Unplanned downtime of the belt conveyors, widely used in mining, causes significant costs and production losses. Whereas ABB offers condition monitoring for conveyor motors, drives, belts, and transformers, the many thousand rollers that carry the belt and the load remained largely unmonitored – until now.
Eduardo Botelho ABB Process Industries, São Paulo, Brazil, eduardo.botelho@br.abb.com; Harald Staab ABB AG, Ladenburg, Germany, harald.staab@de.abb.com
Low market prices for many mined commodities are driving miners to maximize their efficiency. The reliability of key pieces of equipment is a critical factor in this effort. One strategy to achieve reliability is to introduce tools and services for intelligent process monitoring, analysis and optimization. The conveyor belt systems that are often so essential to mine operations are already usually equipped with monitoring tools and services for motors, drives, belts, and transformers. However, the many thousand rollers, or idlers, that carry the belt and the load have, until now, been largely excepted from this monitoring world.
The problem with idlers
While noisy idlers can infringe noise emission regulations, failing idlers not only waste energy but also cause excessive belt wear and misalignment – or, in the worst case, belt rupture or fire. All these factors also present risks for personnel. Belt conveyors are found in all climate zones, in low- and high-altitude locations and underground →1.
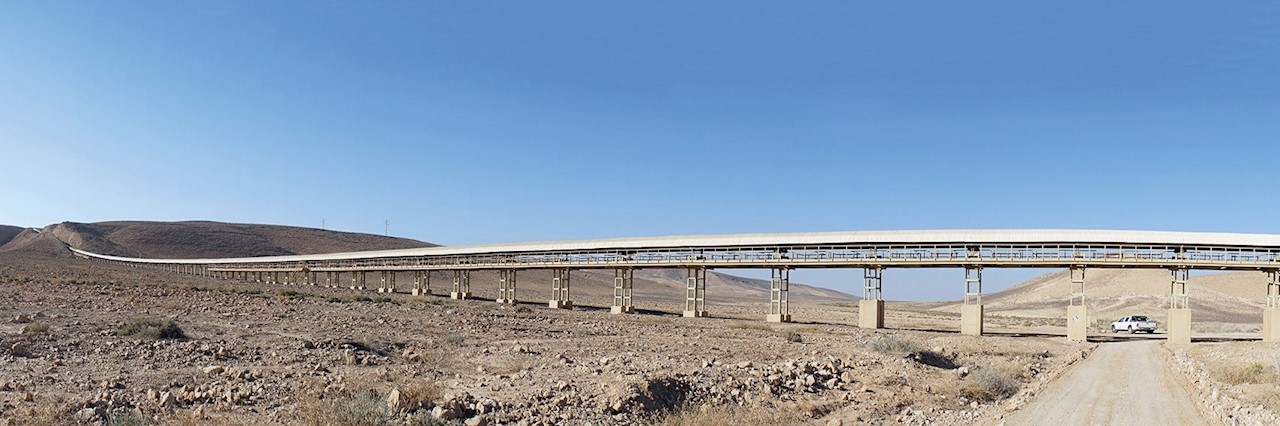
Belts are usually several kilometers long, have a capacity of several thousand tons per hour and run at several meters per second. Such conveyors have tens of thousands of idlers →2,3. A basic problem of idler degradation detection is that degradation has various symptoms – such as ultrasound emissions and warm idler bearing faces – that call for multiple sensing technologies. Past attempts to measure idler degradation using vibration and temperature sensors at or inside the idlers were not shown to reliably detect wear and failure, or, indeed, to be any more reliable than the idlers themselves, given the harshness of mining environments.
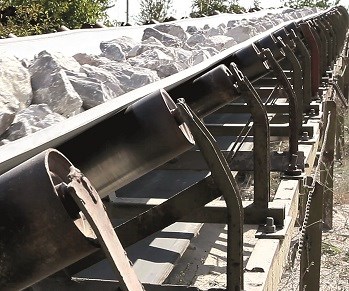
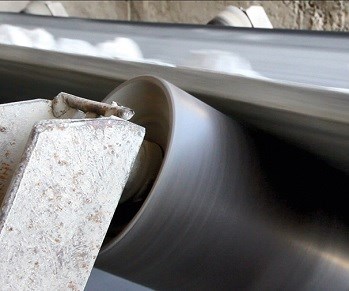
A new idler service
ABB found that a combination of ultrasound and thermography snapshots, taken on a regular (eg daily) basis provides rich and sufficient information to catch idler degradation long before failure. This approach is similar to the current practice of inspection walks by conveyor operators but with much better consistency and data quality because operators often only use hearing or handheld thermal cameras and personal judgement. The current common practice of manual inspection is not only costly and inconsistent but is also hazardous.
ABB has now developed a system that will do the idler inspection job not only fully automatically and very consistently but also with higher sensitivity and better cost-effectiveness than manual inspection. This new service works with an automatic vehicle that carries the sensors, thus allowing repeatable, fast and safe inspections.
The service is called ABB Ability Conveyor Roller Inspection Services (CRIS). CRIS targets all global mining and metals companies and their conveyor installations. CRIS can be offered as a standalone item or as a complement to other ABB conveyor services. The service provides automated monitoring of all idlers and detects failed idlers or predicts failure ahead of time. This latter feature is achieved by rating the condition of individual idlers on a performance curve →4 and finding idlers in the initial stages of degradation, early in the potential failure (P-F) interval. This allows the identification of idlers that need to be cleaned, greased or replaced during the next planned shutdown.
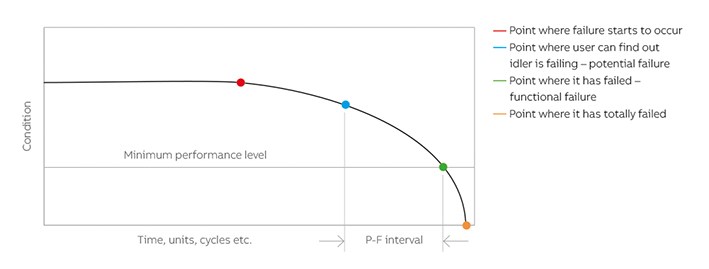
Vehicle and rail system
Besides supplying the correct sensor technologies, a major technical challenge is to position the sensors automatically, accurately and reliably. Since, as a minimum, thermography and ultrasonic recording are need, a fixed installation is not an option, for cost reasons if nothing else. Instead, the sensors have to be brought to the scene regularly and remain there for the short duration of snapshot recordings.
As a sensor carrier, a ground or aerial vehicle, or the belt itself, were all considered. However, the best option was found to be a rail-guided vehicle because the carrier is required to collect data automatically – and for many weeks – without the need for manual intervention or maintenance →5.
Image currently unavailable
Image currently unavailable
Image currently unavailable
Image currently unavailable
Image currently unavailable
Image currently unavailable
Image currently unavailable
Image currently unavailable
Image currently unavailable
05a The inspection vehicle is a train with one locomotive and one sensor car. The sensor head has a pan-tilt unit. 05b The vehicle has a compact cross-section. 05c The rail can be mounted at A or C with covered belts, or preferably at B for the best view of idlers.
05 Techno;ogy prototype of the CRIS inspection vehicle.
The rail, the main cost item, is simply a standard L-stock, preferably steel, which can be sourced worldwide both in metric and imperial sizes. The brackets that mount the rail to the conveyor structure are also inexpensive and just need to be adapted for mounting to the particular conveyor design.
The vehicle is a hanging (for stability) train with at least one locomotive and one sensor car. The locomotive provides traction and power supply. The sensor car controls the motion of the locomotive and the position of the sensor head on a pan-tilt unit. Inspection tours are preprogrammed and executed on a regular schedule, which eliminates the need for continuous radio connection to the vehicle and makes the behavior of the system predictable and consistent.
The total weight of the train is only about 6 kg. Derailing is prevented by mechanical guards, which ensures safe operation and practically eliminates any injury risks to personnel. The vehicle design includes a rubber shell and a tilted roof to prevent damage from falling rocks or rubble.
Flexibility of installation
To adapt to the many different designs of conveyor structures and environments, a number of design variants are possible →6:
Image currently unavailable
Image currently unavailable
Image currently unavailable
Image currently unavailable
Image currently unavailable
Image currently unavailable
06a The design of the rail mount bracket can be adjusted to the conveyor design. 06b Horizontal and vertical curves, and inclines are possible.
06 Rail installation options.
• The rail can be installed on either or on both sides of the conveyor. Installation on both sides improves detection results since the same idlers are sampled from different points of view.
• Curved rail sections allow obstacles to be bypassed or transition between locations A, B, and C in →5c. The minimum radius is currently 1 m. Horizontal and vertical curves are possible. Curves are prefabricated with a bending machine and shipped to the site.
• Slopes of up to 30° are possible in friction mode. A cogwheel mechanism can be added for even steeper sections.
• Depending on the mount points of the rail, there are different design variants for the mounting brackets. Welding is preferred for installation and joining rail segments, but there also is a bolting option, eg for coal conveyors and for underground.
• For additional protection of the rail and vehicle, the rail can be roofed.
• An additional locomotive can be added for long conveyors or slope conveyors where more traction power or battery capacity is needed. An additional sensor car can be added to speed up inspection or to improve detection results.
• The sensor head has a thermal camera, a visual camera with an LED light and an ultrasonic microphone. Other combinations are possible for certain conveyor types or environments – eg more microphones or a mix of microphone types for improved sonic mapping, or omission of the cameras in very dirty environments.
After each inspection tour, the vehicle docks at the battery-charging port of a base station and uploads all inspection data for analysis.
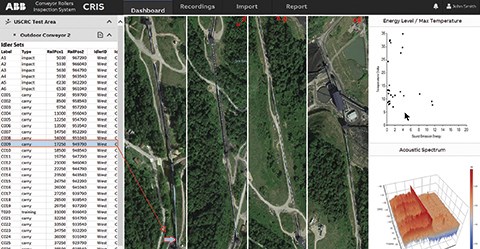
The CRIS control and analysis station is the graphical interface for the service expert to remotely schedule inspection tours and to display and analyze raw data →7,8.
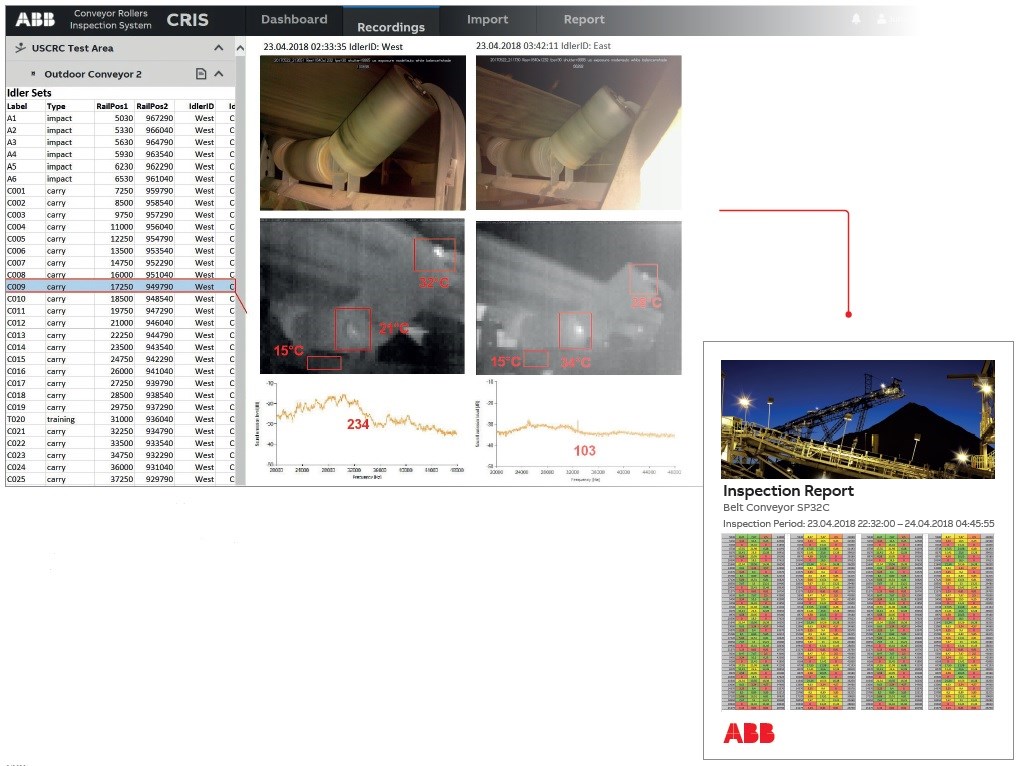
Each inspection tour provides a detailed snapshot of the current status of each idler. By analyzing the history data of individual idlers, a detailed condition map of the entire conveyor belt is created. Furthermore, trend analysis can indicate imminent failure likelihood and allow replacements to be planned.
CRIS presents mining customers with a flexible inspection tool that is fully autonomous, easily installed, and simple to operate and maintain. CRIS travels alongside the conveyor belt and uses sensors matched to a variety of different physical parameters to identify impending idler failures. The data gathered allows the customer to reduce unplanned downtime, maintenance costs, production losses and the exposure of personnel to risk.
Acknowledgment
The authors would like to acknowledge the dedication, hard work and valuable contributions made to the CRIS project by its core team members: Otavio Rocha and Tiago Prata, ABB Process Industries, São Paulo, Brazil; Harshang Shah, Daniel Lasko and William Eakins ABB Corporate Research, Bloomfield, CT, United States; and Maria Rozou, ABB Process Industries, Baden-Dättwil, Switzerland.