Georg Gutermuth, Bernhard Primas ABB Corporate Research Ladenburg, Germany georg.gutermuth@de.abb.com, bernhard.j.primas@de.abb.com; Jan Bitta ABB European Operations Centre Ostrava, Czech Republic, jan.bitta@cz.abb.com
Hydrogen, the simplest and most abundant of all molecules, holds the potential to help solve one of the most complex problems the world faces today: climate change. Hydrogen is an energy-efficient fuel, clean and storable and – after many years of stop-start progress – has picked up unprecedented momentum, driven by the urgent need to decarbonize society. Substantial investments are being made to achieve this goal.
Hydrogen fuel technology is advancing rapidly, propelling efforts to scale up production to the magnitude needed to satisfy a world striving for “net zero” →01.
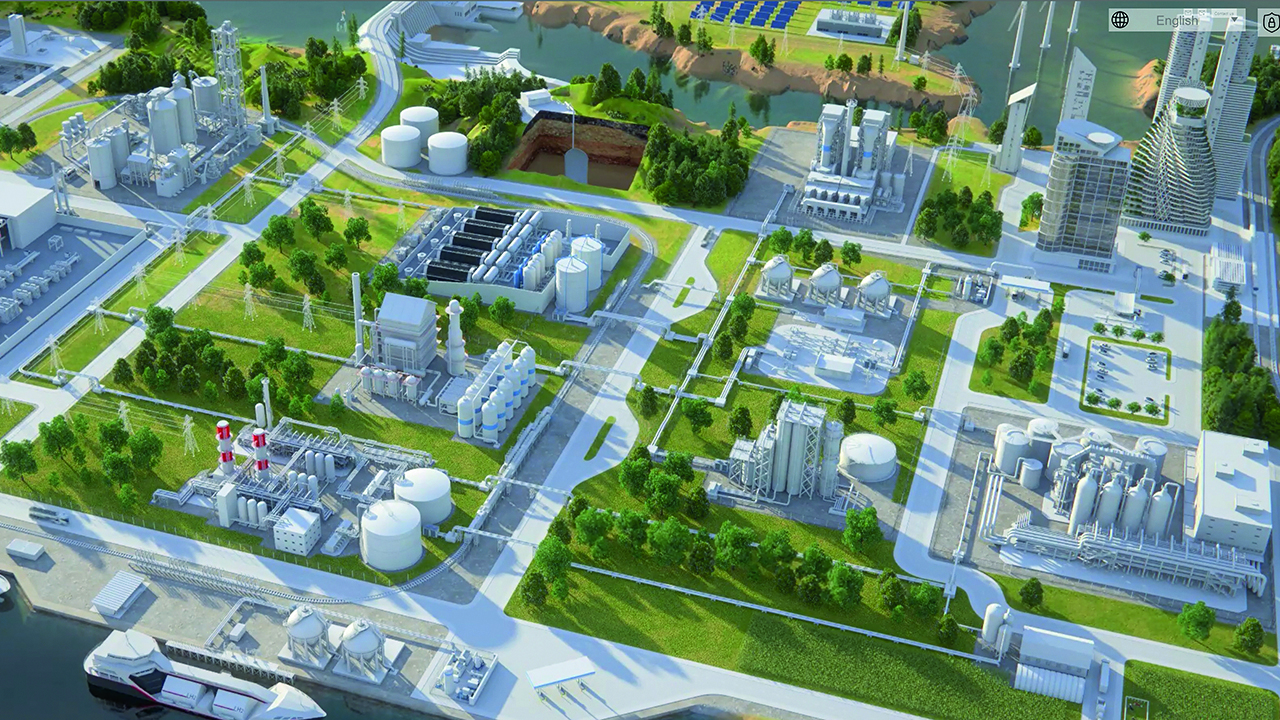
Optimizing hydrogen plants during construction and operations
As hydrogen production plants (HPPs) grow in size and complexity, enterprises may struggle to construct new plants that are both commercially viable and tailored to a specific use-case. For a successful HPP, considerations such as desired plant capacity, equipment specification, variation in hydrogen demand and fluctuations in renewable energy supply must all be taken into account at an early design stage. Factors that may complicate these considerations, however, are the fast-changing technology landscape, the lack of expertise of many new entrants and the multidimensional nature of optimization endeavors.
These aspects are particularly relevant when specifying the key elements of an HPP. When planning a new facility – or upgrading an existing one – the designers must decide on
• Electrolyzer type, size and capacity.
• Storage tank volume and vessel pressure parameters.
• Throughput capacity of a compressor unit.
• Presence and size of an electric battery.
• Type and capacity of (renewable) power sources.
• Electricity cost model: flat, time-of-use (ToU), spot market or tailored power purchase agreement (PPA).
• Regulatory requirements and subsidy schemes.
• Hydrogen demand profiles (distribution and amount) to be supplied.
• Energy source mixes and the consequent greenhouse gas profiles.
All these aspects are to be considered and, ideally, optimized for a financially sound project. The levelized cost of hydrogen (LCOH) is an important measure here as it includes all operating and depreciated capital costs combined to determine the production cost of 1 kg of hydrogen.
In other words, sizing an electrolyzer plant is a nontrivial task that requires much detailed know-how. ABB has developed a tool that assists planners and HPP operators in this undertaking: the HPP Sizing Tool.
Fundamental principles of the HPP Sizing Tool
Both simplicity and accuracy were major guiding principles in the design of the HPP Sizing Tool: Only limited input is required by the ABB personnel working in conjunction with the customer concerned. If a requested input is unavailable, the tool recommends a typical value. Reliability is obtained by operating on actual project data and using calculations based on tailored optimization models run in the background. Detailed technical and financial models are used to choose configurations that ensure total cost is minimized.
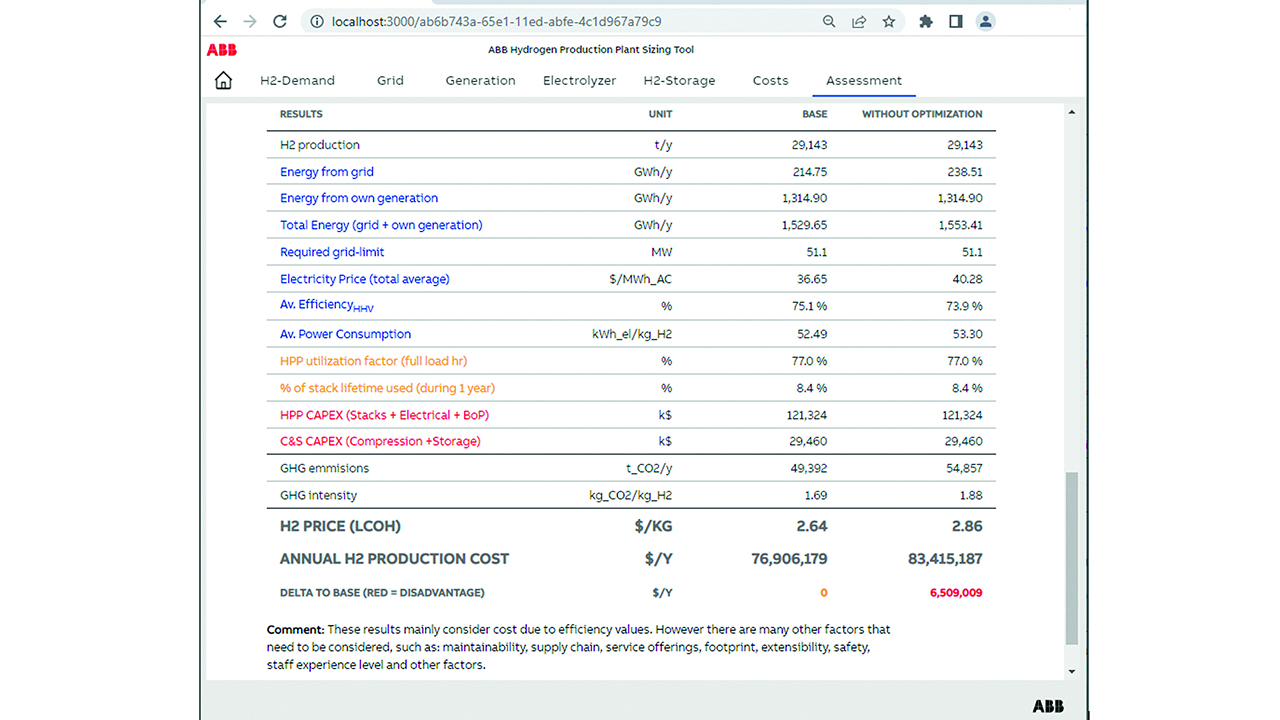
The tool presents the user with a graphical overview and comprehensive numerical insights of all relevant aspects of the proposed optimized plant →02. CAPEX and OPEX are considered, and a digital twin capability allows alternative scenarios to be easily constructed, manipulated and compared. The model overview and required input parameters of the sizing tool are shown in →03. Two quite different example scenarios highlight the tool’s flexibility.
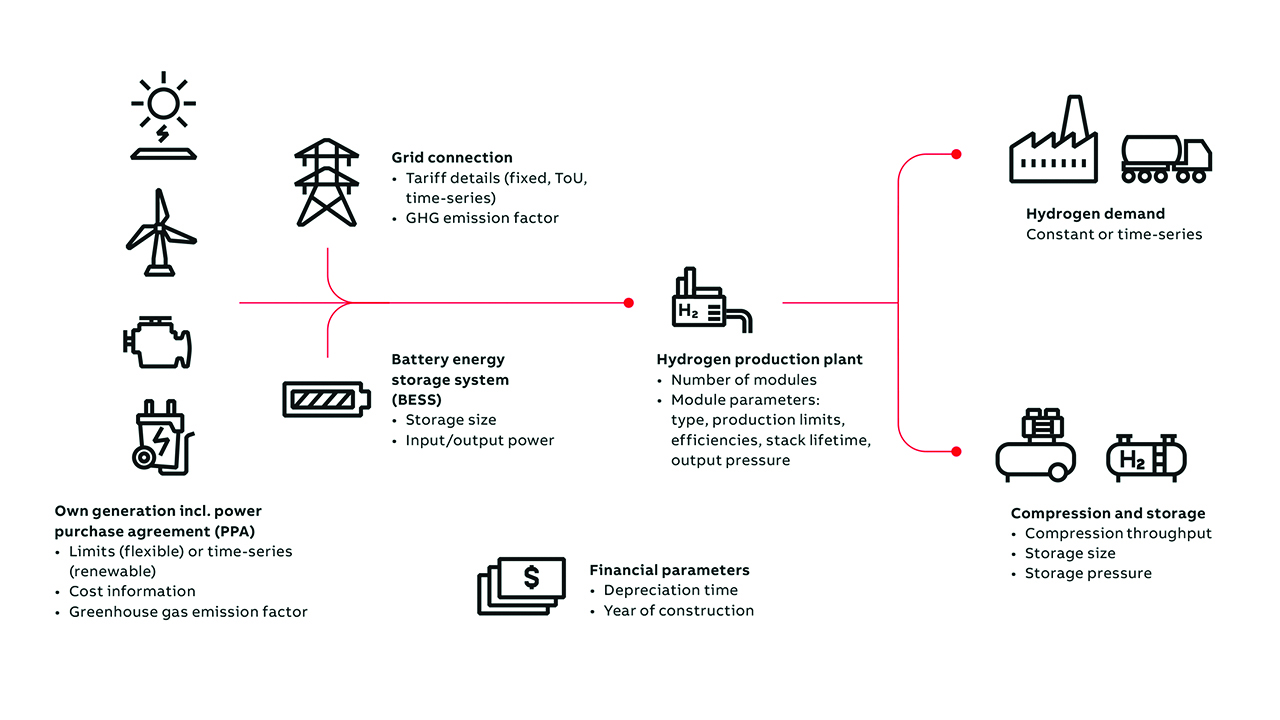
Example: sensitivity analysis of an industrial hydrogen production plant
The first example involves an industrial partner who wants to produce large amounts (up to 40,000 Nm³/h – normal cubic meters per hour) of hydrogen to be used in the production of, for instance, ammonia, cement, or steel. Most of the energy needed is secured via a PPA for 150 MW of renewable energy; the rest is supplied from the grid under a ToU tariff. Twelve alkaline electrolyzer (AEL) modules and hydrogen storage facilities at 250 bar have already been decided upon →04. ABB ran an HPP analysis on the project, resulting in the following:
• The PPA covers 83 percent of the total electricity consumed annually; the remainder comes from the ToU tariff.
• The overall LCOH is $2.75/kg hydrogen due to the competitive PPA price and high plant utilization of 77 percent.
• The greenhouse gas signature is 2.1 kg CO₂/kg of hydrogen produced.
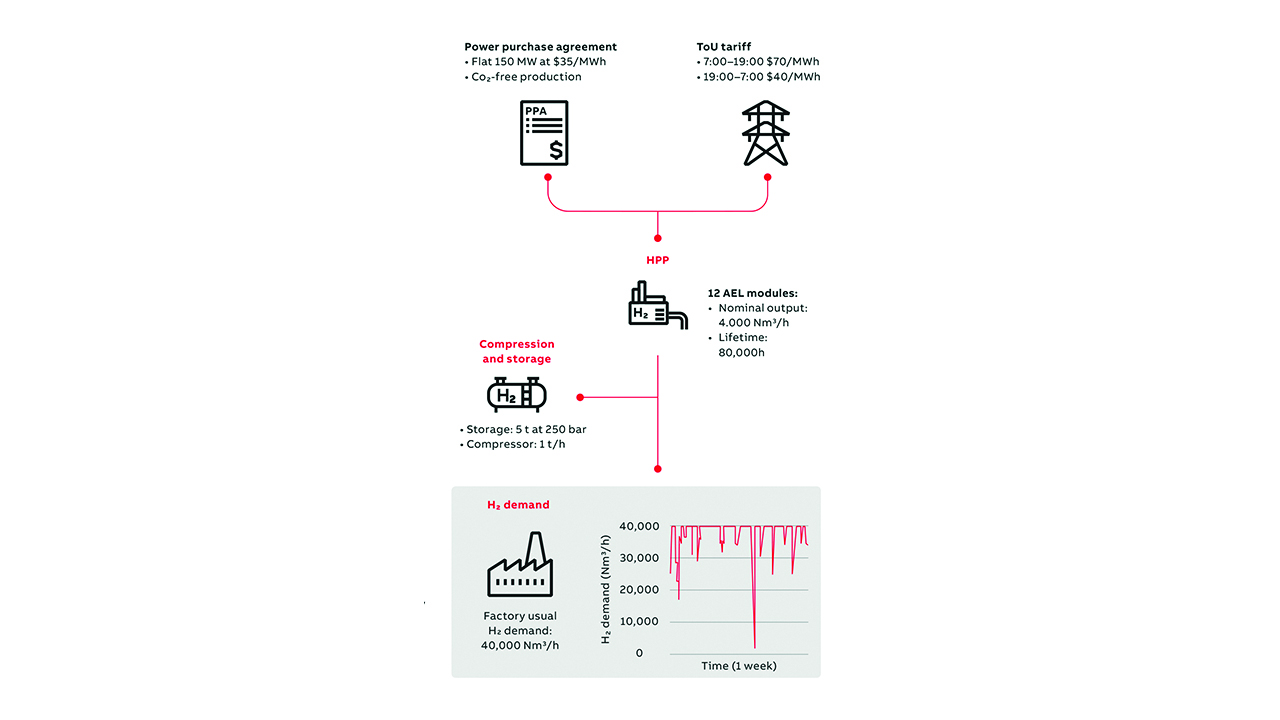
The sensitivity analysis conducted by ABB identified the impact of various levers for further reduction of the LCOH →05. The main levers are (in order of significance):
1. Lower electricity price in the PPA.
2. Utilize more efficient electrolyzer modules.
3. Increase the PPA quantity (and thus reduce the more expensive ToU volume) while ensuring that all the energy ordered can actually be consumed.
4. Lower electricity prices from the grid.
Image currently unavailable
Image currently unavailable
Image currently unavailable
Image currently unavailable
Image currently unavailable
Image currently unavailable
05a Base case result. 05b Sensitivity analysis. The corresponding percentage reduction in the LCOH caused by a 10 percent beneficial movement (eg, a decrease in the PPA price or an increase in PPA volume) of each factor is reflected the bars of the chart. For the modules, the change is not a percentage but a move to a system with one module fewer.
05 Results of sensitivity analysis.
Other factors might be more significant in projects that are not dominated by electricity costs, such as: financial parameters (eg, depreciation time), initial CAPEX of the HPP, number of modules or stack lifetime, water price, or the size of compression and storage. For each specific project, the analysis gives a good indication what aspects to look at for further overall cost optimization.
Example: optimization analysis of a trailer filling station
A customer wants to supply hydrogen to fill three to four trailers daily with 1 t of hydrogen each. Power comes partly from a directly connected wind park (9 MW peak output) and the rest is purchased on the spot market. The customer preselected a supplier of two 2,000 Nm³/h polymer electrolyte membrane (PEM) modules and decided on a reasonable size of hydrogen storage and compression →06.
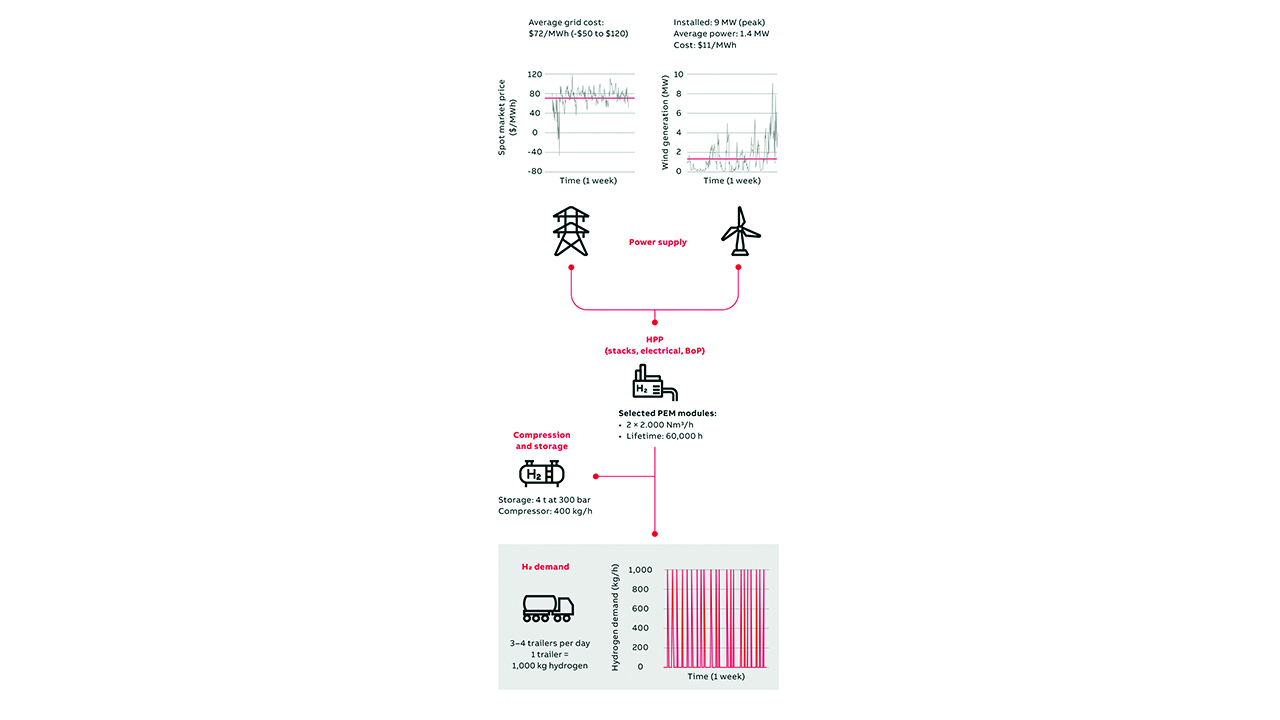
The initial calculation of the customer case with this 4,000 Nm³/h PEM plant resulted in an LCOH of $5.45/kg of hydrogen, only half of which comes from the electricity cost, due to the low plant utilization of 36 percent. Taking this base case, ABB used the digital twin to calculate various scenarios with stepwise improvements. The results are shown in →07 and can be summarized as follows:
• Using ABB OPTIMAX as an energy management system reduces the electricity cost significantly by selecting better setpoints to benefit from low-cost energy and higher efficiencies of the nonlinear plant efficiency curve.
• Reducing the number of electrolyzer modules from two to one – ie, cutting capacity to 2,000 Nm³/h – lowers the fixed cost significantly, but has the disadvantage of increased operational cost and lost module redundancy.
• Optimal sizing of compression and storage reveals that reducing their size (and CAPEX) by around 50 percent brings a benefit greater than the small disadvantage on average electricity cost increase.
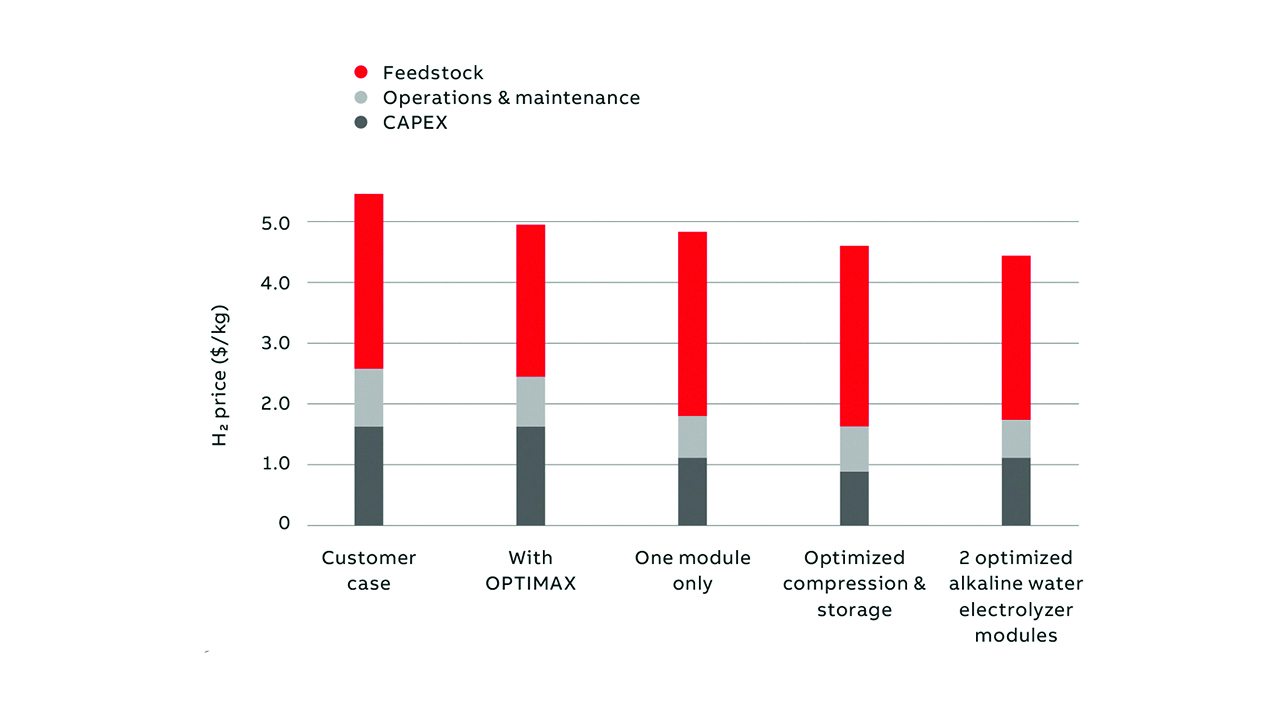
Further, a scenario using two slightly smaller alkaline electrolyzer modules, with a total capacity of 3,000 Nm³/h, was calculated. This change reduces the electricity costs (due to higher efficiency at nominal production) and stack replacement costs (due to longer lifetime).
The disadvantage of the larger – and thus more expensive – total plant is more than compensated for by reduced average electricity price due to increased flexibility to produce more when prices are low. Compression and storage capacities were enlarged again to maximize this advantage.
Overall, the final ABB layout proposal offers the plant operator the following benefits:
• Annual savings of $1.14 million, unlocked by the overall reduction of the LCOH by 18 percent (to $4.50/kg from $5.45/kg). The savings come from reductions in electricity cost (9 percent) as well as CAPEX and OPEX (30 percent each).
• Reduced greenhouse gas emissions (8 percent) by consuming less energy overall and using grid energy when its green content is higher.
• Guaranteed supply of the hydrogen demand, even with failure or maintenance of one of the modules.
These benefits can fully be unlocked during operations when using an EMS system like ABB OPTIMAX.
Making the correct investment decisions
The HPP sizing tool is an ABB Web-based tool for the benefit of electrolyzer projects in early concept and planning phases. The tool takes the actual project data as input and offers appropriate default values when data is missing. For accurate calculation of the project-specific LCOH, the tool uses very detailed models of fixed costs (CAPEX, OPEX). For plant efficiency, nonlinear models are employed. These models are crucial for the operational setpoint optimization that ABB OPTIMAX does in the background to determine accurate variable costs. The results are used for discussion with the industrial partner or dedicated consulting activities. The specific customer case can be revisited any time to update parameters according to ongoing project planning as laid out in →03. The tool can be used to respecify existing plants as well as set up new ones.
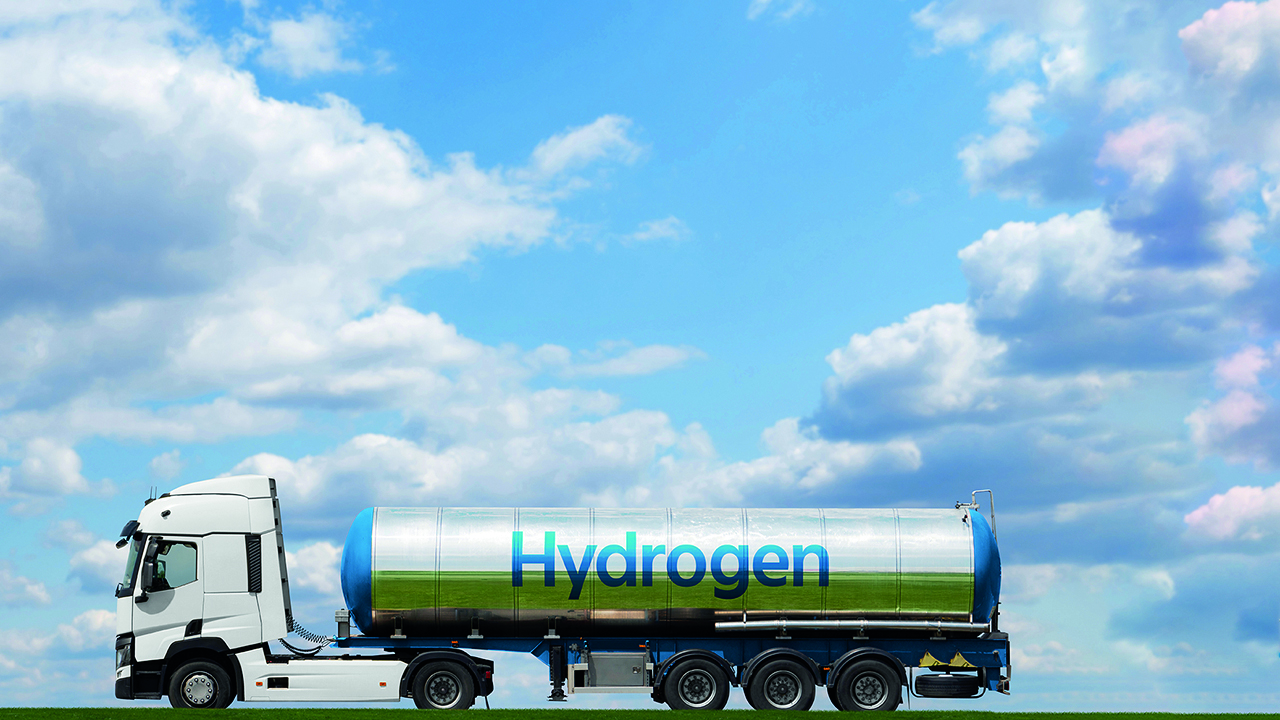
Together with the expertise of the ABB sales and consulting team, the HPP Sizing Tool supports ABB’s partners in making the right investment decisions on their way to decarbonization and switching to a low- or zero-carbon hydrogen production regime →08.
Footnotes
¹ See also “Carbon neutrality and net zero” in this issue of ABB Review pp. 228 – 229.