Naveen Kumar Motion-Device Products, software tools Bangalore, India, naveenkumar.e@in.abb.com; Sunil Kumar S Motion-Device Products Bangalore, India Sunilkumar.x.s@in.abb.com
Thanks to a new platform, technicians, commissioning engineers, customers and distribution partners can now use a handheld device such as a mobile phone to access a world of information from their ABB drives, motors and PLCs by simply scanning a device’s QR code →01. The key is ABB Access, a responsive web application that links users to product-specific information, such as manuals, installation guides, and step-by-step instructions regarding commissioning and troubleshooting.
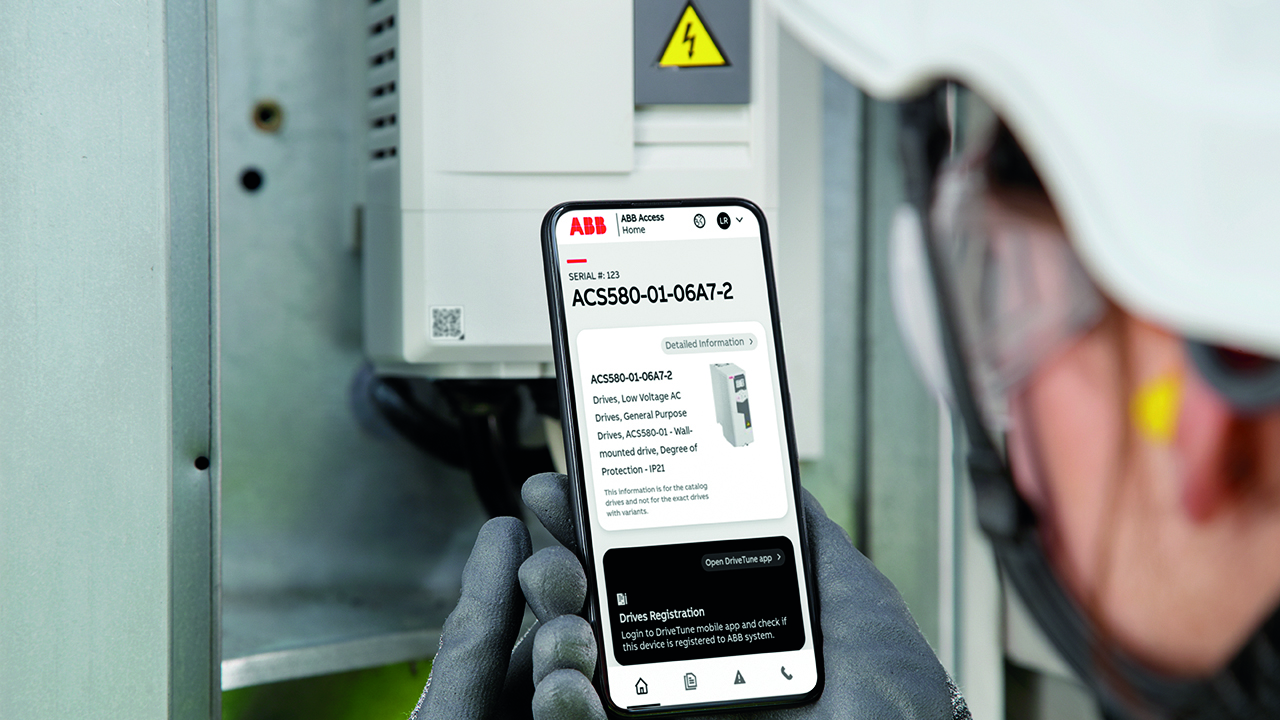
The responsive web application also allows users to rapidly and easily reach expert support from ABB to report and solve problems on-site. Furthermore, ABB Access complies with DIN SPEC standard 91406:2019-12, thus making it easier for OEMs and end users to read QR codes using commercially available hardware and software. The result is faster troubleshooting, which results in higher uptime and lower downtime, as well as a unified user experience across a range of ABB products. As the web application facilitates self-service, troubleshooting can be performed by any user with basic knowledge, thus allowing more bandwidth for experts to handle challenging issues. In addition, ABB Access helps to reduce users’ carbon footprint by avoiding hardcopy booklets, catalogs, manuals, hardware instructions, installation guides, etc. and by ensuring that the latest version of such information is instantly available, can be stored, secured and downloaded when needed to any authorized device.
A star is born
The new platform is the result of an extensive effort that included a QR code initiative and user interface design website prototype development. In this part of the project use cases were gathered covering areas ranging from system drives to motors and generators. At the same time, design and development of the QR code landing prototype was performed and early mock-ups of the web application were created with a view to understanding which elements should be prioritized and how to build the customer experience flow.
In late 2020 a working model was implemented. This enabled the flow of the customer experience from scanning a QR code to finding the correct documents pertaining to a target product type, reporting an incident, or finding the correct contact information for a specific site. Approximately one year later an initial minimum viable product was piloted and tested. This provided a foundation for the implementation of the product as well as a comprehensive set of requirements for future expansion. The product’s first release took place in early 2022.
How ABB Access works
The ABB Access web application is a channel for Motion Drives customers to access digital services through their everyday handheld devices. Scanning a QR code displayed on an ABB device connects the user to a page that offers relevant documentation, the possibility to report an issue to a product-specific organization and various other capabilities →02. Device-specific QR codes are included during the product-manufacturing phase.
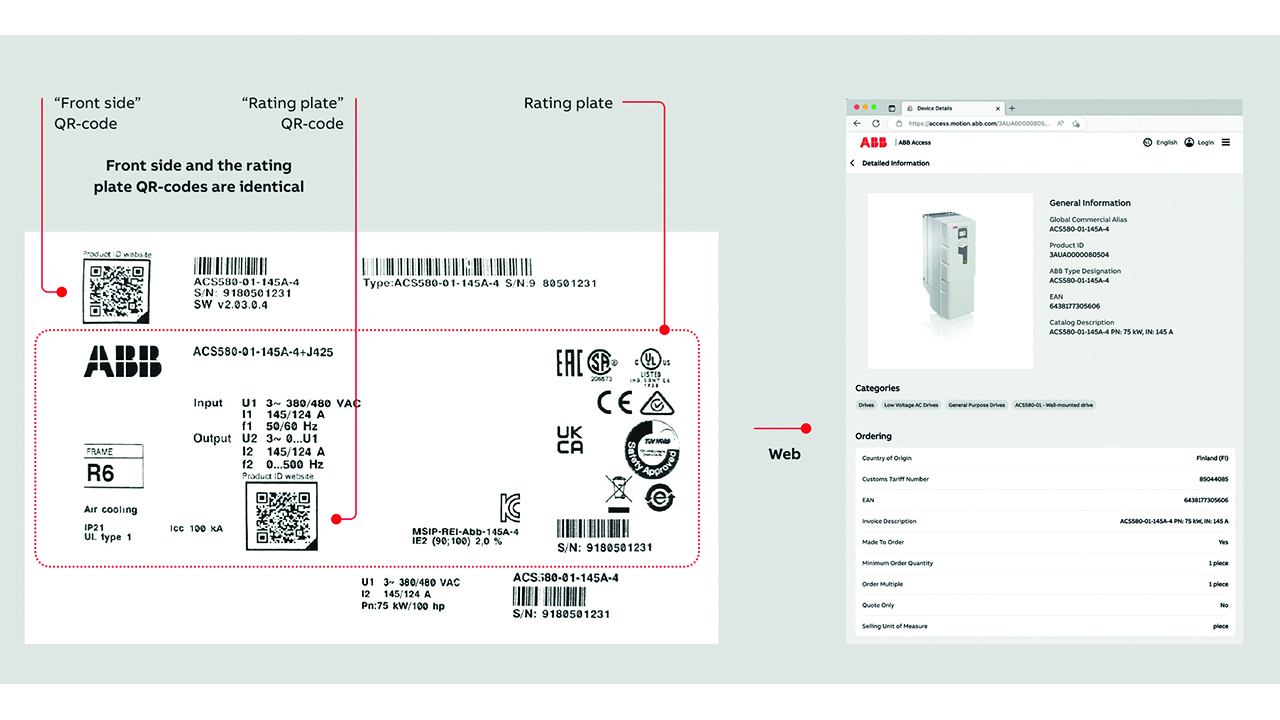
The application offers two types of user flows, ie, anonymous user flow and authenticated user flow. For the anonymous user, no authentication is needed. Authenticated users are identified using motion customer identity and access management (MO CIAM) based on Open ID Connect identity, which is built on top of the OAuth 2.0 protocol, an open standard for access delegation.
Although authorization is not applicable for anonymous users, authenticated users are provided with some extra information. For ABB internal users some additional documentation, such as electrical wiring diagrams etc., is visible. The web application itself is implemented using React frontend →03 running as an Azure App Service Static Web App, and a C# Dotnet backend running as Azure Function. The application communicates with the ABB knowledge base for device documentation and device manuals content.
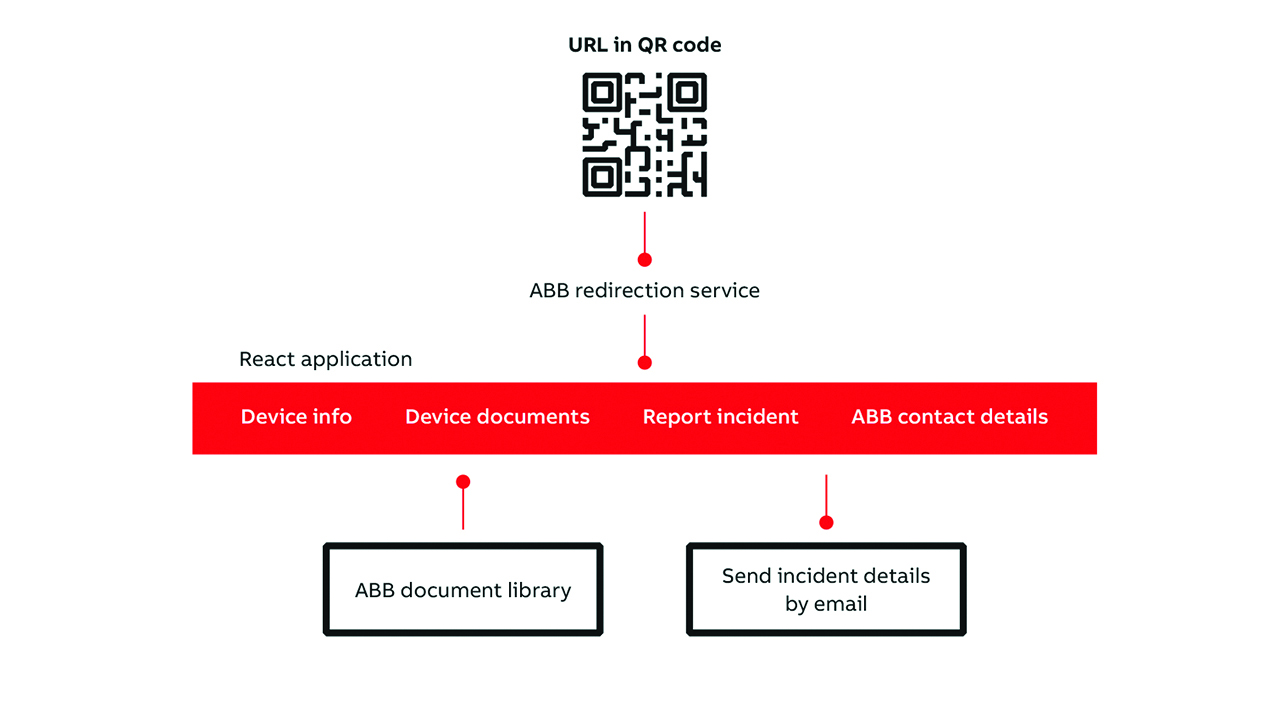
Further enhancements are planned for upcoming releases to provide data related to the installed base, product master, service events, incident cases, and project documentation. In addition, the application will communicate with asset lifecycle management (ALM)to receive data from DIB, MoR, ServIS, BOL, PowerTrain and other databases.
Architecture and security
ABB Access architecture →04 is based on a representational state transfer application programming interface (REST API). After scanning a QR code, the user is redirected to ABB Access using the Auto ID redirection feature →05. Data is then made available using a responsive user interface. ABB Access also communicates with other ABB internal data service providers by offering related information for different ABB products, all of which is in compliance with standard security policies and principles. Furthermore, ABB Access does not store any user information in its cache or databases, thus making it more reliable and secure.
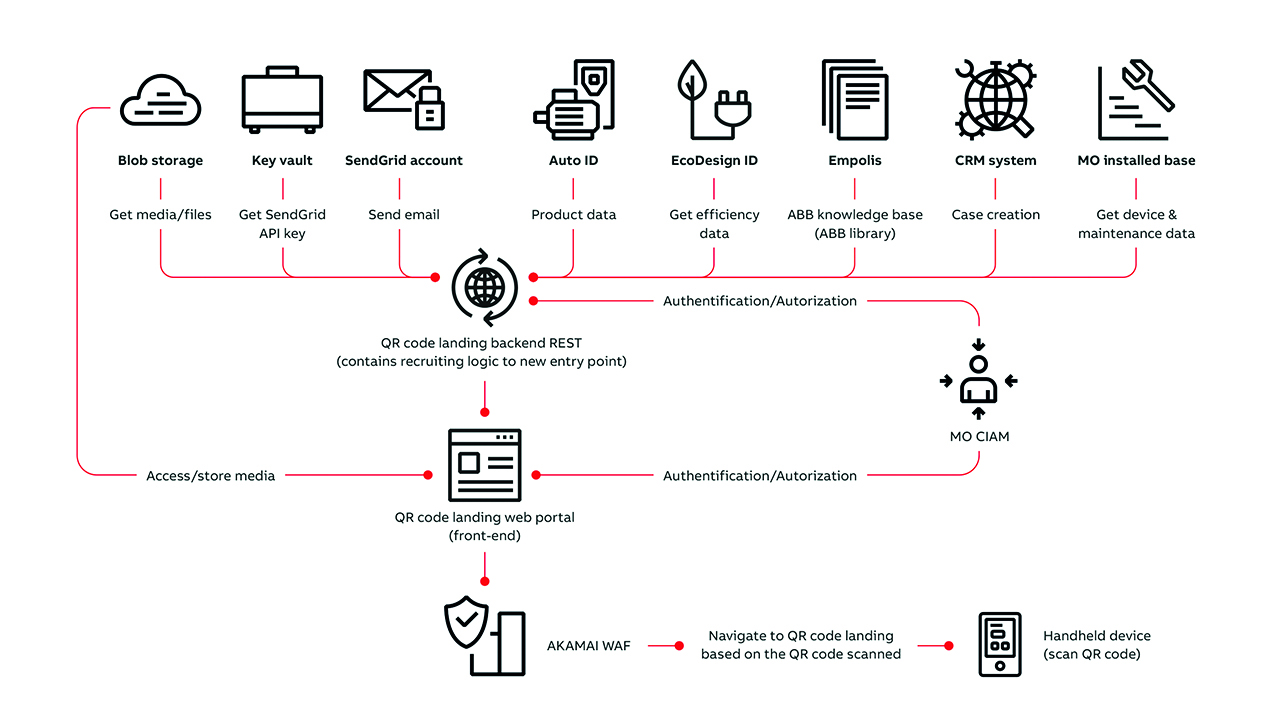
Security is based on the Akamai WAF web access firewall, which is designed to prevent cyber, phishing and cross site attacks, which might be caused by malware scams. In addition, before any major release to a production environment ABB Access undergoes DSAC, WAF, and WAS scans in order to detect potential threats or vulnerability issues.
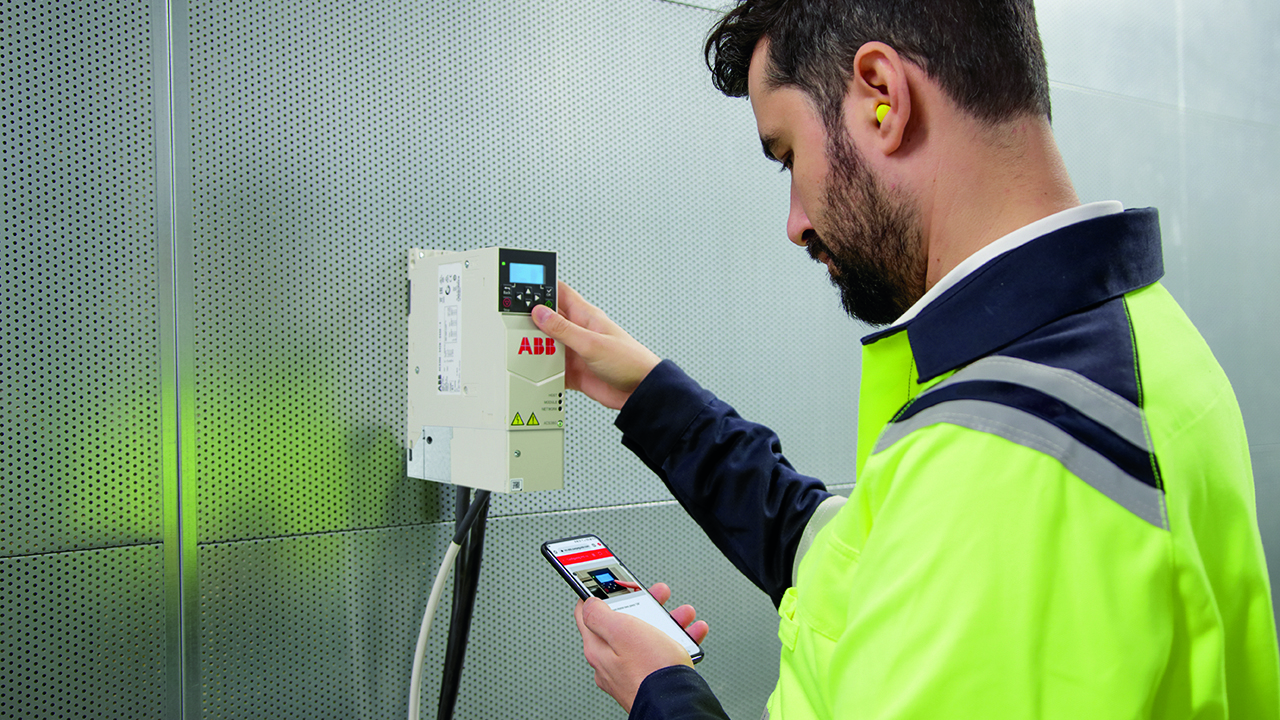
The Device Information Page: A world of data
At the heart of ABB Access are five key sections: Device information, Documentation, Troubleshooting, Contact information, and Maintenance →06. All are available in six languages: English, Chinese, Spanish, French, German, and Italian. The Device Information Page helps users easily find up-to-date product information. This begins by downloading ABB’s DriveTune Mobile app, which opens the door to wirelessly starting up, commissioning and troubleshooting the user’s drives by means of a mobile device. Here, a detailed information tab provides access to product catalog information, catalog descriptions, ordering information. Also shown are technical specification details, such as country of origin, Cn8 values, customs tariff numbers, EAN values, invoice descriptions, minimum order quantities, order multiples, quote only, selling unit of measures, eco design data, marketing descriptions, short and long descriptions, etc., along with additional information, such as product dimensional data, classification information and environmental information.
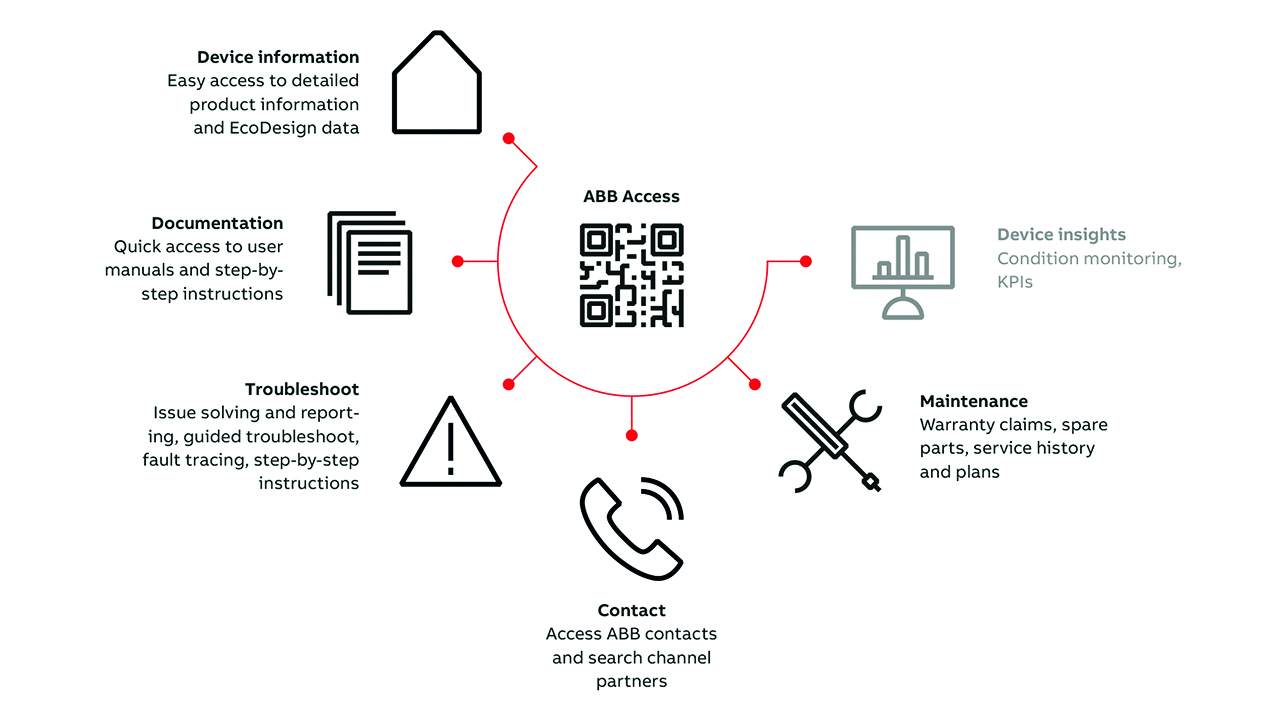
Documents page
The Documents page provides easy access to data and manuals for fast problem solving. Here, ABB SmartGuides →07 are one of the handiest ways to get short, clear visual instructions. Simple and animated step-by-step instructions assist with wall mounting of drives, electrical installation, and drive programming. The page offers an advanced document search tab that allows users to view lists of all applicable documentation related to the scanned serial numbers of products or devices. Associated documentation may include firmware manuals, hardware manuals, catalogs, standards, operating procedures, safety precautions, preventive and maintenance checklists, user manuals, related communication modules and installation guides.
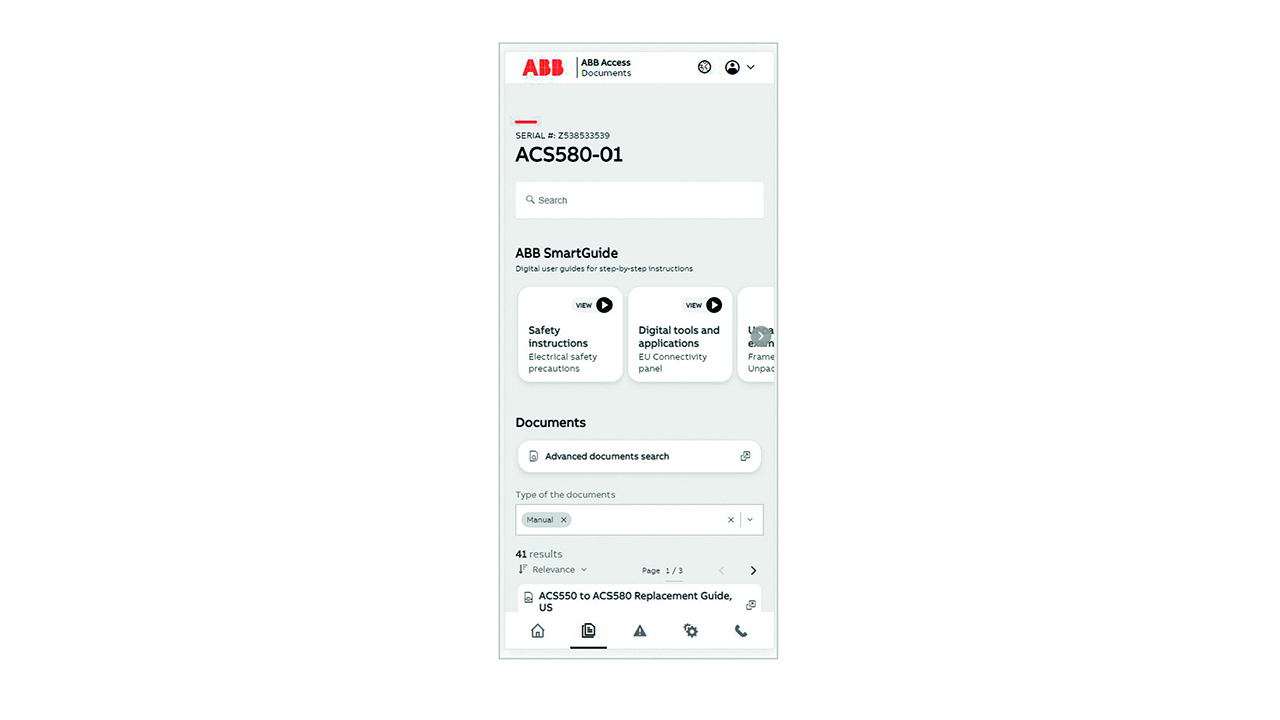
Troubleshooting page
The Troubleshooting page →08 allows users to access support from experts by reporting an issue and logging in to see a case history. Here, a step-by-step guided troubleshooting procedure can be followed to identify the root cause of an issue, contact ABB service representatives, or enter a fault code or warning code to identify the reason behind a fault or warning in a drive or PLC and take appropriate action to resolve it.
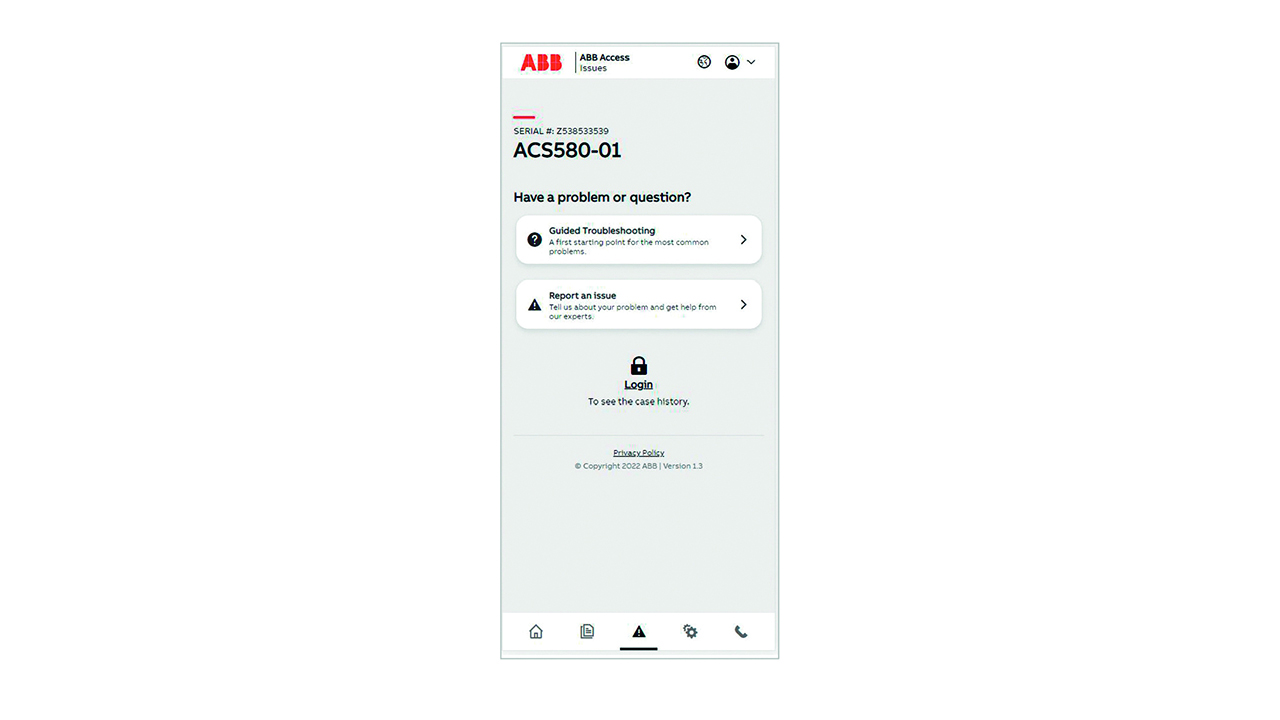
Contact page
The Contact page →09 allows users to reach ABB and service contacts, locate detailed, country-specific contact information, find channel partner networks, and discover ABB locations globally with contact numbers and email IDs.
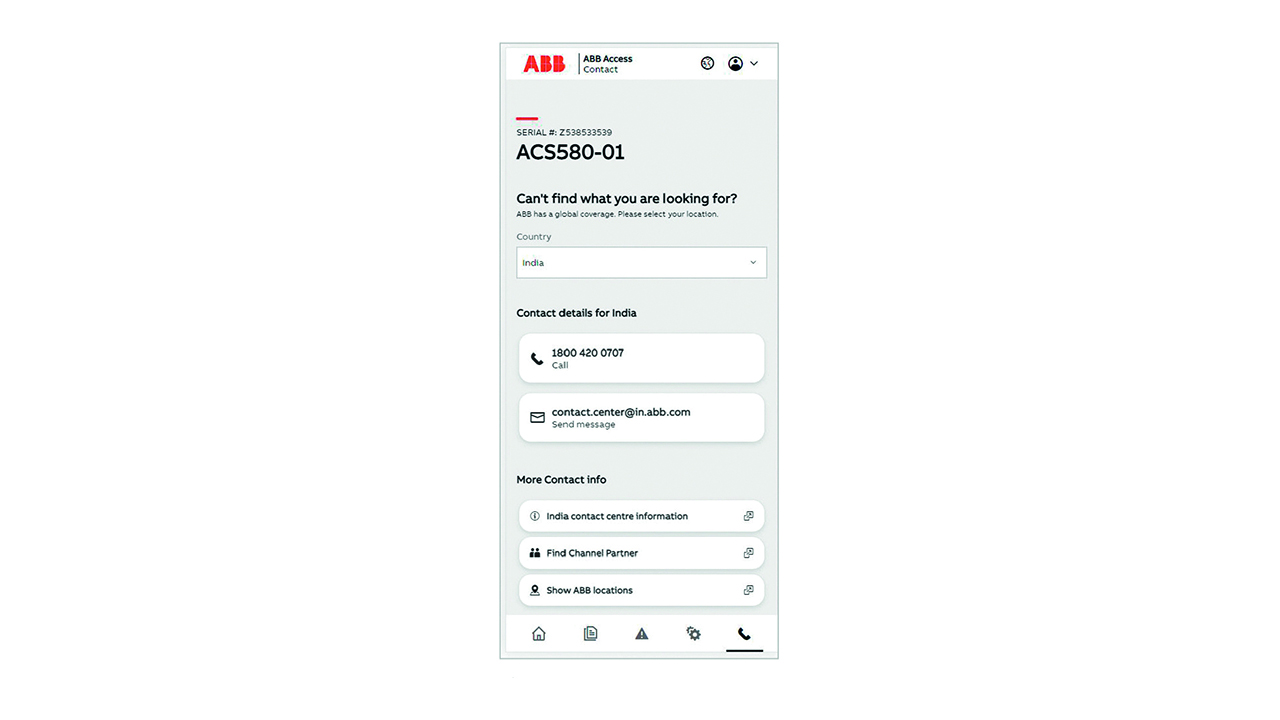
Maintenance page
The Maintenance page covers a wide range of information on ABB Motion products, including product maintenance history, warranty information, spare parts information, planned maintenance schedules, user classifications, digital passport gateway, and additional serial number-based information for special access users.
The number of ABB Access daily users has increased steadily. Since its first release in early 2022, the platform has logged 28,000 sessions, and the average number of daily users has been approximately 200. In fact, the platform has been so successful that plans call for it to soon begin covering other major business areas of ABB, which may include Industrial Automation and Robotics.
Further information:
https://new.abb.com/drives/mobile-tools/abb-access