Mitigating internal arc impact in switchgear is a rare but dangerous event. ABB has launched an arc simulation platform that incorporates three gas-flow simulation tools. With this platform, the internal arc withstand capability of a product can be assessed.
Marley Becerra, Ulf Sand ABB Corporate Research Västerås, Sweden, marley.becerra@se.abb.com; Jörg Lehmann ABB Corporate Research Baden-Dättwil, Switzerland, joerg.lehmann@ch.abb.com
Unintentional electric arcs created between energized conductors in electrical systems can be highly energetic. These arcs can create plasmas with temperatures well in excess of 10,000 °C that drive a fast and violent expansion of the gas, leading to a high-energy explosion →1.
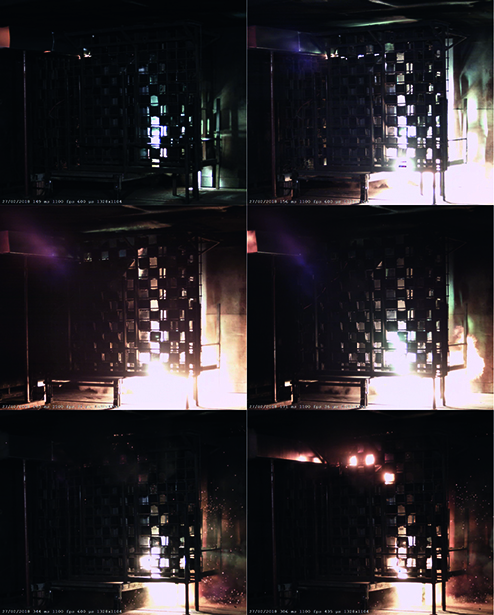
As an example, an arc fault from a 25 kA peak short-circuit current of one quarter-second duration releases an energy comparable to that of 2 kg of dynamite [1]. Such an explosive energy release stresses – mechanically and thermally – that endanger personnel and seriously damage equipment and structures.
To mitigate the harmful effects of an internal arc fault, the formed gas pressure wave needs to be directed to buffer volumes or to the exterior by using ducts or exhaust channels. In addition, pressure control devices (PCDs) such as openings, metallic meshes, bursting flaps or disks are also used to cool down the gas, to redirect the flow and to limit the maximum permissible pressure.
Products designed to protect operating personnel from internal arcing faults are usually labeled as arc-resistant. ABB arc-resistant products are tested using relevant standards (eg, IEC 62271-200 and IEEE C37.20.7) to verify that they can withstand overpressures and release hot gases away from personnel during faults. However, type-testing of such products is a very costly and time-consuming effort.
Computer simulation of internal arcs
Computer simulations of the temperature and pressure rise in a virtual prototype can be used to assess the internal arc withstand capability of a product. When validated, this approach is a valuable and cost-effective tool for cases where tests are not feasible, for early stages of product development or for validation of changes in an already-classified design. Such a simulation can also be used to identify regions in the structure where above-critical pressures will occur in the event of arcing and to locate and dimension appropriate PCDs and exhaust channels/ducts. Moreover, these calculations can provide the input data (forces) for a mechanical analysis to assess potential structural damage due to internal arcs and to virtually test a product.
According to CIGRE [1], the physical processes in internal arc faults can be calculated in different ways, using either basic or enhanced models or even computational fluid dynamic (CFD) calculations. These models all require the current and voltage across the arc fault as input, but they differ in complexity, predictive power and simulation effort. These differences are related to the simplifying assumptions they use regarding:
• Arc representation: The internal arc fault is generally represented as a simple heating source by using the empirical fitting factor kp. This factor represents the net fraction of the electrical arc energy that leads directly to the increase of pressure [1]. Alternatively, the arc can be modeled by using energy and mass sources including different physical processes (eg, radiation, metal vaporization, etc.).
• Gas properties: The thermodynamic properties of the gas are considered as constant values or as temperature- and pressure-dependent variables using real gas data.
• Geometry: The compartments containing the gas in the fault can be modeled as non-dimensional, lumped volume zones or
three-dimensional (3D) zones corresponding to the real geometry of the device.
• Flow analysis: The flow can be evaluated by using conservation of average energy and mass in the volumes (neglecting the effects of pressure traveling waves). It can also be spatially resolved in detail using a CFD analysis.
• PCDs: PCDs are represented as simple openings with a known flow efficiency factor or they can be modeled in CFD considering their actual resistance to the flow (also including the rotational or translational motion of flaps and bursting disks).
In order to meet the needs of internal and external customers, three different tools with different levels of accuracy, geometrical resolution and computational cost have been developed by ABB. These tools are known as IAT (internal arc tool), DIAS (DymoDAT-based internal arc simulations) and PRIAS (pressure rise in internal arc simulation) and their general features are shown in →2. These tools allow the assessment of the impact of internal arc faults in a broad spectrum of applications: from rapid calculations while tendering switchgear and substations, through investigations of internal arc incidents in already-installed units to product development.
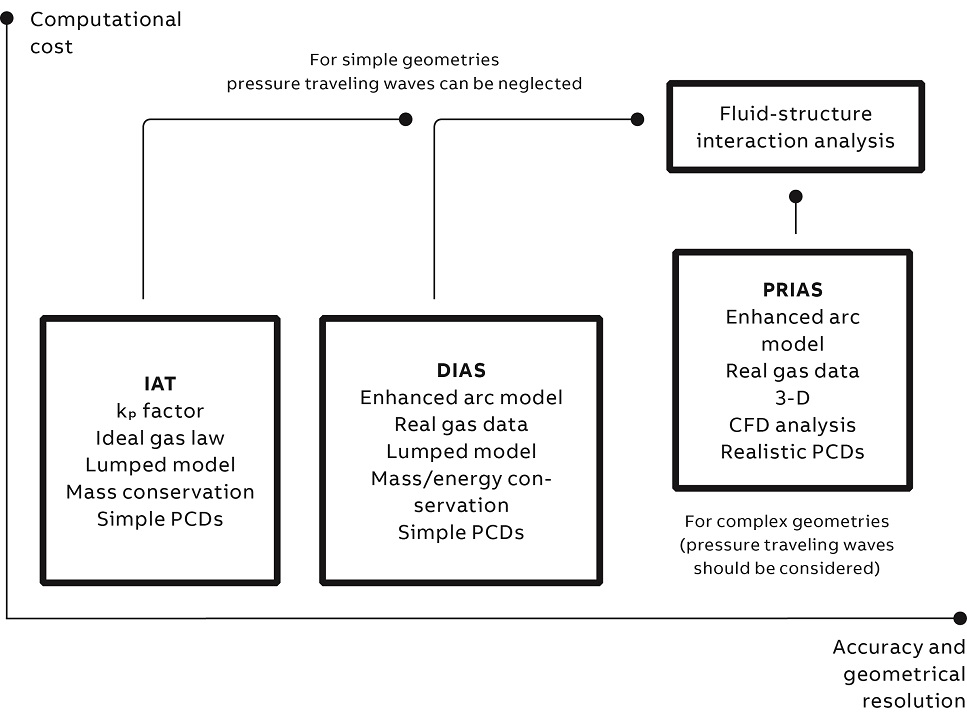
IAT internal arc tool
IAT is a fast simulation tool using a basic internal arc model with the empirical fitting factorkp, p that has already been extensively described in a previous ABB Review article [2]. IAT is distributed as an executable file for installation on computers using Microsoft Windows. A simulation case can be set by filling in input data textboxes in the IAT graphical user interface (GUI) and can be run in any computer in a few tens of seconds. It has been validated for internal arc faults in air and SF6.
Due to the simplifications used, there are some limitations regarding the accuracy and predictive power of the IAT calculations. Some accuracy issues can occur for temperatures above 6,000 K in air and 2,000 K in SF6 [2]. Since the calculations are based on lumped volumes, IAT cannot resolve traveling pressure waves in space and uses average values instead. Therefore, it has limitations for the evaluation of pressure waves travelling along elongated objects such as long ducts and exhaust channels. It also cannot resolve the motion of bursting disks and flaps.
DIAS DymoDAT-based internal arc simulations
DIAS is a tool that provides a fast simulation based on an enhanced lumped model for mass and energy conservation. Its core stems from the ABB internal tool DymoDAT for describing the pressure build-up during high-voltage circuit breaker operations [3]. An internally developed, enhanced arc model that includes physical models of the most important effects, such as electrode erosion, is central to the tool. Exothermic reactions between eroded electrode material and filling gas are considered within a real model of the gas or plasma [4]. Consequently, a kp factor is not required as a fitting parameter and a valid description of gas properties over a wide range of temperatures and pressures is obtained. The gas flow between different device compartments is approximated by standard gas dynamics relations and can be corrected by effectively reduced flow areas. The opening dynamics of burst disks and flaps are taken into account by prescribing an opening time after a given overpressure has been reached. →3.
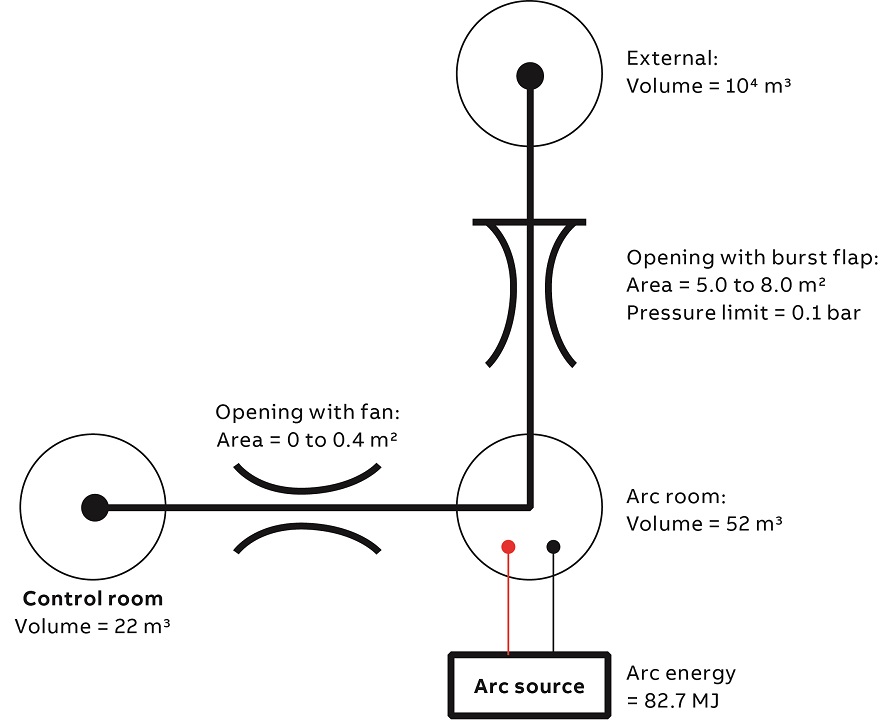
DIAS requires the installation of the commercial simulation platform Dymola, which also provides the GUI for entering model parameters and evaluating the results. Simulation times are around one second on standard computing hardware. The predictions of DIAS have been validated for a large set of internal arc faults in SF6- and air-filled equipment with copper or aluminum electrodes.
PRIAS – pressure rise in internal arc simulation
PRIAS is an accurate and complex CFD simulation tool intended to complement the IAT and DIAS tools by resolving, in three dimensions, all the flow parameters. It allows the accurate evaluation of the flow, considering traveling pressure waves, which cannot be resolved within a lumped description. PRIAS has been developed by ABB as a collection of scripts running on the third-party CFD software ANSYS Fluent under Linux. In contrast to the other tools, PRIAS requires a detailed description of the analyzed geometry and the PCDs in order to generate the CFD-compatible mesh required as input. Up until now, the predictions of PRIAS have been validated for internal arcs in air only.
A simulation with PRIAS must be run on a high-performance computer cluster and usually takes under two days. However, the typical simulation workflow (from the planning of a calculation task to its setup and then its execution) can take from several days to a few weeks. For this reason, PRIAS is mainly aimed at high-end simulations in complex configurations where lumped calculations are not accurate or sufficient or where the behavior of PCDs is not known beforehand. Furthermore, PRIAS is recommended for simulations in structures containing elongated parts (such as ducts or exhaust channels) or in large structures with several PCDs installed along the periphery, where the effect of pressure traveling waves should be accounted for. In those cases, PRIAS can also be used for the more complicated simulation of the fluid-structure interaction necessary to evaluate mechanical damage due to internal arcs. An example of the PRIAS simulation for air-insulated, medium-voltage switchgear, including dynamically moving bursting disks, is illustrated in →4.
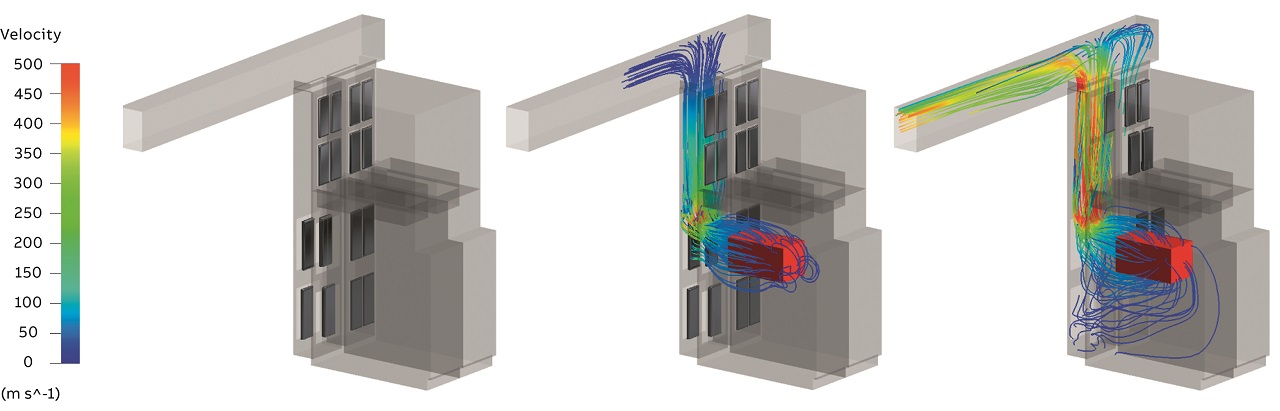
ABB-internal arc simulation platform
In order to have a common platform across ABB for the development, archiving and usage of the arc simulation tools, an internal ABB SharePoint site has been set up. The platform also allows the coordination of development activities between the service providers and the software development teams. The site platform is administrated by arc simulation specialists.
An application example: Alba PL6
In 2016, a detailed investigation of the pressure build-up and structural impact of an arc failure in the Alba PL6 container rectifier was commissioned. The investigation involved finding an improved design, including the specification and positioning of PCDs. The main target was to reach an optimal structural design for an arc-safe rectifier container that allowed effective relief of pressure to the exterior.
The investigation was conducted in steps, initially using DIAS to roughly determine the overall opening areas of bursting flaps, without involving geometrical details and aspects of flow in the rectifier container.
Once the DIAS simulations were complete, the task focused on calculations with PRIAS under the detailed conditions of the flow and the pressure on the arcing and service rooms in the rectifier.
Using these calculations, the number of bursting flaps and their location were found such that the overpressures generated were minimized →5.
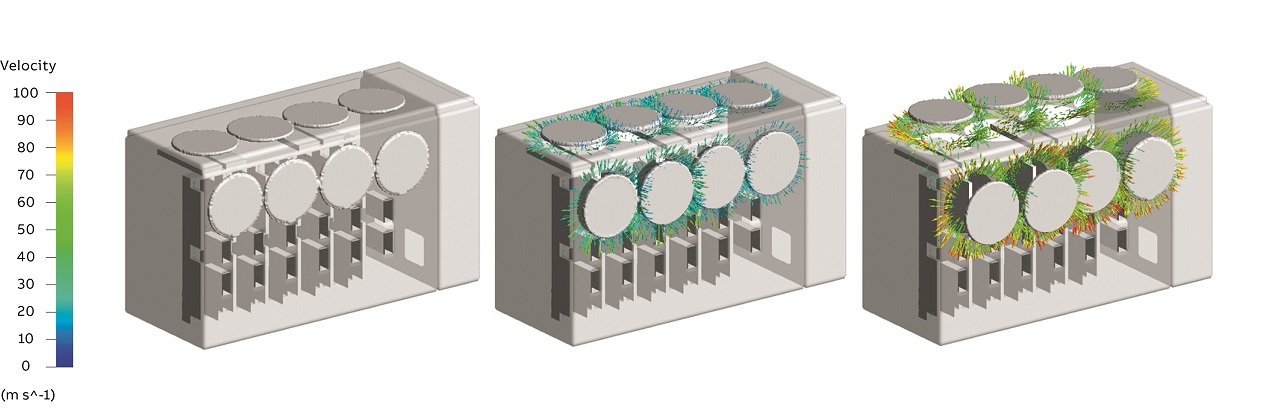
In the next step, the pressure and forces on the walls and surfaces estimated with PRIAS were used to assess the structural integrity of the system using 3D finite element simulations (the ABAQUS finite element analysis software suite was used). The structural response from the arc failure was investigated in terms of wall displacement, plastic strains, stress on welds and force on joints →6.
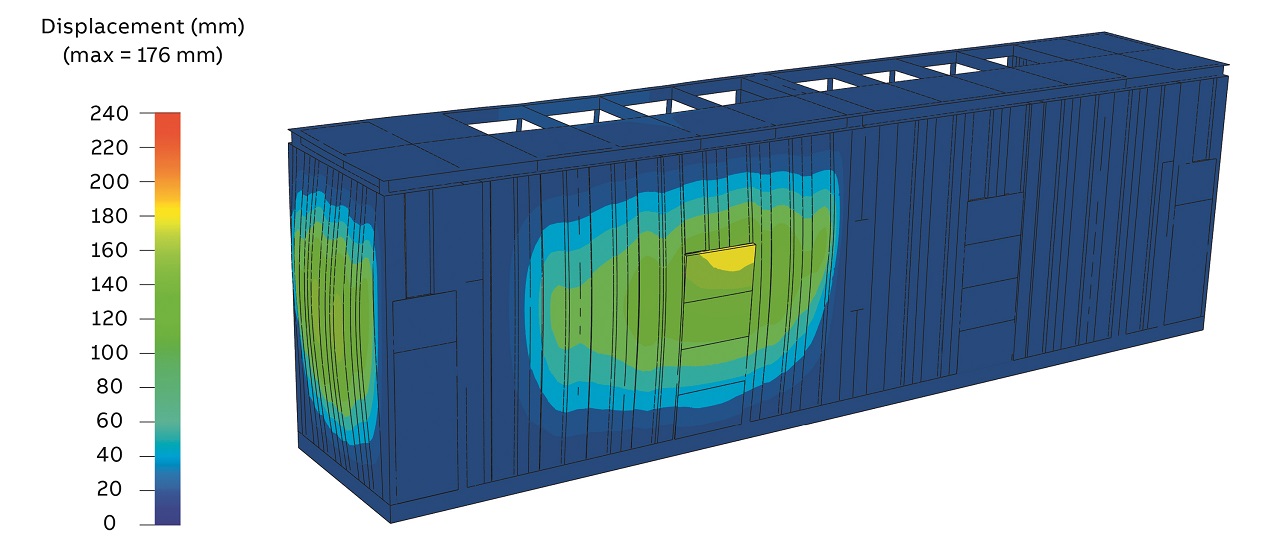
Cost-effective and fast
Although internal arcing is a rare event, its effects can be devastating – and even fatal. The simulation tools discussed here provide an effective means to design internal-arc-prone electrical enclosures in a way that massively reduces the detrimental effects of these events. The tools have, for example, been used for a new efficient design process for rectifier container and pressure relief device dimensioning. Further, field experience has shown that the overpressures calculated are very close to the values measured during an internal arc test on the same object. The platform provides a very cost-effective approach too: in one case, it was possible to simulate the pressure rise inside a pressurized unit at internal arcing for one-twentieth the cost of physical testing.
The platform can radically shorten development timescales. In one example, it supported the decision between a complete redesign or an improvement to the existing design, thus saving hundreds of thousands of dollars. Furthermore, the platform provides a way to demonstrate to a customer the efficacy of a particular cabinet, container or room design in a very short time.
References
[1] CIGRE WG A3.24, “Tools for simulation of the internal arc effects in HV and MV switchgear,” Electra, 2015.
[2] E. Dullni et al., “Feeling the pressure: Simulating pressure rise in switchgear installation rooms,” ABB Review, 3/2013, pp. 54–59.
[3] J. Lehmann et al., “A Modelica library for High-Voltage AC Circuit-Breaker Modeling,” Proceedings of the 7th International Modelica Conference, Como, September 20–22, 2009, pp. 855–860.
[4] C. Doiron and K. Hencken, “Calculation of thermodynamic and transport properties of thermal plasmas based on the Cantera software toolkit,” Proceedings of the XXII Europhysics Conference on Atomic and Molecular Physics of Ionized Gases, Greifswald, July 15–19, 2014.