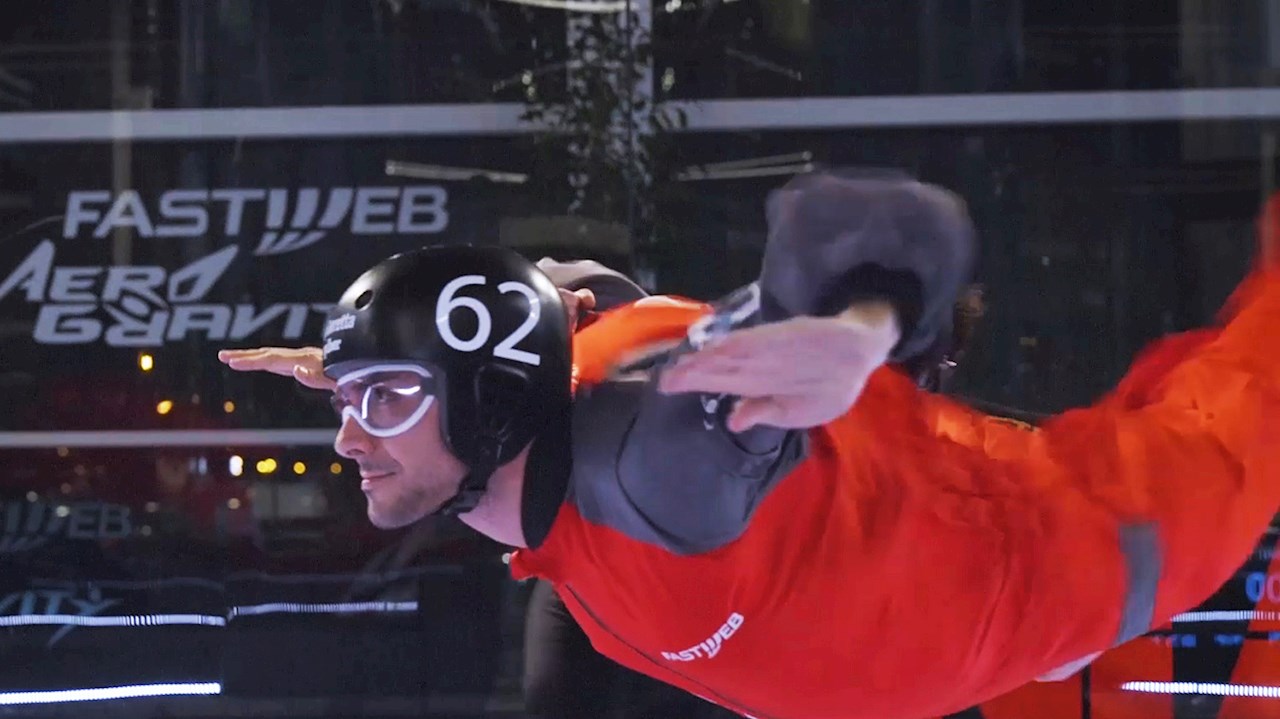
A boost of adrenaline. Sugars delivers a surge of energy. The heartbeat jumps and respiration increases, causing a rise in oxygen circulating through the muscles. It is what the human body experiences during a free-fall from say 4,500 meters.
Aero Gravity in Milan, Italy, offers that experience but only a few meters above the ground and a parachute is unnecessary. It is the world’s biggest free-fall simulator. There you will find people tumbling, gliding and twirling in a 21-meter high and 5-meter wide transparent tube.
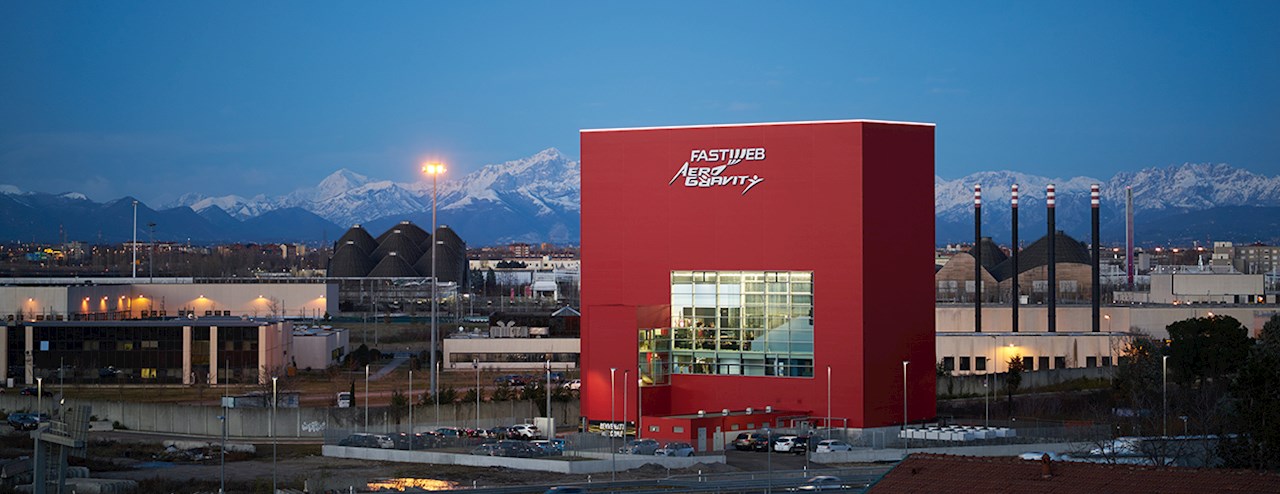
ABB technology is at the heart of the experience. Six mega-fans provides the uplift of air needed to give thrill-seekers the same experience as a free fall from an airplane high in the sky. The touch of a joystick operates ABB’s variable speed drives (VSD) on the electric motors powering the fans and ABB Ability™ digital technology monitors safety levels of the wind turbines.
More than 55,000 people enter the wind tunnel every year, ranging from advanced skydivers to families celebrating a birthday or companies motivating their workers. The center is open 14 hours a day. The long operating hours, combined with the need for second-by-second speed adjustments, call for the highest level ofof safety and operation. Preventing breakdowns and interruptions has the highest priority.
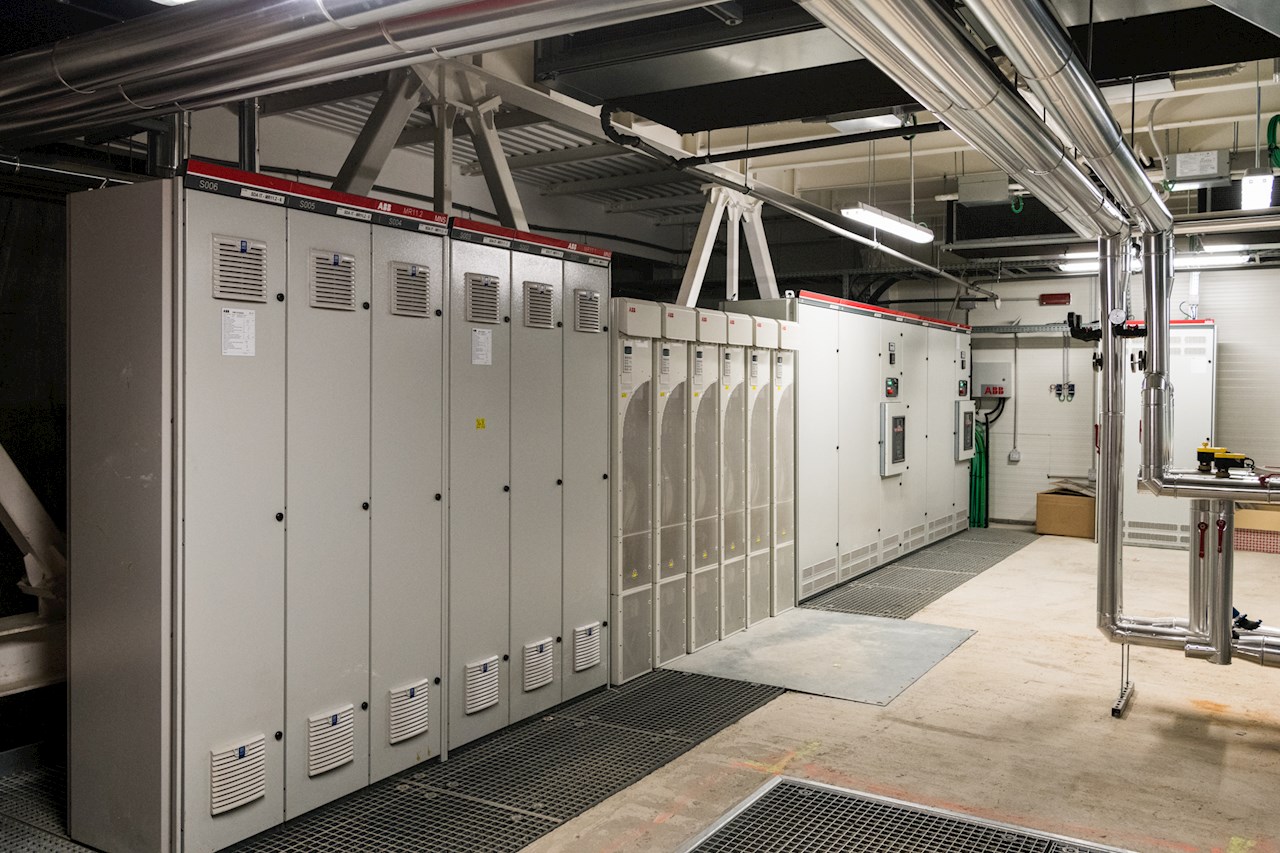
The six 400 kilowatt (kW) fans creating the air updraft each operated by asynchronous three-phase ABB M3BP 400LA electric motors and ACS 800 VSD. With a touch of a joystick, the drives enable the wind tunnel operator to regulate the air flow to meet the needs of the flyers in the chamber – ramping up from 120 km/h to a peak of 370 km/h and back down in a matter of seconds.
To meet the highest safety standards Aero Gravity uses the cloud-based ABB Ability™ Condition Monitoring tool for the drives. The service continuously monitors the status of the drives, collecting data on key parameters such as abnormal temperatures and incorrect operations.
The ABB server analyses the data and provides an overview through an indication system to identify areas that may need extra attention. ABB technicians can diagnose and analyse potential problems through an advanced set of online tools.
For Sandro Andreotti, Aero Gravity CEO, ABB technology is synonymous with safety and reliability. As an engineer, Andreotti’s father relied on ABB products for the construction of safety-critical iron and steel plants. “I have known the ABB brand since I was 12,” Andreotti said. “Based on all the products used by my father, I knew from experience that ABB is a guarantee of the essential safety and reliability we needed."
Aero Gravity also uses ABB’s service is for spare parts to ensure that replacements are always available to minimize the impact of a potential breakdown on its operations. “So far everything has worked perfectly, and we have not recorded any major failures,” says Andreotti. “The service gathers valuable feedback every day and helps us to take corrective actions. This reduces thermal stress on the equipment, which will result in longer lifetime and improve overall machine’s efficiency, while helping to maintain comfortable temperatures for the flyers in the chamber.”
Watch the video of the world’s biggest free-fall simulator:
As a leader focused in digital industries ABB also provides the drives and digital monitoring technology for Europe’s top thrill ride of 2018, the gravity-defying Loke Gyro Swing at Liseberg amusement park in Gothenburg, Sweden.