Jukka Maattanen, Product Manager, ABB Ability™ OCTOPUS – Marine Advisory System, ABB Marine & Ports
World container port throughput grew from 36 million TEU in 1980 to exceed 800 million TEU by 2019, according to a forthcoming Port Economics, Management and Policy report by renowned industry analysts Theo Notteboom, Athanasios Pallis and Jean-Paul Rodrigue1.
These figures demonstrate how the container and its economies of scale have continued to drive globalization, and safety specialists also know that, while the number of containers that are lost over the side of ships each year is relatively small, in absolute terms it is a number that has also been on the rise.
With around 6-7 million boxes in transit on the water at any given moment, the estimated 1,500 containers that are thought to be lost each year is certainly of moderate proportions. That said, some of these losses can cause major incidents grabbing the headlines.
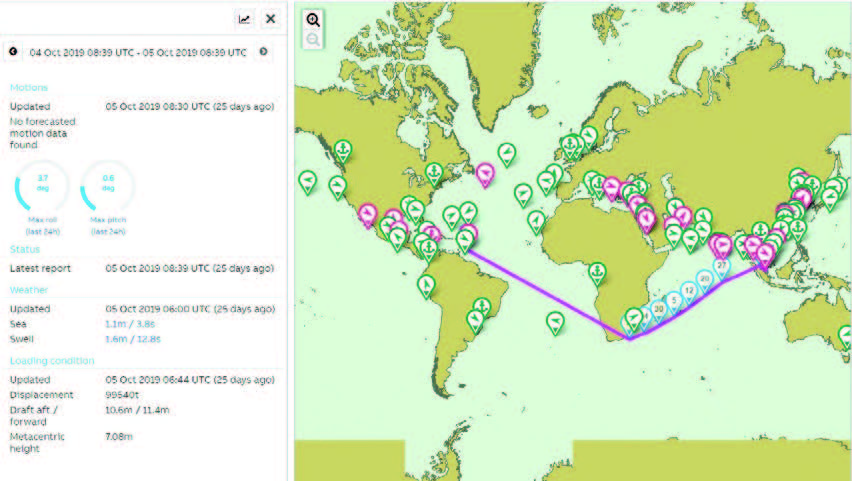
The consequences of any loss can be significant. Aside from the short-term financial costs, reputations are at risk. Environmental impacts can also be a major concern – particularly when the cargo in question is hazardous. Meanwhile, stray containers – whether afloat or on the seabed in shallow waters – represent a threat to navigational safety.
Today, closer attention is paid to the way cargo is secured than ever before, while rules to establish the weight of the cargoes being loaded into containers have also been put in place. However, while containers withstand compressive and shear forces, heavy weather can still bring extreme vertical loads that can cause structural failure at the bottom of the stack. Again, high lateral loads can break lashings and corner fittings, causing containers at the edges of the stack to topple over.
Reading the waves
Given that the forces acting on containers in the stack are a result of the ship’s responses to prevailing conditions, the ability to monitor and predict vessel motions offers a self-evident safety benefit for containerships. In reality, vessels are not rigid, and the vessel’s structure does bend due to the varying loads on the hull. In addition, accuracy can be limited in some calculations. However, when accelerations are measured at a minimum of three locations that are widely distributed over the vessel these limitations can be overcome. Motion monitoring of this kind may be used as a basis to quantify the risk of losing containers due to excessive accelerations in the wave conditions at the time of measurement. This is a key and well-established component of the ship operations performance management package ABB Ability™ OCTOPUS – Marine Advisory System.
If the ability to retrieve historical time series data on the accelerations at any container location on board is clearly useful when investigating an incident, and to ensuring current conditions are safe, the true value of monitoring becomes clear when motions and accelerations can be predicted – and data used to achieve safer operations.
Weather forecasts, which include information on sea states, are fundamental to predicting the motions of a vessel and the subsequent forces exerted on its cargo. With accurate insights into conditions at sea, shipmasters can avoid areas where vessel motions are likely to be most severe. Simply considering the height of waves may not be sufficient, however, as the distribution of wave periods and wave direction relative to the ship’s heading can have a greater impact on acceleration levels than wave height alone.
Interpreting a wave forecast with the aim of minimizing accelerations at container locations is clearly a task that is too complex to execute manually. Instead, protecting cargo against excessive loads is best achieved using an automated process known as ‘vessel response forecasting’, in which forecast wave conditions are translated into predicted vessel motions. Knowledge of how a ship responds in different sea states is essential to this process; accordingly, its motions in a range of wave directions, periods and heights are recorded over time – with vessel speed and loading condition also taken account of – and stored in a database.
Protective reach of OCTOPUS
It is the capability to support real-time decision-making in voyage planning and execution that has led heavy lift vessel owners increasingly to turn to OCTOPUS. In fact, ABB estimates that the system is currently utilized by around 90 percent of the semi-submersible heavy lift ships in operation worldwide.
In addition to providing users with detailed information about current conditions, OCTOPUS helps to identify the risks related to vessel motions when changing heading or speed. Motions such as roll and pitch are calculated for the full range of headings and ship speeds and compared with an upper limit. On the onboard display, red areas indicate conditions where at least one of the given limits is exceeded, while amber areas correspond to conditions where motions are acceptable but close to the limit; green areas signify favorable sailing conditions.
Vessel motion risk management of this type is already a powerful safety tool in the project cargo market, where heavy lift ships transport huge, unwieldy cargoes such as wind turbine parts and jack-up rigs. The sheer scale of these structures means that they are subject to far more extreme accelerations and stresses than are exerted on container stacks, no matter how ‘mega’ the container vessel.
References include all five existing project cargo carriers for Norwegian heavylift specialist OHT, which describes ship motion calculation and control as essential to its operations.
Even though project cargo voyages are meticulously planned in advance, rapidly developing weather systems at sea may require quick changes of plan. The sheer size of tripods, jackets and wind turbines themselves is only one issue. OHT’s clients often ask for the log of accelerations after a transportation, in order to assess the fatigue on the cargo. Furthermore, where in the past cargo transporters and installers were different parties, one company can increasingly be fulfilling both functions.
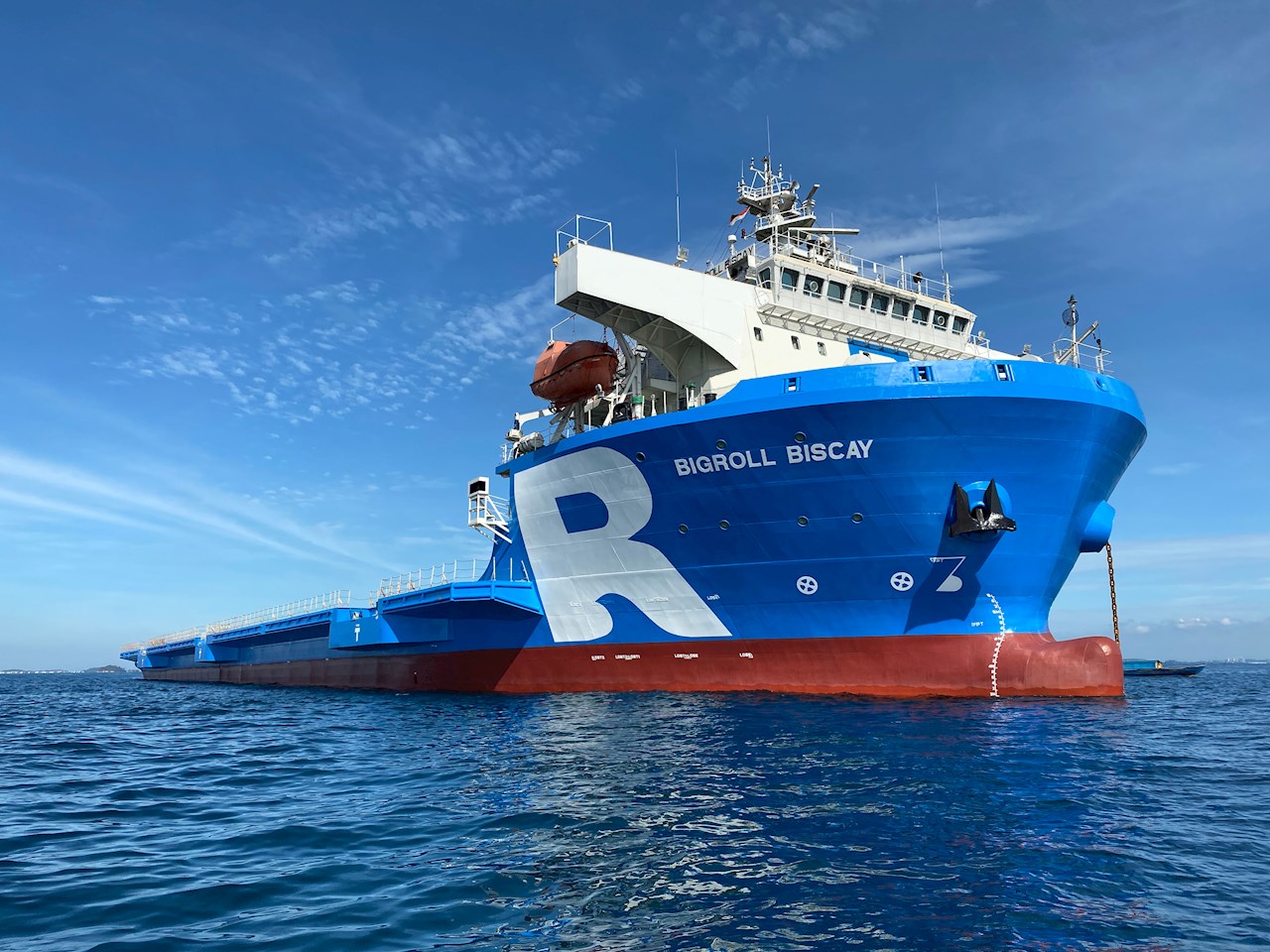
Dutch company Roll Group, meanwhile, has been using OCTOPUS for 10 years, with its latest ship BigRollBiscay deploying the solution to protect its high-value payloads. The 146-meter long, 12,285 DWT module carrier, which allows project cargoes to be rolled or lifted on board, has joined the Roll Group fleet in early 2020. The BigRoll Biscay order extends a relationship between ABB and Roll Group that has been developing since 2009, when the first contract for ABB Ability™ Marine Advisory System – OCTOPUS was signed.
Knowing which way the wind blows
Alongside improved safety, vessel response forecasting based on the OCTOPUS platform also brings efficiency gains. According to Roll Group’s senior project manager Joep Janssens, the solution not only ‘minimizes the environmental forces’ to which Biscay and its cargo are exposed but ‘decreases fuel consumption and helps cut emissions as a result’.
Furthermore, ABB’s ship-type specific expertise in hydrodynamics is ensuring that the attractions of OCTOPUS are ‘transferrable’ across a growing range of vessels. They include wind turbine installation vessels, where there is a direct relationship between minimizing vessel motions and maximizing the operational window. A forthcoming vessel for Louis Dreyfus Armateurs will be leveraging OCTOPUS as it serves the world’s largest offshore wind farm, for example.
Image currently unavailable
Image currently unavailable
Image currently unavailable
Image currently unavailable
Image currently unavailable
Image currently unavailable
OCTOPUS user interface with indication of different heading sectors in red, orange and green providing assistance in voyage planning, minimizing the risk of cargo damage or loss The OCTOPUS Motion Monitoring function helps the onboard staff to take immediate action when maximum allowable motions and accelerations are exceeded
Again, OCTOPUS is also making a key contribution to the far-reaching European Union-backed ‘Project ATLANTIS’ research initiative to develop new wind energy fields in the Atlantic Ocean, one off the coast of Viana do Castelo, Portugal and another further out to sea. A newly developed OCTOPUS module will provide actionable insights to help onshore operators optimize the planning of missions from port to wind farm, cut transfer times between land and wind farms, and reduce vessel waiting time and working times on-site.
The new module will also take into consideration the operational limitations of the ship and personnel and assess deployment opportunities for remotely operated underwater vehicles (ROVs), unmanned surface vehicles and unmanned aerial vehicles. This is an industry first as it allows the user ashore to plan offshore operations according to the performance of the vessel, crew and equipment in the conditions they face. This is a significant step forward for remote decision making: in adverse weather or rough seas, a mission or an ROV launch could be aborted to save a wasted deployment or worse. There are clear benefits for safety as well efficiency.
Although the latest addition to the OCTOPUS suite was developed with ATLANTIS in mind, once more potential applications for the advisory extend beyond a single sector. ABB’s vision is to develop the module to serve multiple sectors, such as the cruise industry, where it could be used to plan short routes, and the offshore oil and gas industry to map supply operations for rigs and floating offshore units.
For an advisory software system also already selected to provide gangway safety on the accommodation vessel Edda Fides, the latest module confirms that, while OCTOPUS offers an immediate answer to shipping’s pressing container stack safety challenge, OCTOPUS would be able to assist in finding a smoother, safer and more efficient course for each vessel type.