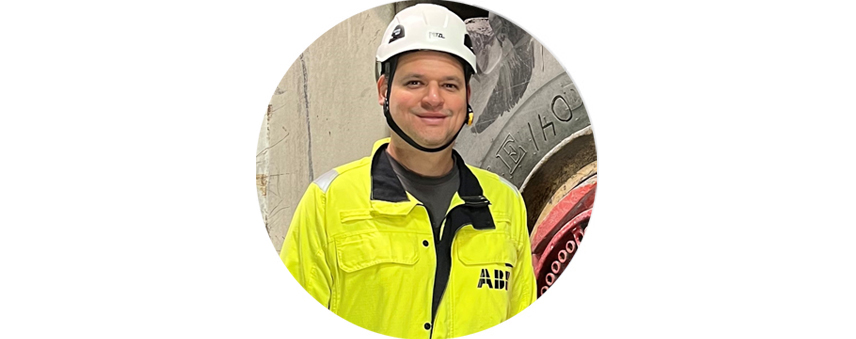
About Myself & Why Advanced Process Control?
I have worked with Advanced Process Control (APC) for almost 18 years. I started soon after graduating in Chemical Engineering at the University of São Paulo in Brazil in 2005. In those days, I was interning at an automation company in Brazil, where I was exposed to various automation projects within the process industries, including those of APC. After graduation, due to my background in Chemical Engineering, I was assigned to the APC engineer role, where I had the chance to further develop these skills with other engineers from Brazil and abroad.
During these years, I have worked with APC applications for different companies, including ABB, in Brazil between 2008 and 2013. In 2015, I joined the global APC engineering team in ABB Switzerland, implementing ABB's APC solution, Ability™ Expert Optimizer, and started an international career, delivering APC projects globally. The change has not only allowed me to work with people from different cultures but also allowed me to learn about many exciting countries and regions.
A recent project I have been involved in
Recently, I worked on a project at a cement plant in Japan. I commissioned an Expert Optimizer for the two pyro-processing lines with the support of ABB Japan and the end customer. The project included Expert Optimizer applications for one twin-calciner, one single calciner, two kilns, and two cooler units.
The cement plant manufactures high-quality cement with a clinker production capacity of 4.5 million tons annually. It supplies to customers in Asia, Oceania, and Japan. The company has invested in an efficient and sustainable factory that manufactures cement, incorporating by-products, raw material waste, and fuel substitutes mainly from neighboring areas.
The interaction and commitment of the customer and ABB Japan was crucial for the project's success since it happened during COVID-19 times. Because of the time difference between Switzerland and Japan, the key personnel from the plant had to work during the afternoon/night shift during the commissioning. I started in Switzerland early, between 5 and 6 AM, to maximize our time together and adequately define the strategy and control actions. Their knowledge of the process, targeted requirements, and early engagement also made achieving the correct control structure, solution buy-in, and change management easier, making sustaining long-term benefits easier.
What were some of the challenges of this project?
There were several challenges in the project, from the interface and communication with the end customer, who did not speak English and required translation from our colleagues from ABB Japan to the high complexity of the kiln/calciner design that allowed processing of multiple wastes as fuels (also known as alternative fuels), thus turning the plant into an efficient and sustainable process.
The complex design of the system, especially of the larger kiln, had a significant impact on its operation, causing big fluctuations in the calciner and kiln temperatures. Before implementing ABB Ability™ Expert Optimizer, also known as "EO," operators had to take actions to control the calciner temperature constantly; inside Expert Optimizer, we were able to replicate similar actions performed by the operator to be done automatically.
These were customized actions that would take priority over the standard controller actions since they required a more robust intervention to bring the temperature back to normal values. Automating these actions brought immense benefits to operators constantly challenged to maintain the temperatures within acceptable limits. If the temperature in the calciner gets too high, the clinkerization process starts too early, turning the powder material into a sticky liquid phase, which could block the calciner, thus requiring a long shutdown of the process to remove the blockage.
The processing of multiple wastes was challenging due to the big difference between them and the variability of the calorific values. The plant served as a disposal of different wastes, like high moisture sludge and organic sludge from the sewage treatment, plastics, and waste oil from the local city and surrounding areas. All these different materials were fed into the Calciner/Kiln system to be destroyed and, when possible, used as a heat source, reducing the amount of coal required for clinkerization. However, the operation of the waste feeders was not as stable as that of the main fuel; thus, multiple feed failures occurred, an ongoing challenge with manual operator control.
Expert Optimizer with its Fuel Management module, based on Model Predictive Control Technology (MPC), was deployed to allow for quicker reactions to variability in fuel, enabling the plant to compensate for the missing energy with the main fuel or a second waste fuel that was running, reducing the impact of the disturbance in the process. The Fuel Management module also gave flexibility to the plant to maximize or minimize certain fuels/waste based on their costs.
Expert Optimizer offers a flexible configuration environment where multiple control techniques, like simple arithmetic or nested functions, fuzzy logic, and MPC, can be combined in one application tailored to specific customer needs.
Twin-Calciner Control:
Process variables and manipulated variables used in the twin-calciner control strategy are listed below. The twin-calciner was part of the larger kiln, which had a more complex design and had big problems with temperature oscillation. The solution required two MPC controllers, one for each calciner; however, balancing the total energy split between them was necessary. Therefore, changing the fuel flow to one calciner to control the temperature would also impact the other calciner. If the energy balance deviated too far from the 50/50 split, then oscillations would grow and become a big problem.
Controlled Variables Side 1:
- Temperature Calciner 1 (°C)
- CO Calciner 1 (ppm)
- Energy Split Calciner 1* (%)
Controlled Variables Side 2:
- Temperature Calciner 2 (°C)
- CO Calciner 2 (ppm)
- Energy Split Calciner 2* (%)
Manipulated variables Side 1:
- Main Fuel Calciner 1 - Coal (tph)
- Sludge 1 (tph)
- Sludge 2 (tph)
- Waste oil (tph)
Manipulated variables Side 2:
- Main Fuel Calciner 2 - Coal (tph)
- Waste oil (tph)
Feedforward variables Side 1:
- Plastics (tph)
Feedforward variables Side 2:
- Plastics (tph)
*Energy split calculation: Energy Split = (EnergyCalciner1/(EnergyCalciner1+EnergyCalciner2))*100
Kiln Control:
Process variables and manipulated variables used in the kiln control strategy are listed below. This strategy combined a fuzzy logic soft sensor (BZT) used to estimate the actual kiln temperature with two MPC controllers, the Kiln Main module and the Fuel Management module. The Kiln Main module MPC was responsible for manipulating and stabilizing most of the kiln parameters, providing one output to the Fuel Management module, the required energy for the kiln. The Fuel Management module received the required energy setpoint from the main module and was responsible for splitting it into the different fuels used in the main burner. It was also responsible for fuel failure compensation.
Kiln Main module
Controlled Variables:
- BZT soft sensor (combination of Kiln AMPS, Pyrometer, and NOx)
- Oxygen Kiln inlet (%)
- Oxygen Pre-heater tower 1 (%)
- Oxygen Pre-heater tower 2 (%)
- Energy split between Calciner and Kiln (%)
Manipulated Variables:
- Kiln Feed (tph)
- Required Energy (GJ/h)
- IDFan Pre-heater tower 1 (rpm)
- IDFan Pre-heater tower 2 (rpm)
- Kiln Speed (rpm)
Fuel Management Module
Controlled Variables:
- Required Energy (GJ/h)
Manipulated Variables:
- Kiln Main Fuel – Coal (tph)
- Plastics 1 (tph)
- Plastics 2 (tph)
- Plastics 3 (tph)
Results
The APC applications maintained the operational quality at the plant and reduced the thermal energy consumption by 3 percent. Furthermore, it has helped operators reduce their operational load daily by around 70 percent, allowing them to focus on more important tasks in the plant.
Possible future work and expansion
Expert Optimizer applications are already consolidated in the cement industry; therefore, the possibility to expand the project to other areas is quite significant. After the positive results achieved during the initial project, the customer has already shown interest in implementing Expert Optimizer for the grinding processes, including raw material processing (Raw mills) and finish product processing (Cement mills). APC and the strategies developed in Expert Optimizer have already delivered good results for these processes in hundreds of applications worldwide. Hence, it would be achievable for this specific customer as well. We from ABB look forward to a long-term relationship with the customer, aiming to improve their operations further and bring significant benefits.