An ABB digital monitoring system is giving chemical company Evonik real-time transparency about the consumption of every switching component in the low-voltage power supply at its production site in Essen, Germany. The ABB technology complements Evonik’s existing system’s real-time data collection.
The solution also logs temperature values for switching elements and plug contacts, enabling Evonik to prevent thermal losses and premature mechanical wear. The ABB system ensures Essen’s production-critical power distribution system benefits from a longer service life and significantly increases its availability.
Specialty chemicals may sound like a niche industry – in fact specialist materials from innovation leader Evonik help make tires more energy-efficient, mattresses more elastic, medicines more effective and pet foods healthier. Evonik enables manufacturers from different sectors to achieve higher product quality.
Real-time transparency key to energy efficiency
“Electrical energy has never been as valuable as today,” says Carsten Liedtke, Head of Operations at Evonik Technology & Infrastructure, Essen and responsible for the measurement, control, and management of its energy supply. For Liedtke, energy efficiency has one fundamental requirement: maximum transparency for the site’s complex supply network’s real-time consumption and availability. “Only with valid real-time information can we optimize our production’s energy requirements in a targeted way. This is extremely important for our costs and for the CO2 footprint of our production.”
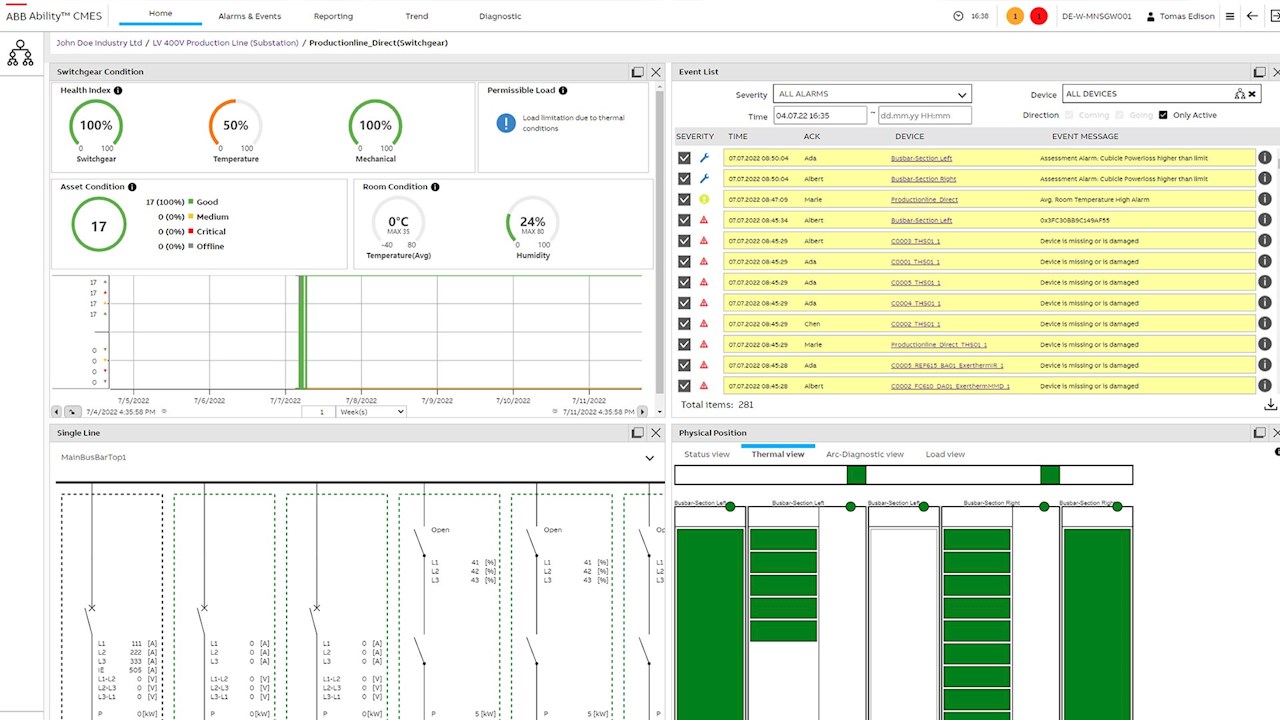
The operations manager turned to ABB in early 2020, sharing his ambition to pursue and expand the real-time digital monitoring of the site’s production-critical supply infrastructure. The upcoming replacement of a low-voltage switchgear with a modern ABB MNS-3 solution provided a welcome opportunity to tackle his digitization plans together.
Central database logs technical status data
In addition to standard multimeters and energy meters, the ABB team also installed temperature sensors at critical connection points within the switchgear. Each feeds data into the central ABB AbilityTM Condition Monitoring Electrical System (CMES): “CMES gives Evonik real-time transparency about the current status of each individual switching component," says Thorsten Volz, Global Product Manager for Low Voltage Switchgear Digital Systems at ABB.
Like all ABB Ability digitization solutions, ABB AbilityTM CMES is available as either a multi-site cloud solution or an on-site system. Evonik chose an on-site installation, logging information in the central CMES database about both consumption and the status of switching elements within the new power supply infrastructure. The contact temperatures of plug, busbar, and cable connections are a particular focus.
“Conventional infrared measurements only provide snapshots: the CMES analyses a permanent record of the values along with the actual electrical current, enabling analysis at selected points and long-term evaluations,” explains Volz.
Less heat loss, wear and tear and maintenance costs
Temperature fluctuations at contact points are an indicator of loose connections or material fatigue. They can increase the contact’s electrical resistance, in turn increasing thermal losses and the risk of arcing faults. Both reduce energy efficiency and threaten system availability. "With ABB’s CMES, we are able to identify potential weak points in advance and address them in good time – before the power supply fails," says Liedtke.
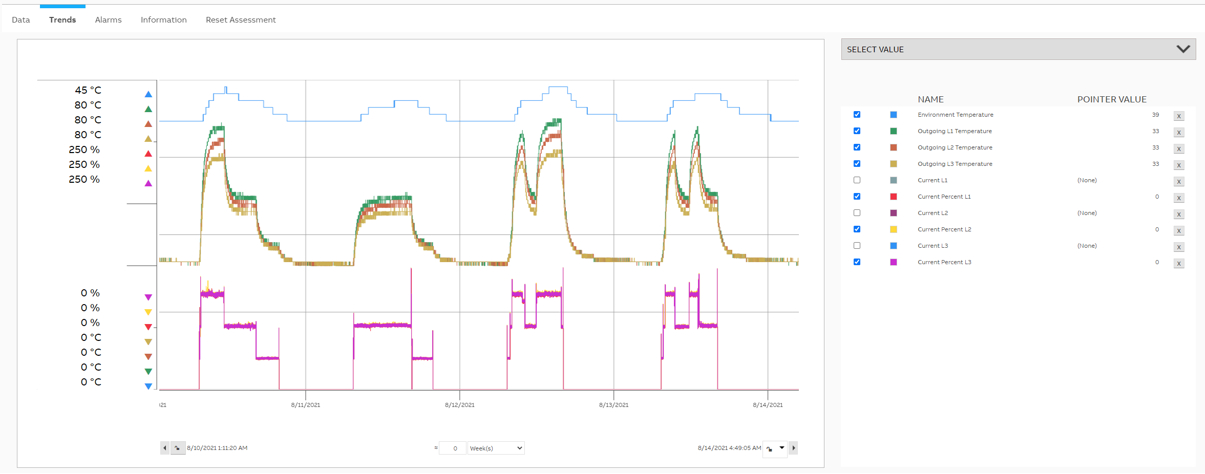
With real-time transparency of the plant’s complete electrical supply platform, the ABB Ability™ CMES makes it possible for Evonik to introduce flexible maintenance concepts. Maintenance can be performed according to the actual condition of components, instead of rigid intervals. Wear and tear is identified and unnecessary work is avoided.
"The digitization of our power distribution with ABB is significantly improving energy efficiency, increasing the stability of the production-critical power supply and, thanks to predictive maintenance, is extending the service life of the switchgear," says Liedtke. “All three fit perfectly with Evonik's sustainability strategy.”
____________
ABB (ABBN: SIX Swiss Ex) is a leading global technology company that energizes the transformation of society and industry to achieve a more productive, sustainable future. By connecting software to its electrification, robotics, automation and motion portfolio, ABB pushes the boundaries of technology to drive performance to new levels. With a history of excellence stretching back more than 130 years, ABB’s success is driven by about 105,000 talented employees in over 100 countries. www.abb.com
ABB’s Electrification Business Area: Electrifying the world in a safe, smart and sustainable way, ABB Electrification is a global technology leader in electrical distribution and management from source to socket. As the world’s demand for electricity grows, our 50,000+ employees across 100 countries collaborate with customers and partners to transform how people connect, live and work. We develop innovative products, solutions and digital technologies that enable energy efficiency and a low carbon society across all sectors. By applying global scale with local expertise, we shape and support global trends, deliver excellence for customers and power a sustainable future for society. go.abb/electrification