“We are truly on the verge of a new innovation,” describes Lekatech CEO Antti Anttila.“We are developing a completely new linear electric motor technology for hammering, a world first, with support from ABB,” adds Anttila.
Based in Iitti, Finland, Lekatech began as a startup, and is now a part of Normet Group. It manufactures mining machinery and equipment and is a pioneer in electric solutions. The company's core business is strongly based on energy efficiency and environmental awareness.
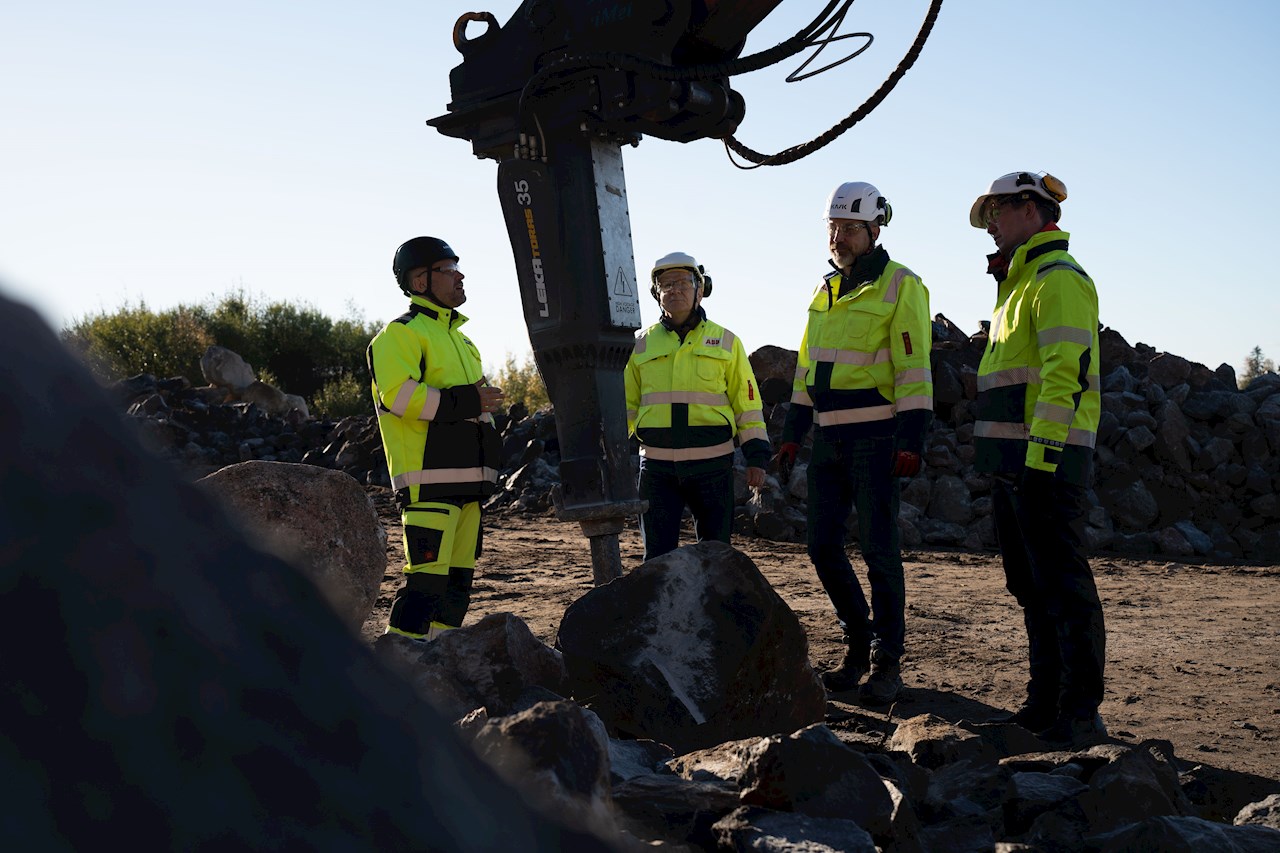
Collaboration and tailored solutions at the core
The project began with the need to develop an electric solution to replace the traditional hydraulic impact hammer. Lekatech needed a competent partner to control the motor of a new linear hammer. “ABB was immediately enthusiastic about the topic, and their versatile products in combination with their strong application expertise made them a natural choice as a partner. Our collaborative experience has been very positive,” Anttila says.
The project was no ordinary one for ABB, as the HES880 frequency converters, developed for mobile machinery applications, had not previously been adapted for linear motors. The software application tailored for Lekatech therefore differs significantly from a standard frequency converter application. ABB's application specialist Asko Salminen specially developed the software for the HES880 frequency converter together with Lekatech's experts.
“Generally, motors rotate, but in this application the motion is back and forth, like hitting with a hammer. I created a special program inside the frequency converter that enabled the desired movement and allowed the impact force and frequency to be adjusted. We tested different ways to control the device, and eventually found the best settings,” says Asko Salminen.
Image currently unavailable
Image currently unavailable
Image currently unavailable
Image currently unavailable
Image currently unavailable
Image currently unavailable
The hammer is controlled with an application software, which was tailored specifically for the LekaToras hammer. Image: Lekatech From ABB, closely involved in the project was Asko Salminen, a member of the OEM Hub expert team of application specialists
The HES880 was chosen for the project because it has built-in support for application programming, meaning that the operation of the frequency converter can be adjusted without changes to the standard software. This feature allows the customer to complete the application programming themselves or, as in Lekatech’s case, obtain it as a service from ABB’s OEM Hub*.
Energy efficiency and responsibility guide development
The electric hammer consumes up to 98% less oil than the typical hydraulic hammer, improving energy efficiency. “The energy efficiency of an electric hammer is in a class of its own. It uses up to 70% less energy than a comparable hydraulic hammer, which makes it a very interesting application from ABB's perspective,” says Pekka Mattila, Product Manager at ABB.
The development of the Lekatech electric hammer is linked to the electrification of work machines, as the hammer is specifically intended for electrically powered machines. “The only factor limiting development is that electricity is required to use the device. All other factors are positive compared to the technology currently being used," Antti Anttila states.
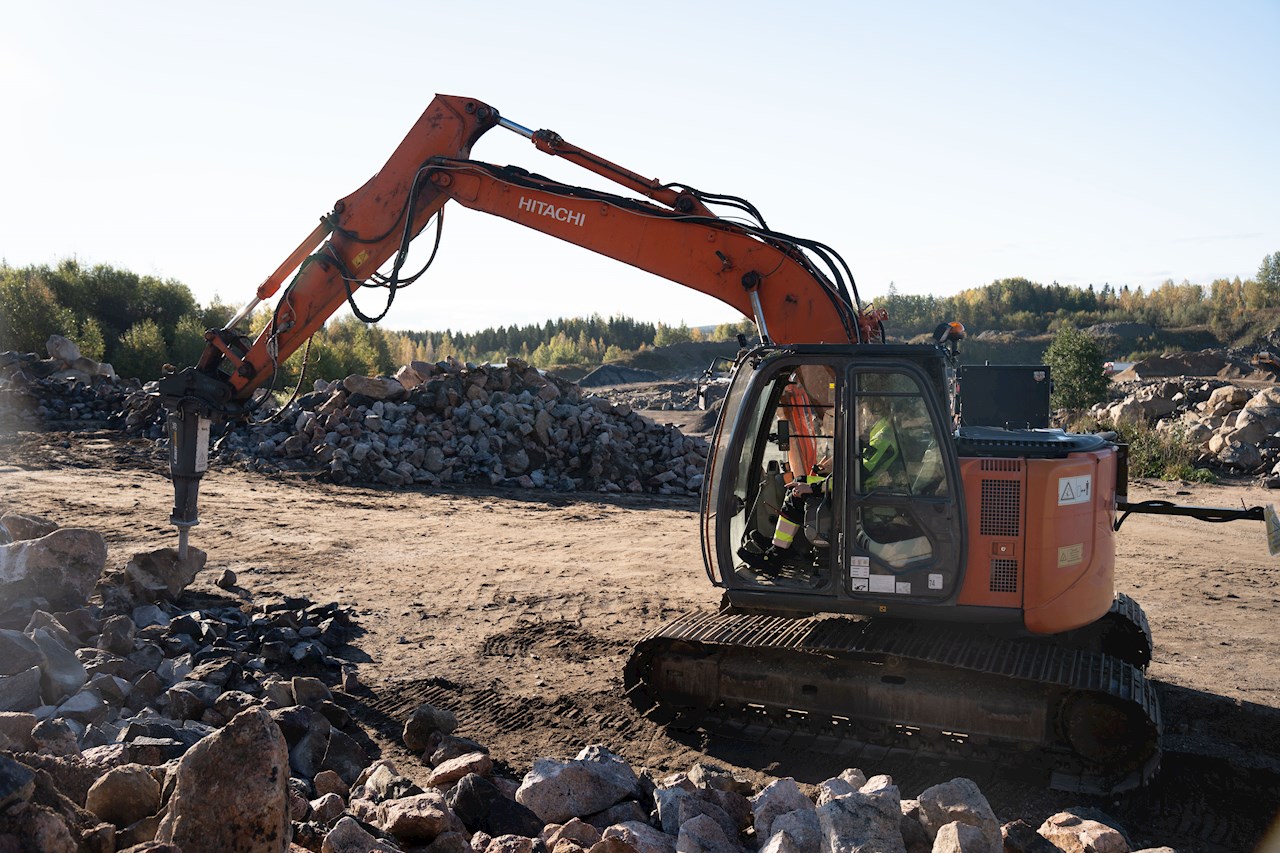
Future markets and commercialization
Lekatech is already very close to commercializing the product. "For a couple of years, we have been testing several pilot hammers in different environments, such as demolition sites and mines, and the results have been promising," says AnttiAnttila.
Lekatech expects that the demand for electric hammers will grow significantly in the coming years, and they are preparing to commercialize the devices in the coming months. The first deliveries will be directed to so-called zero-series customers, with whom we will continue to gather user experience.
"Development is inevitable, and in ten years the electric hammer will be a given," Antti Anttila believes.
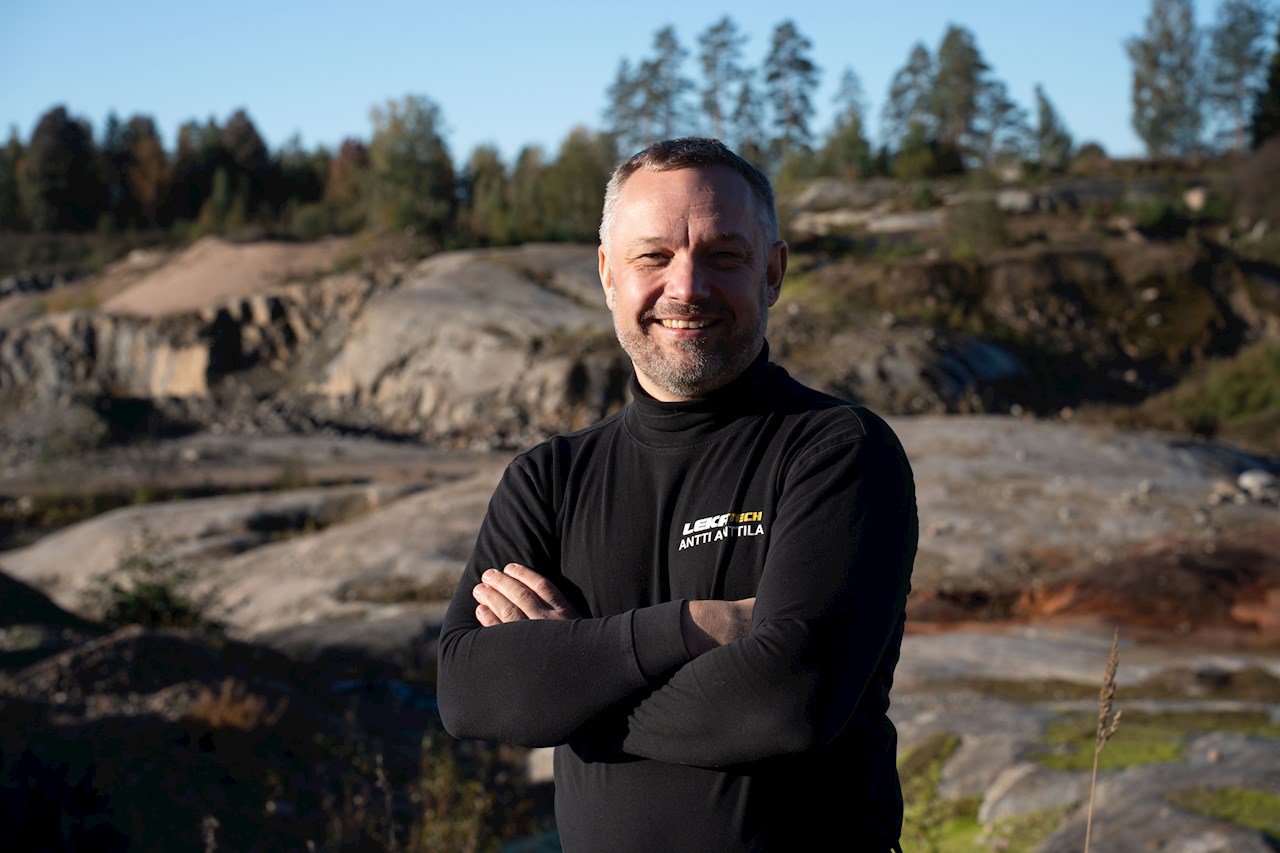
Through strong collaboration with Lekatech and adapting standard solutions for new innovative applications, ABB is helping hammer industry operators to run leaner and cleaner through more sustainable, efficient, and productive operations
*The ABB OEM Hub is a team of ABB application specialists that in close collaboration with its customers researches and develops tailored software applications to customers’ application requirements. In short, the OEM Hub team is ‘your external software R&D team’.