Originally published in Control Engineering on February 14, 2024.
ABB discussed future process control capabilities, cyber security services and integrated asset management to help users interact with automation more easily, as discussed at the 2024 ARC Industry Forum.
Learning objectives
- Understand how a distributed control system (DCS) of the future will include a process control system with enhanced capabilities, said ABB at the 2024 ARC Leadership Forum in Orlando.
- Learn how process control cyber security can improve with cloud-connected services, ABB said.
- Examine options for how workers can connect with plant assets more logically and see how advanced batch controls provide more advantages.
DCS of the future insights
- A distributed control system (DCS) of the future will include a process control system with enhanced capabilities, said ABB at the 2024 ARC Leadership Forum in Orlando.
- Process control cyber security can improve with cloud-connected services, ABB said.
- Workers can connect with plant assets more logically and see how advanced batch controls provide more advantages.
Advances in process control systems, cyber security services and in connecting workers with automation were among ABB topics in a Feb. 5 preview to media and analysts at the 2024 ARC Leadership Forum in Orlando and subsequent discussions with Control Engineering.
Distributed control system (DCS) of the future: Enhanced process control system
Luis Duran, ABB Global Initiatives and Strategy Manager – the DCS, edge and cloud, outlined a vision for the ABB process automation vision to provide the DCS of the future (Figure 1). Data drives digitalization, but ABB said an average chemical plant uses less than 20% of the data it generates. Interoperability of DCS, edge and cloud applications enhances real-time data analysis and decision-making capabilities in industrial environments. Emerging edge and cloud technologies change the automation landscape when combined with the future DCS to enable companies to transform more of this data into actionable insights to achieve smarter and more sustainable operations.
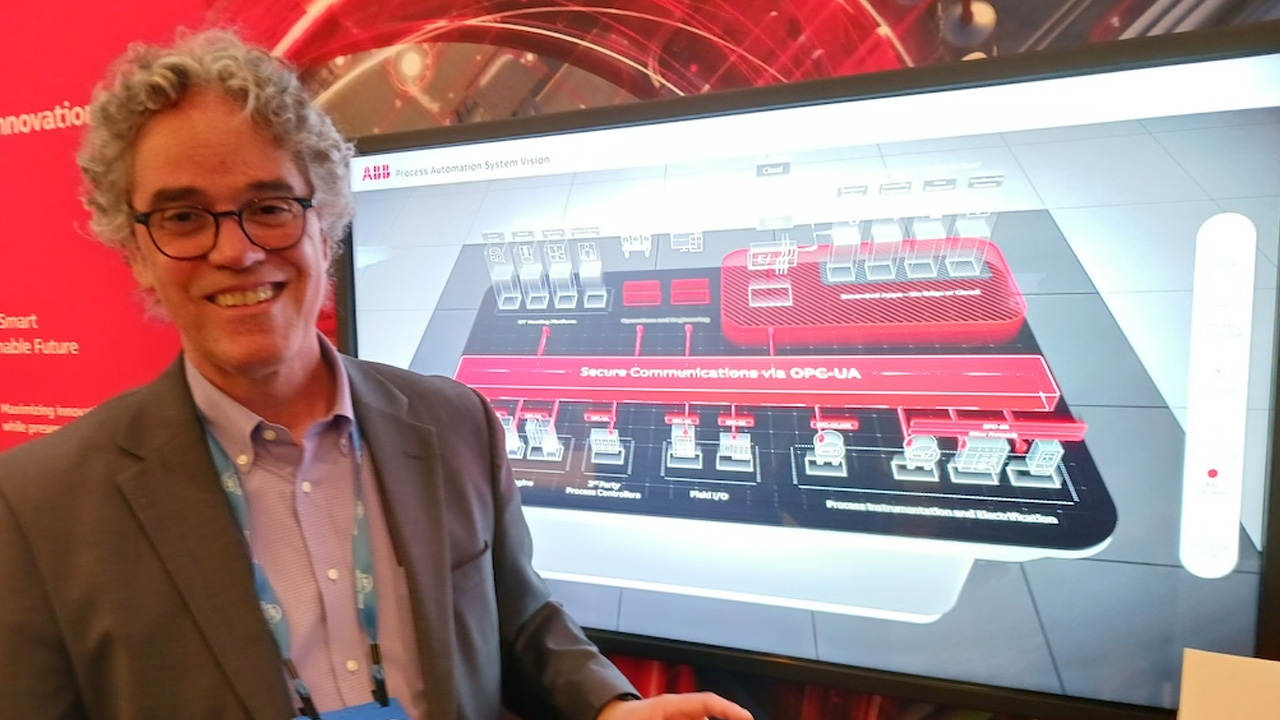
New expectations include the need for faster production, more diverse use of technologies, Duran explained. One size won’t fit all applications, next-generation workers are digital natives, and energy transformation requirements are less predictable than in the past. Past systems didn’t easily allow interoperability and became obsolescent. Today’s world requires process controls that are modular, standards-based, interoperable, securable, reliable, affordable and easy to use while enabling digital transformation and automating engineering management across industries. Information needs to be integrated and available to other parts of the organization transparently (Figure 2). Duran said helpful tools include the ABB Digital Experience, ABB Ability™ Genix and ABB Ability Edgenius. The core of these upgrades began 10 years ago, Duran said, and help sustainability and automation for electrification needed today, with help from domain experts.
Standards and implementations underway following Open Process Automation Forum (OPAF) are for components, not systems, he said. OPAF builds profiles into an architecture, and products will be available over the next few years. Those with a need for a DCS upgrade can do so today, Duran suggested, and ABB can help. Duran said ABB has strong process control system integration and process system architecture experience having integrated 13 DCS platforms through acquisitions over the past 20 years. Because of the technologies and standards, the next process automation platform upgrade can be the last one and include the OPC Unified Architecture (OPC UA) backbone for networking and communications.
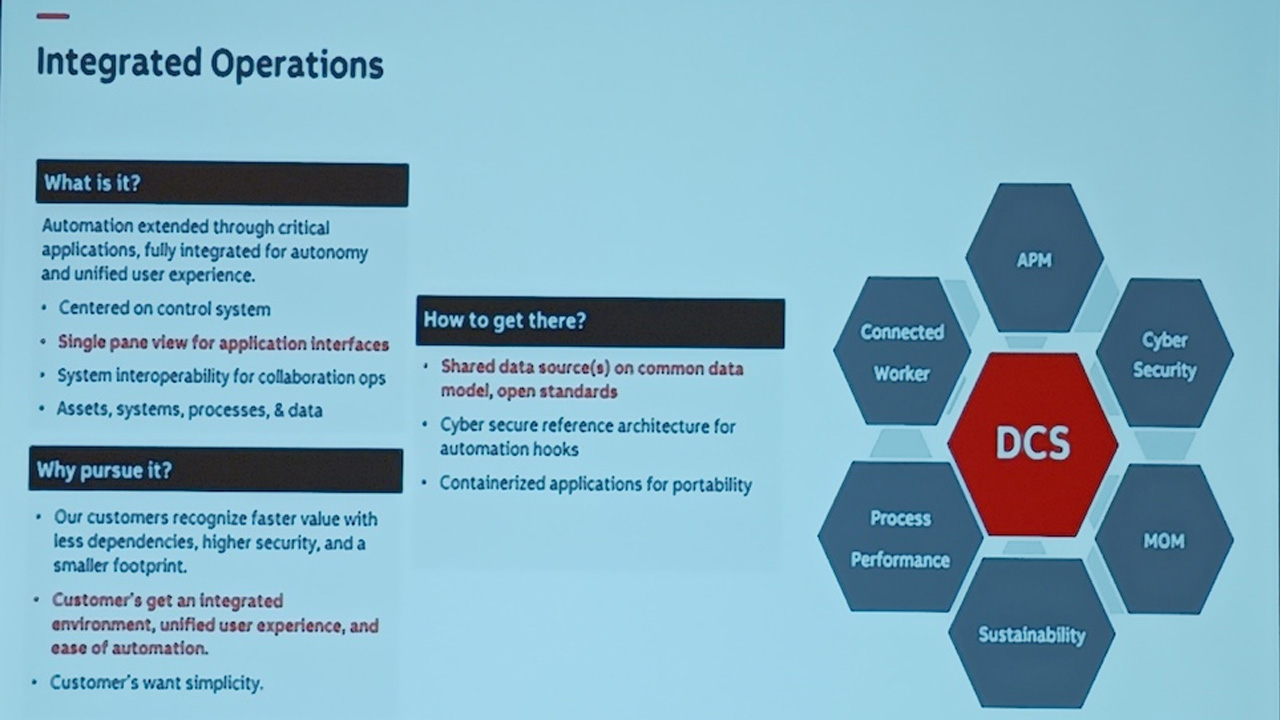
Process control cyber security advantages through cloud-connected services
Patrik Boo, ABB Commercial Portfolio Manager, Cyber Security, in a news conference, said developing and implementing a process control cyber security risk reduction roadmap is easier when using the ABB Cyber Security Workplace web portal for implementing industrial cyber security (Figure 3).
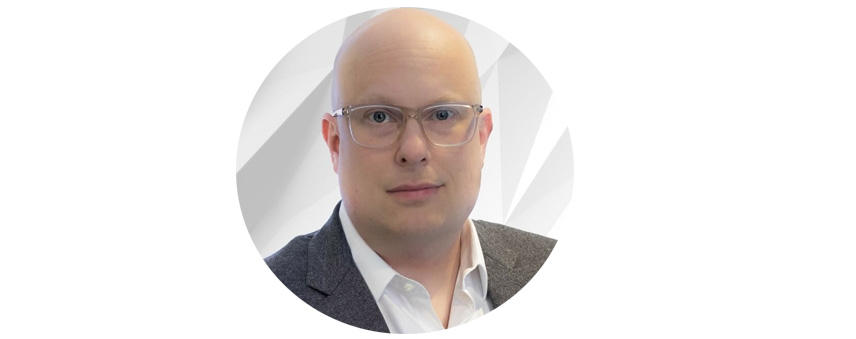
More industrial companies are recognizing increased cyber security risks getting more advanced with cyber security, Boo said, by hiring dedicated cyber security personnel.
Known threats to cyber security number 1.2 billion and grow by 350,000 malicious programs daily; 81% of cyber security information security officers (CISO) in the energy sector reported a clear rises in cyber security attacks in the last two months; and 83% of organizations report improving efficiency by introducing internet of things (IoT) technologies, Boo said.
Because of the breadth and depth of control systems in many plants, it may be impractical to implement fully redundant backup systems for the entire plant. Assessments help stakeholders calculate risk to figure out how bad an outage would be to each system, providing greater understanding of which systems are most critical, Boo said, asking questions such as:
- If a control system were only down for 24 hours, would the company and its connected suppliers and customers recover?
- Which systems need to be up and running sooner? (An eight-hour recovery could be a huge investment.)
- Which systems might be able to wait longer for full recovery?
Site decisions need to be made about the level system criticality, and connections to cloud-based cyber security can help with that. The ABB cyber security web portal can be used to help:
- Assess with a system finger print and risk assessment.
- Plan with consulting services.
- Implement a reference architecture, malware protection, security updates, backups, system hardening, asset inventory, allowed applications listings and training.
- Sustain and maintain.
- Detect network monitoring and event monitoring.
- Monitor security operations.
- Respond to incidents.
In 2024, ABB plans product expansion to view cyber data from anywhere. ABB’s new ransomware resilience information outlines how organizations can improve resilience by focusing on prevention and recovery, and what critical measures must be taken to protect their critical infrastructure. ABB’s upcoming Cyber Security Workplace (CSWP) FleetView will provide a complete picture of security operations across all assets to help operators identify and remediate cyber risks quickly.
How to connect workers to plant assets; advanced batch controls
Luis Gamboa, Segment Director for Global Partner Business, said asset-intensive industries face multiple pressures including difficulty finding people, margins, throughput, sustainability, returns on asset performance, regulations and safety. A point of differentiation among competitors can be more tightly integrated operations. What is integrated operations management (IOM)? Why can more integrated operations help and how can industrial organizations get there?
A connected worker moves away from disconnected paper-based practices. Also, memory-based execution can introduce errors into processes and can be the default with lack of time and inadequate access to information when needed in real time. Gamboa said paper-based or memory reliant practices result in:
- Data duplication
- Manual data input errors
- Lack of support for other operations
- Lack of systematic capture of variations and non-conformances
- Limited and sporadic improvements.
ABB upcoming operational excellence portfolio product launches will help, Gamboa said. ABB launches in the operational excellence space are designed to drive digital transformation and autonomous digitally connected workforces.
ABB Ability Connected Worker applications enhance health and safety, increase efficiency by standardization and digitalization and improves field operation collaboration, Gamboa said. The updated ABB Ability Connected Worker has new functionalities that further digitalize the field operator experience to mitigate the risk of human error and unplanned downtime. Said to be a state-of-the-art digital solution, it supports field operators step-by-step through critical procedures to provide more flexibility, control and ease-of-use.
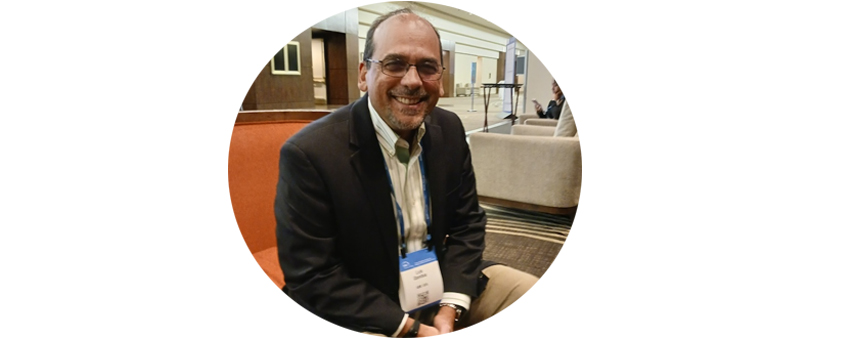
Late in the first quarter, Gamboa said, ABB Advanced Batch Management portfolio will help users automatically or manually schedule batches. It adds capability to ABB Ability MOM Report [MOM is manufacturing operations management] and ABB BatchInsight products. ABB Ability Advanced Batch Management (ABM) is a new application software package that helps overcome manufacturing challenges and accelerates process improvements with better data visibility. It configures and schedules batch operation by enabling communication and integration of batch management execution systems with company-wide enterprise resource planning (ERP) systems, to improve production profitability, consistency and traceability.
Late in the second quarter, ABB Ability PlantInsight – Operator Assist will add functionality to industrial operations by providing dashboards for early alerts to avoid deviation from steady state conditions, Gamboa said. Other functions include heat map, daily support and incident mitigation. ABB Ability PlantInsight Operator Assist is a new solution to address the challenge of continuous operations by providing plant operators more visibility into process parameters through a robust and reliable operator-assisting technology.