Alf Kåre Ådnanes, Manager, Electric Solutions, ABB Marine & Ports
Mikko Lepisto, Manager, Digital Solutions, ABB Marine & Ports
The vision of autonomous shipping may be closer than many may think. Some of the key technologies are already available today, and pioneering shipowners are gearing up to put them to the test in commercial applications.
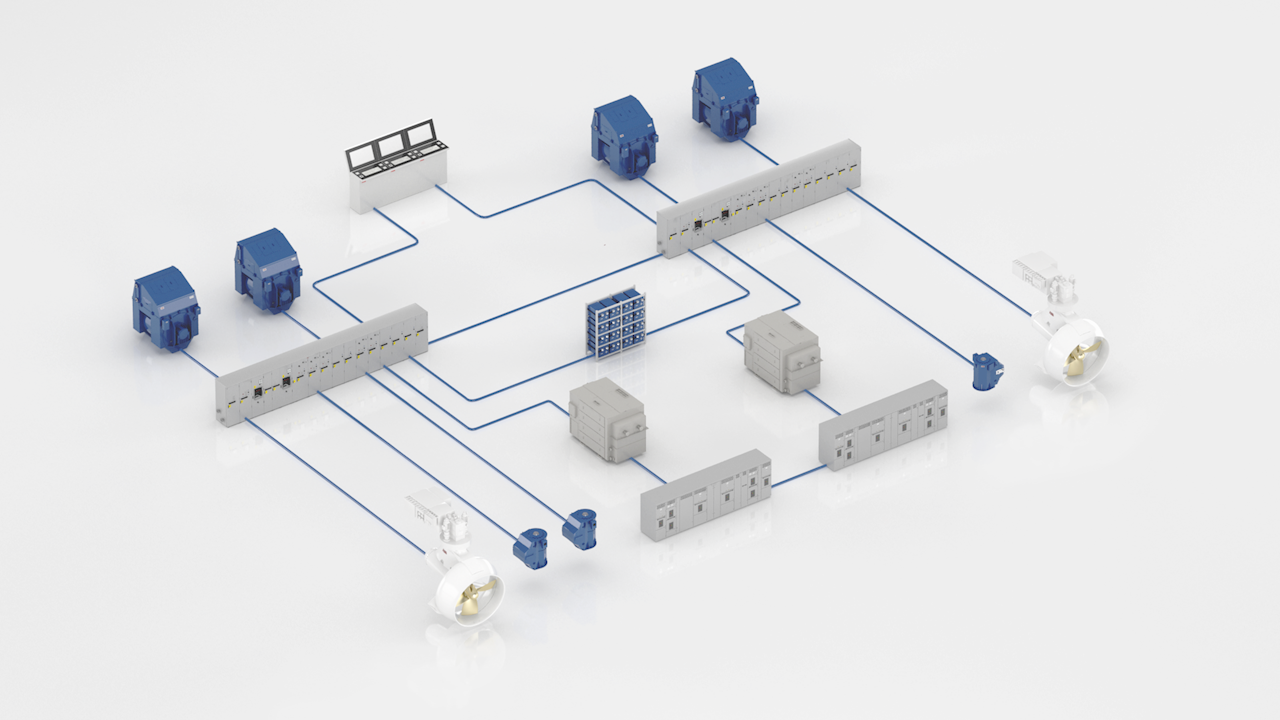
With autonomous technologies maturing fast, there is still a need to establish standards for design and operation of self-sailing ships. Rules and regulations ensuring safety and reliability of autonomous vessel operations also need to be in place. In the meantime, we will see a stepwise development with automated systems, remote connectivity and software for operational support being deployed. Each of these consecutive steps will add value for crews, fleet owners and service providers.
Central to autonomous concepts are the methodologies for visualizing and analyzing the ship’s surroundings, as well as controls for maneuvering and voyage planning. This includes sensor technologies, software analytics and artificial intelligence or machine learning methods for safe and optimal operations between ports. Remote connectivity is essential to monitor and interact with the vessels.
It is equally important to ensure that the ship’s essential systems for docking, maneuvering and navigating are ready for increasingly autonomous operations. The traditional mechanical propulsion train does not support high fault tolerance and redundancy, and is dependent on the ability of engineers to intervene in case of failures. In unmanned vessels, such failures must be avoided. Alternatively, the system should be able to reconfigure into a safe mode for continuous operation, either through automatic self-healing or by means of interaction with onboard digitalized control and monitoring system through remote connectivity. This is one of the reasons ABB believes that the next generation of ships – including increasingly autonomous vessels – will be electric, digital and connected.
In the past, integrating different shipboard systems was restricted by limited communication between hardware and proprietary technologies, as well as by the inadequate performance and high cost of ship/shore communication via satellite or radio.
Now, the digital revolution, cloud technologies and the Internet of Things, Services and People (IoTSP) have changed the game. Platforms and standards are in place for collecting and transmitting more data from thousands of embedded sensors, ultimately enhancing vessel management. ABB has established ABB AbilityTM, the company’s unified, cross-industry, digital offering — extending from device to edge to cloud — with devices, systems, solutions, services and a platform that enables customers to increase productivity and to lower costs. ABB Ability™ was launched in 2017 and already offers more than 210 solutions, including the ABB Ability™ Collaborative Operation Centers for marine.
Development continues in the direction of autonomous and even unmanned ships and fleets. Already today, technologies are ready for demonstration and piloting of unmanned vessels on commercial routes. In November 2018, Ice-class passenger ferry Suomenlinna II was remotely piloted through test area near Helsinki harbor, proving that human oversight of vessels from anywhere is achievable with today’s technologies. Suomenlinna II was retrofitted with ABB’s dynamic positioning system, ABB Ability™ Marine Pilot Control, and steered from a control center in Helsinki.
The transition from traditional to future ship designs has been enabled by electric propulsion. Electric power plants have evolved substantially since the first large-scale applications some 25-30 years ago. Development has been driven by demands for higher efficiency, lower emissions, safety through redundancy, and comfort for crew and passengers.
Today, electric propulsion is used in a wide range of ship types, with a variety of basic concepts ranging from AC and DC distribution systems to electric-mechanical hybrids, and more recently, fully electrical power trains employing energy storage systems.
New and cleaner energy sources are gaining ground in shipping, such as natural gas or new liquid fuels as alternatives to the traditional heavy fuel oil and marine diesel oil. Hydrogen fuel cells are also being explored for zero emission designs. In mid-2018, ABB signed and MoU with Ballard Power Systems covering the development of a next-generation fuel cell power system for sustainable marine e-mobility. ABB and Ballard Power Systems will leverage the existing kilowatt-scale fuel cell technologies and optimize them to create a pioneering megawatt-scale solution suitable for powering larger ships.
Besides the well-known advantages of energy efficiency and the flexibility to utilize any kind of electric energy sources, the electric power grid is easy to design for fault tolerance and availability. For passenger vessels and ships with higher safety requirements such as DP ships, redundant, electric propulsion has become the industry standard.
For autonomous and unmanned vessels, the electric power and propulsion system is the fundament for achieving the robustness and availability required to overcome the need for onboard maintenance crew.
This paper sets out a holistic approach to system design, showing that fault tolerance automated, remote, or manual reconfigurations are beneficial in themselves. It also provides a platform for enhancing safe navigation and docking, and these building blocks will ultimately make autonomous and unmanned vessel operations feasible.
Electric propulsion as the backbone
An electric power generation and distribution system enables tight integration with automation and control systems, transforming ship installations from merely connected ‘blocks’ into a collaborative and highly automated system. The electrical ‘backbone’ also expands the range of viable energy sources beyond conventional combustion, accommodating environmentally friendly batteries and fuel cells.
Flexibility in the design of electric propulsion can provide high availability and efficiency through optimal engine control and loading, use of propulsors with high reliability such as Azipod® propulsion, and mechanical and hydrodynamic efficiency.
A recent, transformative technology is Onboard DC GridTM, a DC-based power system enabling simple, flexible and functional integration of energy sources such as variable speed gensets and shaft generators, batteries and fuel cells, Figure 1. Unlike AC based distribution systems, where connected generators need to match system voltage and frequency, the Onboard DC GridTM only requires the generators to match system voltage. This means that generator and engine speed can be dynamically optimized to the system load situation. When engine load decreases, engine speed is also reduced. For a medium speed diesel engine working at part load, this can result in more than 20% reduction in specific fuel consumption, as well as lower emissions and maintenance requirements. Since the power is individually controlled from each source, loading can be optimized for efficiency, performance, and lifetime management.
Onboard DC GridTM is a good choice for its simplicity, heightened fault tolerance, ease of energy storage integration, and alternative fuel sources that reduce emissions such as LNG or hydrogen in power production. System integration and control play to the strengths of the various energy sources in the system, and keep strict control of consumers using a Power and Energy Management System (PEMS™) to manage the balance of power and energy in the system.
Stepwise evolution towards autonomy
The list of benefits may already appear compelling, but intelligent and environmentally-friendly vessels benefit from the electric backbone for yet another reason: automation systems can be fully integrated, with all information needed to operate the vessel available in one system and one platform.
Onboard DC Grid™ with power electronics provides a unique platform for digital solutions on board a vessel. Using sensors and communication infrastructure, data is transmitted between systems in an instant. This provides access to information that enables the bridge to monitor and optimize performance, either manually or automatically.
This unified platform makes it possible to support full integration between the automation and power systems and the vessel’s digitalized connectivity. Ultimately, this provides the gateway through which ever-increasing computing capabilities in the cloud can be exploited on the owner’s terms, allowing machine learning and connected data analytics to provide what has not previously been possible in energy efficiency, asset and equipment maintenance management, and vessel safety. The high level of integration Onboard DC Grid ™ also means that high quality information on status and performance is available to onboard or remote operators and maintenance engineers as needed.
From this starting point, the path to fully autonomous and eventually unmanned vessels is achievable with a stepwise approach, with each step demonstrating results of individual value to ship operations.
Along the way, it is important to recap steps that have already been taken and examine those considered inevitable, to assess how far the maritime industry has come at any given point. From ABB’s perspective, the building blocks in place include:
- Highly reliable and reconfigurable electric propulsion systems, based on years of experience from vessels with dynamic positioning, passenger ships, and icebreakers, where requirements include high availability and reliability, and optimized design and control to reduce operation costs.
- Azipod® propulsion for reduced mechanical complexity of the propulsion train and high propulsion efficiency and maneuverability (Figure 2).
- Energy storage systems for reducing wear and tear of engines, further optimization of the operation for lower fuel consumption, and backup power for engine failure.
- Fuel cell power sources to reduce emissions and enable multiple energy source systems.
- Advanced protection systems and Onboard DC Grid™ to allow for fault tolerant electric system design, utilizing each energy source in individual, optimized conditions by integrating all sources and consumers, and reconfiguration with minimum impact on vessel performance and safety following component failures.
- Distributed and redundant automation systems, fully integrated with electric propulsion systems for automatic control, monitoring and plant diagnostics.
- Integrated navigation systems with extended functionality for augmented reality, situational awareness and navigation support, such as ABB Ability™ Pilot Vision.
- Operational support systems for operation planning, vessel optimization and route planning.
- Fleet information online and available in real time and connected to on-shore operations, with unlimited opportunities to process data in to analyze and optimize operations, performance and condition of vessels and fleets. In ABB, this is realized in the ABB Ability™ Collaborative Operations Centers.
Each of these building blocks have their own value in improving vessel performance and operations. Combined, they provide staging posts on the journey towards unmanned or reduced manned ships with autonomous control and navigation.
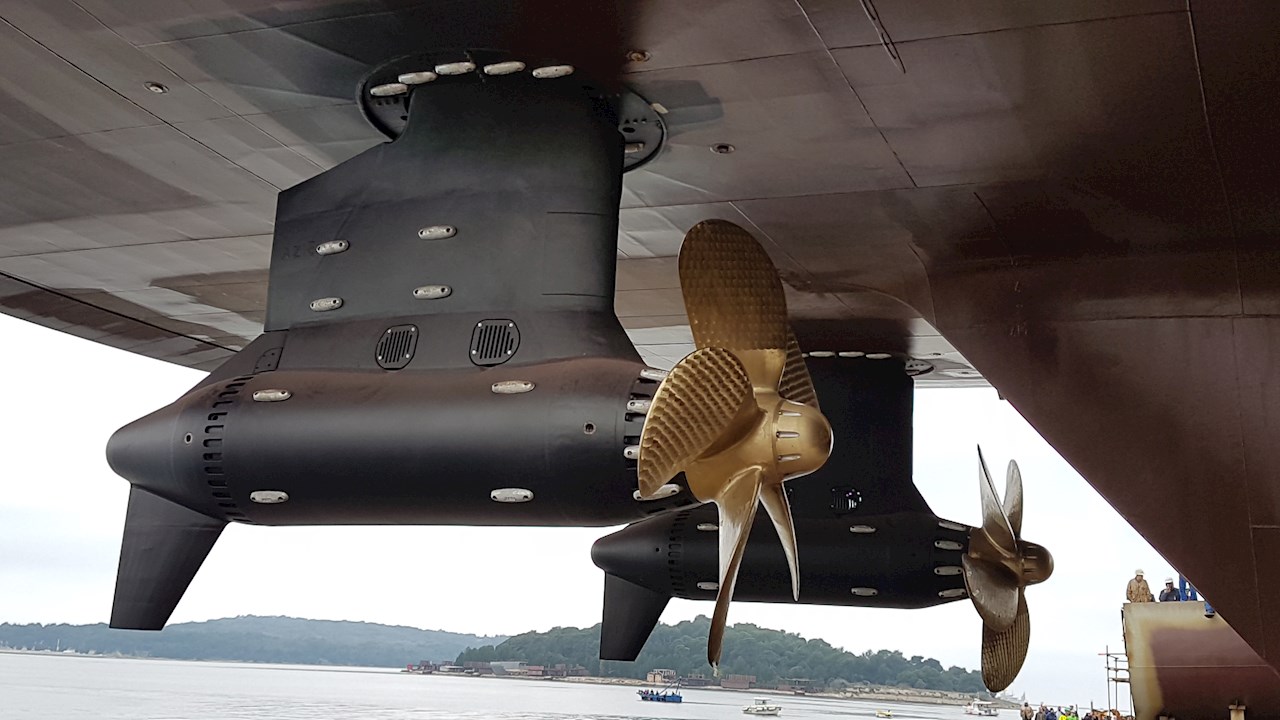
Availability by design for unmanned machinery
At any level in the total concept, the availability and reliability of all essential ship systems will be crucial for the acceptance of autonomous and unmanned vessels. The electric power plant is the necessary backbone for providing reliable and optimized power to propulsion, maneuvering and control systems.
In traditional ships with electric propulsion, availability has been achieved through redundancy. Such systems have been essential for the safety of passenger vessels, icebreakers, and offshore vessels with high requirements for safety using dynamic positioning (DP).
The system for an offshore vessel in Figure 3 is designed using a power plant with two sub-plants electrically connected at the main switchboards through the bus tie or transfer. These two sub-systems must be able to operate independent of each other. By increasing the number of sub-systems, the consequence of a failure will be relatively reduced, from 50% loss of capacity in a two-split balanced system, to 33% in a three-split (Figure 4), 25% in four-split and so on.
Image currently unavailable
Image currently unavailable
Image currently unavailable
Image currently unavailable
Image currently unavailable
Image currently unavailable
Figure 3 Figure 4
The traditional design is based on the assumption of onboard engineers able to identify and correct the failure and bring the vessel back to normal operation. Therefore the philosophy is to make the system tolerant for any single failure. In vessels with unattended machinery space, the crew can rely on the automatic alarm system for failure detection. In principle this means that they do not need to be in the machinery space at all times. Only when an alarm sounds do they enter the space to identify and solve the problem before resuming other duties.
Traditionally, radial power plants (Figure 5). have been used to simplify design and verification of protection systems. Lately, due to stronger focus on fuel consumption and emissions, the closed ring configuration has been used to allow for better efficiency and availability following a single failure.
Image currently unavailable
Image currently unavailable
Image currently unavailable
Image currently unavailable
Image currently unavailable
Image currently unavailable
Figure 5 Figure 6
In unmanned vessels, no crew is available to intervene and repair. In many cases, support can be days or even weeks away. Since a faulty part cannot be repaired or replaced, it will be necessary to redefine the rules for availability. One approach is to design availability by high reliability of critical components and availability through re-configurability to handle multiple failures (Figure 6):
- For components that cannot easily be multiplied, such as the main propulsors or dominant power sources, availability should be achieved by highly reliable components, i.e. with reduced probability of failures
- For other components, such as power distribution, the system should be capable of reconfiguring itself to continue operation with minimal impact on performance, operating in a fault-tolerant state following failures. Reconfiguration can be fully automatic based on predefined or intelligent algorithms, or done remotely from a shore control center.
Obviously, there will be a limit on the number of failures that can be accounted for, depending on the fault and risk analysis for the operation
In addition to radial and ring, more complex topologies could also be considered where the systems can be interconnected with star-points, or in combination with ring (Figure 7). This could in principle take place at each distribution level in the power plant, thereby creating multiple paths for energy flow from the sources to the consumers.
Due to their modularity, new energy sources and energy storage have a relatively similar efficiency and power density over a larger power rating. For increased availability, one option would be to design with smaller source/storage units. The different topologies mentioned can in principle be connected in any combination to achieve the required fault tolerance and reconfigurability. For the purpose of illustration, a conceptual design is shown in Figure 8.
Image currently unavailable
Image currently unavailable
Image currently unavailable
Image currently unavailable
Image currently unavailable
Image currently unavailable
Figure 7 Figure 8
Such alternative and advanced topologies still need to be evaluated before concluding on their feasibility. However, we will likely see a tendency in this direction. While conventional AC systems might be used as the infrastructure for the advanced topologies, Onboard DC Grid™ is the natural choice due to its ease and speed of connection.
Summary
The maritime industry is not far away from reaping the benefits of full digitalization, much as they were first envisioned.
ABB’s view of future ships is simple. They will be electric, digital and connected. First, the power train is electrified to utilize cleaner fuels and optimized design for the intended operation. The next step is to establish digital operations. This, in turn, enables the implementation of connected collaborative operations. Autonomous, and perhaps unmanned ships will enter fleets. The aim is not to eliminate crew, but rather to provide more added-value tasks for personnel to enable them to achieve more effective and safer operations.
An electric ship is more efficient, simpler, more flexible, more digital and better connected. Electric ships are also the natural platform for more intelligent, digital and automated shipping. Smaller and simpler systems, with less moving parts require less maintenance and supervision. Almost everything can be diagnosed remotely, and many faults can be fixed or bypassed automatically or remotely. The fully electric power train is already a viable choice for offshore support tonnage, as well as for smaller ferries and coastal ships that are most likely to become the first fully automated vessels in commercial operation.