AI AND ROBOTICS: A FORMULA FOR FLEXIBLE FACTORIES
The combination of artificial intelligence (AI) and robotics can substantially improve the flexibility of factory automation by replacing rigid applications with learning capabilities. This powerful mixture of technologies enables the expansion of robot functionalities, thus improving productivity, making work safer and accelerating production. ABB’s range of applications in this area includes the use of AI to enable robots to sense and respond to their environment, inspect and analyze defects, and optimize processes autonomously.
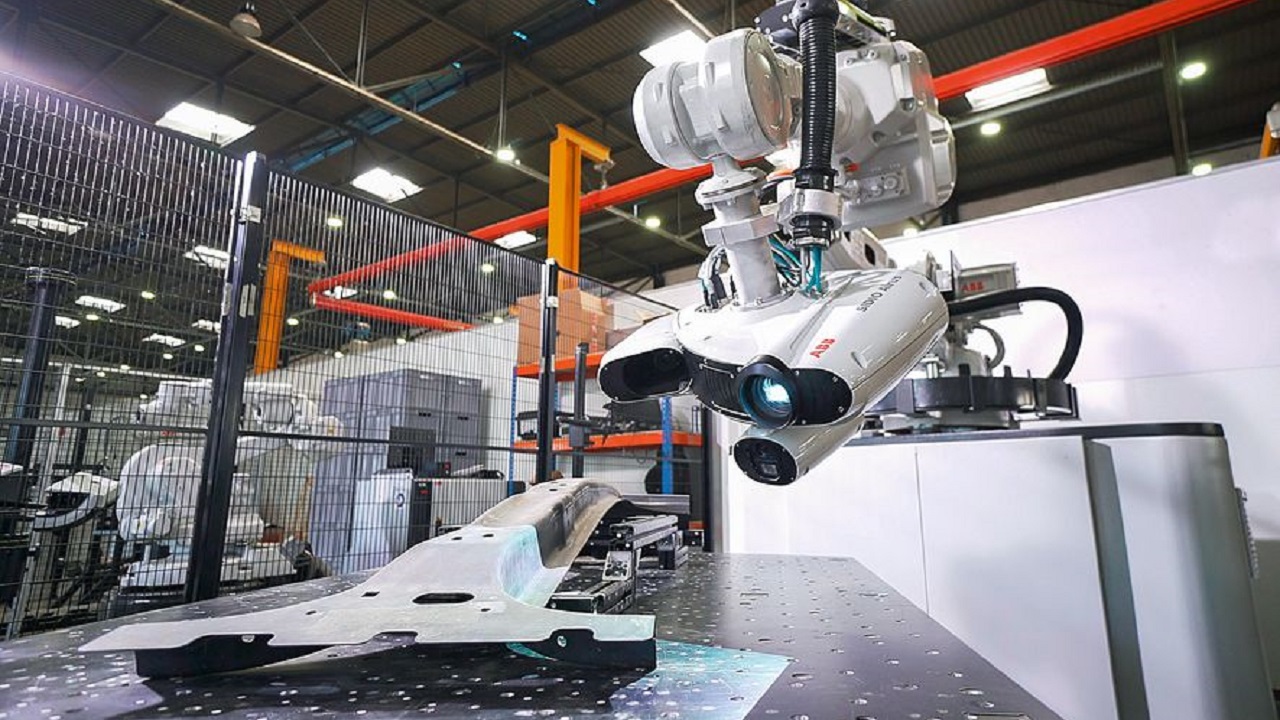
For instance, robots equipped with vision sensors can use AI to identify objects regardless of their position, while machine learning algorithms make it possible for robots to determine the best path and gripper positions for picking objects.
AI also enables robots to inspect and analyze a wide range of objects – welding seams are a case in point (graphic) – to detect defects and quality issues. This is achieved through a combination of vision sensors and supervised learning – essentially training by examples.
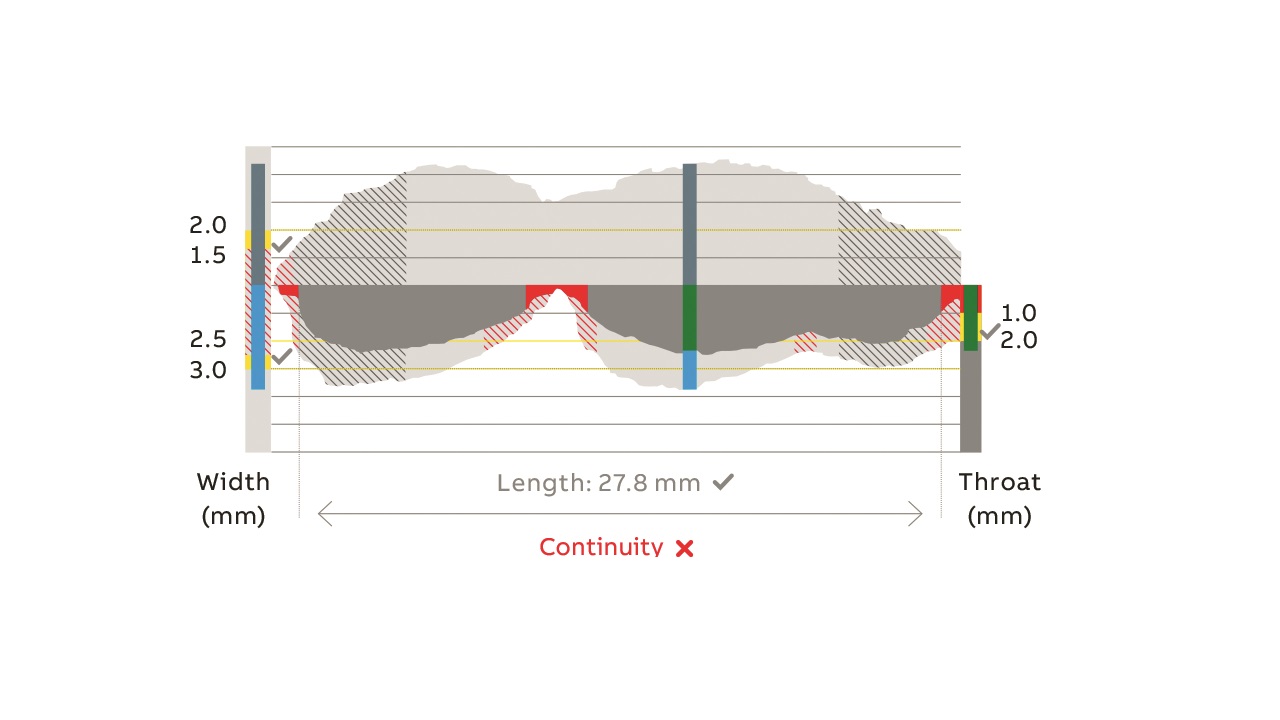
And when it comes to autonomous process optimization, there’s nothing else like the ABB Ability™ Connected Atomizer, the first connected, sensor-equipped, robotic paint atomizer to allow for real-time smart diagnostics and paint quality optimization. By monitoring the condition of key variables such as acceleration, pressure, vibration and temperature, the atomizer reduces internal waste during color changes by 75 percent and reduces compressed air consumption by 20 percent.
ABB is also applying AI algorithms to the analysis of presses and robot behavior in press and stamping lines to minimize equipment waiting times. Using a holistic approach, a control algorithm identifies bottlenecks and manages the start and stop times of robots and presses, thus making lines more stable and predictable.
ROBOTS: FOCUSING ON FINAL AUTOMOTIVE ASSEMBLY LINES
Automobile production plants are often pictured as highly automated, with lines of robots busily welding bodies. But not all aspects of vehicle production are as technologically advanced. Final assembly is a case in point. Here, the complexity of processes such as cabling, seat installation and cockpit insertion demands dexterous manipulation.
Nevertheless, engineers at ABB are developing techniques that will allow robots to perform a number of initial duties in this area. Probably the most difficult aspect of this challenge is the fact that during final assembly, vehicle bodies are constantly moving linearly. To deal with this, an associated robot is guided by a combination of visual and force control sensors in real time, rather than moving according to a programmed trajectory.
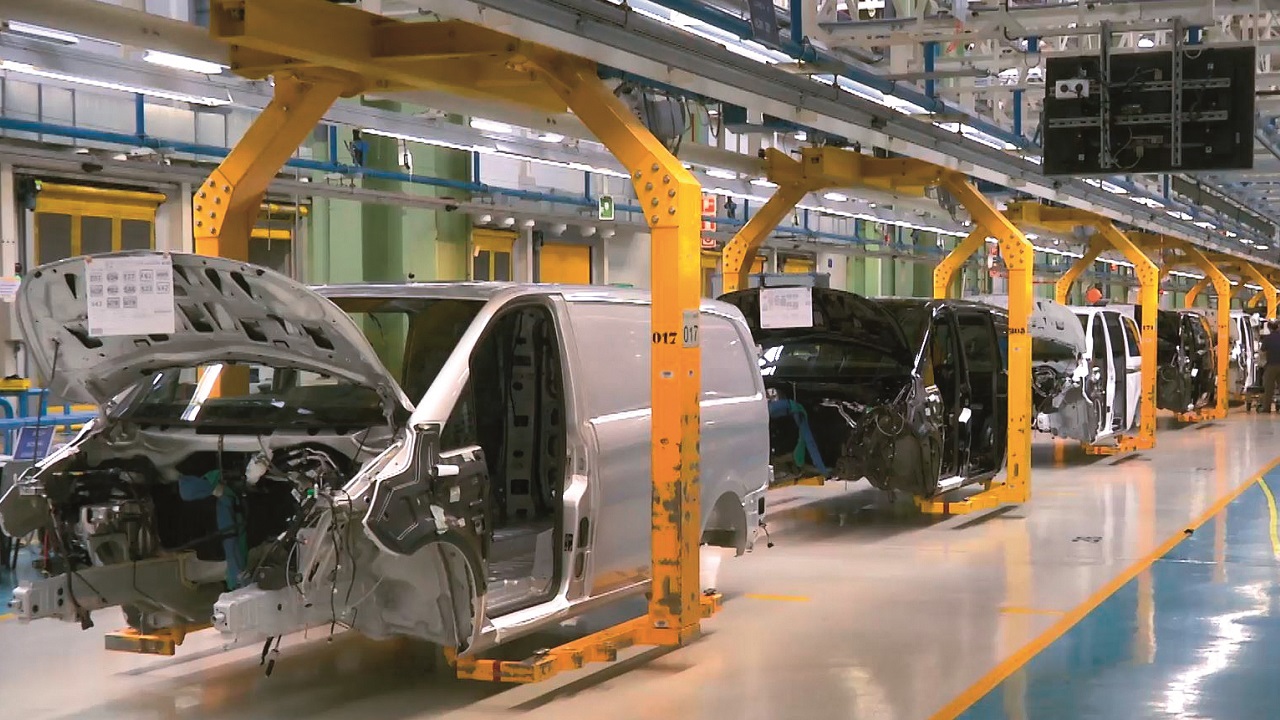
To complete an assembly task in this unstable environment, the first step is that the robot must synchronize with the assembly line’s linear movement. This is done by conventional conveyor tracking or by automatic guided vehicle (AGV) tracking technology. AGV tracking, which can also be used in conventional conveyors, is based on real-time vision tracking of high-range, two-dimensional bar codes known as AprilTags. An AprilTag is typically mounted on the AGV-equipped device that is transporting a vehicle while the tracking camera is fixed either in the floor or in the robot foot, when the robot is mounted on a linear axis.
Once a robot has been synchronized with a target vehicle’s movement, it starts performing an assembly task while continuously tracking natural features of the target assembly area with an ABB-developed functionality known as Real-Time On-Board Vision that is installed on its gripper. The input from this vision system is combined with continuous feedback data supplied by a force control sensor installed between the robot’s wrist and gripper.
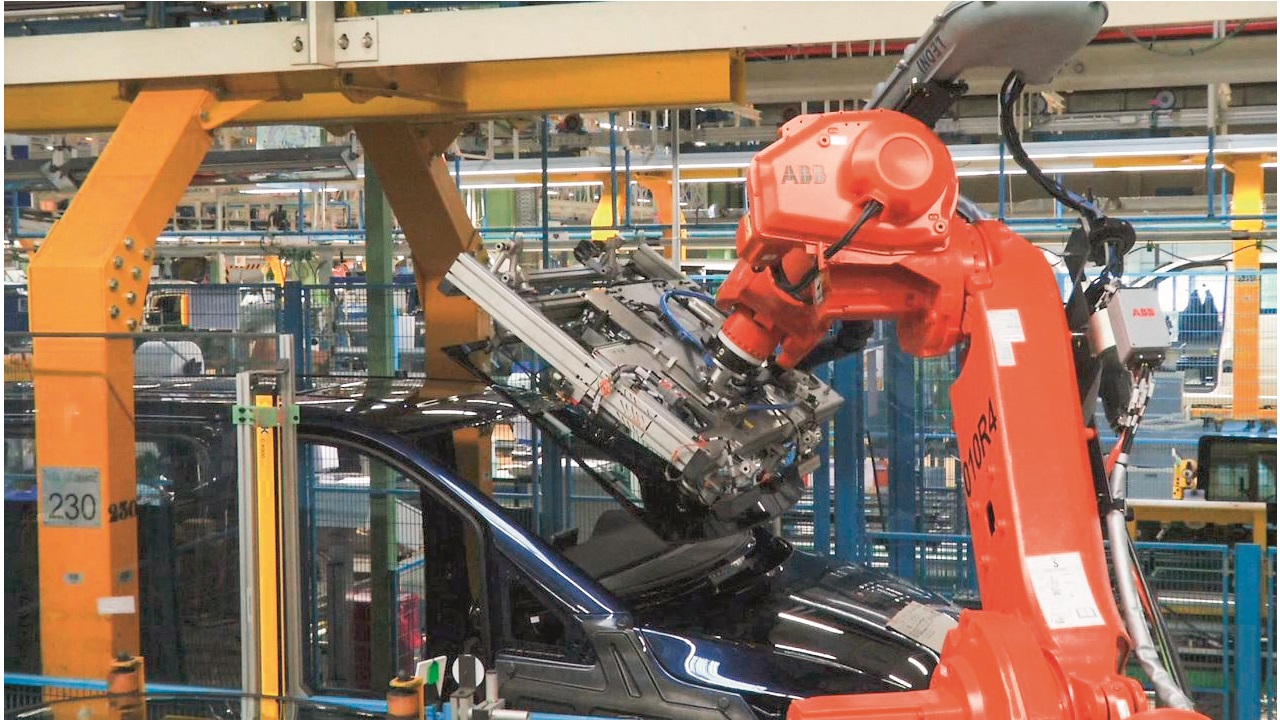
The combination of real time on-board vision guidance and force-controlled manipulation (sensor fusion) is the key to successfully performing a given assembly process. Pilot application cases are now in progress in coordination with a major automobile manufacturer. For instance, cockpit assembly is currently underway in German and Chinese plants. Experience gained in these and other facilities is potentially highly applicable to other automotive assembly applications, as well as to other manufacturing environments characterized by continuously moving targets.
ABB EXPANDS AZIPOD® POWER RANGE FOR FERRIES AND ROPAX VESSELS®
Since its launch in 1990, Azipod electric propulsion has become the industry standard for a wide range of vessels, from small craft to icebreakers. In response to customer requests, ABB has filled the gap between the low- and high-power Azipod propulsors with the launch of a new series available in the 7.5 to 14.5 MW range. In addition to ferry and RoPax (roll-on/roll-off passenger) vessels, this power range is also relevant for larger offshore construction vessels, midsize cruise ships and shuttle tankers. With this addition, the Azipod propulsion family now flexibly covers the power range of 1 to 22 MW.
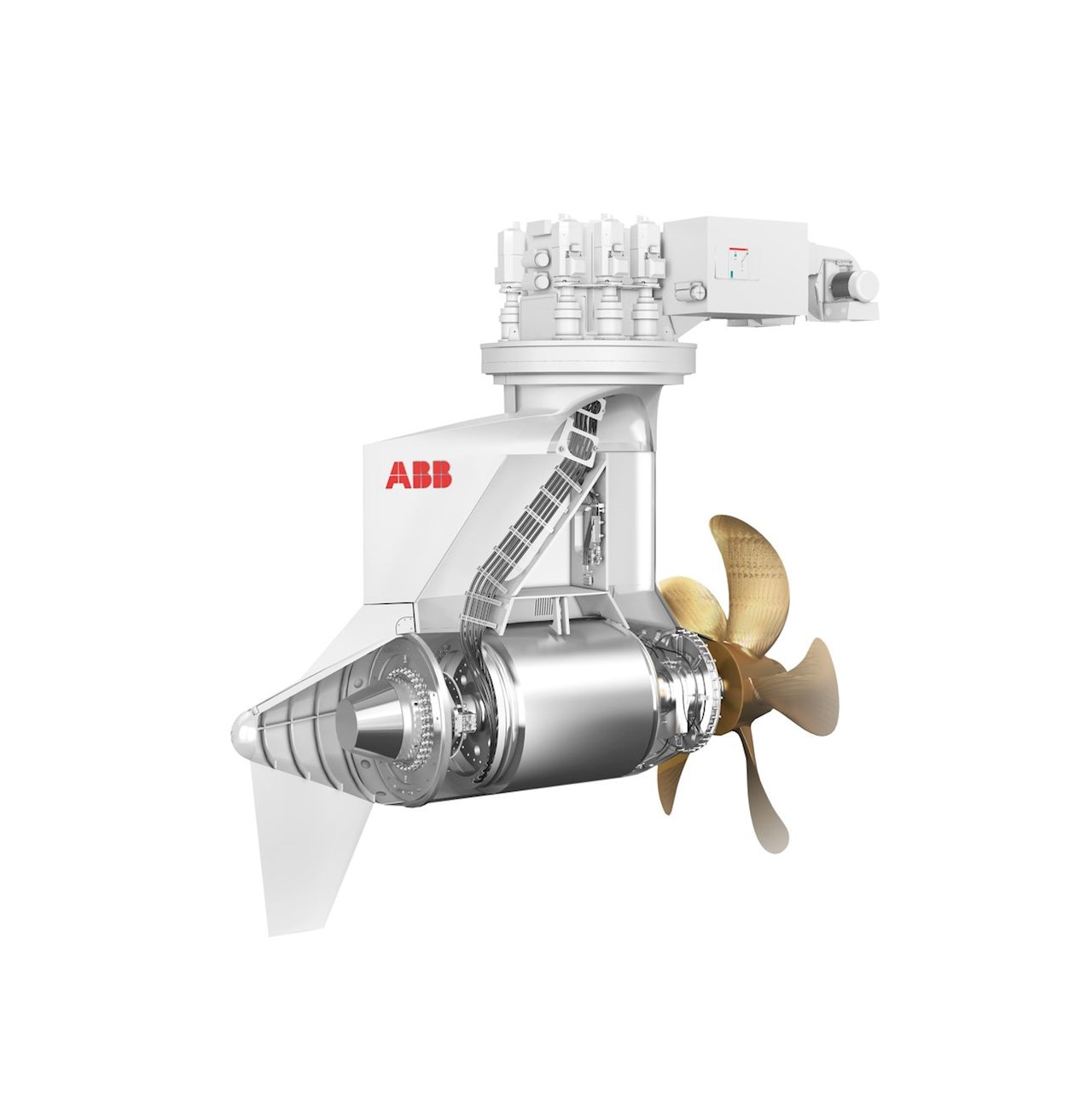
At the core of the new midpower range are ABB’s latest fourth-generation permanent-magnet motors, which draw on proven Azipod propulsion technologies but which have been refined to increase power and maximize efficiency. The design simplicity of the propulsion system provides increased robustness and reliability and makes maintenance easy.
Additionally, this “M” series of Azipod propulsion is tailored to provide operating benefits for ferry and RoPax owners and operators. For example, the new series is designed for low onboard height, which allows the Azipod system to be located under the car deck of RoPax vessels so no deck space is taken up and vehicle movement is unhindered.
Based on the straightforward, robust and easy-to-maintain design principles that have seen Azipod propulsion selected across 25 vessel types over close to three decades, the latest midpower series comes to market at a time when ferry and RoPax ship owners face increased pressure to improve energy efficiency and cut emissions.
OMNICORE™ ROBOT CONTROLLER NOMINATED FOR THE IERA INNOVATION AWARD
ABB’s OmniCore™, a new generation of robot controllers designed for the flexible factories of the future, has been shortlisted for the 2019 Invention and Entrepreneurship in Robotics and Automation (IERA) award. Considered one of the most important competitions in the robotics industry, IERA recognizes companies and inventors who turn innovative ideas into market-changing products. The award is presented by the International Federation of Robotics (IFR) and the IEEE Robotics and Automation Society.
ABB’s robot controllers are already recognized for their best-in-class path accuracy and cycle times. In developing OmniCore, ABB built on these characteristics while creating a new controller that significantly increases manufacturing flexibility yet is future proofed for developments in the digital manufacturing age.
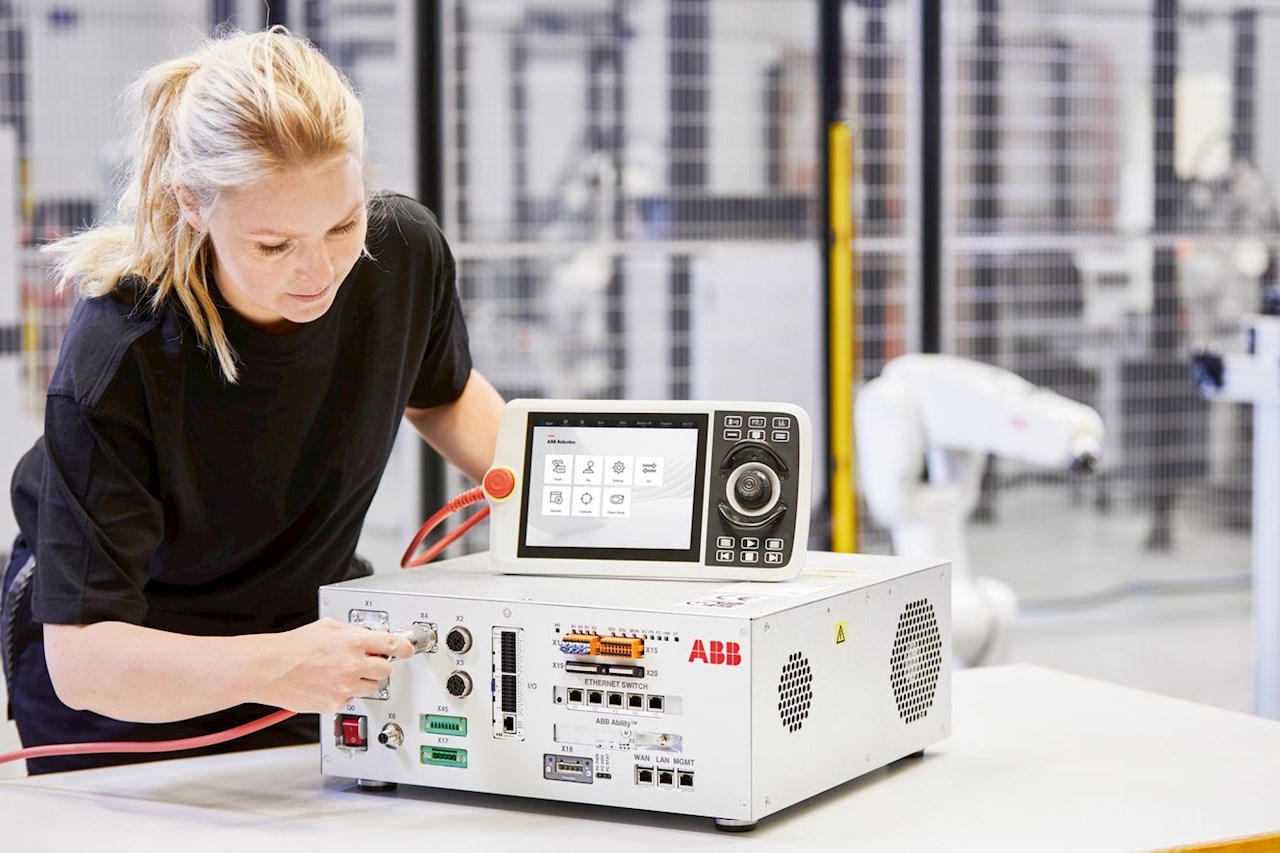
Thanks to its high level of flexibility, OmniCore gives customers the ability to produce an increasingly diverse mix of products in smaller lots while maintaining productivity.
Featuring “Power-on and Connect” and ABB Ability™, OmniCore can be connected to advanced services that increase performance and reliability, while offering easy connections to a variety of fieldbus protocols, as well as vision and force control systems for complete solutions. OmniCore includes cyber security enforcements to prevent data loss, thereby closing the loop between connectivity, data and control. It also includes SafeMove2, an ABB software solution that transforms industrial robots into collaborative robots capable of safely working alongside humans while remaining productive.
Despite all these advanced features, OmniCore is simple and intuitive to use and is accessed through a newly designed FlexPendant human-machine interface with a simple touch screen for visual programming.
SUBSEA ELECTRIFICATION SYSTEM ENABLES THE OIL AND GAS INDUSTRY TO TAKE THE DEEP-WATER PLUNGE
In 2013, ABB and its joint industrial partners, Equinor, Total and Chevron, began an expansive project to design and test a complete subsea electrification solution for the oil and gas industry. To enable operations at remote locations in ultra-deep waters, ABB developed modular equipment – components and assemblies – that integrate to form a subsea electrification system.1 The system consists of variable speed drives (VSDs) switchgear and a protection and control system for the transmission, distribution and conversion of power to subsea pumps and gas compressors at a peak capacity of 100 MW to water depths up to 3,000 meters; and with transmission distances up to 600 km with lifetime requirements for up to 30 years. Topside area is freed, power supply demands and greenhouse gas emissions are reduced.
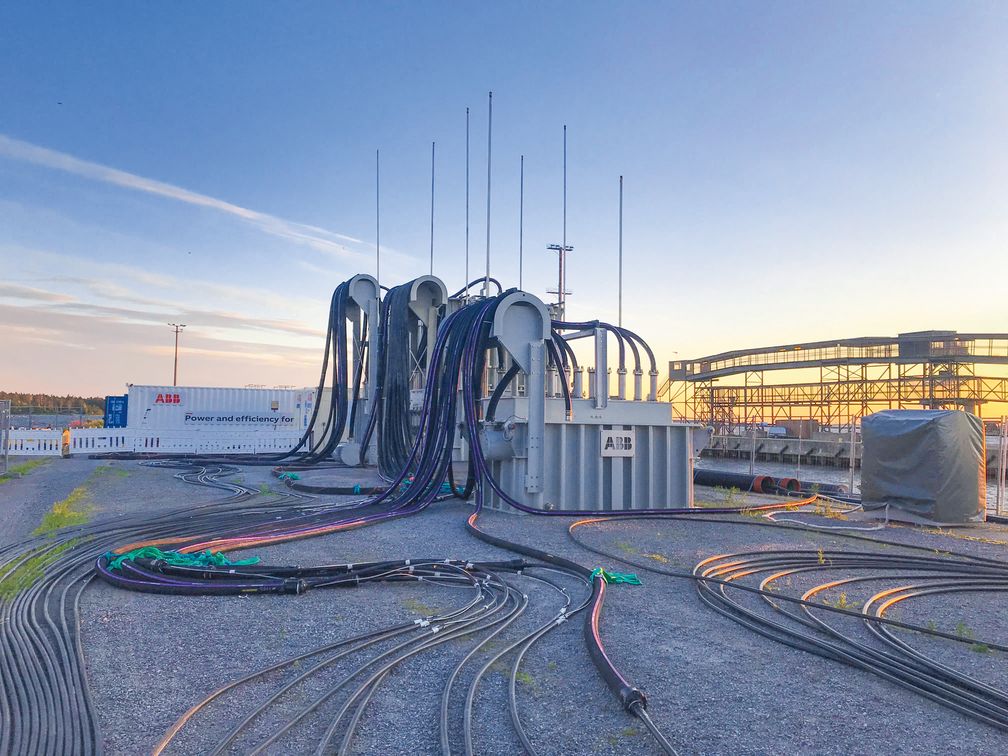
Adopting a pragmatic step-wise approach to equipment design, ABB successfully ran simulations, laboratory and field tests to ensure every component, sub-assembly and assembly met qualifications according to Technical Readiness Level (TRL) stages defined in DNV RP-A203 and API 17F Standard for Subsea Production Control Systems.
Satisfied with individual device results, shallow water tests (SWT) were conducted: a prototype of a medium-voltage VSD, was operated in a protected harbor test site for over 1,000 hours2, with impeccable results.
In June 2019, a second SWT was run – this time for 3,000 hours – of a prototype of the entire electrification system: two VSDs in parallel configuration with switchgear and controls. Results of this test and all previous qualification accomplishments ensure system reliability under harsh subsea conditions. This successful SWT test, completed in November 2019, lets the oil and gas industry know that this electrification solution is ready-for-use in the remote subsea environment.
Footnotes
1) Stimulated your interest? There is more to read in this issue about the system, its design and qualification on p.44, “ABB’s subsea technology is powering the seabed for a new energy future”.
2) Please refer to “Setting a course for subsea power conversion facilities” for an in-depth article about the technology, design and functionality of the subsea variable speed drive (VSD) on p.50.
ULTRAFAST HIGH-CURRENT DC BREAKER BASED ON POWER ELECTRONICS
DC distribution systems often need very fast fault protection that simultaneously provides protection selectivity, high survivability and reconfigurability after a fault. ABB has now developed a power-electronics-enabled solid-state DC circuit breaker (SS DCCB) with extremely low conduction losses, high power density and ultrafast reaction time that meets these protection challenges. The high-current SS DCCBs are rated for nominal currents of 1,000 A to 5,000 A, at an operational voltage of 1,000 V DC, and can interrupt a prospective short-circuit current of several hundreds of kA, up to 1,000 times faster than electromechanical circuit breakers.

ABB’s SS DCCB is based on the parallel connection of silicon reverse-blocking integrated gate-commutated thyristors (RB-IGCTs) that were developed in-house by ABB. The solid-state breaker can be cooled with water for high power density or, alternatively, with advanced two-phase cooling, which delivers the simplicity of air cooling with a performance close to that of liquid cooling and ensures low installation and maintenance costs and long asset life.
Power losses are 70 percent lower than comparable power-electronics solutions.
With all-electric ships becoming more popular, DC onboard power distribution is attracting a lot of attention thanks to its ability to handle large power flows in a confined space with high system efficiency and low life cycle cost. The SS DCCB is perfect for such marine applications and it is there that the device will be used initially. This is the first ABB breaker that is ready to be integrated straight into any DC ship distribution system. A modular architecture, simplified hardware and digital interfaces ensure maximum flexibility.
The new breaker is ideal for numerous other areas too, such as DC microgrids, battery energy storage systems, data centers, electric vehicle charging infrastructure, etc. First commercial application is planned for this year.
ANOMALY DETECTION APP HELPS ROBOTS REDUCE DOWNTIME
Everyone knows what an anomaly is… right? Well, if all the buttons on your shirt match except for one, that’s pretty obvious. But when it comes to separating real alarms from false alarms generated by factory robots, things can get tricky.
A branch of machine learning, anomaly detection focuses on detecting and identifying discrepancies that significantly deviate from the majority of other observations in large data sets or data streams. Such discrepancies, if repeatedly detected and localized, can provide an early warning of malfunctions or confirmation of an event that may require human attention.
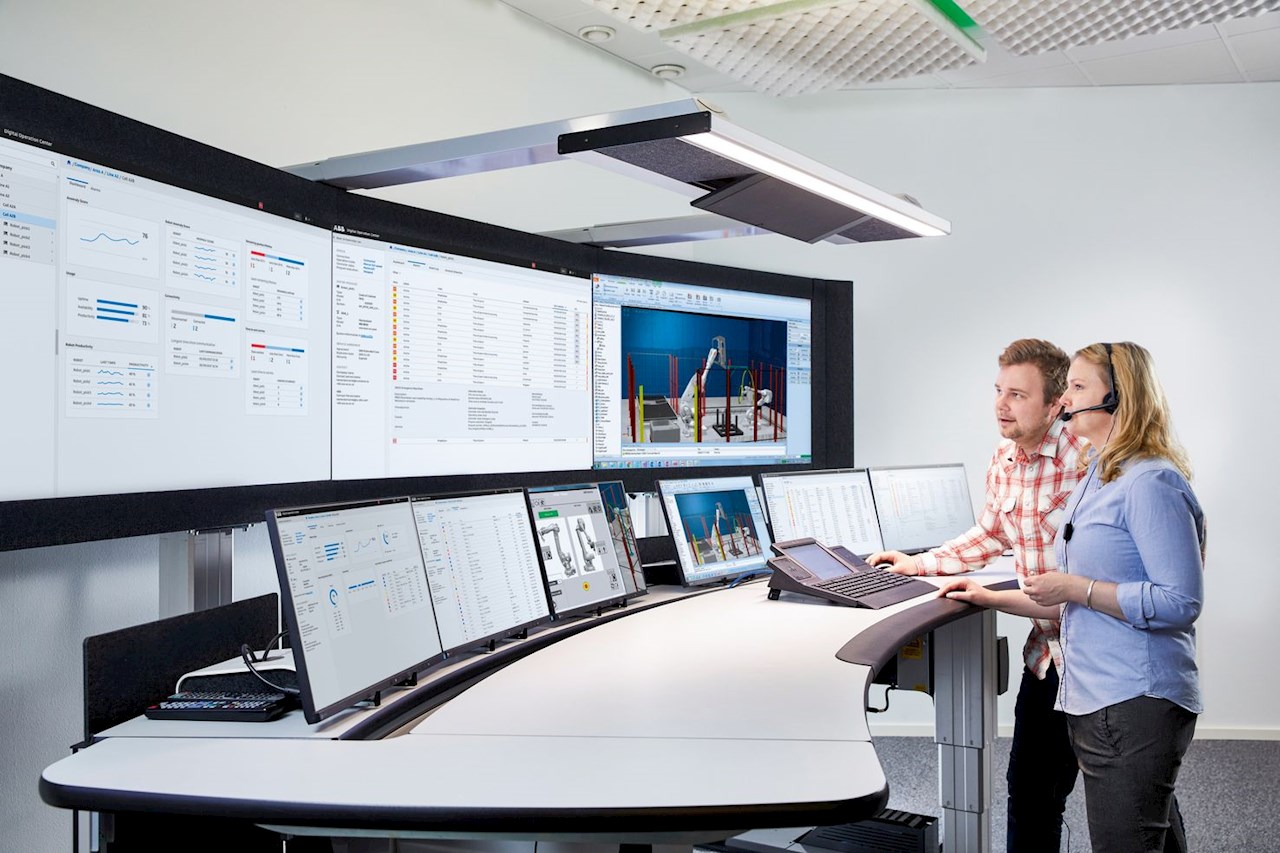
By using an historical approach to a huge amount of data, ABB software engineers have developed a statistical path to understanding the event distributions for individual robots in factory environments and obtaining robot status information in real time while each robot is in operation. The approach is designed to show anomaly scores in robot fleet dashboards, generate event alarms automatically, be proactive and predictive in executing maintenance activities, reduce downtime, avoid micro stops and, ultimately, maximize overall equipment effectiveness (OEE).
The idea is to create a tool that customers can use to manage physical parameters’ data as well as robot-generated alarms and events on an aggregated basis with a view to obtaining robot status updates, together with score trend graphs that might indicate future issues and a way to quickly identify the root causes of problems.
The tool will be offered by ABB as a machine learning-based application and it will be part of the latest generation of ABB Ability™ Connected Services.
EC TITANIUM INTEGRATED INTELLIGENT MOTOR AND DRIVE
As its name suggests, ABB’s new EC Titanium integrated intelligent motor and drive combines both motor and variable-speed drive (VSD) into one easy-to-install package. The EC Titanium is aimed at 1 to 10 hp applications and incorporates the latest advances in motors and drives into a highly efficient, compact and connected solution.
A ferrite-magnet-assisted synchronous reluctance (FASR) motor design was chosen as low losses mean these motors can cost-effectively reach an efficiency class of IE5. An easy-to-install design and high power density (twice that of induction motors) are further benefits.
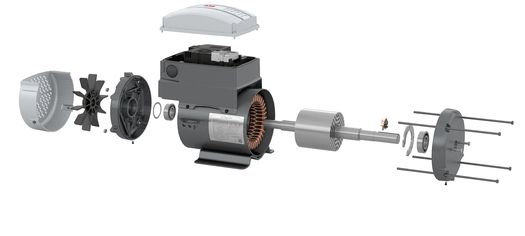
An integrated VSD allows customers to match drive speed to process requirements and operate equipment at its most energy-efficient point, thus extending lifetime, saving energy and making conformity to efficiency regulations easier. There is a high total system efficiency at full load. At partial load, where many customers operate, efficiency can be 16 percent better than with an equivalent induction motor.
Other benefits for pump and fan applications include reduced inventory requirements as different flow rates are available from the same package. Further, integrated products lower costs through part reduction and simplified purchasing and assembly. The EC Titanium offers customers multiple connectivity options (hard-wired, RS485 or Bluetooth). Moreover, the drive acts as a sensor for the motor/drive package and a Smart Sensor for Motors can be added to measure additional performance parameters. Once connected, data can be sent to the ABB Ability™ platform where software with advanced algorithms analyze the information and detect anomalies for condition monitoring and predictive maintenance.
3RD GENERATION PICK-AND-PACK SOFTWARE CUTS COMMISSIONING TIMES FROM DAYS TO HOURS
How can manufacturers respond efficiently to demands for mass customization and shorter product life cycles? Increasingly, the answer is digital twin technology, which allows customers to test out configurations on virtual production lines before physical lines are modified or built.
With this in mind, ABB Robotics has launched the third generation of its PickMaster® software for robotic picking and packing applications.
The software is the market leader for easy configuration of complex robotic actions and has set the industry benchmark for simplifying robot integration in vision-guided random flow picking, packing, and material handling for more than 18 years.
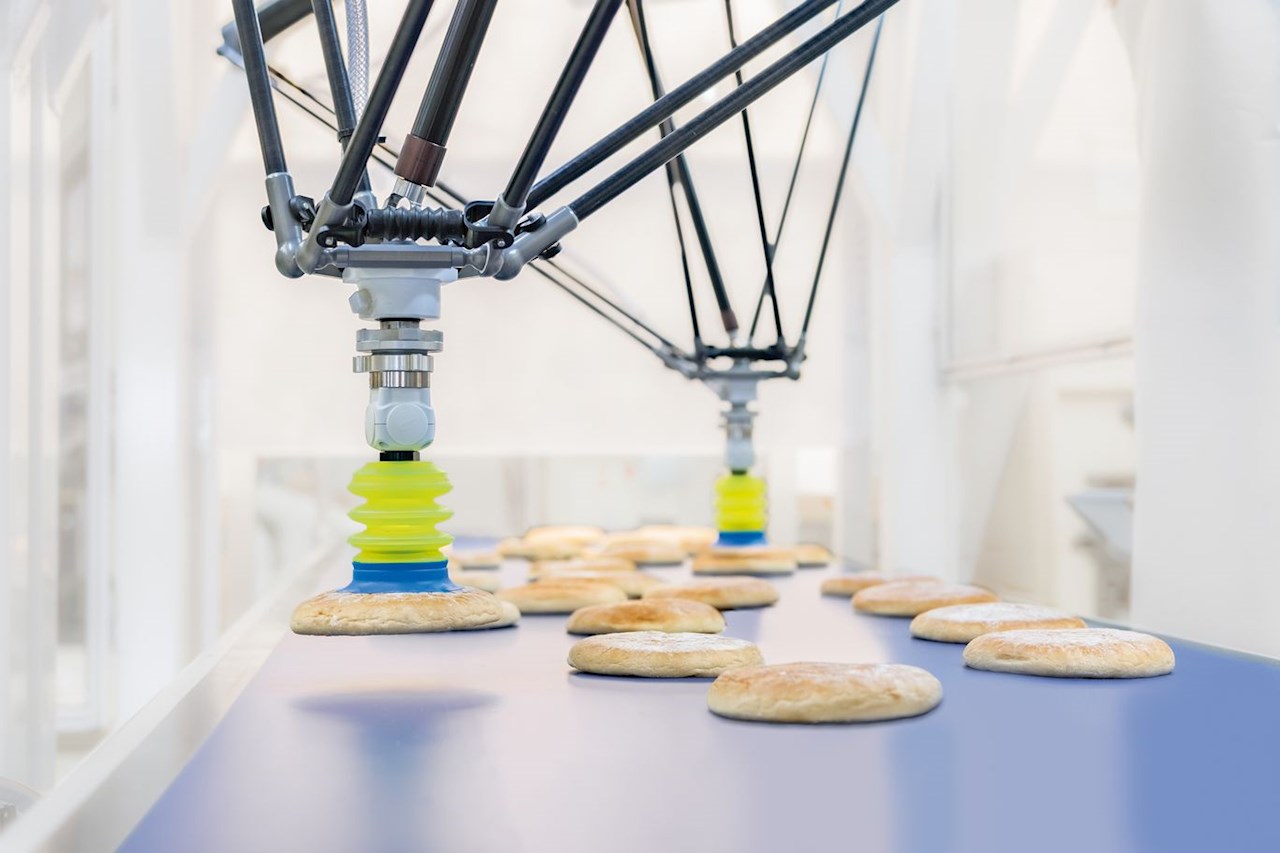
Equipped with digital twin technology for the first time, the software shortens commissioning times from days to hours and cuts changeover periods from hours to minutes. It offers greater flexibility and improved visualization of the cooperation of multiple robots, thus achieving optimized flow results without product losses or incomplete packages in flow-wrapping, tray loading, case and carton packing and handling applications.
As the software enables the offline programming of picking and packing tasks, users can create, simulate and test a complete robot installation in a virtual environment without interfering with their actual production lines. Using digital twin technology, the picking process can be optimized in the virtual world in real time while the real process acts accordingly. This not only helps customers mitigate costly and time-consuming risks, but also shortens the time to market for new products, as product lines can be installed faster and ramped up to full speed without surprises during commissioning.
PickMaster® also offers a modern operator interface for the factory floor, giving operators and plant managers full insight and control of production results. Compliant with the PackML industry standard, it integrates seamlessly with other packaging machinery as well as with production and factory planning systems.
PickMaster® is available in a multitude of configurations and can work seamlessly with all ABB robots, as well as with a range of virtual and physical machines. It is best suited for factories and production lines where higher output, faster response times and quick changeovers are vital.
A200-H – THE NEW BENCHMARK IN SINGLE-STAGE TURBOCHARGING
ABB’s flagship single-stage turbocharger generation, the A100-H, currently leads the single-stage turbocharging field with pressure ratios up to 5.8, an efficiency of up to 66 percent and brake mean effective pressure (bmep) of up to 22 bar. For higher bmep, ABB’s Power2® two-stage system fits the bill. For an application with a bmep of between 22 and 24 bar, two-stage turbocharging is potentially too complex.
To fill this gap between single- and two-stage turbocharging, ABB has developed the single-stage A200-H, with a pressure ratio up to 6.5 and a peak turbocharger efficiency in excess of 69 percent. The A200-H enables single-stage turbocharging on high-speed gas engines with a bmep of approximately 24 bar while increasing engine efficiency compared to the A100-H.
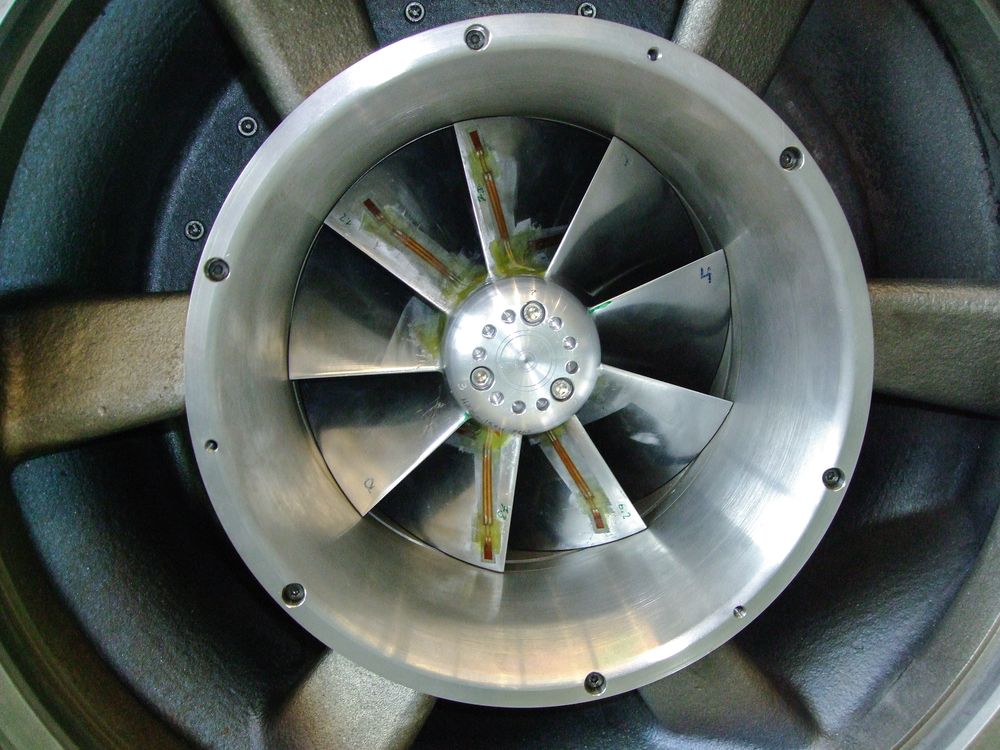
The A200-H turbine has been matched to the compressor to obtain the highest possible turbocharger efficiency while meeting the mechanical requirements. Further, with a view to future peak-shaving applications with many start-stop cycles, housing stress has been minimized.1
For the first time, the customer can choose between two bearing concepts: a patented bearing module design that supports ABB’s plain bearings or newly developed and highly efficient ball bearings, which, at part load, have a power loss of around 15 percent that of the plain bearing option. These new bearings reduce time-to-full-load by 15 percent.
Monitoring of turbocharger speed and temperature, start-stop cycles, ambient conditions and other parameters will be introduced using turbocharger-integrated sensors or by accessing genset data. These rich data sources enable an exposure-based component life assessment and can, for example, enable rotors to exceed the runtime predefined by more rigid conventional approaches.
Footnotes
1) For more information on the A200-H turbocharger, please also see “A200-H – the new benchmark in single-stage turbocharging” on pages 56-61 of this issue of ABB Review.