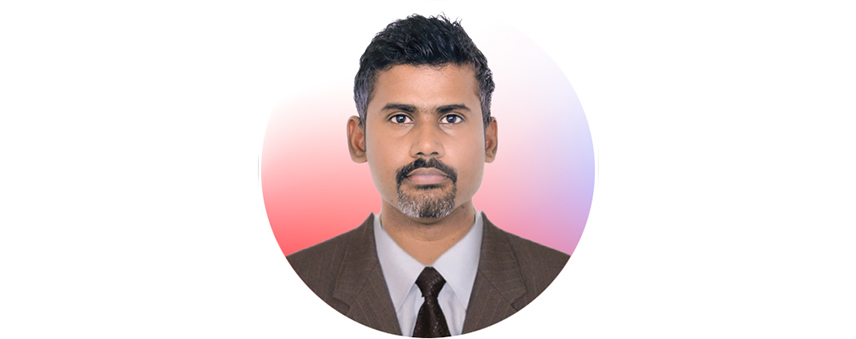
About Myself & Why Advanced Process Control?
In today's fast-paced industrial landscape, efficient and optimized processes are crucial for organizations striving to remain competitive. Advanced Process Control (APC) plays a pivotal role in enhancing process performance, maximizing productivity, and minimizing costs. As a professional with 12 years of experience in the field, I have had the privilege of witnessing the transformative power of APC firsthand. In this blog, I will briefly share my journey and delve into the challenges, triumphs, and lessons learned throughout my career in advanced process control.
My journey in advanced process control began with a deep fascination for the intersection of technology, automation, and industrial processes. After completing my formal education in Process Control engineering, I started my career in an American company that specialized in process control systems. Here, I honed my skills in foundational control techniques and familiarized myself with various control system architectures.
As the industrial landscape evolved, so did the complexities of process control. APC emerged as a necessity to optimize operations and cope with dynamic challenges. I eagerly embraced this evolution during my career, delving into predictive control models, model-based optimization techniques, and real-time optimization strategies. It was a period of continuous learning and growth, attending conferences, workshops, and collaborating with experts in the field. This enabled me to stay at the forefront of APC advancements and contribute to the development of robust and maintainable solutions.
A recent project I have been involved in
With ABB, I further scaled up my career into the mining and metals industry. I would like to showcase one of the notable projects and a success story in ABB. This project involved applying APC to a minerals concentrator in Southern Scandinavia. This plant and company has a rich history of adopting sophisticated technologies and is often referred to as a leader in “modern and autonomized” mining.
This plant mines complex ores containing zinc, lead, silver, copper and gold. The grinding circuit here has one autogenous primary mill one autogenous secondary mill which operate in tandem, the discharge of primary mill feeds the secondary mill. Discharge slurry is then sent to hydro cyclone targeting a cut size of 150um and the overflow is sent to flotation process to recover and concentrate the valuable minerals. ABB Ability™ Expert Optimizer facilitates advanced process control and was implemented in the grinding circuit for better mill utilization and stability of the grinding process.
Like all APC endeavors, this project presented a unique set of challenges, from optimizing complex grinding mills in tandem to utilizing the installed capacity of the grinding circuit due to limitations in the existing control loops. One specific area of focus were the variations in ore feed size and hardness. It is very challenging to stabilize grinding operations and push throughput with manual human operators working with single in single out (SISO) control methodologies. Here, I spent some time on the process observing the mill dynamics and collaborating with the plant team onsite, to determine how we could balance robustness and model accuracy of a multivariable predictive control strategy to ensure a sustainable solution that automatically stabilizes the operation and constantly looks for opportunities to maximize throughput.
The current scope of the Expert Optimizer is to maximize the mill utilization, thereby maximizing the feed while considering the load limitation or torque limitations set by Operations:
AG Mill Control:
- Process variables and manipulated variables used in mill control strategy are listed below.
Main Control Variables (CVs):
- Primary mill Torque (%)
- Primary mill Load (t)
- Secondary mill Torque (%)
- Secondary mill Load (t)
Mill powers as a CV were not included in the model, because maintaining the torque and load is critical here and high-power condition is practically not possible with low torque. High torque/load is handled by the APC strategy.
Manipulated variables (MVs):
- AG Mill Feed Total setpoint (tph)
- Primary mill speed (%)
- Secondary mill speed (%)
With Expert Optimizer, we were able to significantly reduce specific energy, product quality variations, and enhance overall process stability. The key objective of also utilizing the installed capacity was improved, even with load limitations due to bearing issues. Realizing the tangible impact of APC on the bottom line of an organization is always a defining and fulfilling moment in any APC project.
- Throughput Increase by between 3 - 4%
- Reduction in Specific energy between 6 - 7%
- Reduction in mill load standard deviation by ~ 40 %
What are some of the challenges and highlights of working with APC in industry?
While the rewards of working with advanced process control are substantial, the journey is not without its challenges. The dynamic nature of industrial processes, coupled with the complexities of integrating APC systems, demands resilience, adaptability, and problem-solving skills. From overcoming data acquisition limitations to developing robust models and addressing real-time optimization constraints, each project presents unique hurdles that required innovative solutions.
Additionally, effective communication and collaboration with cross-functional teams are vital in ensuring successful project implementation. Aligning the goals and expectations of process engineers, operators, and management play a crucial role in overcoming resistance to change and securing organizational buy-in for APC initiatives.
Despite the challenges, the rewards of implementing advanced process control are immeasurable. Beyond the financial benefits of increased efficiency and reduced operating costs, APC has the potential to enhance safety, reduce environmental impact, and improve product quality. Witnessing the transformation of underperforming processes into highly optimized systems has been the most rewarding aspect of my career.
Moreover, the knowledge and expertise gained in APC have allowed me to become a trusted advisor, providing guidance to organizations seeking to embark on their own journey towards process optimization and digitalization. Sharing insights, best practices, and success stories has become a passion, as I strive to contribute to the growth and advancement of the field.