As part of the first greenfield Ethernet Advanced Physical Layer (Ethernet-APL) project for BASF in Europe, ABB has been awarded Distributed Control System (DCS) contracts.
Ethernet-APL describes a physical layer for the Ethernet communication technology that is designed especially for the requirements of process industries. These require high data communication speeds over long distances, power and communication transmission through a single cable, and protective measures for safe use in hazardous areas. Ethernet-APL is highly robust for extremely reliable operation. Ethernet has long been the standard IT communication solution, while Industrial Ethernet has been the variant of this standard for the process industries. Ethernet-APL bridges the gap between the two.
Testing 240 connected devices to prove the viability before European debut
Prior to proceeding with their first greenfield Ethernet-APL project in Europe, BASF required potential suppliers to conduct Ethernet-APL performance tests before final contracts were awarded. These tests were completed in March 2023 and following their success, BASF placed order for ABB DCS shortly after.
The performance tests were executed by ABB using ABB Ability™ System 800xA® equipment under realistic production equipment environments. Due to this effort, BASF was able to test the APL technology, integration capabilities and maintainability in the overall automation system.
Gerd Niedermayer, Senior E+I Engineering Manager at BASF, now sees the results of all the previous efforts.
We have been working for about five years with industry partners to jointly drive this technology forward, and now we have proven APL’s operational readiness,” he said. “As a result of these tests, we are now planning to equip new BASF plants in Europe with this technology.”
Dr. Emanuel Trunzer, BASF automation engineer at the Center of Technical Expertise for Automation Technology, explained the reasons that the testing was undertaken, and the results achieved.
These tests were done to demonstrate the functioning and robustness of a PROFINET network via Ethernet-APL on a realistic plant scale,” Trunzer said. This was a great value add to previous lab-scale testing and was essential to gain user acceptance and confidence in this technology. We in Engineering at BASF were invited to incorporate our user requirements into these tests, and that meant almost 240 devices, plus 10 field switches and multiple control systems, were jointly set up to reflect a realistic large-scale system. It was impressive to see that a system with 240 devices operates with such robustness and reliability.”
Higher speed gives many benefits
Ethernet-APL brings several benefits enabling faster, seamless communication between field devices in a process plant, while maintaining the intrinsic safety built into the systems.
The solution also allows easier engineering, commissioning, and maintenance of field instrumentation; provides higher availability and better performance; and ensures more usable and insightful data from the production process.
ABB has been an early adopter of Ethernet-APL, working closely with other early adopters in their areas of specialization to introduce this new technology. By fully integrating Ethernet-APL technology into the wider automation scope, users will get smarter and safer overall operations.
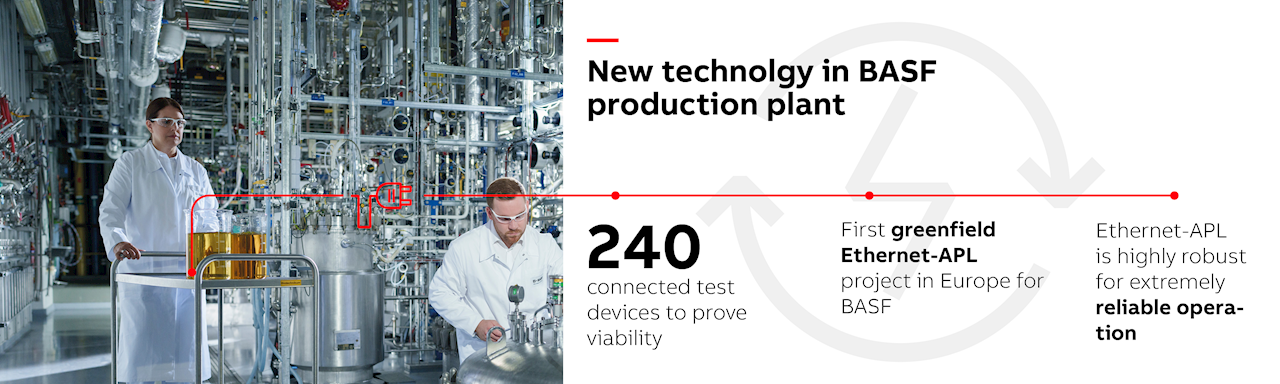
*Image source BASF