Guido Jouret ABB’s Chief digital officer, Guido Jouret explains what the new ABB Ability platform is all about.
Guido Jouret discussed ABB’s digital strategy in a previous interview (published in ABB Review 1/2017). In this second interview he talks about ABB Ability.
AR ABB Review (AR): In March of this year, the ABB Ability platform was launched at the ABB Customer World in Houston. What exactly is ABB Ability?
GJ Guido Jouret (GJ): ABB Ability is a set of industrial solutions that use digital technology. It is also the name of the platform to build such solution. ABB will digitalize its complete range of products and services and use a cloud-based platform built on technology from Microsoft Azure to offer a broad range of analytics and services.
AR In what way does ABB Ability go further than previous ABB automation and digitalization offerings?
GJ The Internet of Things is often described in terms of individual devices having embedded sensoring and processing power, meaning they create data streams. Long before we launched ABB Ability, ABB was already speaking about the potential for leveraging productivity by not leaving data marooned in the field. Continuous progress in digitalization and communication meant this data could be shared to a higher hierarchical level where it was aggregated and analyzed to be made available to managers, for example in the form of reports. What was often still missing was ABB Ability’s means to take decisions based on that data in a direct manner. This is what in ABB we call “closing he loop”→1.
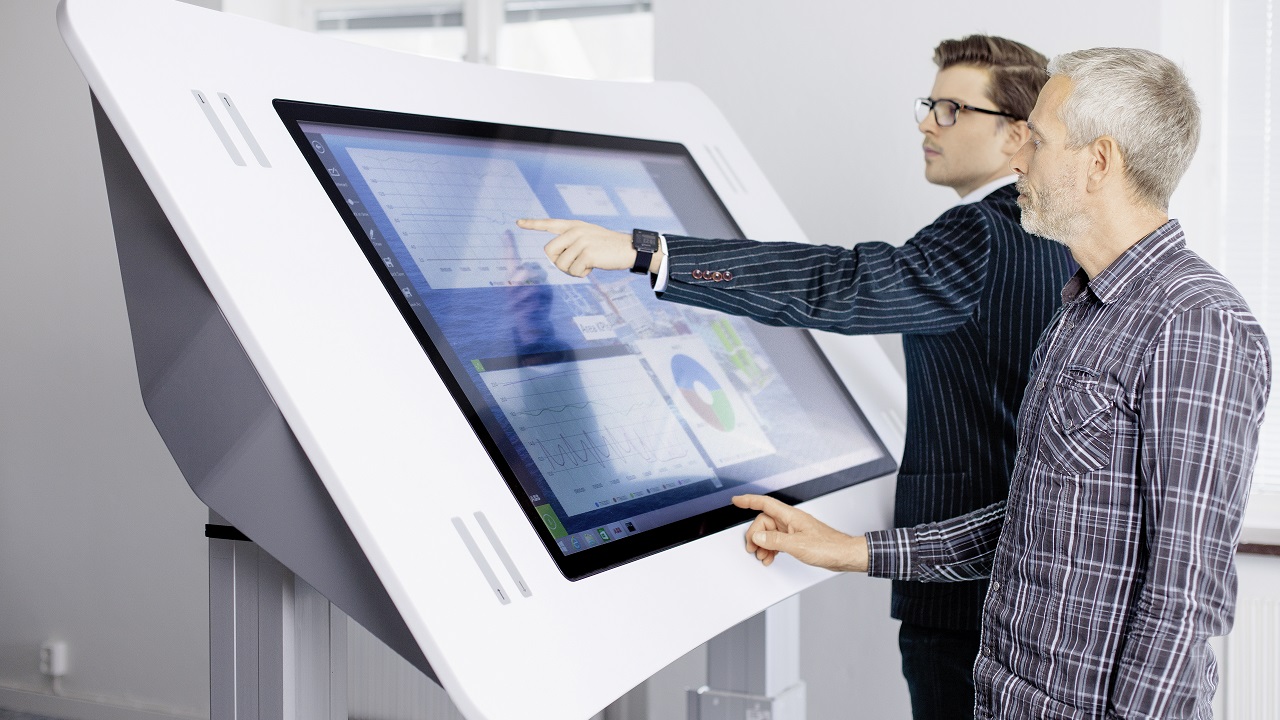
Control engineers know about control loops: Process data is fed back to influence actions
with minimal latency. Sensor and actuator are in close proximity so that any adverse shift in output parameters can immediately be mitigated. This principle is at the heart of control theory. The loop we are closing with ABB Ability is conceptually similar, but concerns more over-arching decisions relating to operations and maintenance. It looks at higher-level patterns and correlations and has latency requirements that are more generous→2.
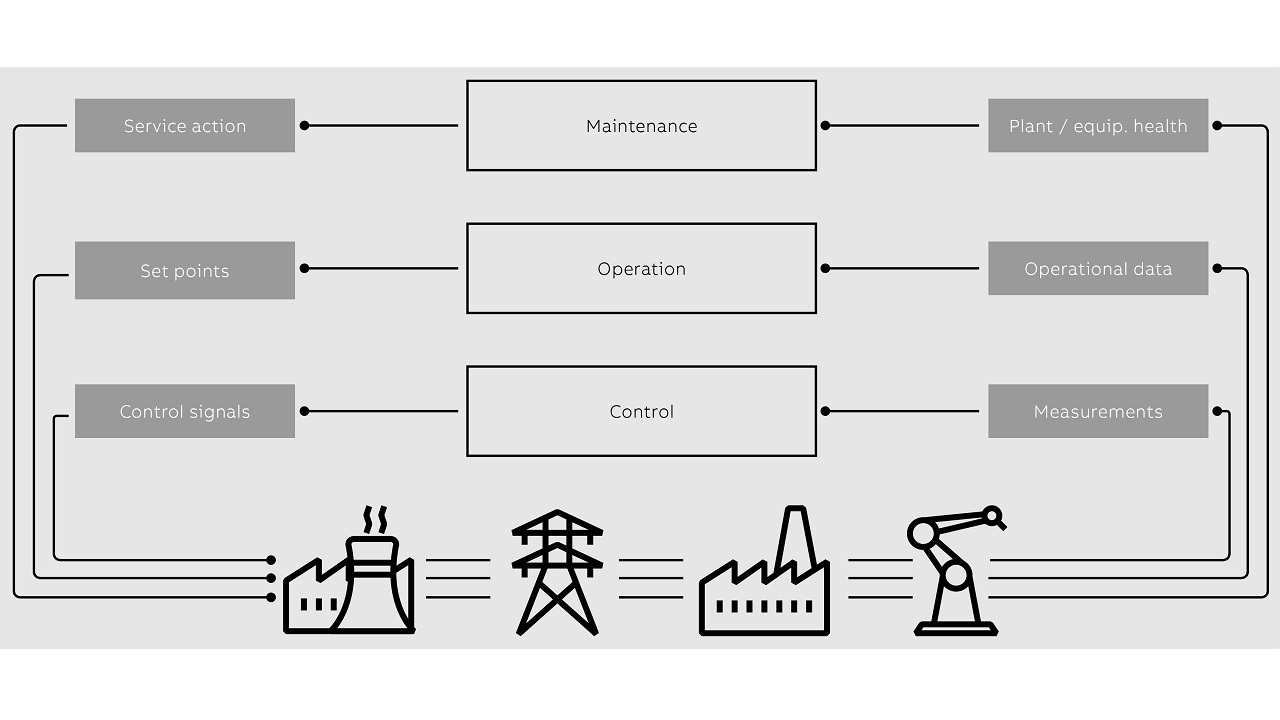
AR What sort of parameters would such higher-level control loops deal with?
GJ The type of control decisions being supported here can range from optimizing maintenance cycles to supporting higher-level management decisions that take into account the bigger picture. This means opening the focus beyond the immediate process and looking at the broader situation within the plant and beyond. Management decisions can thus be based on actual real-time information rather than on data that has been collected beforehand – sometimes manually, and often limited in scope or potentially even containing transcription errors. By bridging this gap, the boardroom is increasingly meeting the control room→3.
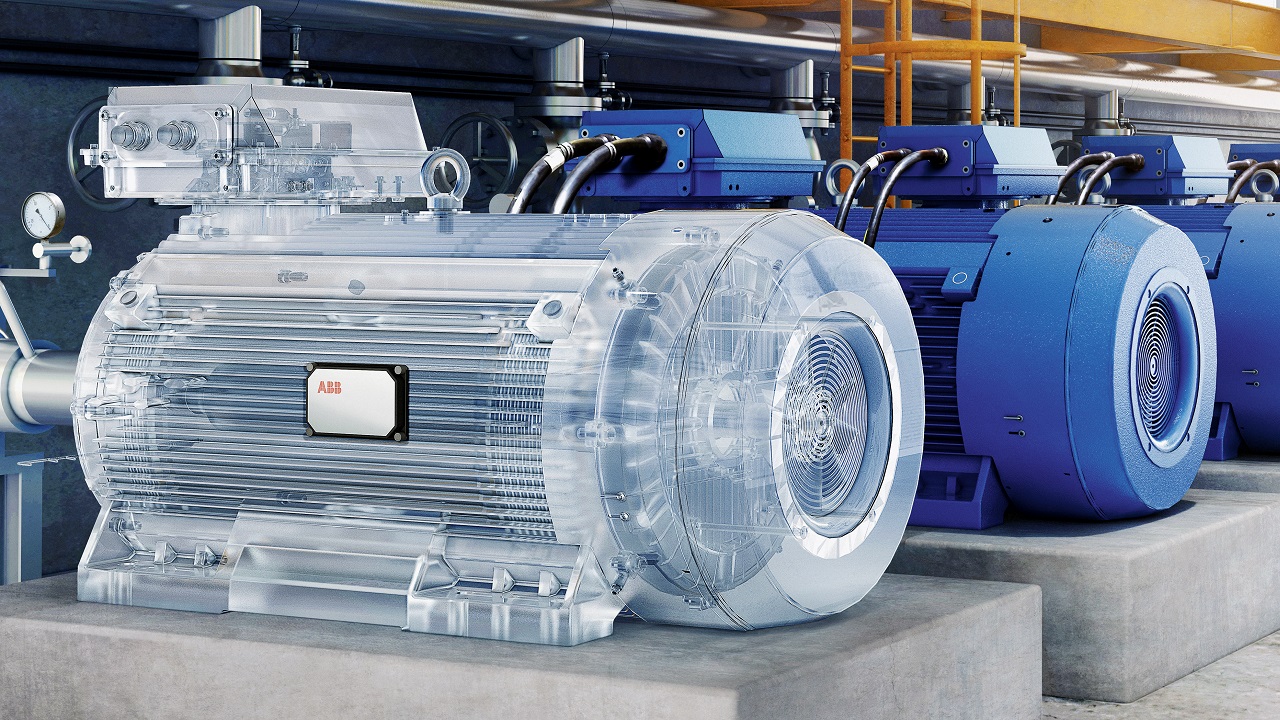
This opening is occurring in both directions as not only do managers see current data, but decisions can flow back and be implemented immediately. This is the integration of IT (information technology) and OT (operational technology).
One example is the charging of an electric car. Obviously, the car and the charger need to talk to one another, for example for purposes of billing the electricity, but also to ensure the battery is charged with the appropriate voltage and current and that the device disconnects when the battery is fully charged. This is the basic functionality of such a system. But moving beyond that, it also makes sense for the charger to talk to the grid. For example, the charging rate can be temporarily reduced if insufficient power is available and there are other consumers with higher priority.
Another example could be in discrete manufacturing: Managers might see that the delivery of a vital component has been disrupted upstream. Rather than running a downstream process at full force until a component unexpectedly runs out, this process be scheduled differently to mitigate the disturbance. The delay can be bridged by shifting production to a different product for example. Similarly, if a disturbance further downstream is detected, there may be more meaningful ways to use a given resource than manufacturing parts that cannot be consumed.
AR In the past, manufacturers sought to lock in customers and lock out competitors by creating proprietary standards. More recently, interoperability has become the prevalent policy. ABB supports standards such as IEC 61850 (for substation communication) assuring interoperability of devices from different manufacturers. The age of proprietary solutions on a system level is largely history. But what about the cloud level? Will we see history repeat itself with manufacturers attempting to lock out competition?
GJ On the contrary. Rather than chasing a bigger share of today’s automation pie, we need to look at the vast potential there is for growing the pie.
Just as devices within the same system exchange information, clouds will exchange information regardless of manufacturer or architecture. We can thus talk of the “intercloud” in which entire clouds exchange information and collaborate→4.
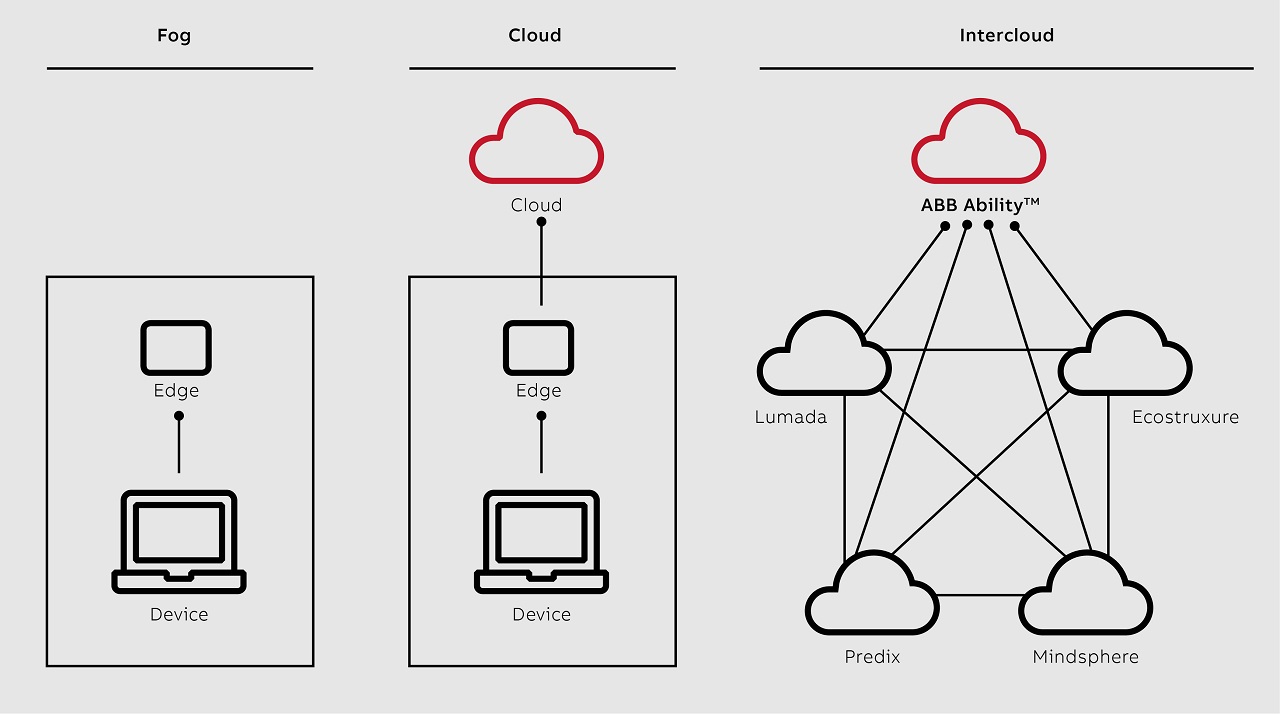
AR The examples discussed previously pertain to data being shared within a customer organization. What about data being shared with ABB?
GJ ABB can analyze data and predict failure modes, advising customers about maintenance, or depending on the arrangement in place, taking action. In a way, it could be interpreted that ABB is hurting its own business by doing this. If better maintenance is extending the life of, for example, a motor, we may be missing out on the opportunity to replace it. But we need to see the bigger picture here. ABB’s offering and market presence will shift away from selling equipment and towards selling services.
Besides maintenance, the customer is also benefitting by giving ABB a better understanding of its operations. For example if ABB understands how the customer is using a robot by looking at typical load cycles, ABB will be able to design the next generation of robots to better meet those needs.
AR So the more data a customer chooses to share, the more the customer also stands to benefit. But won’t the increased reliance on the cloud also make customers vulnerable?
GJ That is a very important question. We can already observe that more and more robots have cameras, for example Yumi. As a next step we will probably also see microphones becoming widespread, both to respond to human commands but also to increase the overall sensory awareness of robots. Access to these devices can pretty much provide eyes and ears into otherwise restricted areas of a factory. A customer might see trade secrets at risk, and also proprietary information such as production data. Let us take for example a manufacturer of high-end sports cars. A robot on that production line can provide an accurate measure of the number of any given model that has being produced. If such data should, whether through malice or by accident, fall into the hands of a competitor, they might gain an unfair market advantage.
AR So there is a conflict here between the advantages a customer can gain from sharing data, and the risks the customer is exposed to from sharing that data.
GJ What we need here is a sort of Bill of Rights. Just as the original Bill of Rights is about restricing a government’s ability to take adverse actions against its citizens, the IoT Data Bill of Rights will codify fundamental rights concerning data.
ABB has already produced a first draft of such a document and is presently seeking input from customers on it. It is important to us that this document will not be drafted by lawyers but will remain in a form that is easy to understand by all. The bill will form a fundamental understanding between ABB and its customers, and will be at the heart of all dealings between ABB and its customers.
Important elements of this bill include:
• What data does ABB gather from its customers.
• Why does ABB need it.
• How does ABB secure it (via technology and policy).
• How do customers benefit from these practices.
• What ABB will do with somebody’s data if they choose to stop being a customer.
In format and concept, the IoT Data Bill of Rights could draw inspiration from such things as the US government’s highly effective Airline Passengers’ Bill of Rights, which protects airline passengers from long waits on the tarmac, hidden fees, being kept in the dark about reasons for delays, no access to water or lavatories, and bag-check fees for luggage that ends up lost, among other guarantees.
We look forward to discussing this with customers.
AR Thank you for this interview.