In 2021, the machine manufacturer Junttan from Kuopio, Finland, launched the world's first electric piling machine. Those were the early days of the electrification hype, and Junttan strongly followed megatrends and encouraged sustainability.
"The initial catalyst for the electrification project was a customer who wanted to be a pioneer in these products. Even though we are a small manufacturer, we want to be at the forefront of technology, so when electrification becomes mainstream, we are no longer at the starting point " says Tomi Voutilainen, Junttan's Product Manager. Considering its size, Junttan is also ahead of time on the international scale, not only in Finland.
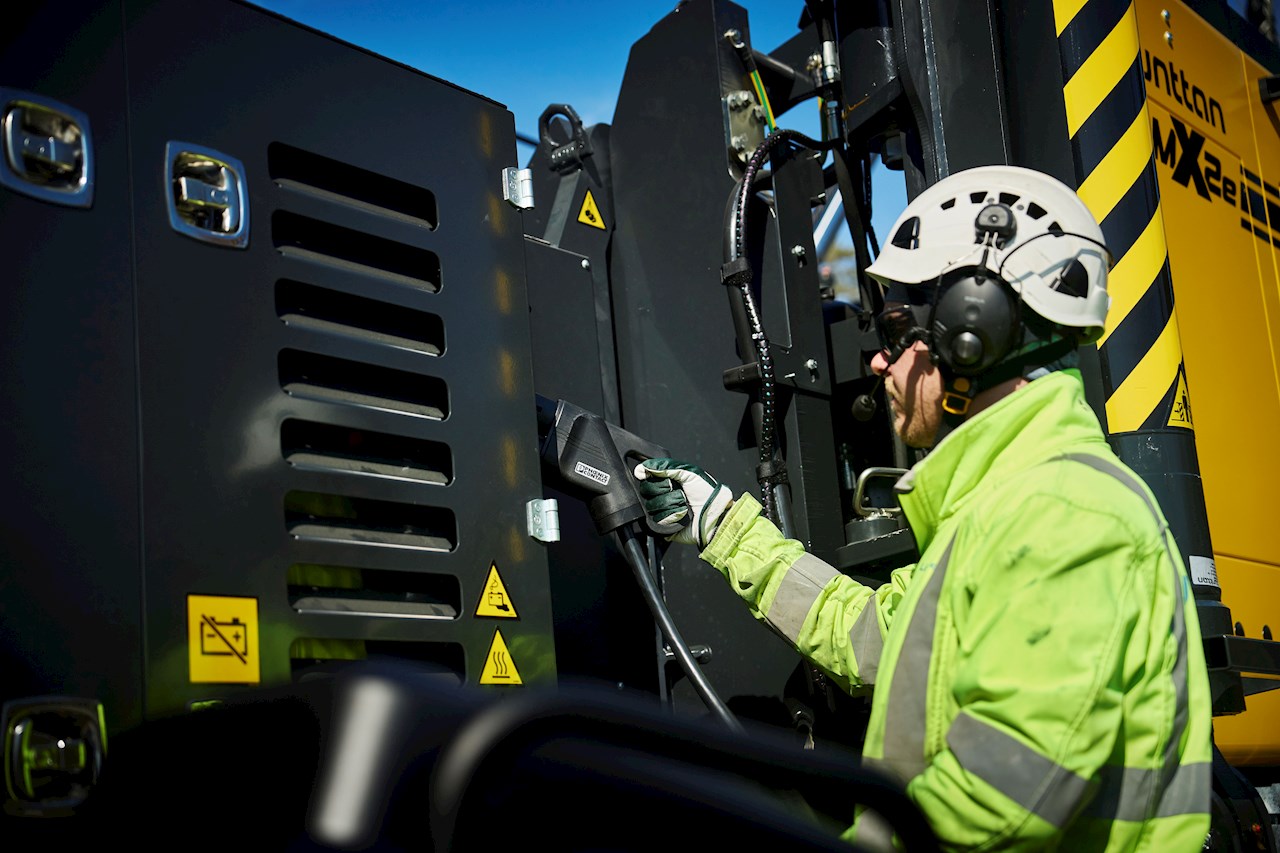
The cooperation network helped to succeed
The machine was developed in direct cooperation with the customer, so Juntttan had to create the cooperation network on a tight schedule. Hevtec, a Vantaa-based long-term operator specialized in electrification, was selected as the system integrator. Hevtec was responsible for the control and electrical design of the electric power line and advised on the selection of the components. "We wanted reliable, secure and ready-made components on a tight schedule. That's why they were ordered from ABB", summarizes Sami Martikainen, Junttan's Operational Project Manager.
According to Heikki Hakala, Hevtec's Chief Technology Officer, all challenges and requirements were openly discussed in the project. "We have in-depth expertise and understanding of the components, while machine manufacturers know their own application precisely. Hevtec's expertise is to combine these elements: we find out from the machine manufacturers what they really need, and then we recommend the right components. Our project is a strong example of how Finnish collaboration can achieve a really great end result "
We wanted reliable, secure and ready-made components on a tight schedule. That's why they were ordered from ABB.
"In such a project, it is important to understand the end customer's needs, and to be able to bring the right components to help the machine manufacturer in the best possible way," agrees Pekka Mattila, ABB Product Manager.
The HES880 mobile inverter was selected for the project as it is designed for harsh environments with high shock and vibration requirements and a wide range of ambient and coolant temperatures. The drive integrated seamlessly into the whole system ensuring the power needed for the working machine. HES880 drives are key to electrifying heavy duty machinery, helping customers increase productivity, while reducing C02 emissions.
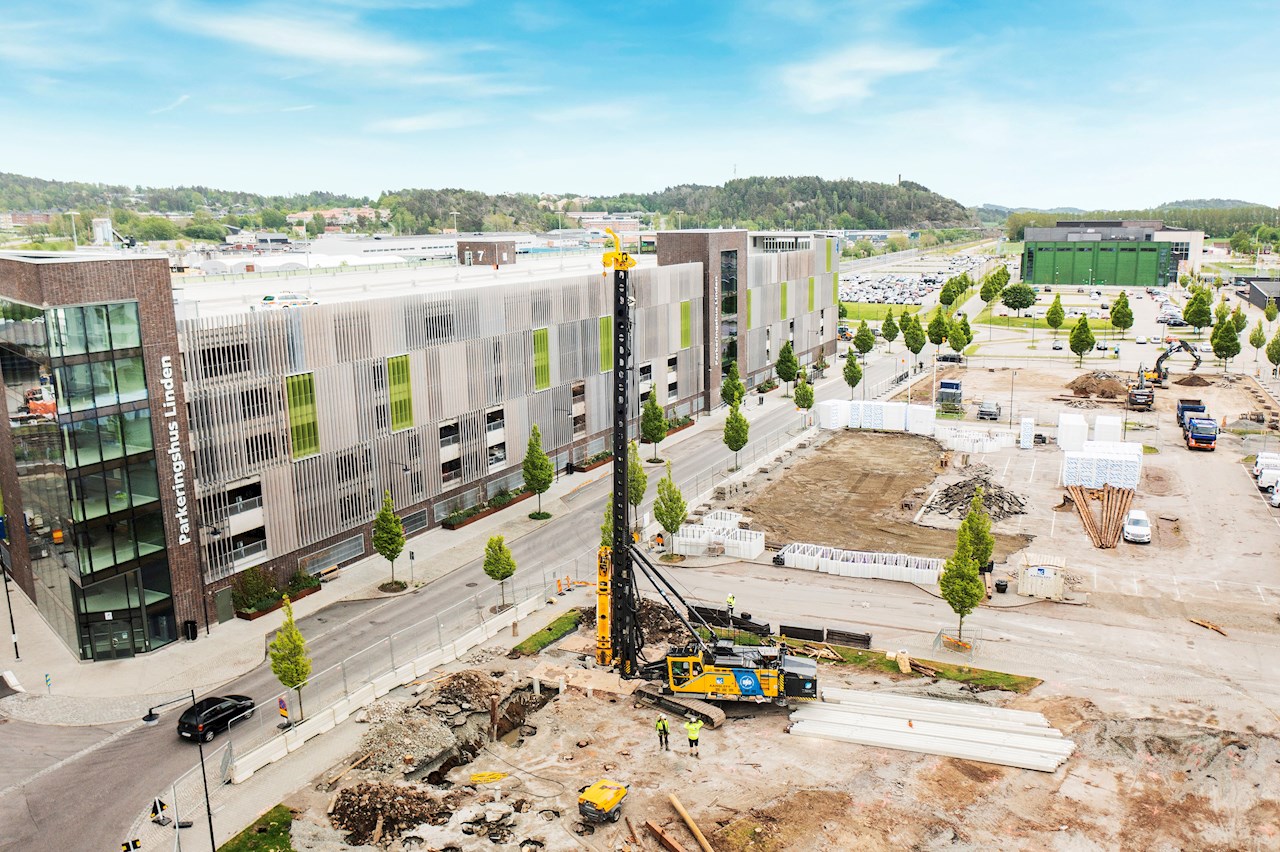
The benefits of an electrified machine
An electric working machine has many advantages: it doesn’t produce CO2 emissions or require much maintenance; it is user-friendly and quieter. "The battery-powered machine is a zero-emission solution for future zero-emission sites. A positive surprise for us was how quiet it is compared to a diesel-powered machine. Of course, it’s also a good thing for the environment," says Tomi Voutilainen, Junttan's Product Manager.
For the machine operator, electrification means the machine doesn’t "lack torque" because the power comes immediately from the electric power line. "Utilizing an electric machine is inherently better, because it has better adjustability and power output," emphasizes Heikki Hakala, Hevtec’s Technology Director.
The aim was to make the charging of the machine as easy and flexible as possible that it is practically the same as with electric cars.
An open ecosystem
It was also important for Junttan to create an ecosystem open to electrification, where components can be varied flexibly. "We try to be as agile as possible as an operator. The advantage for us and for our customers is that if the production of a component stops, many years of work will not go to waste, as we can quickly map the need for the component and define replacement solutions," says Tomi Voutilainen, Junttan's Product Manager.
Switching from one ecosystem to another would be a much larger project that inevitably generates waste.
A pioneering market
In Europe, from 2025, the electrification of working machines will be guided by the EU's green transition roadmap. Currently, only a fraction of Junttan's production is represented by electric machines. They are primarily aimed at the Central European pioneer market, which has a strong investment support system.
"In the long run, it's all about dispelling the fears of customers and the industry. New technology is easily perceived as something completely miraculous. But I believe that the pace of electrification will accelerate in the next five years. Our project is a first example of how a Finnish network can achieve a truly great result on a global scale ", Tomi Voutilainen, Junttan's Product Manager said. “Junttan intends to keep up with the pace and push others. The key to success is cooperation.”
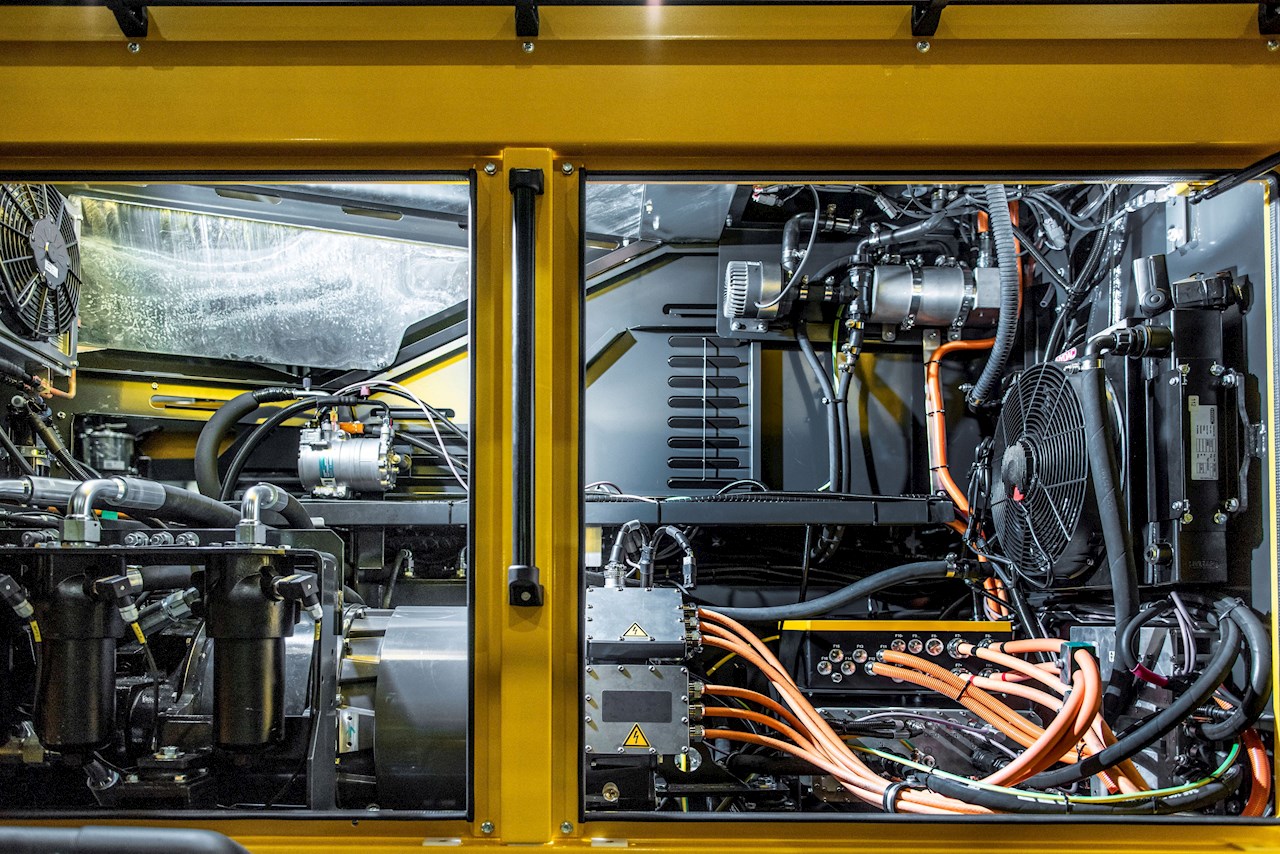
“ABB has been involved in the electrification of heavy vehicles for decades, and the development of the current generation began more than ten years ago in Pitäjänmäki, Helsinki, Pekka Mattila ABB Product Manager points out. "As a major player, ABB can offer its long-life cycle products and support globally."
This is another example of how ABB’s technology is enabling construction sites to be safer, smarter, and more sustainable.