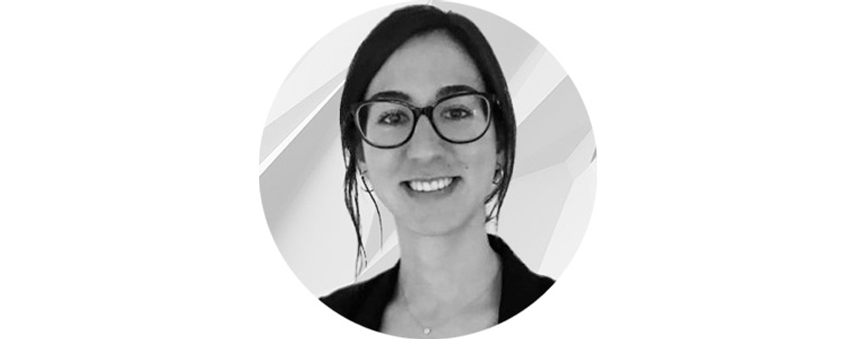
About Myself & Why Advanced Process Control?
I am relatively new to Advanced Process Control. I have a Ph.D. in chemical engineering, focusing on removing pharmaceutical compounds from wastewater by applying different oxidation processes. Before joining ABB, I worked for several years as an R&D engineer at a cleantech startup, focusing on innovative membrane technology for energy-efficient separation and purification of gases.
What attracted me to the field of Advanced Process Control with ABB is the current opportunities to apply this technology to uplift process performance across many industries, such as mining, cement, pulp, and paper, through digitalization. This can be achieved by increasing process profitability (making more of a better product for less) or reducing not-so-friendly consumables that can impact the environment, e.g., reducing overdosing of xanthates in flotation or coal firing in pyro applications. The challenges across different industry verticals are technically unique, but all strive for a common goal which I find fascinating. Another great thing about working as an APC project engineer at ABB is the direct customer contact. It allows me to work on-site with the customer and thus develop new customized solutions and solve real-life problems. I love to see the impact that we have through our solutions.
A recent project I have been involved in
Recently, I have been working on a project for an iron ore mine in northern Sweden. The area of the plant that is in focus for this project is the production of pellets. This is a complex process that includes different stages: sorting, ore concentration, purification, and pelletization. During the entire process, exhaust gases are produced, including SO2, which must be removed before being emitted into the atmosphere. This is where we apply ABB Ability™ Expert Optimizer, also known as “EO,” to facilitate advanced process control and improve operating efficiencies.
How is SO2 removed?
Lime is used to remove SO2 from the exhaust gas stream. By an absorption process, the gas stream reacts with an aqueous solution of lime to produce calcium sulfite. This chemical reaction must occur at certain temperature conditions to prevent condensation and achieve a maximum yield of the reaction.
CaCO3 + SO2 → CaSO3 + CO2
Ca(OH)2 + SO2 → CaSO3 + H2O
The project consists of the implementation of Expert Optimizer software. This involves defining dynamic models through data-driven techniques such as state space identification and then commissioning these models to exploit the process to stabilize operating conditions and optimize the gas cleaning phase by reducing SO2 emissions. The main variables on which we focus to achieve our goal and that of our customer are water and lime slurry flow that enter the reactors, which are the variables that will mainly control the chemical reaction. Once the process has been stabilized, the next goal is to minimize the consumption of these raw materials. This is done by setting the software's optimization function always to seek opportunities (automatically) to minimize (when there is capacity to do so).
What are some of the challenges of this project?
This project in Sweden is slightly different from the more common projects associated with mining and cement, for example, grinding, flotation, calciners, kilns, and coolers, as it involves a challenging chemical process. Due to the uniqueness of the project, we started the engagement with the customer through what ABB calls a “Fingerprint.” A Fingerprint is essentially a technical audit to determine the opportunities, both technical and economic, for applying advanced process control. This allowed us to evaluate the process, instrumentation, automation, and plant economics to better understand what drives plant profitability and what is technically possible.
Another challenge concerning Advanced Process Control in this project is the existence of two reactors that do not always treat the same volume of gas, and that do not always operate in parallel. That means that we are paying special attention to the implementation of the application regarding flexibility and robustness, so that the process is constantly driven to an optimized state regardless of the current balance across reactors.
Possible future work and expansion
Advanced Process Control is such a flexible and wide-reaching technology. It is a huge mine, so it is possible to implement EO in other parts of the plant, such as crushing, grinding, pelletization, and induration. Furthermore, maintaining open and transparent communication and relationship with the customer is vital to ongoing collaboration and success and local support from the ABB Sweden team.
What I personally believe is essential for customers in this field of engineering is a solid track record of other projects successfully implemented. This is something I am looking forward to furthering with this project in Sweden. As a new joiner, I am surrounded by an experienced team that allows me to develop and grow as an APC engineer. Moreover, ABB has offices and projects all over the globe, which exposes me to a wide range of different people, cultures, projects, and technologies, allowing me not only to grow professionally in the advanced process control area but encourages me to keep my mind open to different ways of working and negotiating engineering challenges!