As an important global textile machine manufacturer, Dilmenler Textile Machinery supplies textile producers in numerous countries around the world with dyeing and finishing equipment that they can count on to work efficiently. Dilmenler, which is headquartered in Istanbul, Turkey, makes a wide portfolio of machines for textile processing steps such as dyeing, centrifuging, drying, heat-setting, cutting, slitting, compacting, coating, and packaging. Their production facilities consist of 10 halls covering a total area of 85,000 m2 where the machines are built and tested, prior to delivery to customers.
Partnership is the vision
Dilmenler’s vision is based on establishing close partnerships with their customers, to be close enough to attend to their requirements right away with fast solutions, when needed. The main aim is not only to provide the highest quality and latest technology equipment at favorable prices, but also to be there to assist customers at every step, helping them to solve any problems that may come up in the dyehouse and textile finishing process.
Dilmenler has a continuous research and development program aimed at improving existing products and advancing new dyeing technology. All machines are built to meet the requirements of their customers, and Dilmenler possesses all the major pressure-safety certificates such as ASME and CE.
To test its new technology and improve the machines it builds, the company has an operating Research and Development (R&D) dye house. The goal is to reduce their customers’ production and energy costs, and also to provide consulting and advice regarding chemicals, dyeing processes, and costs in general.
Looking for mutual benefits from a drives and PLC supplier
“More than a decade ago, Dilmenler began working with ABB by using their variable speed drives (drives) in their textile machinery,” explains Umit Kahraman, Global Segment Manager, Machinery, at ABB Drive Products. “Prior to that, the company had been using a different drives supplier but was looking for a new provider that would not only sell them equipment but also partner with them on a higher level to make better textile processing machinery.”
Dilmenler’s aim was to find a trustworthy drives supplier who could deliver a whole range of solutions, depending on the specific needs, and eventually become a close partner with which they could develop projects together and share information for the developments. In this manner, there would be mutual benefits for both sides, as Dilmenler would be able to develop and perfect their machines faster and ABB would be using its combined domain expertise and efficient motion control technologies to support this key customer.
For Dilmenler, ABB and their trusted channel partner Halici was the ideal partner based on the wide range of drives, PLCs, and customization packages it could offer, as well as the application expertise support and various tools it has for machine design, building and commissioning. In addition, ABB’s global scale made it highly capable to enter into such a close relation with a leading machine builder.
The cooperation has developed nicely, step by step
As the cooperation has grown, ABB has created tailor-made, drive-based software solutions for Dilmenler drives. The software is installed on the drives at the ABB factory, before they are delivered to Dilmenler for installation and commissioning in their machines. In this way, the time and effort necessary to program and start the drives and machines is substantially lower than before. And it also ensures correct programming of the drives, which in turn minimizes room for mistakes.
ABB supplies machinery drives, general purpose drives and industrial drives to Dilmenler machines. They also supply AC500 PLCs with related Human-Machine Interface’s (HMIs). Dilmenler constructs their own drives cabinets since it has a production unit that can make up to 50 cabinets at the same time and then install the ABB drives into them. So, the combination of textile machinery, drives and PLCs that are controlling them can all be built at Dilmenler, ready for delivery to customers around the world.
They help our machines to work perfectly, all over the world
Mr. İsmail Şengüller, General Manager at Dilmenler, states: “We began partnering closely with ABB many years ago, to get the best automation solution to make our machines work perfectly. From the very beginning we were impressed by the total value ABB offered to us and to our customers. This was not only due to the most comprehensive drives-motors-automation solutions it has, but also because of ABB’s willingness to offer its extensive application knowledge and on- and off-site support – which is definitely a key to our trusted partnership. Dilmenler machines are running all over the world, so in case we need support we know who to contact and get the best assistance quickly. This is why we appreciate working with professionals from ABB and their wide range channel partner network.”
“Our customers expect reliable, high-uptime operation from our machines,” continues İsmail Şengüller. “To do this, ABB drives and PLC products as a complete solution have gained the trust and confidence of our technical department. They are very happy with the ease of use, adaptability, technical features and flexibility. Our customers also like ABB products because the textile industry is so energy dependent. ABB’s approach that focuses on energy efficient solutions provided by the variable speed drives gives the textile industry very meaningful ways to get both cost savings and environmental benefits at the same time.”
Supporting the success of textile industry operations
Making sure your customer is happy is always a key aim, and when they are, you have certainly succeeded. One of Dilmenler’s pleased customers is Megam Textile Dyeing company in Tekirdağ , Çorlu, Turkey.
Megam Tekstil was established in 2009 as a full capacity knitting-fabric dyeing facility for the textile industry. The industry is always under time pressure for deliveries, due to fast changing fashion trends. This is a big challenge and there is absolutely no tolerance for any troubles which can cause the textile operations to stop or be interrupted, resulting in very costly lost time.
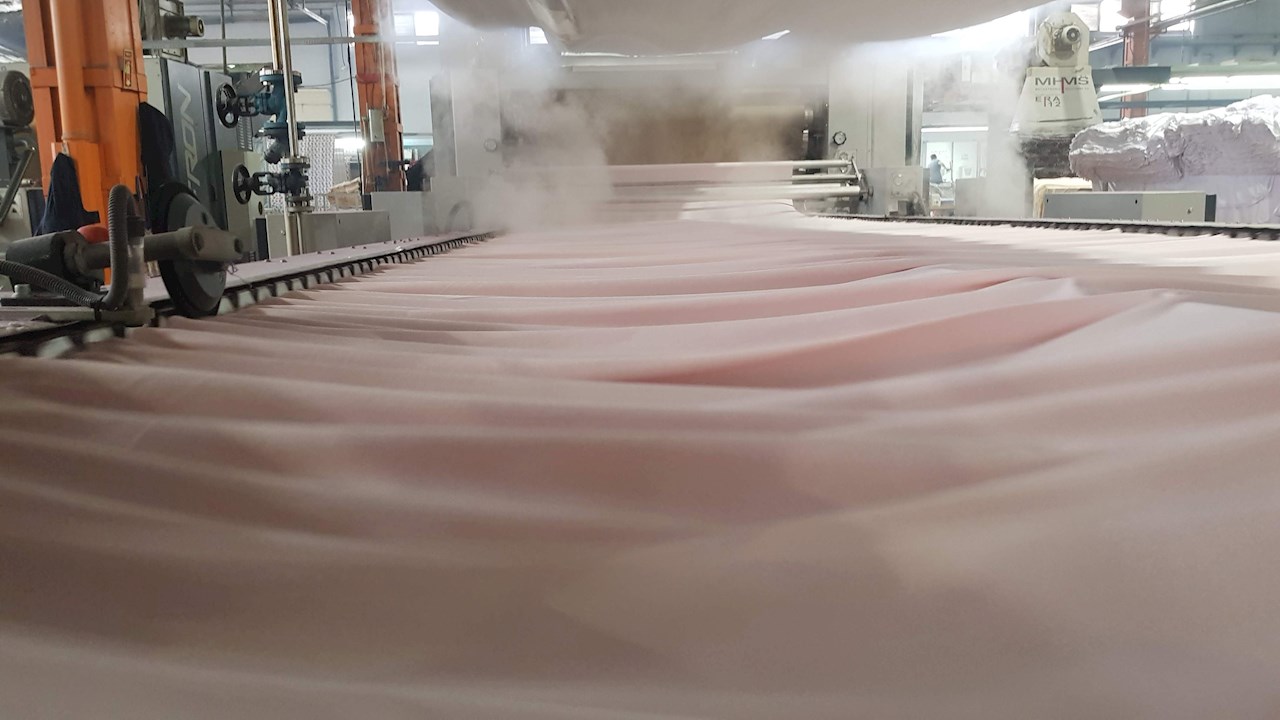
“We have a continuous challenge to meet precise time schedules, to deliver fabrics to our customers so they can go to market exactly when needed,” says Mr. Kaan Kalıpçıoğlu, Factory Manager at Megam. “Therefore, we must always keep operating efficiently. And a second big challenge is energy prices, where we must always improve to stay competitive.”
“To help us meet these difficult challenges,” continues Kaan Kalıpçıoğlu, “Dilmenler has been our biggest machine supplier for years. We were very careful before we decided to buy from Dilmenler. Ultimately, we chose them due to their deep expertise in the textile industry and also many recommendations from other companies that depend on and trust their reliability and technology.”
“By using Dilmenler machines we have decreased our downtime much more than expected. Besides keeping our production running smoothly, with few headaches, this also has important secondary effects, since by optimizing efficiency and productivity, we also help to achieve our energy efficiency goals and cost targets.”
Ensuring energy efficiency and uptime
The fact that Megam always strives to be operating efficiently with high uptime and low energy expenses is something that any textile maker is likely aiming for as well. By using Dilmenler dyeing and finishing machines, which are in turn supported by ABB’s drives, PLCs and worldwide channel partner and service organization, plays a crucial role in achieving those aims