There are entrepreneurs, and then there is Mikael Hugoson, an energetic man who constantly wants to develop his business. He and his family are the owners of Alviksgården, the parent company of Nyhléns Hugosons, northern Sweden’s largest meat and sausage company.
“I build, build and build and love development, always using the latest technology. At the farm we have a very good network and in total there are 130 kilometers of cable which makes it possible to have a very high level of automation”, says Mikael Hugoson.
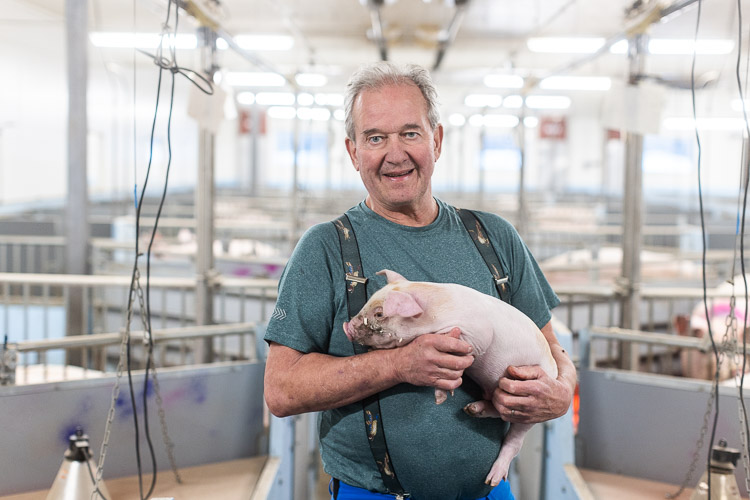
In 1975, Mikael Hugoson came to Alvik where there were several pigs and a few pigsties that Mikael's father had built, but not much more. The breakthrough came a few years later when grocery store Konsum Norrbotten and the charcuterie company Goman started buying animals from the farm, and after the merger in 2005 with competitor Nyhléns, the company grew further. Today, Nyhléns Hugosons handles everything from animal breeding, selection processes and slaughtering to cutting and processing of meat and charcuterie products.
To have success in this growth has required major investments in Alviksgården, which now produces around 27,000 pigs per year. Beef and lamb are also slaughtered and cut here. With impressive plans for the future, including producing natural manure and investing in wind turbines on its own land, several key local advisors are involved in the technology solutions.
One is Krister Johansson, who runs the company AutoEl i Alvik AB and is responsible for programming the automation solutions. Krister buys much of the material for his projects from Mikael Hugoson's pig farm via wholesaler El-ektroskandia in Luleå, as well as products directly from ABB. These include low-voltage and automation products, drives and electric motors.
“When Mikael Hugosson started his big expansion ten years ago, he chose our ABB Compact HMI automation system, which has been further developed at each new stage. With its help, he can have full control of the cooling machines and ventilation in the slaughterhouse and cutting plant, the biogas plant, as well as heating, ventilation, fertilization, lighting and water management in the animal houses, which plays an important role in the farm's sustainability profile”, says Kent Öhlund, sales engineer at ABB Electrification in Luleå, Sweden.
He notes that this efficient system has even enabled energy consumption to be reduced despite the expansion of the stables.
Since the Smissline rail system is used for the control cabinets in Alviksgården, all technical equipment has been able to be placed in a small area in a safe, accessible and flexible way.
Mikael Hugoson together with Kent Öhlund, ABB.
An important partner is Tobias Johansson, who runs TJ Elkonsult AB. He is responsible for drawing up the technical documents and building the equipment cabinets. Another partner is Elektroskandia, which supplies many of ABB's products for its projects used at the pig farm.
“It is fun and inspiring to have Mikael Hugoson as a customer. He always wants the latest in technology which gives us great challenges. The fact that we have such a good relationship with ABB also means that we can always offer the latest cutting-edge technology to Alviksgården," say Krister Johansson and Tobias Johansson.
Automation system creates a good environment for the pigs
Mikael Hugoson is a man of action, but he has a long-term mindset. He has put a lot of effort into creating a good environment for the pigs. Here, for example, the piglets are always with their mother and siblings for as long as they need to be, according to nature's own laws.
The pigs live in an environment where they are relieved of stress and where the sows get a chance to recover properly after each litter. Barns are built according to the pigs' needs and behavioral patterns. With the automation system, the pigs' environment is controlled with, among other things, the temper-ature in the stable.
Mikael Hugoson was early to come up with advanced technical solutions. Since 1998, the first in Sweden, there has been a biogas plant at Alviksgården that makes use of all residual products and makes the farm self-sufficient in electricity. There is also a wood chip boiler that produces all the heat and hot water needed on the farm, using wood chips from the farm's own forest.
“Our next major investment is a digestate plant where we will produce natural manure to feed our fields, which in turn will produce feed for the pigs. Sales on the open market are also on the cards. This plant should be ready in April 2022”, concludes Mikael Hugoson.
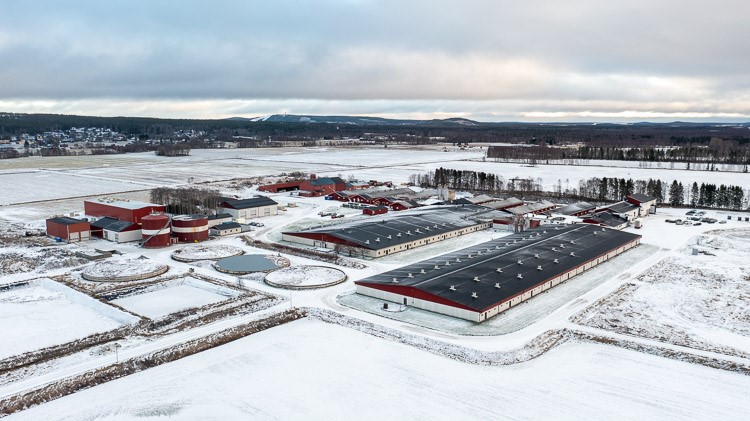
Facts: Nyhléns Hugosons
Nyhléns Hugosons is headquartered in Luleå, where it also manufactures charcuterie products such as sausages and sandwich foods. In Skellefteå, meat is packaged and “palt”, “kroppkakor”, sandwich cakes, salads and wraps are produced. In Ullånger Nyhléns Hugosons operates a slaughterhouse for beef, veal and lamb and in Boden they produce their chilled ready meals. The company, which has a total of 600 different products, are owned by Mikael Hugoson and the CEO Magnus Nilsson.
Facts: What ABB has delivered to Alviksgården
- Automation system System Compact HMI with about 2500 signals with AC800M, PM867, PM851, virtual servers, virtual clients and mobile clients.
- Electric motors and drives; ACS580, ACS880 and ACS310.
- Pilot devices from the Compact series and Modular plastic series: pilot lights, potentiometers and accessories such as enclosures and legend plates.
- Combi Module socket-outlet switches, connectors, front and side-controlled safety switches
- Smissline rail systems for install Smissline miniature circuit breakers and Smissline personal protection switches, contactors, manual motor protectors, Softstarters, standard products such as ESB miniature circuit breakers, personal protection switches, earth leakage switches, load break switches, circuit breakers, energy meters, car heating control panels, voltage aggregates, plug-in relays and compact starters.
Text: Lars Westerlund
Photos: Patrick Degerman