In the smart factories of the future, processes take place in real time, production is flexible, and the entire value chain is automated from order to delivery. Production can be monitored remotely and customer orders and manufacturing handled automatically. Traceability is integrated into all stages of production, processing and distribution. This future has already arrived at ABB's plant for low-voltage products in Beijing. The plant benefits from improved competitiveness, more reliable deliveries, better quality and higher customer satisfaction.
There are 27 robots working alongside humans at ABB LV Installation Materials Co., Ltd., Beijing. The plant is largely automated and automation is used throughout the order-delivery process chain. The plant has applied automation to functions from parts manufacturing to assembly and logistics. Automation has increased the reliability of deliveries, product quality, competitiveness and profitability, leading to continuous improvement in productivity.

Smart manufacturing based on MES
The highly automated Beijing plant has entered the era of smart manufacturing with the help of manufacturing execution systems (MES).
MES can respond to customer orders in real time, enabling manufacturing system configuration to be set automatically according to customer needs. Automated assembly lines then assemble and test products via human-machine collaboration. This seamlessly connects customer demand and manufacturing, resulting in shortened lead time and improved services.
MES can also automatically generate production planning and scheduling based on real-time inventory levels. New orders are generated as stock runs low or big order is received. Automatic scheduling reduces the need to stock finished products and enhances operational efficiency.
With MES, the status of the Beijing plant can be monitored remotely. The production monitoring system works in real time and indicates equipment malfunctions, analyzes the status of each process, reports test results with root causes for rejected products, and generates statistics and reports from production data. "Talking" equipment can communicate with each other and operational status can be sent to engineers in real time for faster response.
Increasing automation improves the quality of the entire value chain.
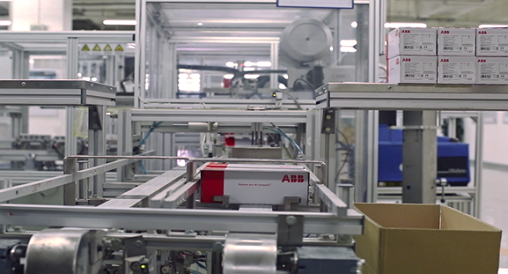
Wireless & mobile terminals eliminate bottlenecks
The Beijing plant uses wireless & mobile terminal solutions to register every shipment both in inbounding and outbounding logistics. As components arrive, they are unloaded and sorted for reception before being picked up by automated guided vehicles and put in storage or a production cell. This technology prevents bottlenecks and human logging errors and enhances the accuracy of the inventory and overall efficiency.
Assembly workers can use touchscreens to request more parts, and order is immediately placed in work queue. Automated dispensing system will bring the necessary components to the assembly line and inform logistics staff to transport assembled products away for delivery.
In a smart factory, automated monitoring and management is taking place in all stages ranging from production, testing to packaging and distribution because every product is uniquely marked with a QR code. This means products can be traced throughout the order-delivery process chain.
While humans and robots are working together in the plant and while increasing automation has reduced demand for assembly line workers, it doesn't necessarily mean that people will become obsolete. Humans are and will be needed to control and monitor the automation systems and to make decisions. Small-quantity assembly lines with complex products will also require human-machine collaboration.
Plant benefits from automation:
- The reliability of deliveries is now 99.94 percent, up from 96.73 percent.
- Productivity has improved more than 6 percent on average.
- The average lead time has improved from eight days to two.
- Manufacturing stability and quality has improved.
- Production can be adjusted according to demand.