The integration and programming of robots represent a major part of any company’s investment in automation. With this in mind, ABB’s RobotStudio® [1] [2], the world’s most used offline programming and simulation tool for robotics, includes software that can be used to design, test and refine entire production cells in the virtual world, thus opening the door to a dramatic simplification of how robots are programed and operated. The most recent addition to the RobotStudio platform is RobotStudio Cloud, which enables individuals and teams to collaborate in real time on cell designs from anywhere [3].
Magnus Seger Simulation Software Göteborg, Sweden, magnus.seger@se.abb.com
Boxes are stacking up, space is tight. Time is short. Wouldn’t it be nice to have robots that could just be told what to do without any ifs, ands, or buts? Although commissioning and assigning new tasks to robots is still far from simple, RobotStudio®’s desktop version makes it possible for users to do programming and simulation offline without disturbing ongoing production. Furthermore, RobotStudio®’s Augmented Reality Viewer app [4] enables users to visualize robots and solutions in a real environment or in a virtual room on any mobile device for free. In addition, associated software and applications enable teams to accelerate decision making and speed up the design and commissioning phase.
Offline programming and visualization offer an ideal path to maximizing return on investment for robot systems; these techniques reduce risk and errors while eliminating downtime by programming outside of the production environment. Widely used by companies throughout multiple industries, ABB’s RobotStudio® presents a wealth of possibilities for programming, designing and testing robots in a virtual environment. Below are ten examples of how it can boost customer facility performance [5] and enhance production.
Cable simulation
Designing robot cables and dress packs can be a challenge. Designers must consider the fact that the cables connected to industrial robots can undergo extensive wear and tear, resulting in a growing risk of collisions. With this in mind, RobotStudio offers cable simulation, enabling engineers to visualize →01 the movements of robots and their cables before implementation, thus reducing collision risks and increasing cable life span.
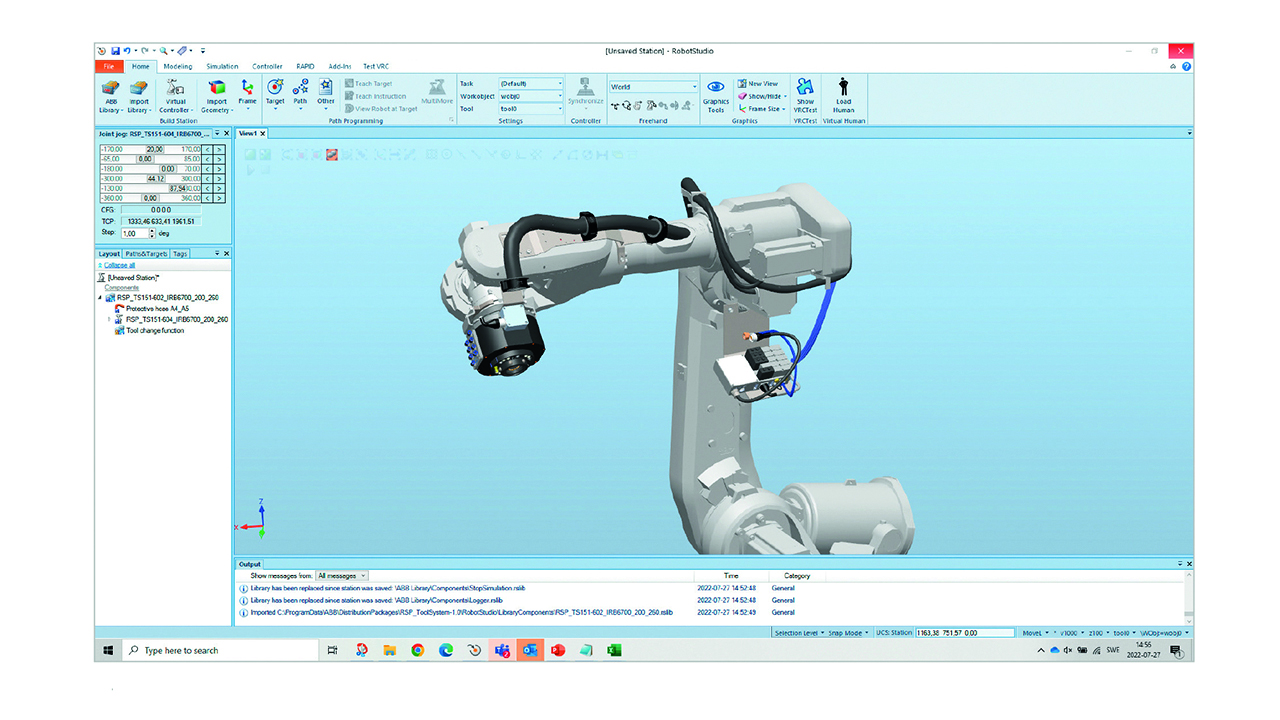
Swept volume
Figuring out the space that a robot requires to perform an operation can be tricky. This can make it difficult to predict how multiple robots might work with each other in a tight space, and where to set up fences and other boundaries where humans and robots intend to work together. RobotStudio can automatically and precisely calculate the swept volume of a robot and its tooling, covering the motion of the robot program. This can help to provide precise recommendations for where to place fences and safety zones, enabling automation process managers to prevent clashes, interferences, and potential accidents during actual production.
Signal analyzer
When retrieving, visualizing, and reviewing motion signals and I/O signals from a robot controller, these signals must come in the correct order. They must also have the correct time stamp to guarantee precision when tuning and optimizing the robot program, with the data received from real and virtual controllers. This data is required from both the real and virtual robot controller to establish why a robot cannot reach a programmed speed, or how quality is being affected by slight adaptations or speed drops. Additionally, analyzing energy performance and efficiency during a cycle, and how variables can affect energy use, is becoming increasingly important for users.
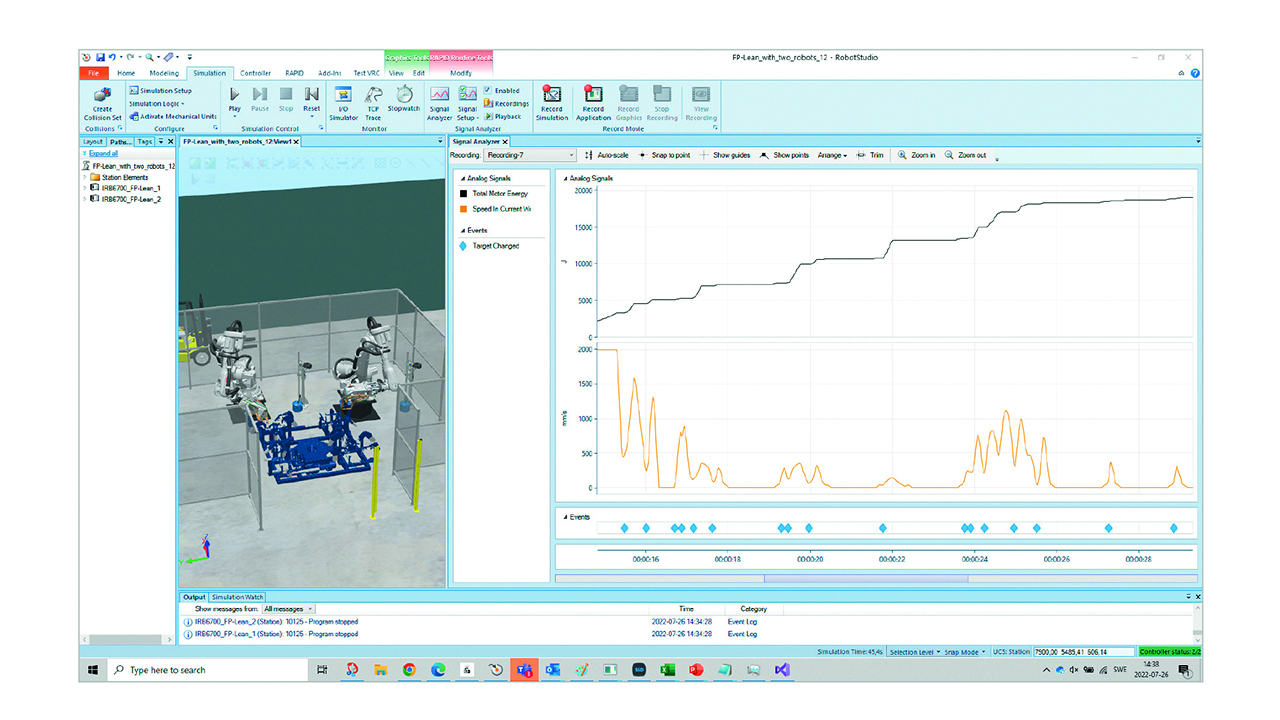
RobotStudio’s signal analyzer →02 allows users to record and display all signals from a robot controller (real or virtual) in one view. The dashboard allows users to optimize and adjust parameters with ease. Robot speed, power consumption levels, I/O signals, tool-center point (TCP) positions, joint values and more can all be recorded. By using the “go to” program or visualization, issues in the program can be identified with just one click.
CAD to path
Using a handheld device and joystick on the shop floor when moving a robot to the correct position to create a robot program is extremely complicated and time consuming. Usually, this will stop ongoing production and result in suboptimal targets. However, by using a CAD-model of a part, it is possible to automatically generate a robot’s positions on the edge of a shape.
In seconds, this will create perfectly oriented targets along the edge, which would have been otherwise cumbersome to achieve online by jogging and teaching the targets with a robot. RobotStudio’s Auto-Configuration feature helps users to automatically define an optimized robot arm configuration for the complete path with just one click.
Jobs
Keeping an entire fleet of robots updated and running consistently is challenging. Traditionally, each robot would require operators to update and validate the installation manually, which is extremely time consuming. In the commissioning phase there can be multiple updates and changes happening at the same time. This makes it almost impossible to get an overview of which robots are installed and ready to go.
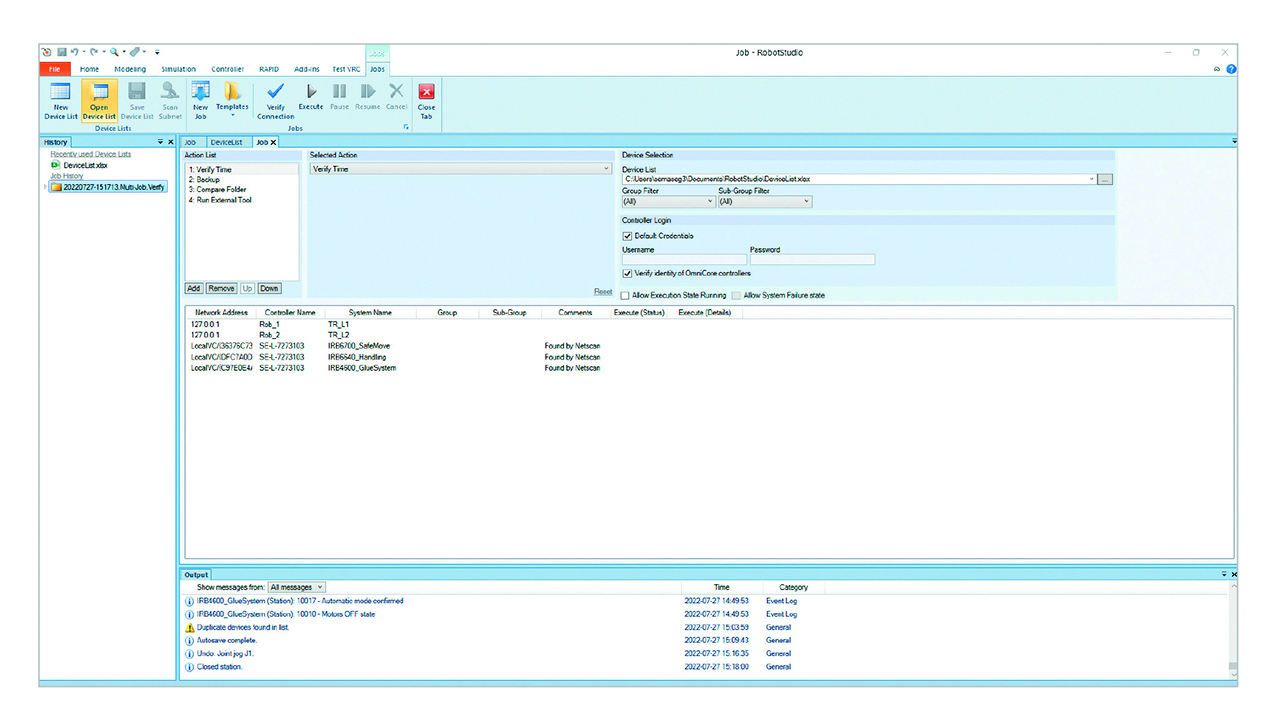
In view of these challenges, RobotStudio’s Jobs feature →03 permits simultaneous operation on a large population of robot controllers in a factory, simply by connecting them to the factory’s network. There are several actions that can be carried out, including backups, synchronizing the time on each robot, reading of RAPID data, updating user rights, retrieving system data, and sending them to external programs like Excel for further analysis, and much more.
Automatic path planning In a tight and crowded robot cell that contains a lot of equipment, it can be a highly complex and time-consuming task to create every robot movement, while also considering every obstacle on each movement path.
RobotStudio’s automatic path planning feature →04 obviates the need to program all the steps to the final desired position. Instead, only the final position needs to be given, and the robot will swiftly follow a path that avoids all obstacles in its movement path automatically. This feature enables a collision-free path from start to finish within seconds, speeding up the engineering phase and time-to-market.
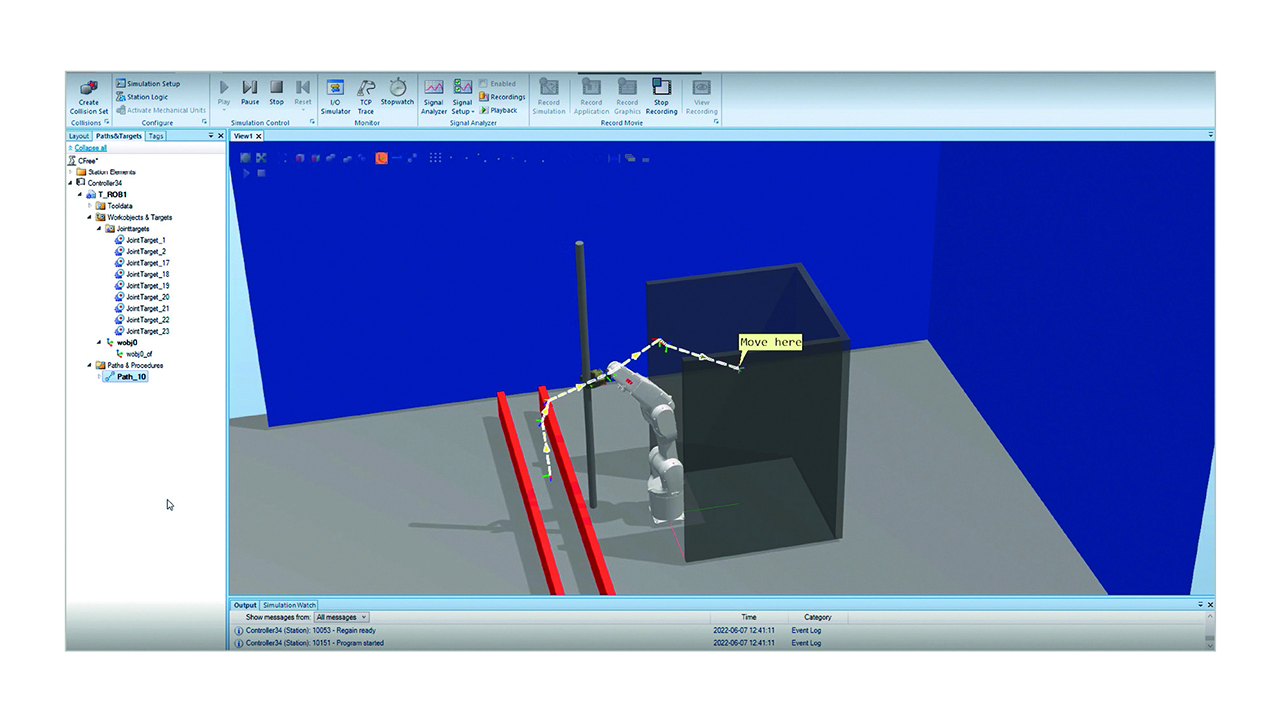
RAPID editing and debugging
Creating robot programs on a teach pendant is not ideal and typically requires downtime. This can be carried out on a PC or third-party simulation tool that emulates the robot code, however, this does not always provide sufficient context, nor does it allow testing and debugging of the program.
With RobotStudio’s text editor, programs loaded into a robot can be viewed and edited either live or virtually. The editor features syntax and error highlighting, tooltips, automatic insertion of arguments, and context-sensitive help for robot instructions. There is also a data editor that allows tabular editing of the program data. The program can be debugged by setting breakpoints, while numerous other variables can also be monitored.
Station viewer
In the discovery and planning stage it is important for the supplier to be able to explain and communicate the proposed solution so that both the customer and the supplier are aligned, thus ensuring effective cooperation and collaboration. This is traditionally done by exchanging reams of documents, which are typically not easy to interpret and understand – a process that often leads to project delays and misunderstandings in the team.
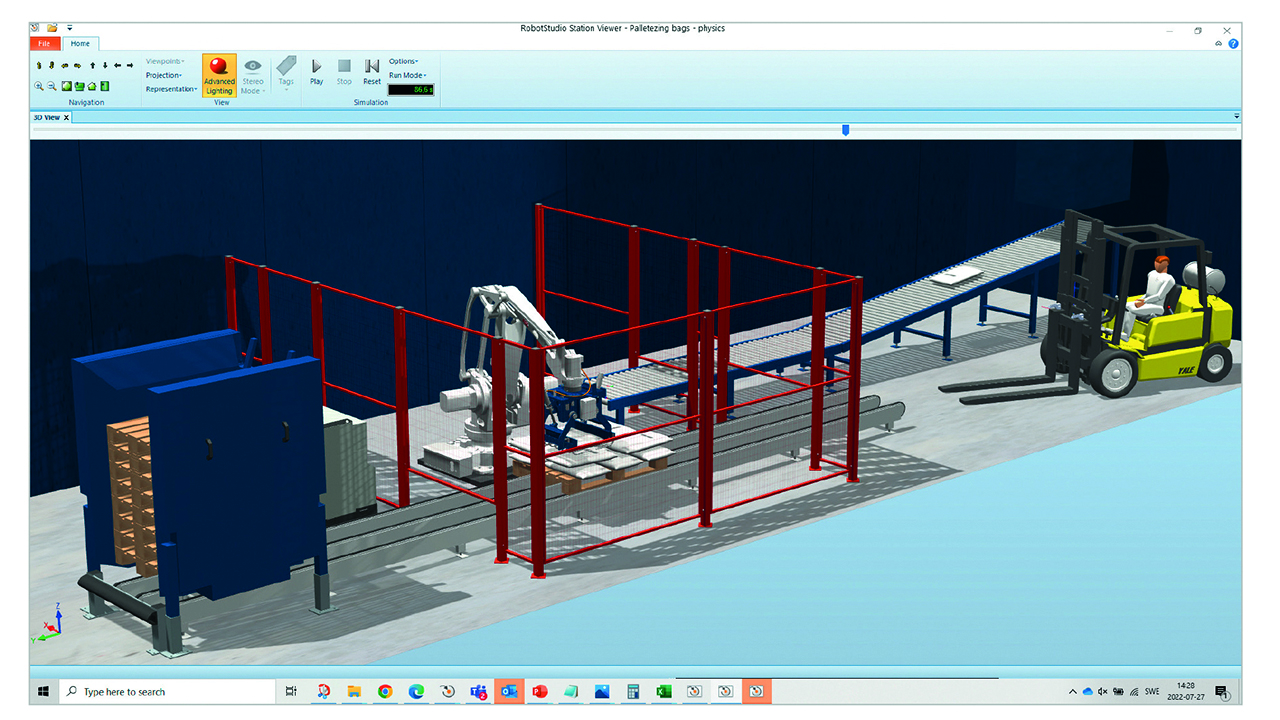
Station viewer →05 is a 3D interactive movie package for showing and sharing a RobotStudio simulation to users who do not have the software installed. The package displays realistic graphics with accurate tooling, movements, and throughput, providing a better understanding of proposals and adjustments. The package also makes it possible to view projects in virtual reality, simply by plugging the headset into a computer.
Path editor
Updating programs online is usually carried out through the teach pendant. However, editing multiple instructions or the complete process path can lead to errors and is a cumbersome process. It can also be difficult to achieve an accurate grasp of the necessary direction to move the positions to get the correct update of the targets. Furthermore, it can be difficult to go back and correct errors without losing previous edits.
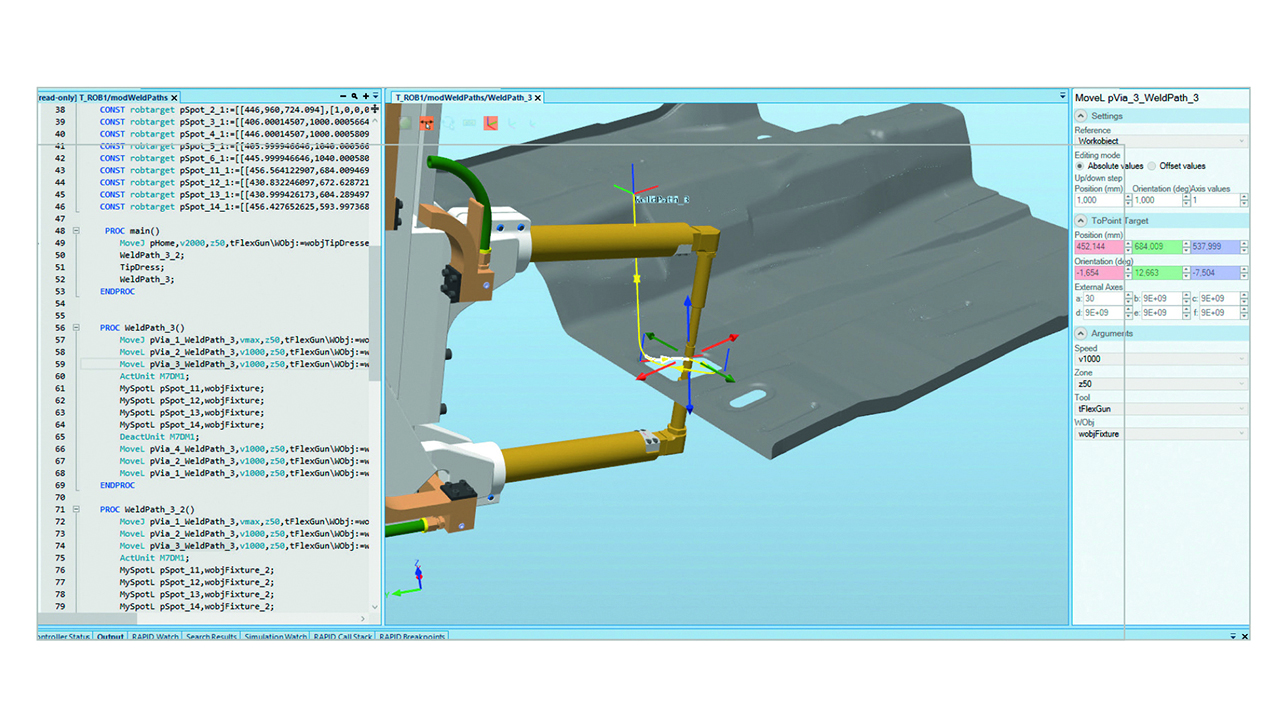
RobotStudio’s RAPID path editor →06 enables 3D views and ways to edit programs loaded into the robot controller, allowing users to edit individual or multiple targets at the same time, while the program is automatically updated. All changes can be undone before being loaded into the robot.
Virtual controller
Getting a system updated and running on the production floor can be time consuming and costly, particularly if easier options are available. Traditionally, offline programming systems have been used, but simulations are by their nature imperfect and do not always reflect reality.
Image currently unavailable
Image currently unavailable
Image currently unavailable
Image currently unavailable
Image currently unavailable
Image currently unavailable
07a Simulated production floor. 07b Actual production floor.
07 Robot controller provides an exact copy of the real software that runs robots on the production floor.
RobotStudio’s virtual robot controller →07a, 07b is an exact copy of the real software that runs robots on the production floor. It therefore provides more realistic simulations, using real robot programs and configuration files identical to those used on the shop floor, including safety zones. The virtual controller allows users to be fully confident that what they see in the program is what they will be getting on the shop floor. •
References
[1] RobotStudio® Suite. Available: https://new.abb.com/products/robotics/robotstudio. [Accessed January 15, 2023.]
[2] RobotStudio®. Available: https://new.abb.com/products/robotics/robotstudio/robotstudio-desktop [Accessed January 15, 2023.]
[3] https://new.abb.com/news/detail/97646/prsrl-abb-robotstudior-takes-to-the-cloud-enabling-real-time-collaboration
[4] RobotStudio® AR Viewer. Available: https://new.abb.com/products/robotics/robotstudio/ar-viewer-app [Accessed January 15, 2023.]
[5] Customer stories. Available: https://new.abb.com/products/robotics/customer-stories [Accessed January 15, 2023.]