Advanced process control
ABB Ability™ Expert Optimizer opens up the benefits offered by Big Data, data analytics, advanced process modeling algorithms and artificial intelligence (AI) to maximize a plant’s potential. Whether optimizing alternative fuel (AF) use, reducing feed variability and raising cement quality, or balancing kiln performance, it streamlines complex and multivariable cement plant processes, boosting productivity and averting unnecessary downtime.
Specifically, ABB Ability™ Expert Optimizer assists cement plants in four key areas: kiln optimization, AF management, mill optimization and material blending.

Kiln |

Mill |

Material blending |
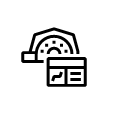
AF management |
In the kiln, ABB Ability™ Expert Optimizer first helps stabilize the process before automatically running the variables to the limits of process constraints, ensuring optimal performance. When AFs are added to the equation, it can control, mix and monitor rates of AF substitution to ensure consistent burning, while avoiding instability due to changes in the fuel’s calorific value.
In the grinding circuit, ABB Ability™ Expert Optimizer optimizes the grinding circuit to increase throughput and ensure consistent output, while lowering energy consumption. It also ensures that the blending of both raw materials and final product is optimized, essential for energy-efficient clinker production, as well as the delivery of on-spec cement to customers.