ABB motors save Michelin energy and emissions
Michelin's motor efficiency and cost reduction program is achieving some remarkable results at its auto and tractor tire factory at Valladolid in northern Spain, one of 72 production facilities that the company operates worldwide.
ABB recently conducted one of its acclaimed energy efficiency audits at the factory, in which an ABB audit team measured the performance of the motors and other key parts of the process to identify the biggest potential for energy savings and reduced emissions.
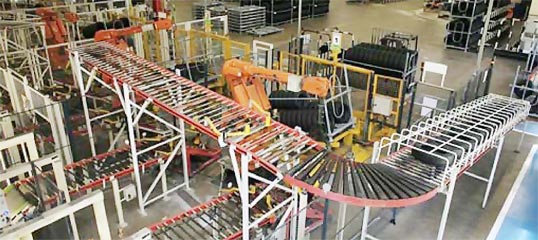
An ABB energy audit at a Michelin tire factory found 436 low voltage motors had a low efficiency rate and were consuming unnecessarily large amounts of electrical energy.
The audit at Valladolid showed that the 436 low voltage motors in the factory had a low efficiency rate of 76.9 percent and, as a result, were consuming unnecessarily large amounts of electrical energy.
ABB is the world's leading manufacturer of motors and generators and variable speed drives. The audit further revealed that by replacing these low efficiency motors - many of which were more than 20 years old - with ABB IE2 high efficiency motors, a significant increase in output to 84.2 percent would be achieved.
Each of the motors operates for 5,880 hours a year at 90 percent load and 100 percent of the time. The annual power consumption of each low efficiency motor was 10,322 kilowatt-hours (kWh), compared to 9,428 kWh for an ABB high efficiency motor.
The resultant energy saving is 895 kWh per motor. This adds up to 390,220 kWh for the entire installed base of 436 motors that ABB is currently replacing. With savings of this magnitude, the payback time for each motor is calculated by ABB at just 1.4 years.
The benefits do not stop there. Lower energy consumption translates into an estimated reduction in carbon dioxide emissions for the factory of 213 metric tons of CO2 equivalent a year.
ABB offers a comprehensive range of energy-efficient motors that comply with the new international efficiency IE2, IE3 and IE4 standards for low voltage motors. ABB has long advocated the need for efficiency in motors, and high efficiency products have formed the core of its portfolio for many years.
The world's first zero-emissions 'natural cooling' data center
Strategically located in Iceland midway between Europe and North America, the Thor Data Center is a hosting and cloud storage services center situated close to the island's capital, Reykjavik.
The facility recently opened its first 40-foot data storage container and has a second under delivery. Both containers use an innovative and patented new cooling technology developed by Spain-based AST Modular, which enables Thor DC to operate with a power usage effectiveness (PUE) ratio of only 1.07 - probably the lowest on record.
Known as modular natural free cooling, the patented technology uses the naturally cool outside air of the Icelandic climate to maintain the correct operating temperature and humidity level inside the sensitive data storage containers.
This, and the fact that the electricity supplied to the center comes from renewable geothermal or hydropower sources means that Thor DC offers its customers a green data storage environment with zero carbon footprint, while benefiting itself from the ultra-energy efficient 'natural and free' cooling technology of the AST Modular concept.
Monitoring and controlling the critical parameters in each data storage container are two ABB AC500 programmable logic controllers (PLCs).
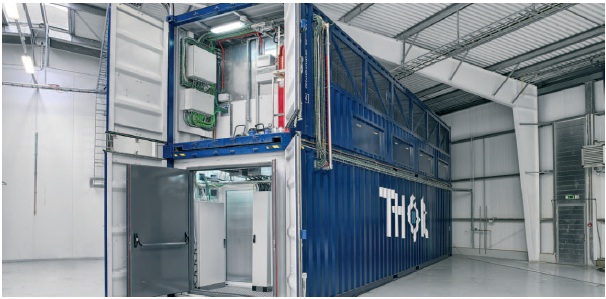
The first AST Modular data storage container at the Thor Data Center, Iceland. Controlled by ABB AC500 PLCs, the data center is cooled by free outside air instead of by conventional energy-hungry chillers.
ABB has been providing AST Modular with programmable logic controllers for several years, and has provided PLC solutions for other AST natural free cooling data centers in Australia and Denmark, which have PUE ratios of 1.09 and 1.13 respectively.
The ABB solution consists of one active and one redundant AC500 PLC. The active PLC measures all the critical parameters in the data center - temperature, humidity, fan speed, energy consumption, fire and water detection, etc - to ensure that operating conditions within the container remain constantly optimal. The redundant PLC takes over control of the data center within just 20 milliseconds in the unlikely event of the active PLC failing.
AST Modular selected the ABB solution for its modularity, robustness and ability to provide all the required functionality necessary to ensure that the data storage centers can operate at exceptional levels of reliability and availability. ABB's global footprint and ability to provide support and service all over the world were also vital to AST Modular's requirements.
The AC500 is one of the world's most widely used PLCs. Modular, scalable and flexible, the AC500 offers more memory (allowing more functionality, more precise algorithms and better visualization) than most competing PLCs. It is also one of the fastest PLCs on the market, providing faster programming, faster calculations and faster data transfer.
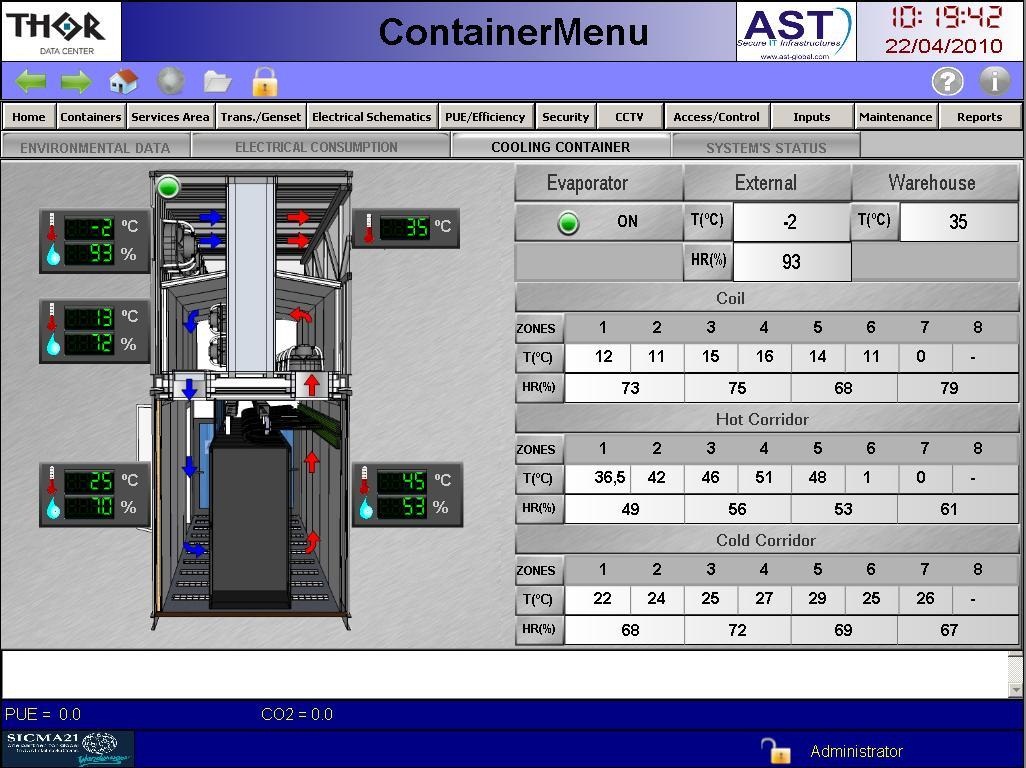
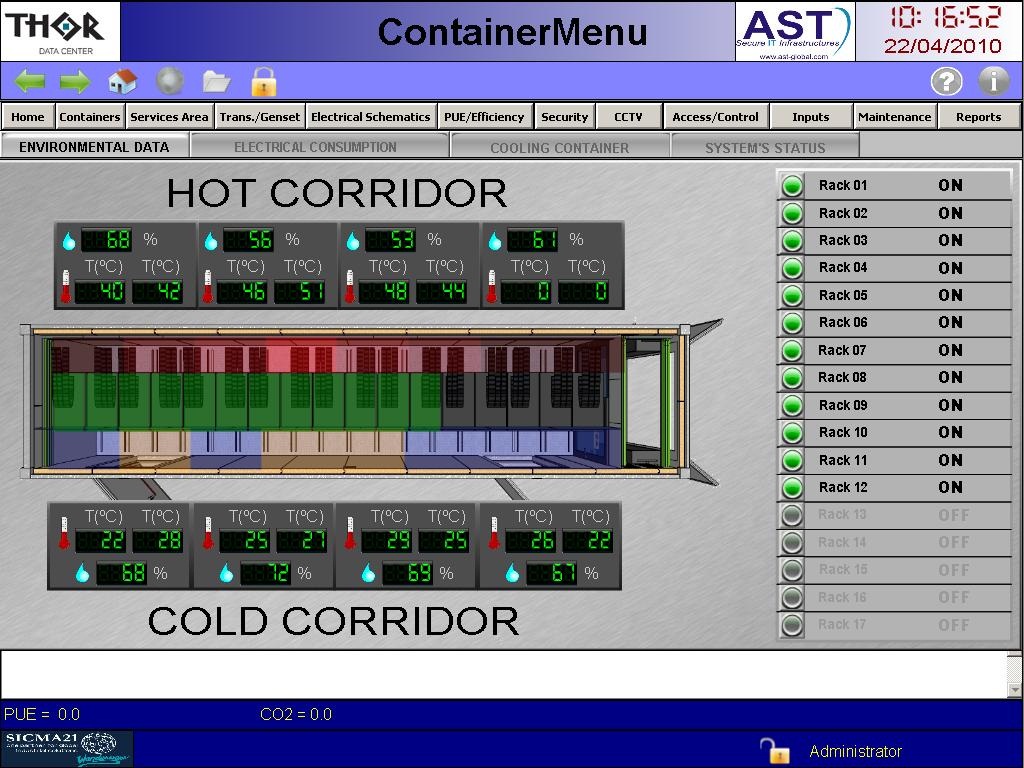
Screenshots of the data measured and monitored by the AC500. The data is transferred to a SCADA system and monitored from the AST Modular control room in Barcelona, Spain. The data can be accessed and alarms received by iPads, iPhones and other tablets and mobile devices.
ABB plant in Argentina the latest to harness solar power
A 160-square meter solar array was installed on the roof of the plant, and generates about 40 megawatt hours (MWh) of electricity per year, or 40,000 kilowatt hours (KWh) per year. Peak generation capacity is 26 kilowatts (kw). The average annual electricity consumption of a typical West-European household is about 4,300 kWh/year.
Project engineers calculate the solar panels reduce the factory's energy costs by about 1.8 percent annually. At peak generation, they can meet about 5 percent of the plant's power needs. ABB engineers also calculate the power generated avoids nearly 24 metric tons of CO2 emissions per year.
"A project like this brings ABB's commitment to social responsibility to life, and underlines our sincere efforts to minimize the impact of our daily business on the areas where we operate," said Christian Newton, ABB's acting country manager in Argentina.
In 2009, ABB in Argentina put together a strategic environmental plan. The goal is to find ways of optimizing the use of resources by applying ABB's own technical and operational ability to the company's industrial operations.
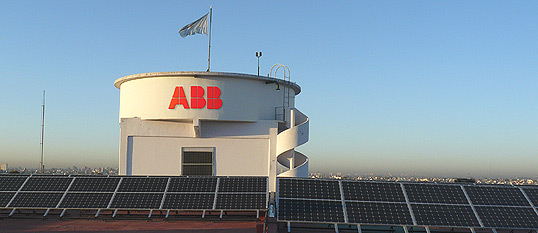
Other ABB buildings that have installed solar generating capacity include a low-voltage factory in Nelamangala, India; a drives factory in Helsinki, Finland; and ABB's head office and manufacturing complex in Modderfontein, South Africa.
"This was an interesting and challenging project, as ABB was both supplier and customer," said Duilio Magi, project manager. "We had to assemble a team and come up with a scope and delivery time that satisfied the final user, which was us. I want to thank my colleagues for their collaboration and flexibility, which helped us solve every difficulty and improve the final results of this project."
For the Buenos Aires factory ABB engineers designed six rows of 18 PV panels each, connected in series, as well as the structural frames holding the panels in place on the terrace. Building-installed PV systems are fine examples of distributed power generation, which helps to reduce the amount of electricity removed from the grid during peak daytime hours, increasing grid stability.
ABB provides water solution for the greatest show on Earth
The Glastonbury Festival in southwest England is one of the world's biggest and most popular open-air festivals for music and the performing arts. Held every year since 1970, the five-day festival takes place on a huge 10 sq km site and has a sellout attendance of 177,000 people a day.
Billed by its organizers as 'the largest temporary performance site on Earth,' this vast and sprawling tent and live entertainment complex requires extensive infrastructure to ensure that its city-size population is adequately provided with food, water, electric power, toilets and waste management facilities.
More than 11 million liters of water are consumed over the five-day period for drinking, washing and showers. The water is supplied from two purpose-built underground reservoirs via a pipeline distribution network and some 700 hand basins and 100 standpipes.
The entire storage and distribution network is monitored by a sophisticated ABB water measurement solution comprising SM500F videographic recorders and WaterMaster electromagnetic flowmeter systems.
The solution enables the festival organizers to accurately monitor reservoir levels, flow rates and water consumption throughout the whole site - for the first time in the festival's 41-year history.
It measures the flow rate of water pumped into the reservoirs and pipe system, correlates water supplied with utility billing, and provides a 'footprint' of consumption rates for any time period during the festival. Reservoir levels are monitored to provide an early warning of supply requirements and ensure dosing routes are in compliance and validate pump rates.
"The information collected by the solution is used for bill evaluation, giving us an accurate and easy to understand record of our usage," says Phil Miller, the festival's infrastructure manager. "This ensures that we don't pay for any more water than we actually use."
A second ABB multipoint videographic recorder solution (the award-winning SM3000) is recording energy parameters at the festival's photovoltaic power plant. The 1,116 solar panels generate 200 kWh of clean power and contribute to the site's energy requirements. The panels are located on the site's cowshed, otherwise known as the 'Mootel'.

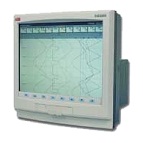
ABB's WaterMaster family of electromagnetic flowmeters for flow measurement and management |
The field-mountable SM3000 multipoint monitors and stores up to 2.8 million samples of data |
ABB's WaterMaster family of electromagnetic flowmeters for flow measurement and management |