ABB has revamped the Porkkala sugar refinery’s power supply, upgrading its safety and operational reliability. The unique project was planned together with the Finnish customer to avoid production shutdowns.
A retrofit project conducted by ABB at Suomen Sokeri’s 50 year-old sugar refinery in Finland has revolutionized site safety and significantly improved operational efficiency. Suomen Sokeri is the member of global Nordzucker Group.
Work started with the replacement of an old outdoor substation with a factory-built eHouse containing 20 kV ABB UniGear ZS1 switchgear with Relion® REF615 feeder protection relays. Conducted during a planned short plant shutdown, the work has continued through a carefully managed cooperative relationship between ABB and the refinery to ensure minimum disruption to production.
When it was built in 1965, the Porkkala sugar refinery was an ultra-modern production facility with its own port, a wastewater treatment plant, and associated employee homes. The machine base has been replaced over the years, but the original power connectivity, medium-voltage switchgear and low-voltage switchboards were still in operation.
“The devices no longer met current requirements,” says Jani Timonen, power supply system responsible at Suomen Sokeri’s Porkkala refinery.
The new ABB UniGear ZS1 switchgear showcases the technological advances that have since taken place. Modern protection and control relays of Relion family have replaced the traditional electro-mechanical relays as protection systems.
“Current switchgear systems have vastly improved enclosures and safety levels. We now have extremely fast arc-fault protection, for example,” said Marko Särkkä, project manager at ABB in Finland
Särkkä continued, “The biggest difference between the old and the new system is employee safety. The open busbars of the original equipment are now consigned to the history books. Employees are shielded from live parts in the new switchgear and access to the eHouse is prevented when the systems are live.”
The project, first launched in 2014, has progressed systematically from the main power supply connection to other systems. The replacement of the 10 kV medium-voltage switchgear is now also complete, and several main distribution boards have been replaced.
The work must take place during production operations, which makes the project challenging. In August 2016, ABB took down the old switchgear in four days, and replaced it with relays that had already undergone testing.
Special projects require close cooperation
According to Timonen from Suomen Sokeri, power supply renewal projects carried out in such close cooperation between the refinery and the supplier are rare these days – turnkey projects are much more common. However, Timonen explained that the replacement of the entire plant power supply was so critical for the continued availability of the plant that the company wanted to remain in complete control of the project.
An exceptional project required a lot of planning with the customer. Good planning helped to avoid many shutdowns. For example, thanks to detailed scheduling and collaborative planning the main switchgear was replaced during full production operation. The customer had external backup generators running at various locations in the production facilities.
According to Timonen, half of the main low-voltage distribution boards feeding the machinery are still waiting to be replaced. The plant has a large number of electrical motors and variable-frequency drives. When running at full power, the combined power consumption of the plant is approximately 5 MW.
Automation helps manage disturbances
A familiar team makes the work easier. A joint project between customer, ABB and Valmet, which is supplying automation systems for the plant, is currently going on. In this project, 10 kV and 20 kV feeder terminals and remote I/O from GenSet, will be connected by COM600 and RIO600 to the plant's control room automation system.
Timonen believes that the new power supply will give peace of mind to the employees in charge of operations. Once the automation connections are in place, real-time data from the switchgear and GenSet will be sent directly to the control room. The difference becomes most prominent in fault situations.
“Until now, we had to go to the site to solve any power distribution issues. Now, the switchgear can manage issues automatically, or the problems can be handled from the control room,” says Timonen.
The refinery's power system will soon be ready to take on the challenges of the coming decades. “The cooperation has been crucial for successful replacement of systems during production operations. Without combined effort, the results would not have been so good, safe and reliable. We care about the tomorrow of our customer” says Alessandro Palin, Managing Director of ABB’s Distribution Solutions business.
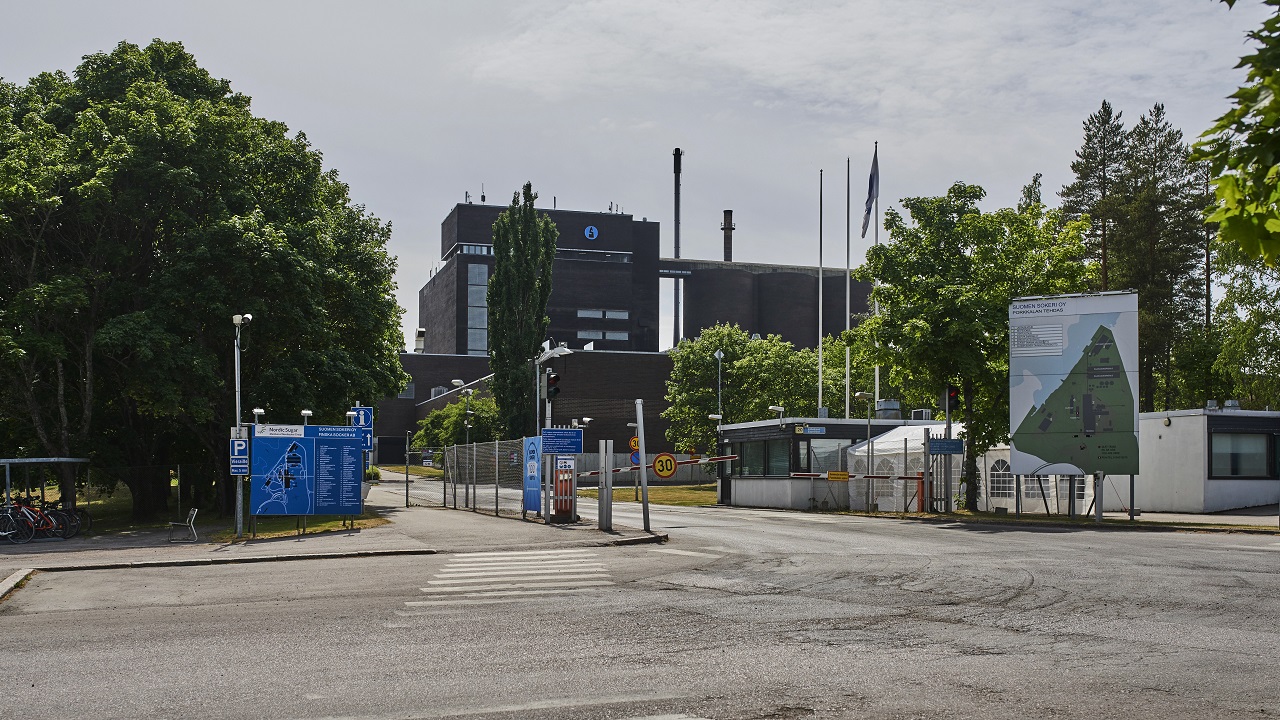