Christian Johansson, ABB Process Control Platform, Malmö, Sweden christian.johansson@se.abb.com
Holger Grosse, ABB Process Control Platform Minden, Germany, holger.grosse@
de.abb.com
Ratified in 2021, the Ethernet-APL standard provides an extended physical layer that carries high-speed process, configuration and diagnostic data plus power over long distances (1000 m) via a single twisted pair cable. Use of this new technology shows exciting promise for the process automation industries, particularly in hazardous environments eg, chemical and oil/gas facilities.
As process plant operators seek to gain new value from data through the convergence of information technology (IT) and operation technology (OT), one of their overarching objectives is an effective reduction in total cost per field measurement.
With field devices becoming more numerous, diverse and intelligent, operators not only benefit from greater availability of data, they are faced with the difficulty of handling vast amounts of process and maintenance data. This challenge is increased as projects grow in scale and complexity with various instruments that often combine a large number of different communication protocols and underlying physical layers.
Plant operators, therefore seek a uniform, intrinsically safe and cost-effective communication technology built around robust open industry standards, one that avoids vendor lock-in while bringing the ability to scale smoothly as their business needs evolve.
Resolving several of these challenges and introducing ‘traditional’ Ethernet as an extended physical layer in an industrial setting, Ethernet--APL offers particular appeal, especially when it is deployed in combination with widely-adopted PROFINET and field device integration (FDI) technologies.
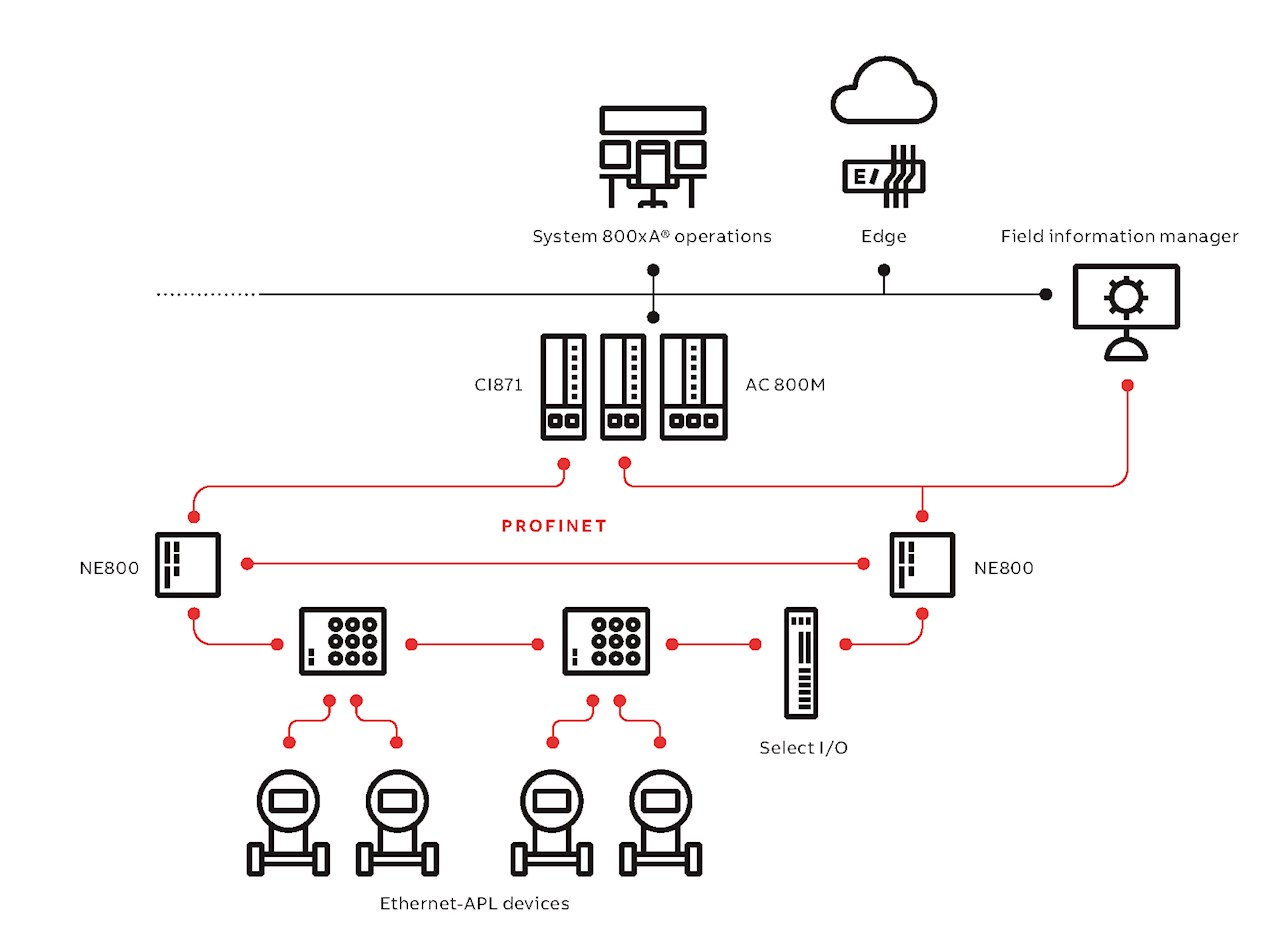
What is Ethernet-APL?
A mainstay of the IT world for decades, Ethernet, standardized in IEEE 802.3, underpins other abstraction layers that collectively define interconnection and data flow between different devices and systems. Ethernet, the established standard for wired digital technologies in industry and business, is already used as the physical layer for the collection of data and control of remote I/O and electrical equipment that use protocols such as PROFINET and Modbus TCP. Until now, however, Ethernet’s wider adoption to field devices in the process industries has been restricted due to its unsuitability for some process industry applications in hazardous areas eg, oil refineries. In addition to cost-effectiveness and simplicity, these facilities require Ethernet features such as the ability to transmit communication protocol and power supply to devices over long distances, enhanced safety, eg, explosion protection, and the ability to be repairable during inclement weather and at any time.
Working with other vendors and standard development organizations since 2015, ABB has been helping to develop technology, guidelines and best practices, thereby contributing to the enhancement of field-level Ethernet connectivity for its use in process automation industries.
Based on open IEC and IEEE standards, eg, IEEE 802.3cg-2019 standard, Ethernet-APL is an extended layer for single-pair Ethernet (SPE) based on 10BASET1L that brings the benefits and economies of scale of high-speed Ethernet communications out into the field →01. Moreover, Ethernet-APL simplifies the direct connection with enterprise systems, thanks to several specific features →02 that are beneficial for plant operation, including:
- 10 Mbit/s data communication rates, orders of magnitude greater (>300 times) than decades-old HART and Fieldbus protocols
- Single twisted pair of conductors within a shielded cable that simultaneously carry process data, device configuration and diagnostic data as well as power
- Accommodates trunk and spur network topologies familiar in the process industries, with a trunk length of up to 1,000 m – an order of magnitude greater than regular Ethernet’s 100 m limit
- Intrinsic safety is fully integrated, including a profile that limits supply voltage and current to eliminate the risk of sparking in hazardous environments
- Works with most common industrial Ethernet protocols (including PROFINET, Modbus TCP and OPC UA)
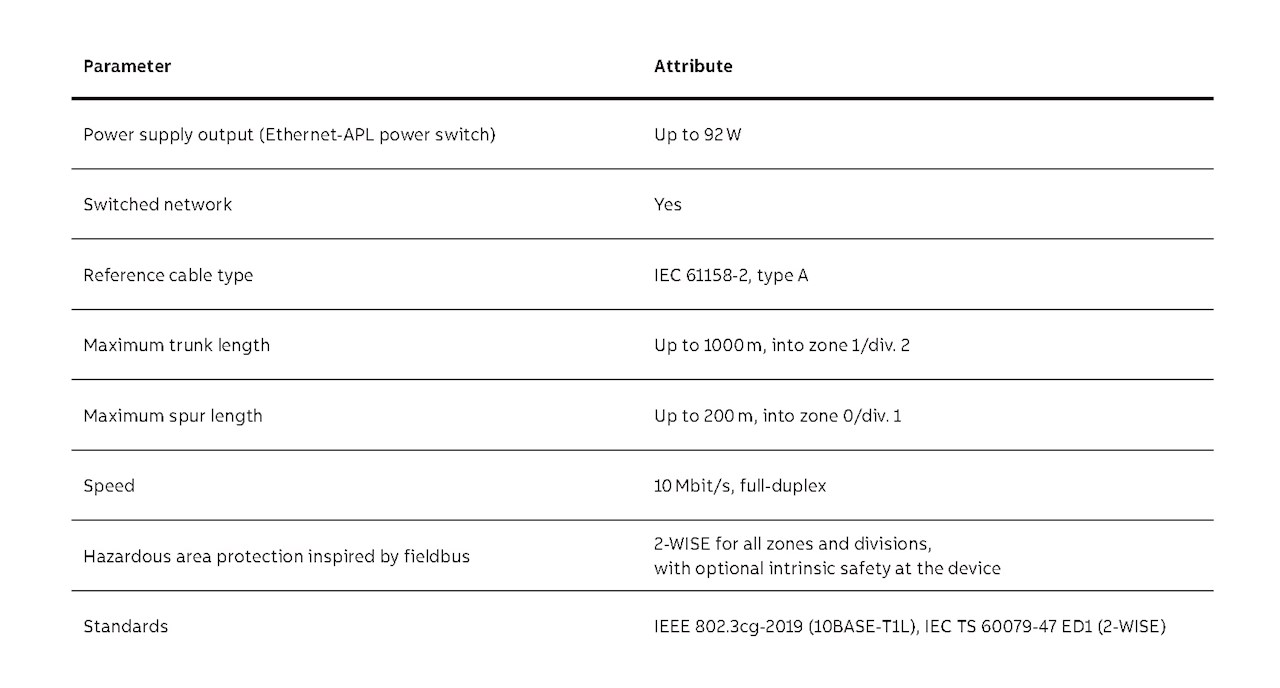
Scalable, simple and cost-effective
Providing a high-speed channel for process data as well as configuration and diagnostic information, Ethernet-APL offers a readily scalable solution for connecting devices in the field to a distributed control system (DCS) via a single cable with power carried over the same physical link as well.
Moreover, Ethernet-APL significantly simplifies installation, eliminating the need for the traditional I/O modules of programmable logic controllers (PLC) or a distributed control system (DCS) because the controller can access the device data directly, instead of via an I/O module that converts analog standard signals and sends them to the central processing unit (CPU).
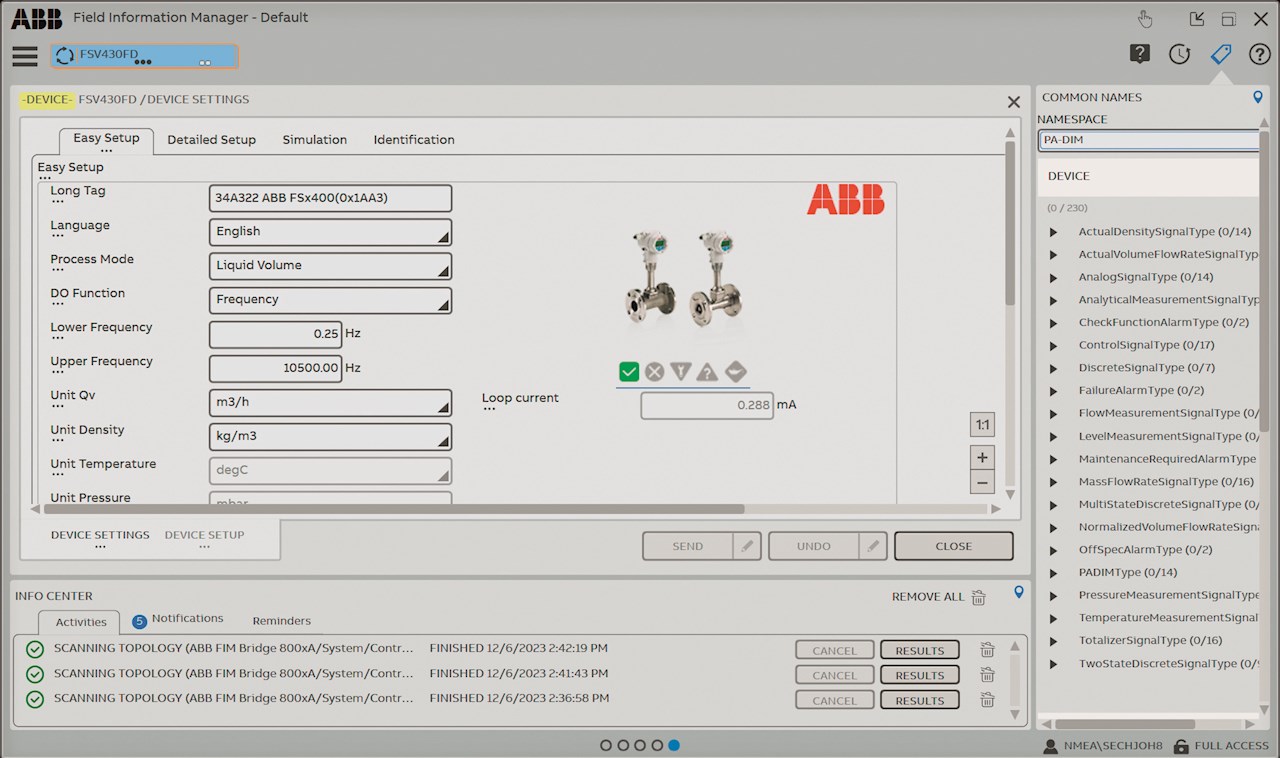
Ethernet-APL network equipment and field instruments are steadily becoming available to the market [1]. ABB has already deployed the technology in a number of large-scale automation projects. Ethernet-APL has been combined with ABB’s Ability™ System 800xA® DCS and with CI871 PROFINET communication interface →03. Up to 252 field instruments can be directly connected through one APL network ring to a controller, while remote I/O can be connected over the same PROFINET ring to collect auxiliary signals that do not originate from APL-enabled devices. Such a combination of technologies helps to simplify engineering: less cabinet space is needed than for classical I/O device solutions and for earlier fieldbus solutions such as PROFIBUS PA or Foundation Fieldbus. The ease and speed of access to device diagnostic and configuration data also facilitates faster commissioning, together with quicker troubleshooting and reduced lifecycle cost by leveraging asset management solutions →04.

Ethernet-APL complements PROFINET
PROFINET, an advanced communication protocol, has become a dominant platform for industrial Ethernet as the market share of other fieldbus technologies has declined steadily over the last decade. Building on the proven foundations of Ethernet such as reliability, PROFINET has several features tailored specifically to its use in process automation environments; these include redundancy, the ability for online configuration, PA-Profile and functional safety (with PROFIsafe as an optional feature).
Already widely accepted and used in remote I/O and electrical integration applications, the appeal of PROFINET is further enhanced by the imminent arrival of a new generation of Ethernet-APL devices and current efforts by instrumentation vendors to implement PROFINET with PA-Profile 4.02.
The PA-Profile 4.02 offers greater freedom for users to achieve improved engineering efficiency through true interoperability between devices from different vendors. While the PROFINET protocol provides a reliable way of transmitting data over a network, no actual meaning or structure is applied to that data. Instead, this function is served by application profiles that act as an extra abstraction layer positioned between the device application and the PROFINET networking stack. This approach simplifies the interface for the application engineer and ensures genuine interoperability among devices from different vendors. When designing control application code, an application engineer can interact with the profile instead of the specific device, thereby enabling the reuse of knowledge, code, and troubleshooting methods irrespective of the device’s vendor.
Since the device is interfaced using the profile, the device as such can be replaced as long as the new device supports the same profile. It is expected that some 80 percent of devices will be able to use this generic profile while only 20 percent will require a specific profile. For example, a specific device driver is typically used for more complex devices such as valve positioners and analyzers.
A key requirement in the process industry is the ability to manage control system configuration changes online without causing any disturbance to the process that could result in downtime, and, or speed/quality losses. PROFINET provides this ability, with functionalities that provide for online configuration changes, including the ability to reconfigure, insert, remove, or replace devices or modules in the system. Additionally, plant modifications and expansions can be implemented in a running system. By combining the automatic device replacement with the device interoperability of PA Profile 4.02, system maintenance users can ensure non-stop operations because the powerful system functionality enables them to manage breakdowns or complex maintenance activities at any time of day.
Of course another key feature of PROFINET is high availability. By providing different levels of redundancy, with the mandatory inclusion of S2 redundancy with PROFINET PA Profile 4.02 devices, the requirements of most real-world process automation applications are satisfied.
Going forward, by including safety applications using PROFIsafe, which ensures functional safety at the field level up to Performance Level (PL) e and Safety Integrity Level (SIL) 3, common uniform communication technology for process automation can be achieved that can be applied across the full spectrum of industrial environments, even those that are high risk.
Making device diagnostics available for control room operators
Diagnostic information from Ethernet-APL devices can be made readily available to plant operators, where NAMUR NE107 conditions and indications are natively supported from the Ethernet-APL device via the control application to the operator’s screens in the ABB Ability™ System 800xA® Operator Workplace →05. This ready availability of diagnostic information allows operators to contribute proactively to maintenance activities in their daily operations.
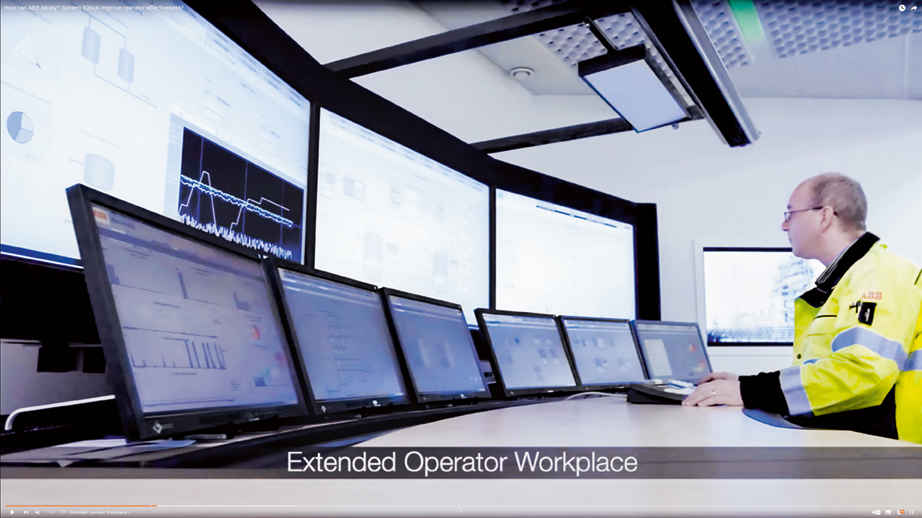
Configuration using FDI over PROFINET for Ethernet-APL devices
ABB Field Information Manager (FIM) simplifies the configuration, commissioning, diagnostics, and maintenance of field devices. A typical FIM deployment with Ethernet-APL serves as a direct bridge to the PROFINET network. FIM can scan, auto-detect, and assign device packages to the connected Ethernet-APL devices. Direct connection to the PROFINET network also provides a separation from the mission-critical control system, in line with the NAMUR Open Architecture (NOA) philosophy.
FIM supports integration of field devices either via Electronic Device Description (EDD), Field Device Integration (FDI) packages or via the latest PA Profile 4.02 device package. The latter is used where ever customers want to benefit from field device interoperability. Ethernet-APL switches are also integrated in FIM, enabling configuration and diagnostic checking using the same workflow and tooling →03.
FIM also provides an OPC UA interface for applications such as asset performance management to leverage device diagnostic and performance data. The Process Automation Device Information Model (PA-DIM) can be applied on this OPC UA interface to further standardize the data stream to edge devices and the cloud.
Enhanced maintenance, health, and performance monitoring
The high data throughput provided by Ethernet-APL enables asset management applications for maintenance, health, and performance monitoring across a fleet of field instruments. This diagnostic data can be routed to the operators in the control room as well as outside the DCS system, where maintenance can perform detailed analysis of the diagnostic data →04. This enables better collaboration across different teams on maintenance activities.
Following the NAMUR NE107 standard, this diagnostic data helps operators and maintenance personnel to identify the possible cause of failure and suggested actions to resolve the problem. This provides clear guidance on how to resolve problems with field instrumentation.
The use of ABB Ability™ Edgenius with Asset Performance Management (APM) applications opens new possibilities for early detection of issues, thus ensuring continuous operations while optimizing maintenance work and reducing costs across the fleet of field devices.
The ultimate solution
The promise of faster and easier access to data holds the key for organizations looking to optimize their performance through enhanced process control. By helping to address many of the hurdles that have traditionally hampered gathering, relaying, and accessing data in industrial applications, including suitability for deployment in hazardous areas, Ethernet APL presents the ultimate solution to meet the growing demands being placed on process control systems.
By resolving many of the challenges of using ‘traditional’ Ethernet as the physical layer in an industrial setting, Ethernet-APL offers an optimal fit for process plants, especially when it is deployed in combination with widely adopted PROFINET and FDI technologies.
Reference
[1] APL Consortium, “Ethernet-To the Field”, White paper, 2021, pp. 1 – 17, Available: https://www.ethernet-apl.org/wp-content/uploads/2022/08/Ethernet-APL_Ethernet-To-The-Field_EN_FINAL_June-2021.pdf [Accessed: Jan. 7, 2024.]