Elevator installations require anchor bolts in the elevator shaft to precisely and safely fasten guide rails and access doors - lots of anchor bolts. The taller the building, the greater the number.
"Drilling holes to install anchors in a concrete elevator shaft is a painstaking, repetitive and physically exhausting task. High accuracy and full concentration are essential to working safely and precisely," explains Christian Studer, head of New Technologies at Schindler. "Hundreds of anchor bolt holes are required to install a lift in a high-rise. The shaft is noisy and dusty and the work taxing."
Schindler has developed an automated, robot assisted installation system dubbed "Robotic Installation System for Elevators" to improve quality and ease working conditions for elevator installers. Schindler launched the pilot project in collaboration with the university of science and technology ETH Zurich and software experts at ABB Robotics in Switzerland.
The robot's primary task is to drill holes and install anchor bolts in elevator shafts. But the robot encapsulates much more than that. This development comprises an autonomous installation system that moves independently from floor to floor by means of an automated hoist, something that has never been done before. "An additional design challenge was the difficulty we had programming the robot to consistently drill holes at the same coordinates within millimeter accuracy. The machine moves from position to position in the elevator shaft and must continually and dynamically adapt the drilling coordinates," explains Studer.
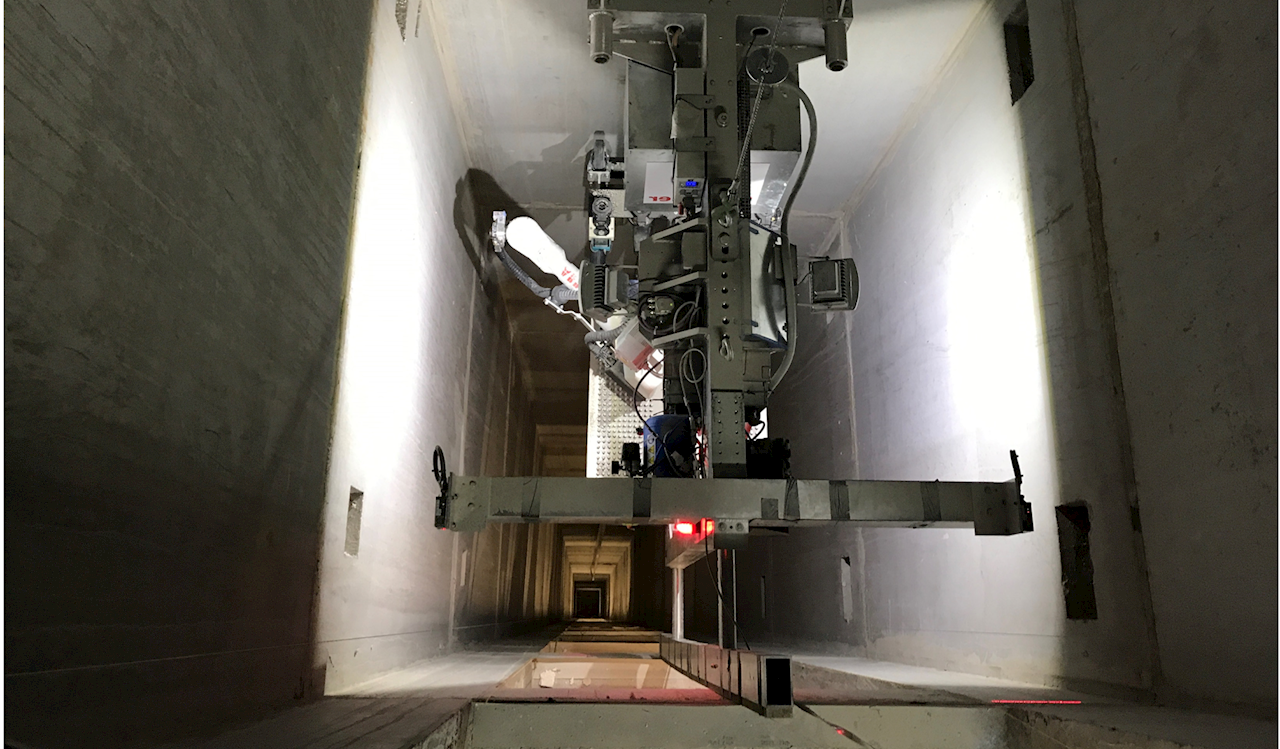
In principle, the drilling coordinates are predefined. But before starting, the robot scans the shaft wall to determine if there is hidden rebar underneath or if the concrete surface is uneven. The installation system uses an algorithm to calculate tolerances and repositions the holes as necessary.
Finding a suitable robot presented the project team with further challenges. They finally selected an ABB IRB 2600. "With a reach of 1.65 meters and a payload of twenty-nine kilograms, it suited the task well. Furthermore, ABB's robust industrial robots are known to operate reliably in tough environments, which is especially important for this application," says Studer.
An industrial robot is normally installed on a foundation in a factory and executes its program with reference to its zero position in space. For the "Robotic Installation System for Elevators" prototype, the IRB 2600 is mounted on a platform, which a temporary hoist moves up and down in the elevator shaft.
Image currently unavailable
Image currently unavailable
Image currently unavailable
Image currently unavailable
Image currently unavailable
Image currently unavailable
© Schindler © Schindler
"The robot was unable to reset to a new zero position for each drill site in this three-dimensional space, so we had to outwit the controller to some extent to ensure that the robot arm is exactly positioned at the hole coordinates each time," says Studer.
Sensors check to ensure the hole has been drilled in the right place before the robot hammers in the anchor bolts and moves on to the next drilling location - again and again, fully automatically.
"Although a camera is mounted on the platform to allow remote viewing and all data related to drilling the hole is documented, the system operates autonomously. No operator is required to monitor and control it," explains Studer. So, it can be simply installed in an elevator shaft, where it operates independently around the clock until all of the anchor bolts are installed.
The prototype has proven successful in several new elevator systems in Europe. "The IRB 2600 never failed once during the process, which speaks to how robust it is," adds Christian Studer.
At the Tall+Urban Innovation Conference in April 2019, the Council on Tall Buildings & Urban Habitat presented Schindler with an Award of Excellence in the Innovation category for its "Robotic Installation System for Elevators". Schindler’s plans call for increased use of these autonomous systems, all equipped with ABB's IRB 2600.
"Automation is a much-discussed topic in the construction industry," says Studer. "Elevator shafts lend themselves to digital construction thanks to their straightforward geometry. This autonomous system allows us to bring digitalization directly to the construction site. It is thanks to the latest sensor developments and artificial intelligence that we were able to implement this world premiere successfully," he concludes.
Schindler AG is headquartered in Ebikon and is a subsidiary of Schindler Holding. The company was founded in 1874 and currently has 65,000 employees worldwide. Schindler is one of the world's leading providers of elevators and escalators along with associated services. Its mobility solutions move over one billion people daily throughout the world. www.schindler.com