Usually, only the most critical rotating machines in a plant are continuously monitored for maintenance purposes. In a pilot plant, ABB has now equipped less-critical equipment with a solution based on inexpensive sensors, machine learning and software that allows cost-effective but advanced monitoring.
Ralf Gitzel, Benedikt Schmidt, Arzam Kotriwala, Ido Amihai, Guruprasad Sosale ABB Corporate Research Ladenburg, Germany, ralf.gitzel@de.abb.com, benedikt.schmidt@de.abb.com, arzam.kotriwala@de.abb.com, ido.amihai@de.abb.com, guruprasad.sosale@de.abb.com; James Ottewill ABB Corporate Research Krakow, Poland, james.ottewill@pl.abb.com; Marco Heese ABB Automation GmbH Mannheim, Germany, marco.heese@de.abb.com; Diego Pareschi ABB B.V. Rijswijk, Netherlands, diego.pareschi@nl.abb.com; Subanatarajan Subbiah Former ABB employee
In a typical industrial plant, condition monitoring and predictive maintenance are usually only applied to the most critical rotating equipment. For cost reasons, less-critical items are often only analyzed on a best-effort basis.
To investigate how to monitor, diagnose and predict failures on less-critical – but widely utilized – rotating equipment, such as motors or pumps, ABB conducted a 30-month study in which a pilot installation at a customer site was equipped with cost-effective sensor technologies, machine learning and a software solution driven by key condition indicators (KCIs) →1. Vibration data was taken multiple times a day from 30 pumps. A network of IoT (Internet of Things) devices collected relevant data from which analytics extract insights.
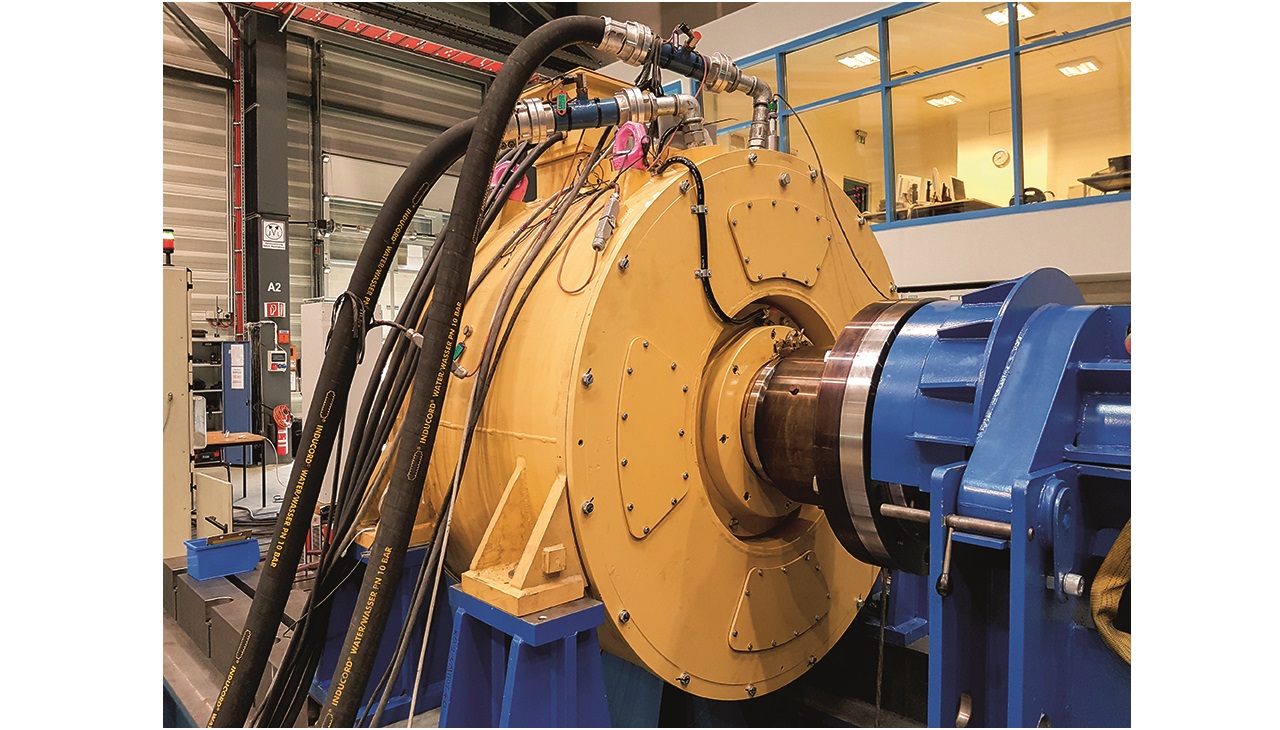
Background and motivation
Condition monitoring of industrial assets, such as motors or pumps, can ensure that critical issues are detected early, thus avoiding unplanned downtime or damage. Early intervention, which reduces the need for corrective maintenance, is more cost-effective than simply allowing a component to run to failure. However, the high costs associated with condition monitoring systems mean that their deployment is currently limited predominantly to critical assets.
A process industry plant – for example, a chemical or pharmaceutical factory – typically contains a large fleet of non-critical motors that drive pumps. While the cost of failure here is considerably lower than that for critical equipment, these assets would benefit from a cost-effective early failure detection system. Not only would early failure detection help avoid further damage, but a pre-diagnosis of problems could also reduce the time needed to repair the asset.
Overall solution architecture
The condition monitoring architecture for the non-critical rotating equipment in the pilot study has three levels →2:
• Field level, with sensors attached to assets to collect data.
• Plant level, which covers plant-wide sensor data aggregation and preprocessing.
• Data integration platform level (eg, cloud or other platform), for fleet data analytics such as benchmarking, predictive maintenance) and reporting.
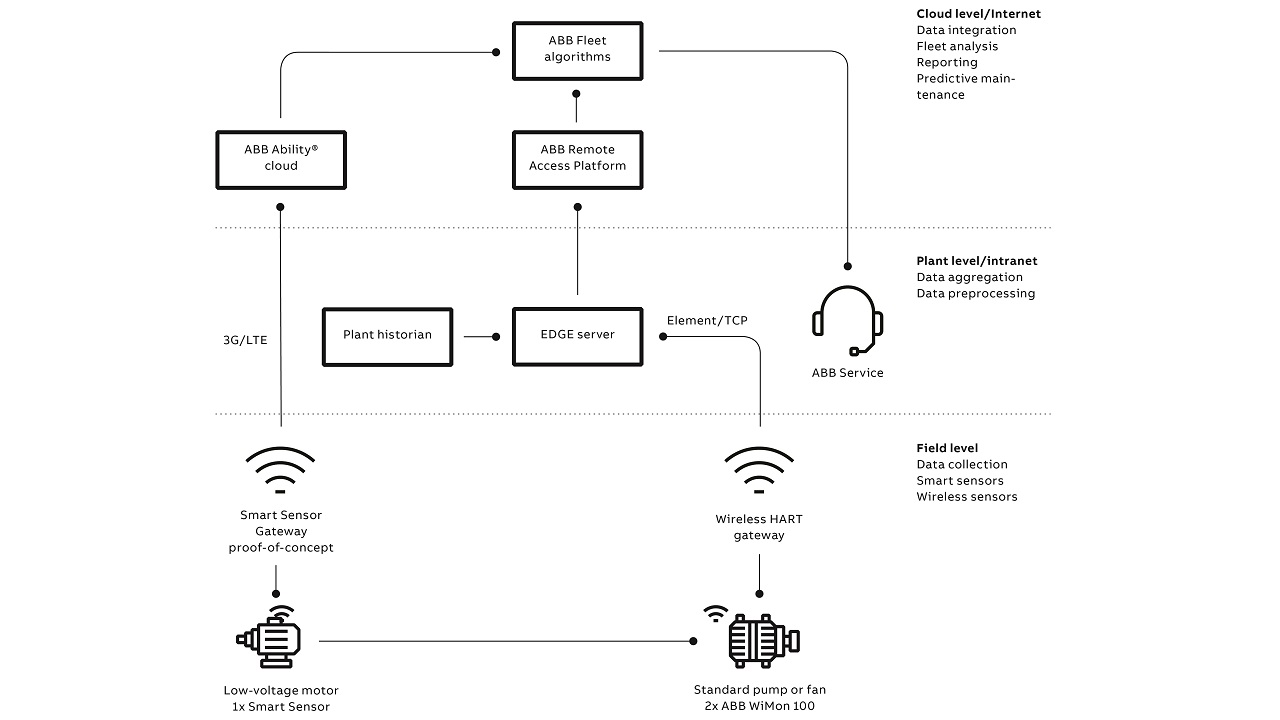
Architecture level 1: field
The field level specifies the sensor-based data collection process up to the transmission of the collected data. The assets considered are the standard pieces of rotating equipment in a commercial process plant – for example, low-voltage motors and pumps. Each item covered by the study was fitted with a commercial wireless condition monitoring system, ABB WiMon 100, which was used to capture vibration data. The WiMon system consists of a vibration sensor (accelerometer) to capture the vibrations and a temperature sensor to capture the surface temperature of the rotating equipment. WiMon systems use a mesh network technology which simplifies the data transfer in the plant. Additionally, low-voltage motors were fitted with an ABB Ability™ Smart Sensor, which converts traditional motors into smart, wirelessly connected devices.
The data collection scheme in the WiMon system can be configured according to the requirements of the user. Typically, every hour, an aggregated value of the root-mean square of the velocity in mm/s and the actual surface temperature in °C is stored as time-series data. To perform detailed vibration analysis, every six hours the raw signal from the accelerometer is captured for a sample time of 700 ms and an FFT (fast Fourier transform) of the captured raw signal is computed. The resulting frequency spectrum allows components of the vibration signal at selected frequencies to be extracted and analyzed further.
Architecture level 2: plant
The mesh network established by the WiMon systems is connected to a wireless HART gateway. Through the gateway, the sensor data collection is connected to the plant network, making it available for different analyses on a plant-wide level. In the realized architecture, the collected asset signal data is stored in the plant historian and processed in the ABB edge server installed at the plant.
Architecture level 3: data integration platform
ABB’s Remote Access Platform allows for the transfer of the asset signal data to the data integration platform. In addition to its remarkable computation capabilities, a major benefit of this platform is the possibility to collect data from
many plants.
With many plants connected, fleet data analytics can be performed on the platform to compare and benchmark different locations and regions. A condition monitoring algorithm is used to process all collected data and allow remote access to the analytics results from different locations.
Diagnostics: analytics behind key condition indices
The usefulness of a condition monitoring system depends on its ability to provide concise, meaningful and actionable information to its user. Vibration data can be used to calculate a series of metrics that are useful for a maintenance manager to identify actions required to avoid further asset deterioration. For example, an imbalance in the rotating equipment manifests itself as an increased vibration at the rotating frequency. In the scenario discussed here, frequency spectrum data are fed to proprietary algorithms developed at ABB to calculate KCIs for failure modes (eg, bearing fault or cavitation) a piece of rotating equipment might experience →3.
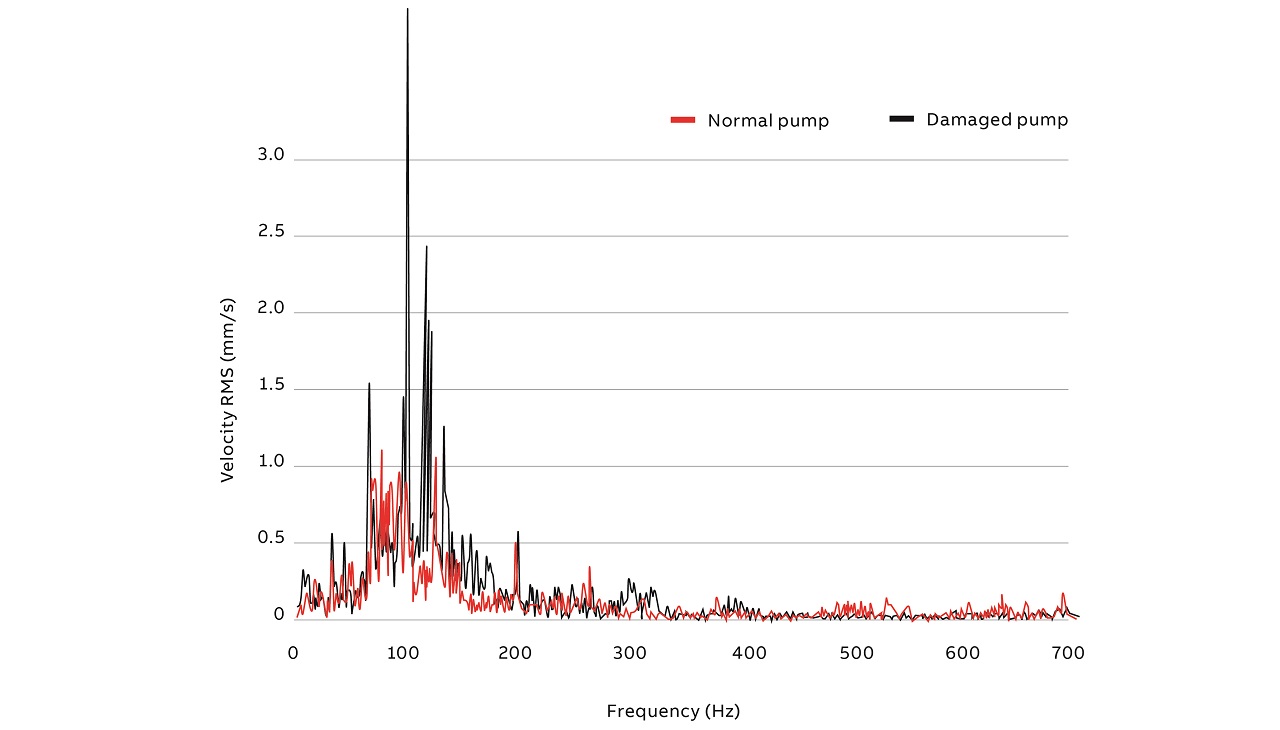
A KCI is a numerical value that indicates the severity level of the corresponding failure mode observed in the equipment. The following example KCIs monitor problems that can be detected using vibration data:
• Blade problems: When monitoring pumps, certain peaks in the frequency spectrum indicate damage to the blades in the pump. The blade problem KCI reflects how pronounced these critical peaks are.
• Flow turbulences: This KCI indicates irregularities in the flow of liquid passing a pump Turbulences can be problems in themselves or indicators thereof.
• Looseness: The central shaft in rotating equipment is often constrained by the bearings so that its rotational axis does not fluctuate. Excessive clearance, typically caused by wear in the bearing, will mean that the shaft will exhibit vertical and horizontal movement, which can quickly lead to further damage. The Looseness KCI indicates whether and to what degree the equipment suffers from this problem.
• Misalignment: All components of rotating equipment must be well aligned. However, damage during transportation or irregularities during operation can cause deviations from the ideal alignment position. Like Looseness, misalignment can cause further damage to the asset as well as reduce its performance.
• Imbalance: Ideally, the rotating elements in a piece of equipment are balanced. This means that the mass is distributed equally in all directions. An example of imbalance would be a piece of matter sticking to one of the blades in a pump, which will exert additional force on the bearings.
• Cavitation: Cavitation is a well-known pump-related problem. Small low-pressure bubbles can occur when force is exerted on a liquid in such a way that there are rapid pressure changes. Due to the higher pressure around them, these bubbles can implode and cause damage to the pump. The Cavitation KCI detects the occurrence of cavitation-related implosions.
Predictive maintenance: using machine learning to predict asset health
A neural-network-based, machine-learning model was trained to predict the future health status of the assets. The prediction, or prognosis, is based on KCIs and other asset information and their changes over time. For example, based on the past KCI values Ct-n, ... , Ct-1, the neural network predicts future values Ct+1 and Ct+n, where n indicates the prediction or “look-ahead” window. If the predicted value of an asset crosses a threshold, a message is provided to the asset manager stating that it ought to be inspected →4.
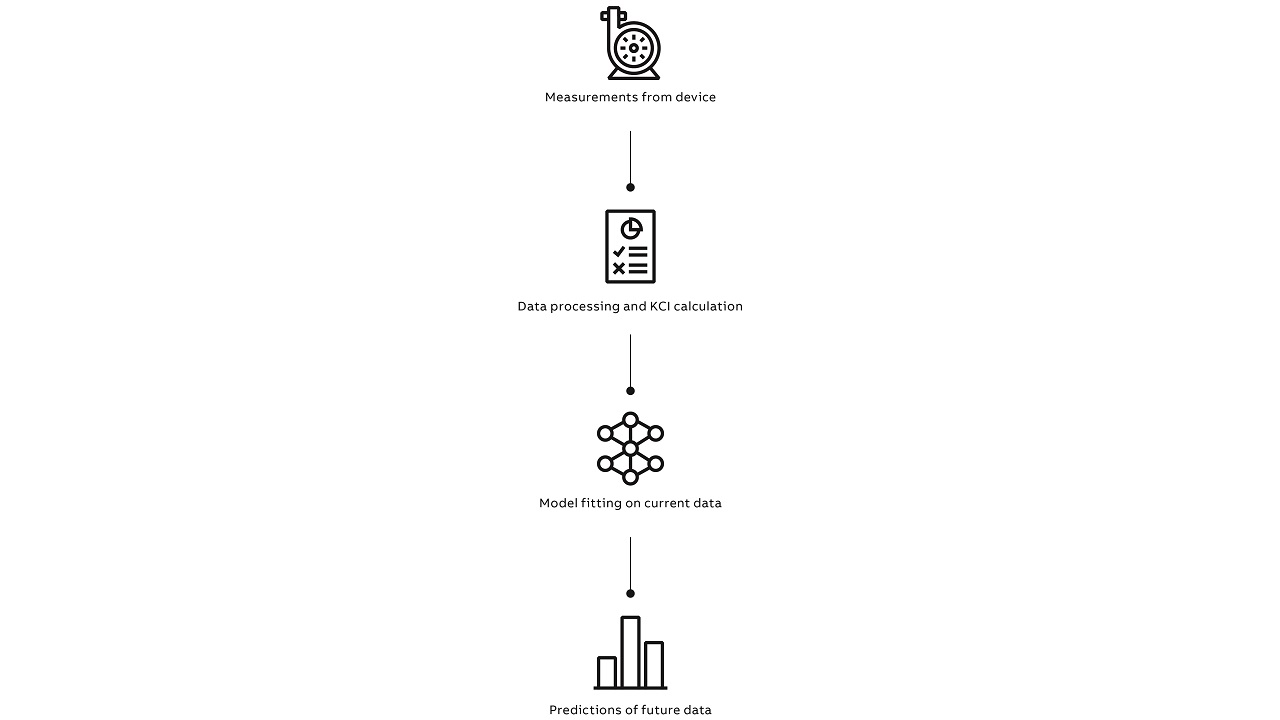
The threshold used to determine poor asset health can be determined using either industry standards or in a data-driven manner, where a large sample of KCI values would be provided to a different machine-learning model that can categorize the data into separate classes based on these values. Regardless of the threshold, ABB’s machine-learning approach proved highly effective at predicting deterioration in asset health, which was detected approximately 90 percent of the time on these asset types (the exact values depended on the KCI used, as well as additional factors like the size of the look-ahead window).
Application scenarios
With the architecture described earlier and with the analytics developed for diagnostics and prognostics as the basis, a prototype solution to serve the asset managers and personnel responsible for maintenance was built →5,6.
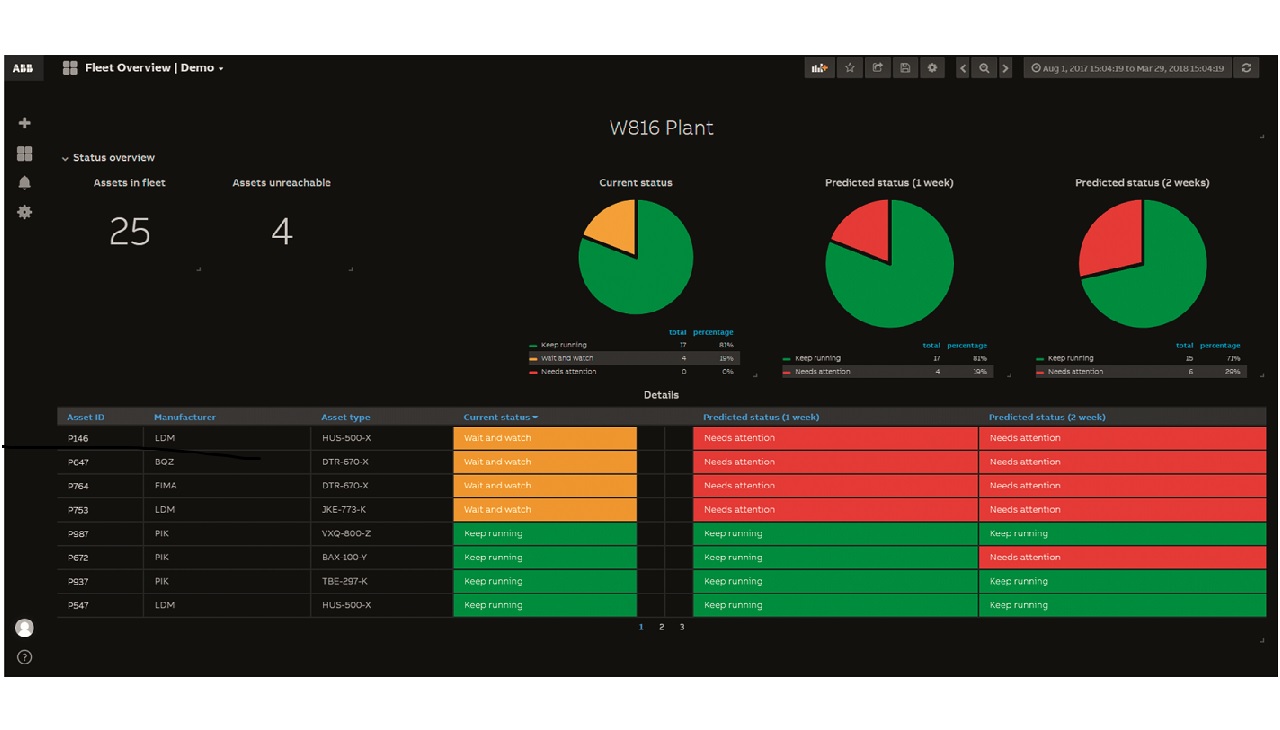
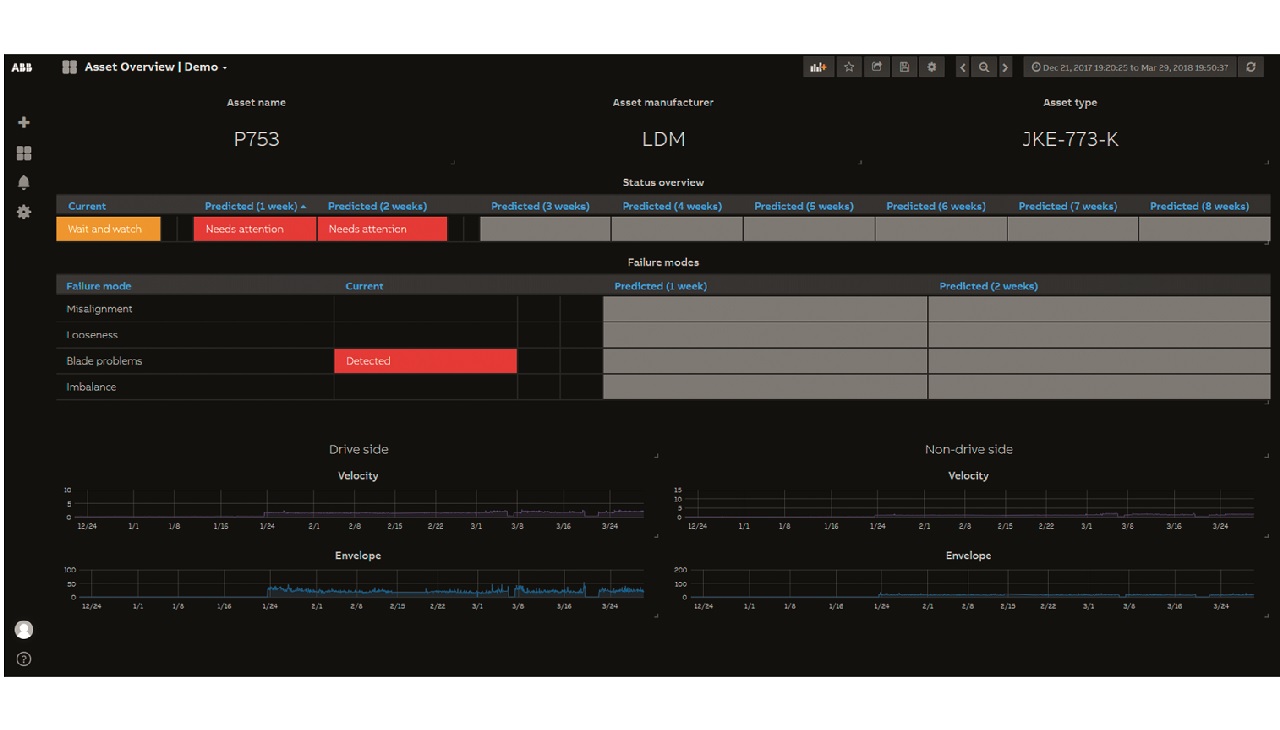
The diagnostic results are presented to the end-user as the current status of the asset, which can be either “Keep running,” “Wait and watch” or “Needs attention.” The predicted status can be either “Keep running” or “Needs attention.” Below, the potential scenarios that can occur and how the technology developed helps the end-user to benefit from it is explained →7.
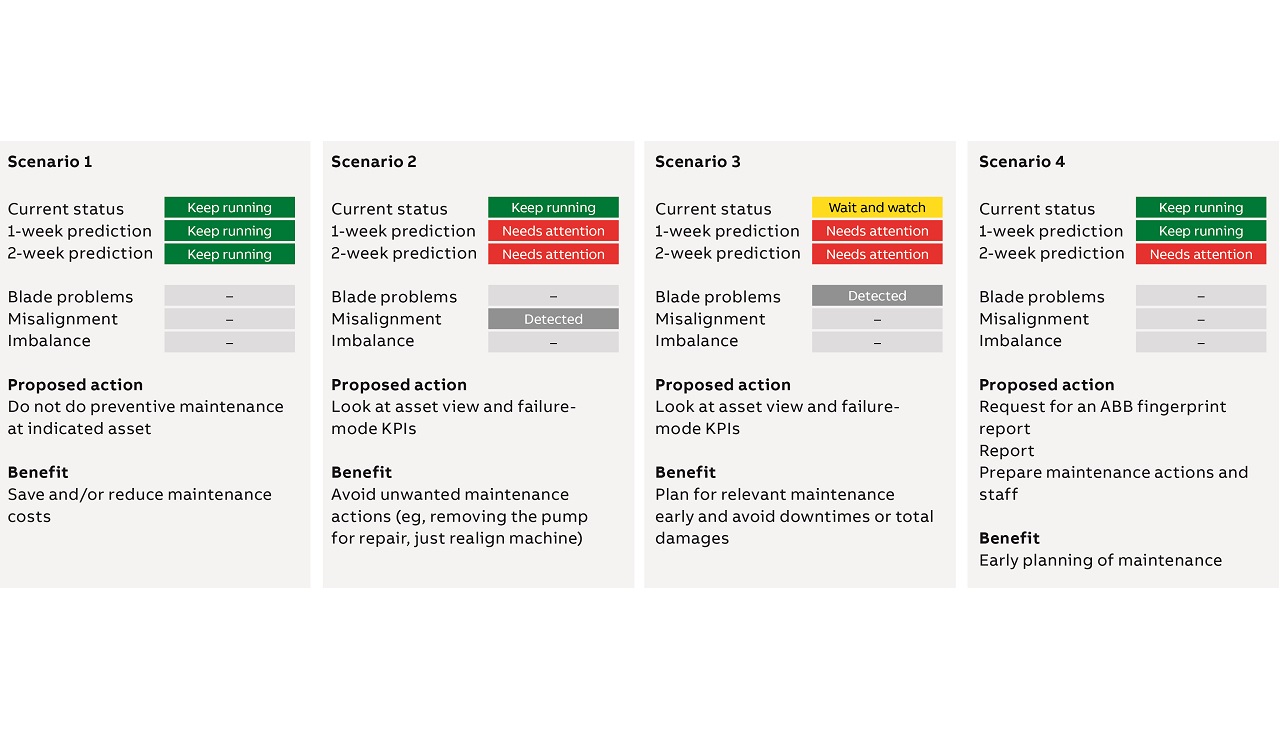
Scenario 1
Starting with the trivial scenario in which the asset is operating normally with no damage predicted, the current and predicted statuses are “Keep running.” No unnecessary time-based maintenance need be undertaken.
Scenario 2
In this scenario, consider the case where the asset is currently exhibiting evidence of damage but not imminent failure. Thus, the current-status field advises the user to keep operating the asset and the predicted-status fields for the weeks ahead would show “Needs attention” and recommend an action. The action proposed to the user is to explore the asset sensor data in a detailed fashion and to take appropriate action. The diagnostic algorithms indicate any damage – for example, a misalignment detected in the detailed view would lead to a recommendation to perform an alignment process rather than unmount the asset, which focusses effort on required maintenance only.
Scenario 3
Here, the case is considered where the asset is currently exhibiting evidence of significant damage, not severe enough that it needs to be stopped, but enough that its condition should be monitored closely. The predicted-status fields for the upcoming two weeks would show “Needs attention” as a recommendation. The action proposed to the user is to explore the asset sensor data in a detailed fashion and take appropriate action based on different failure modes. The diagnostic algorithms indicate any initiated damage. For example, blade problems being detected in the detailed view would result in a recommendation to perform a maintenance process that might require unmounting the asset. This would help the asset manager to plan spare parts and coordinate maintenance effort to minimize downtime.
Scenario 4
In this scenario, the asset is currently exhibiting symptoms of considerable damage and could reach a significant damage level in two weeks or later. However, since there is no devastating damage in the current status, it advises the user to “Keep running” and the prediction based on past historical data and current data would suggest the status field for the two-week prediction as “Needs attention.” The proposed action is to perform a more detailed analysis of the sensor data as a fingerprint report. This would help the asset manager to take an informed decision on planning any maintenance required, if any.
Insights and foresight
Several important insights emerged from the development of this prototype predictive maintenance solution:
• Data preparation is an important, often under-considered, aspect.
• Where new data is periodically collected from the field, special consideration has to be given to data consistency to account for cases, for instance, where a sensor has been moved or replaced.
• There are unique challenges associated with managing and manipulating live data.
By addressing these challenges, and by combining domain knowledge with machine-learning approaches, ABB was able to deliver a reliable and robust condition monitoring solution for non-critical rotating equipment. Results achieved when applying the approach to a real customer case showed that the KCIs could be predicted accurately up to two weeks ahead.