Azipod® – electric podded azimuth thruster produced by ABB
DAS – Double Acting Ship, icebreaking ship designed to run ahead in open water and thin ice, but turn around and proceed astern in heavy ice
DAT – Double Acting Tanker, icebreaking tanker designed to run ahead in open water and thin ice, but turn around and proceed astern in heavy ice
DA – Double Acting, operating astern in heavy ice
DC – Direct Current
IACS – International Association of Classification Societies
IACS UR – International Association of Classification Societies Unified Requirements
ICE – Internal Combustion Engine
IMO – International Maritime Organization
ISM – International Safety Management
LNGC – LNG Carrier, tanker designed for transporting liquified natural gas (LNG)
MDO – Marine Diesel Oil, blend of gasoil and heavy fuel oil
MT – Motor Tanker
MYI – Multiyear Ice, sea ice that have survived at least one melt season
NSR – Northern Sea Route, North-East Passage
NOAA – National Oceanic and Atmospheric Administration
POLAR CODE – International code for ships operating in Polar waters
RDS – Remote Diagnostic System
RMRS – Russian Maritime Register of Shipping
SOLAS – Safety of Life at Sea, an international maritime treaty
SS – Steamship