With 18 vineyards spanning from the Napa Valley to the Anderson Valley, Cakebread Cellars benefits from the favorable weather and terrain that produce exceptional grapes leading to award-winning wines. The region also has its challenges, though. California's wildfires and subsequent power outages aimed at preventing further fires often produce instability in utility grids. Because wine making requires precise timing and accuracy, the process of harvesting, crushing, and fermenting grapes cannot wait for stable utility power. Cakebread Cellars had to find a way to address this issue and, as a result, sought to upgrade their chilled glycol plant, which is crucial for producing their premium wines.
Cakebread Cellars recognized that for the plant to be successful they needed a comprehensive design that could adapt to the unpredictable utility grid. Reliability was obviously a key requirement for the chiller facility. They needed to address California's power grid stress and frequent outages during the windy summer months, when harvest and production are at their peak. Maintaining a stable temperature during fermentation is vital, as even slight fluctuations can ruin the wine. A single day of the chilled glycol plant being offline could result in a loss of an entire year's production, impacting availability and revenue. Cakebread Cellars understood the importance of having a trusted partner for this endeavor and enlisted the expertise of Novate Solutions Inc. Novate is a vertically integrated technology partner specializing in designing, implementing, and supporting industrial technology solutions.
Robert Wallace, Facilities Manager at Cakebread Cellars, expressed the company’s confidence in Novate, saying, "We were impressed with their ability to solve complicated problems, so when we decided to install a new chiller package, we called them for assistance."
The chilled glycol plant needed to be a fully integrated solution with the flexibility to utilize power from multiple sources. Cakebread Cellars already generated some of their electricity using a gas turbine, but it wasn't enough to power the entire chilled glycol plant. Novate proposed a solution that incorporated multiple power feeds into the system, including backup generators, turbines, and the utility grid. The plan also included a condenser to ensure continuous glycol flow, even during power outages, by connecting a generator to a 300-amp feed that kept the air compressors and refrigeration yard operational. The two panels could draw power from different sources when needed to ensure a consistent supply. This approach required collaboration with the plant team and the local utility.
Carlos Rogers, President and CEO at Novate Solutions, Inc., describes the challenge they faced, saying, "Building a chiller plant is hard, but building one that can adapt to multiple power configurations was a unique challenge. We essentially had to create two plants that could seamlessly work with whatever power was available."
Improving process performance
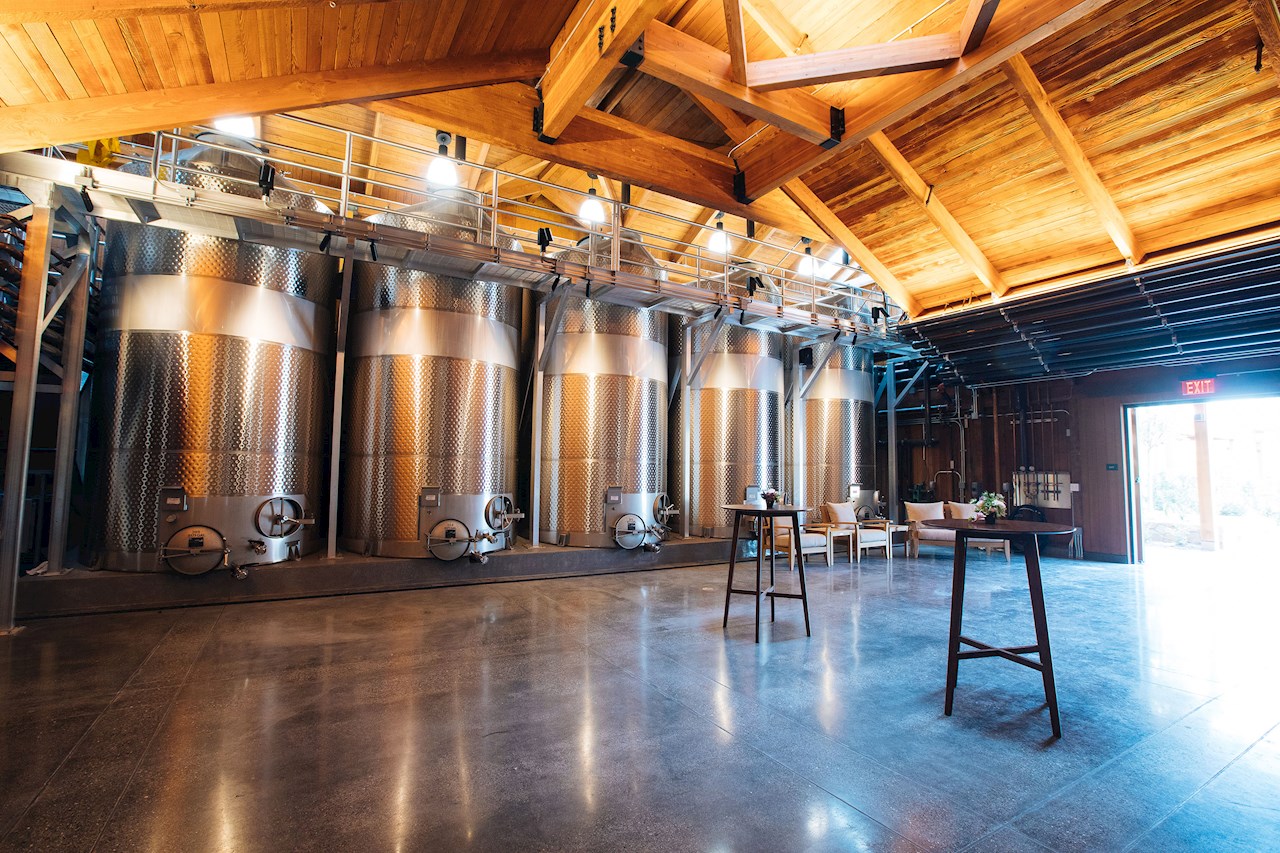
Another requirement for the chilled glycol plant was complying with California PUC Rule 21, which regulates industrial customers generating their own electricity. The plant needed to communicate with the generation system to predict when compressors or pumps should start or stop operations. California PUC Rule 21 prohibits exporting power back to the utility. To address this, Novate selected a combination of ABB ACS580 Variable Frequency Drives (VFDs) and an ABB Soft Start, each equipped with a fieldbus interface, to provide real-time status to the plant’s control system. This arrangement ensures compliance with the rule and optimizes the operation of the chilled glycol plant.
Novate chose ABB ACS580 drives as a reliable solution with an easy-to-use fieldbus interface that seamlessly integrated with Cakebread Cellars' existing control system platform. The ACS580 drives are part of ABB's all-compatible drives portfolio, offering consistency in architecture and user interface. The networked, responsive ABB VFDs played a crucial role in precise power load management, allowing Cakebread to operate with their existing gas turbine generators.
In addition to reliability, the ability to adjust glycol levels based on the load was important. Cakebread Cellars utilizes the intelligence provided by the drives to reduce downtime and maintenance costs and improve process performance. The drive's diagnostic capabilities allow the support team to ensure proper operation and intervene quickly if any issues are detected. The plant’s control system receives this data in near real time through ABB’s advanced fieldbus connection in the VFD.
Robert emphasized the solidity and reliability of ABB VFDs, stating, "ABB drives are second to none. ABB also provides easy-to-use tools that simplify programming the drive to adapt to changing applications and conditions."
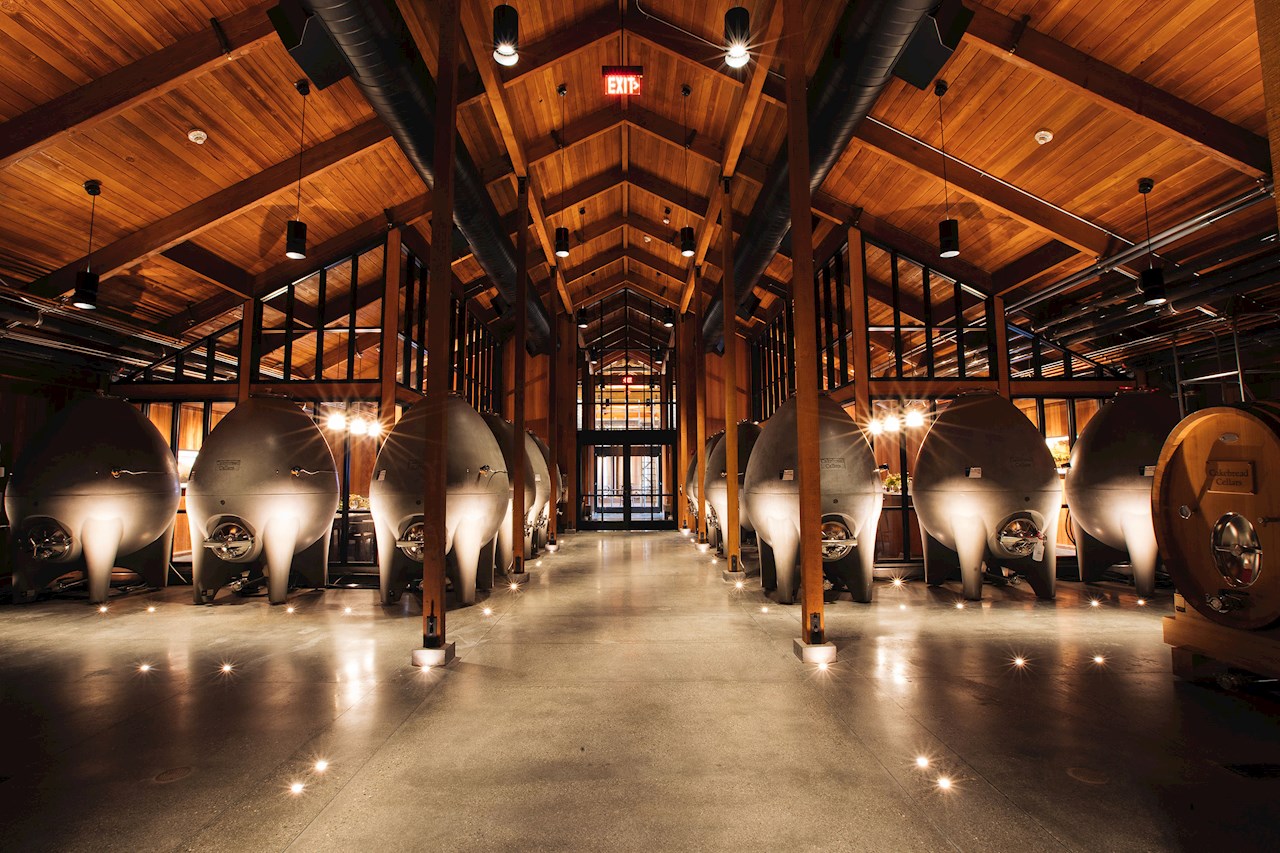
Cakebread Cellars has adopted the ACS580 VFDs as a standard solution, with several ongoing projects that rely on reliability and robust communication.
Implementing the new chiller plant system faced hurdles beyond just addressing power instability. Novate's solution involved integrating VFDs, Soft Starters, and other equipment into a UL508A control panel that was also cooled by the chilled glycol system. Given limited space, the combination of the compact drives and the water-cooled industrial control panel proved to be the optimal solution for Cakebread's demanding operation. Because operations could not be impacted, Novate ensured that the existing chilled glycol system remained operational during the commissioning of the new system.
The collaboration between Cakebread, Novate, and ABB was essential to the project's success. Throughout the process, Novate kept Cakebread's overall goals and productivity at the forefront, working closely to design, install, and monitor the unique system. The teams also engaged ABB drive specialists to review requirements and select the appropriate drives, particularly for the compressor, ensuring accurate electrical demands.
As Cakebread Cellars aims to become carbon neutral by 2030 and prioritizes sustainability with green energy solutions, the partnership with Novate and the use of ABB drives represent significant steps toward achieving these goals.