Innovative 3D printing technology will create a landmark bridge in the heart of historic Amsterdam
The innovative 3D printed bridge, built by ABB robots, will span a canal in Amsterdam’s world famous Red Light District. The fully-functioning stainless steel pedestrian bridge will cross the Oudezijds Achterburgwal, one of the city’s oldest canals.
Dutch 3D printing startup, MX3D, has invented a 3D printing technique whereby ABB industrial robots support a 3D printer which is able to print multiple lines of steel at once, similar to weaving a basket. The ABB IRB 2600 and IRB 6700 robots each move along 6-axis, which means MX3D’s printing head can be precisely controlled across a wide range of positions so the bridge design is not constrained by limits on the printing capabilities.
The ABB IRB 2600 and IRB 6700 robots are currently busy creating the bridge, which will span the six meter canal nearby some of the city’s most iconic sights including the home of the Dutch East India Company and the New Market, setting for Rembrandt van Rijn‘s masterpiece “The Anatomy Lesson of Dr Nicolaes Tulp”. The 3D-printed bridge is scheduled for completion in early 2018.
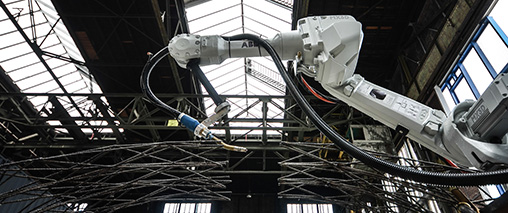
MX3D’s software translates a design to a laser pattern, which is translated to ABB’s rapid software which tells the robots how to move. ABB has worked closely with MX3D to train their employees on how to use the robots.
The production process is simple: A welding head is attached to the end of the ABB robotic arm and small amounts of welding material are added in the production process, resulting in self-supporting metal rods and structures that are essentially made of a multitude of welded points. The robots are printing large parts of roughly one meter steel plates at a separate location. The parts will be assembled after printing.
This bridge will show how 3D printing is a practical tool to create large-scale, functional objects with unique forms and materials. The use of additive 3D printing can also reduce waste by using the exact amount of materials needed – traditional bridges are typically made of carbon-intensive concrete which is poured into molds, often with great waste.
“The MX3D project is a great illustration of how industrial robots are coming out of the factories and playing a major role in public spaces, from material fabrication and construction to public works and lighting. It’s a very exciting and innovative time,” said Martin van der Have, Sales and Marketing Manager for ABB Robotics BeNeLux. “Applying robotic welding technology on this scale and realizing the 3D construction of large objects without any support structure is an important step in the development of new manufacturing technologies. The MX3D project is a unique and ambitious initiative, as well as a good platform to showcase the outstanding motion control and programming capabilities of ABB robots.”
The project also reflects the increasing use of robotics to automate the creation of unique goods. In the consumer world this translates to everything from ‘personalized’ automobile configurations and tailored consumer electronics to specialized food packaging that targets small, local customer segments. This is a large shift from the traditional automation role of robots, performing one repeated task for a long time.
ABB is celebrating its 125-year anniversary in the Netherlands this year. Already having an illustrious history of projects in the country, for example the Delta Works and the port of Rotterdam — Europe’s largest port — the Oudezijds Achterburgwal canal bridge is a link to the future.