“The AC500 is our water supply’s brain. It controls all of our numerous sensors and actuators,” comments Pipe Network Manager Uwe Maigler, who oversees Wendlingen waterworks’ technology.
In Wendlingen, eleven ABB AC500 Programmable Logic Controllers (PLCs) make sure that consumers have uninterrupted access to drinking water. Wendlingen waterworks, located in the south of Germany, has three pump stations, one water tank, three pressure boosters, and three water meter shafts. The AC500 is ABB’s most powerful PLC, providing many communication and I/O options. ABB offers special PLC libraries for the water industry. These water libraries enable the use of advanced pump functions, data storage, remote access, and reliable data transmission.
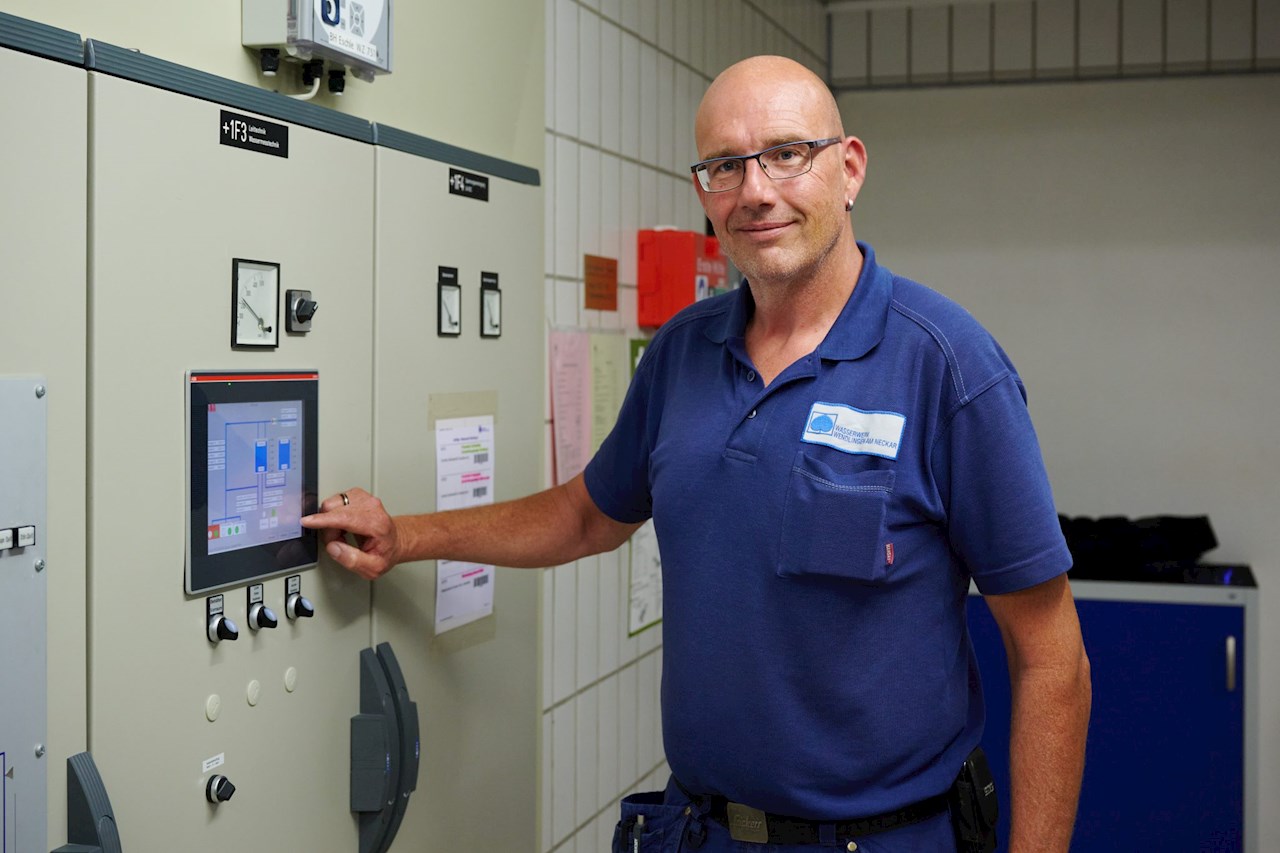
At Wendlingen waterworks the AC500 takes on central tasks in the water supply. At the pump stations, it allows adjusting the setpoint for the pumping capacity precisely. This is especially relevant for groundwater extraction as the groundwater must be gently extracted from the well to preserve groundwater levels and prevent damage to the well. The AC500 also starts the pump according to water demand and depending on the tank’s water level. In case of a pump failure the AC500 automatically switches the second pump on and transmits all notifications and errors to the control center.
In the pressure boosters, the AC500 helps maintain the target pressure of 5 bar, which is essential to prevent damage to the grid. Furthermore, the PLC measures and controls the water inflow, as well as the dosing of chlorine and phosphate in the water tanks. The turbidity of drinking water is also monitored. The AC500 ensures safe operation of the entire plant in the control center by communicating with the controls in the water tanks, the pump stations, and the pressure boosters.
Image currently unavailable
Image currently unavailable
Image currently unavailable
Image currently unavailable
Image currently unavailable
Image currently unavailable
Image currently unavailable
Image currently unavailable
Image currently unavailable
Image currently unavailable
Image currently unavailable
Image currently unavailable
The PLC AC500 at the Eschle water tank has to perform comprehensive tasks (Source: ABB). PLCs, such as those of the pump station Schäferhausen, are monitored via the control center (Source: Waterwork Wendlingen) Different generations of ABB’s frequency converters are used for pump control (left: ACS580, right: ACS550) (Source: ABB) The water tank Eschle has two storage chambers with an overall storage capacity of 5000 m³ (Source: ABB)
Just as comfortable as cruise control
Uwe Maigler compares the AC500 to the cruise control function in a car, ensuring a comfortable ride on the highway. Just like a cruise control system, the PLC constantly adjusts settings in the waterworks to ensure safe water supply. “Compatibility is the AC500’s unique selling point. The PLC can communicate with anything, whether it’s an automation component from another manufacturer or an analog device, such as analog dosing pumps for chlorination systems. All it takes is an additional module, which can convert the analog signals into digital ones.”
A decisive point was also the AC500’s relatively short delivery time, as the PLC is manufactured in Germany. To be on the safe side, Maigler still keeps all the spare parts for the PLC in stock, including a CPU, just to be able to react immediately should there be a defect on the weekend.
ABB’s wide range of technology
ABB’s distributed control system Symphony Plus provides detailed insights into the waterworks. The DCS connects about 1.000 data points in the plant, which are visualized in 15 process images. An integrated remote alarm system, equipped with SMS messaging and Voice over IP speech synthesis, ensures that error and emergency messages are sent securely and quickly to the correct members of staff. The ABB service team performs remote maintenance via remote access technology which meets the requirements by the German Federal Office for Information Security (BIS). As remote maintenance is highly flexible, the plant can be ideally monitored, configured and controlled.
In 2008, Symphony was the first ABB distributed control system to be implemented and the entire water supply was digitalized. The DCS is used for collecting and archiving process data, and for operating, archiving and managing remote access. Eight years later, the DCS was upgraded to Symphony Plus Operations and History. Said system received an update to version 2.2 in September 2022, which represents the current state of the art.
Programmable Logic Controllers and the distributed control system aren’t the only ABB technology at the waterworks. The automation specialist also provided control cabinet technology, frequency converters for the pumps, and instrumentation technology. The Wendlingen waterworks and ABB have been partners since 1996.