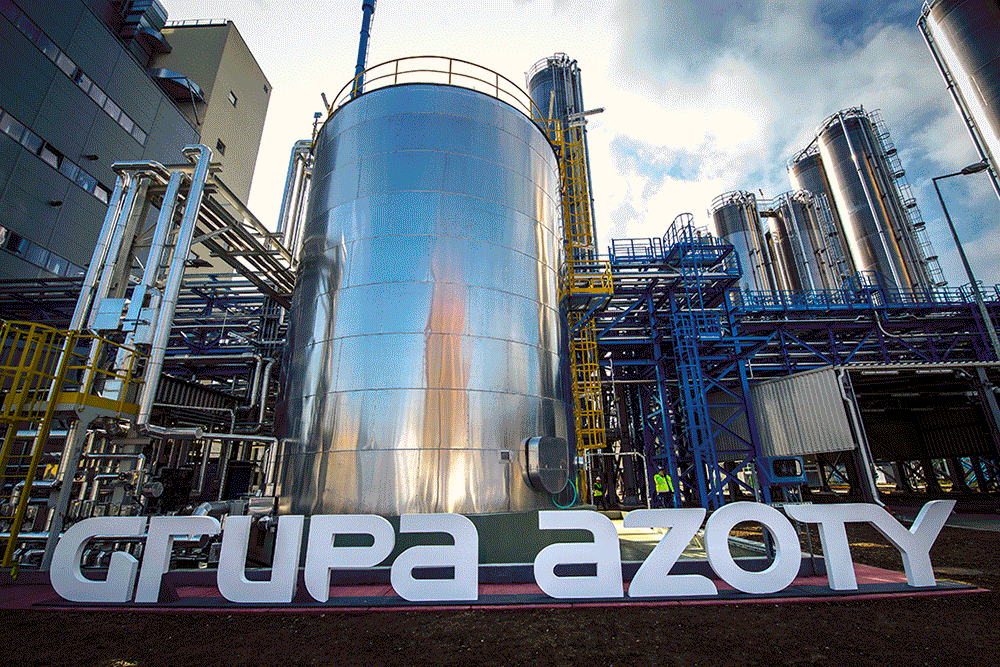
Grupa Azoty has opened a new plant manufacturing polyamide, which is a high-quality thermoplastic construction material. The new plant increases production by 80,000 tons annually, to around 170,000 tons, making Grupa Azoty one of the biggest producers of this material in Europe. The automation investment is an interesting example that demonstrates how the control system matched to the manufacturing profile can minimize the risk of failure and facilitate the everyday work of the operators.
Polyamide 6 (PA 6) is popular material that can replace metals and alloys in a number of products due to its high mechanical strength and heat resistance. It is used in the automobile industry, as well as electrotechnics, pharmaceutical and textile industries and others. In order to increase production of polyamide, Grupa Azoty invested $88 million in the construction of Polyamide Manufacturing Plant II. A part of this project is ABB's Freelance DCS system to control the manufacturing and pneumatic transportation lines. The system integrates many functions within one platform using digital communication. This enables operators to monitor the key parameters of polyamide's production and to control the complex process from one location.
The Freelance system plays a crucial role during polyamide production - it is responsible for overseeing measurement and analytics as well as controlling electrical equipment like drives. A non-standard solution is based on two portable control tablets. They are an addition to the fixed stations located in the central control room. It is a practical method to enhance remote control features. Thanks to the portable solution, the operator may quickly respond to any irregularities detected on the installation.
"The tablets allow operators to move freely in the area of the controlled installations without the risk of losing information about the process. The communication between portable units and the central Freelance system is performed via a wireless network," explains Remigiusz Rabsztyn from ABB's Industrial Automation Division in Poland. The tablets are explosion-proof, therefore they may be used in zones with risks related to hazardous substances.
Polyamide production is a complex process driven by many interrelated installations, which increases the risk of unscheduled downtimes. Therefore, elements of the Freelance system have been installed in a redundant layout. It means that in case of any interruption in the operation of the primary system, a redundant system is automatically activated and the line can operate continuously.
The order has been executed by ABB in Poland together with the following partners: Grupa Azoty Automatyka Sp. z o.o. - responsible for the software and start-up of the system - and Grupa Azoty Polskie Konsorcjum Chemiczne Sp. z o.o., which was responsible for design part of the control system. The combined manufacturing and pneumatic transportation lines control systems in Polyamide Manufacturing Plant II are currently the biggest solution of this kind at Grupa Azoty in Tarnów. It is already the fourth implementation of the Freelance system in the company-owned facilities. For a dozen or so years, it has been used by employees of Polyamide Manufacturing Plant I, and since 2009, in the mechanical fertilizer granulation system.
Grupa Azoty is the undisputed leader of the fertilizer and chemical market in Poland and one of its key players in Europe. It is the second largest EU-based manufacturer of nitrogen and compound fertilizers, and its other products, including melamine, caprolactam, polyamide, oxo alcohols and titanium white, enjoy an equally strong standing in the chemical sector, with a wide range of applications in various industries. In May 2017, the Group announced its updated strategy until 2020. The key development areas include finalising the Group's consolidation, reinforcing its leadership in agricultural solutions in Europe, strengthening the second operating pillar through expansion of the non-fertilizer business, and generating and implementing innovations to accelerate growth in the chemical sector.
ABB (ABBN: SIX Swiss Ex) is a pioneering technology leader in electrification products, robotics and motion, industrial automation and power grids, serving customers in utilities, industry and transport & infrastructure globally. Continuing more than a 125-year history of innovation, ABB today is writing the future of industrial digitalization and driving the Energy and Fourth Industrial Revolutions. ABB operates in more than 100 countries with about 136,000 employees. www.abb.com