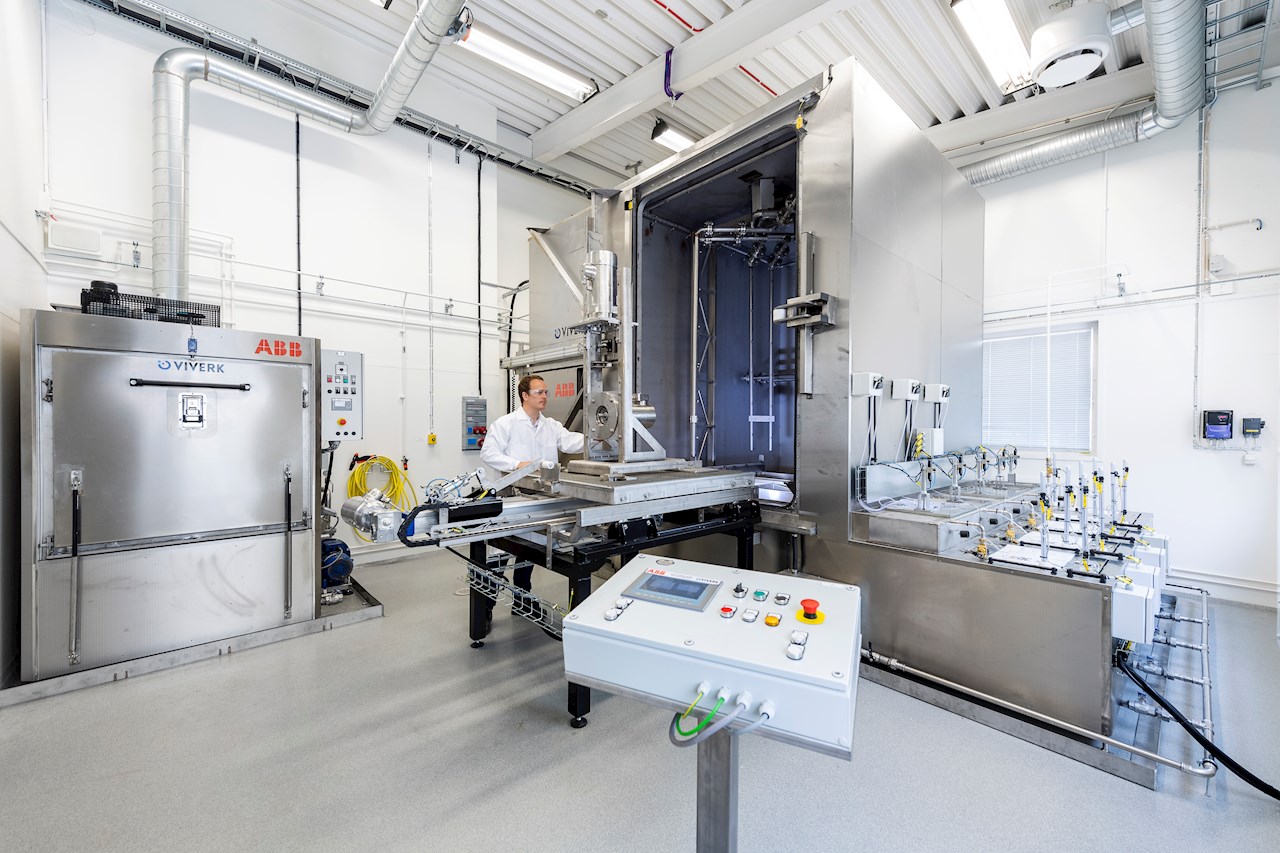
A new state-of-the-art lab has just opened at the ABB Corporate Research Centre in Västerås, Sweden with the ability to study, test and verify washdown procedures in a fraction of the time it would take under normal manufacturing conditions.
For food and beverage manufacturers, hygiene is a top priority to ensure that food and drink is safe to consume. Just one violation could be devasting. However, keeping equipment sanitized across every aspect of production, with complete visibility of food production process and rising food safety standards, is a challenge.
But daily washdown is tough on plant equipment, which can show early signs of corrosion after just two or three months of use, leading to equipment failure and downtime. To address this, the new Västerås lab can precisely replicate the washdown conditions used in a working F&B facility and test products like never before. In fact, it can perform tests corresponding to around one year of daily washdown in just one week.
“This means that we can quickly validate new products and continue to improve performance and increase product lifetime,” says Karin Gustafsson, Manager at Technology Consulting ABB’s Corporate Research Center.
The new lab will also be available to ABB partners and customers to perform testing. This forms part of ABB’s consultative service focused on enhancing reliability at every step of the manufacturing process, from power to palletizing. Good news for an industry faced with an ever-increasing list of demands from health to hygiene, safety to sustainability.
“With ABB’s recent product launches, including the Food Safe family of stainless steel motors, bearings and gearing, we are well positioned to help food and beverage customers improve hygienic design, plant reliability and reduce costs,” says Tomas Lagerberg, Global Technology Manager for the food and beverage industry, ABB. “This lab will help us continue to deliver products with exceptional hygienic properties.”
Rigorous testing will ultimately result in vastly reduced downtime and optimized performance. This in turn means lower consumption of energy, water and chemicals, enabling customers to achieve sustainability targets and improve plant efficiency.