Aldo Dagnino ABB Advanced Analytics Cary, NC, United States, aldo.dagnino@us.abb.com, Carsten Beuthel S+ Operation Mannheim, Germany, carsten.beuthel@de.abb.com, Thomas-Christian Skovholt Digital Delivery Oslo, Norway, thomas.skovholt@no.abb.com, Martin Hollender, Marcel Dix ABB Corporate Research Ladenburg, Germany, martin.hollender@de.abb.com, marcel.dix@de.abb.com
Large processing plants such as petrochemical and power generation facilities rely on complex control systems to keep processes, equipment and operations on track to produce successful outputs. Originally, panel boards with control instruments connected to sensors yielded analog information on display to a well-trained expert who decided what needed to be done. Emergency systems were activated to stop a process in danger of surpassing safety, environmental or financially acceptable limits.
With the birth of distributed control systems (DCS), operators could control processes without understanding the equipment. Configuring and deploying alarms with ease, engineers set alarms throughout the system (typically, at 80 and 20 percent of equipment operating range). The consequence was a proliferation of alarms – every event set off an alarm. Suddenly process plants had to deal with too many alarms due to too much available data, yet insufficient germane information. Limited visual display space required operators to follow instruction manuals in case of an event – a laboriously slow process.
Even though the DCS is part of the Industrial Internet of Things (IIoT), the amount of big data, level of automation, availability of inexpensive accurate sensors, unlimited data storage, and visualization display complexity necessitate a more straight-forward control system that focuses the operators’ attention quickly on pertinent information – to as few and important events/alarms as possible →01. But what if operators could predict critical events before they occur? They could prevent the loss of production and throughput; equipment breakdown and events that threaten both environmental and human safety. To accomplish this ultimate goal, ABB has focused on delivering its customers such a system: ABB’s Intelligent Alarm Management (IAM).
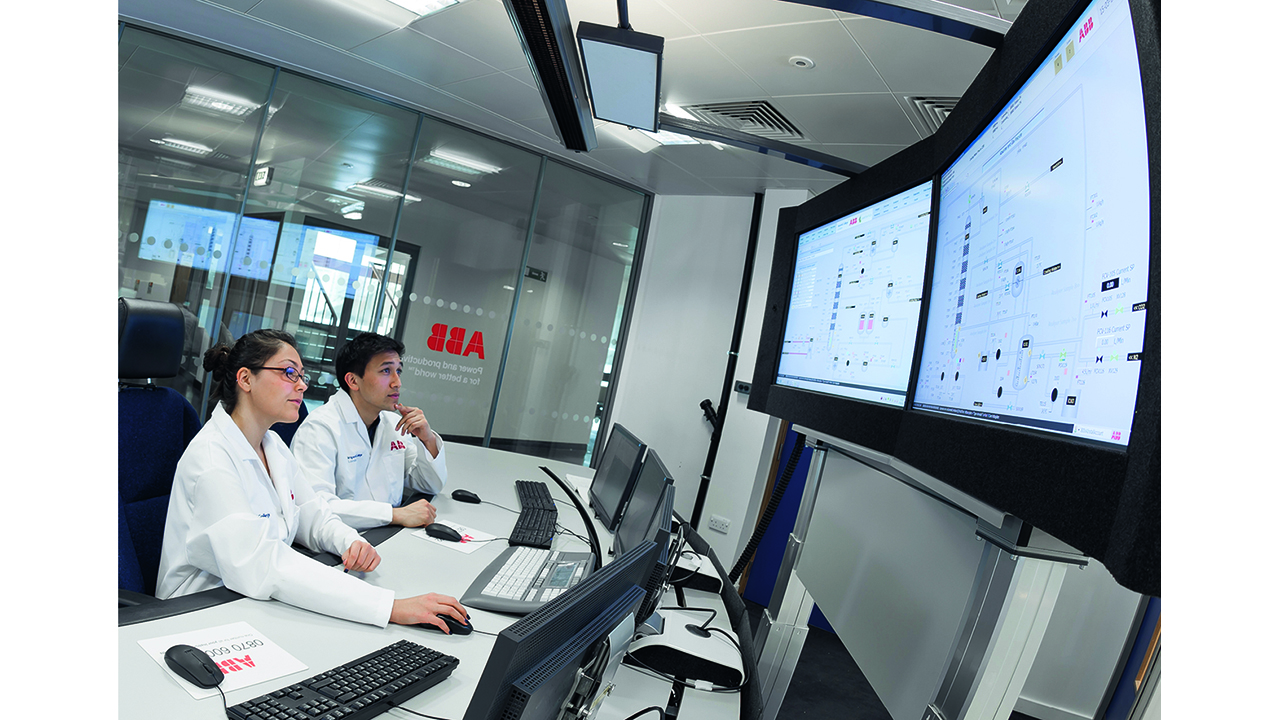
Intelligent Alarm System
Today, alarm management system design must incorporate ergonomics, instrumentation engineering, systems thinking, advanced analytics and visualization to enhance the usability of the control system. Seizing on their expertise in the IIoT ecosystem and DCS experience, ABB’s resultant IAM surpasses existing concepts to perfect analysis and usability. Not only is an extra analysis level added to reduce nuisance alarms (de-chattering), a further sophisticated three-layered second level of analysis has been engineered. The IAM consists of a data layer that extracts alarms and creates an alarm data model according to 25 attributes, an analytics layer with newly developed algorithms to precisely and repeatedly analyze alarm data, and the graphical user interface (GUI) visualization layer based on ABB’s user-design concept for viewing the analytical results →02.
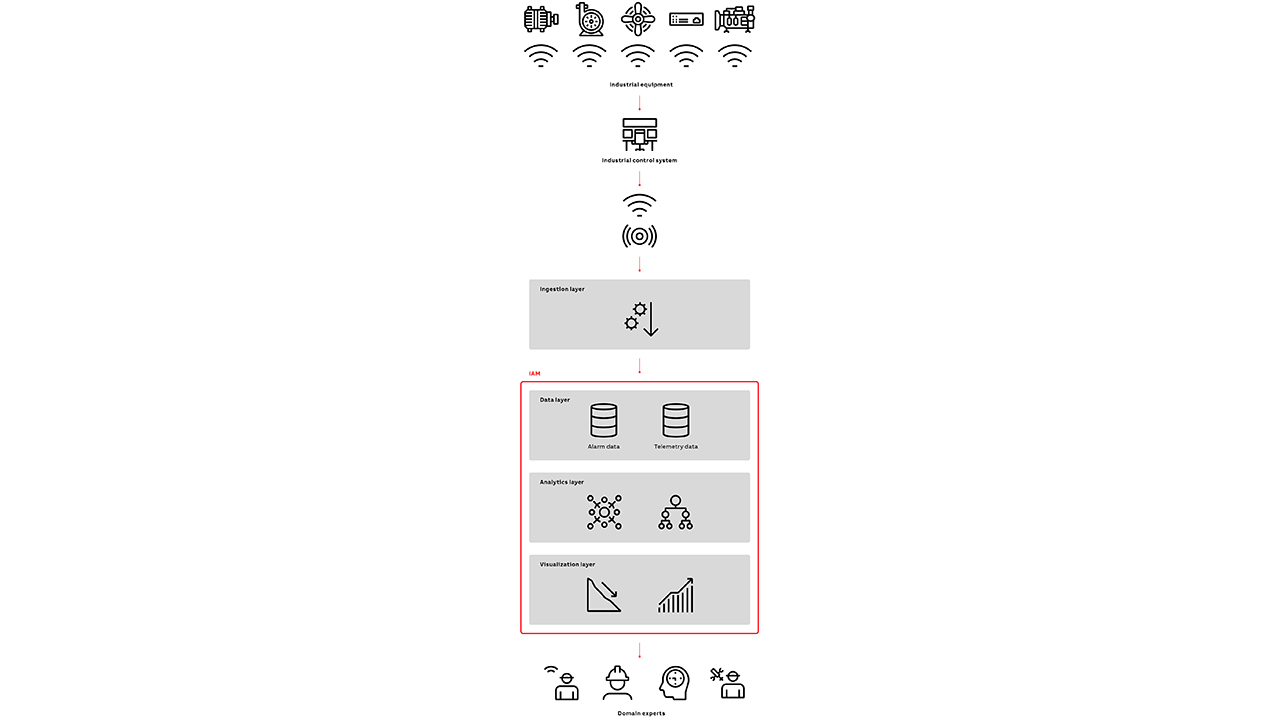
Alarms in control systems and their management
Fundamentally, alarms alert the operator to departures from normal operating conditions. To be effective, operators must quickly and accurately assess those alarms that need split-second attention and action. However, conventional systems are static; the alarms don’t respond to changes in mode of operation or conditions. When a large compressor shuts down in a petrochemicals plant, many resulting alarms are noncritical and secondary; superfluous and annoying, these alarms require the operator to waste time searching and analyzing. ABB’s IAM can remedy such problems. The dynamic system filters events and alarms based on the actual current plant operating conditions, thereby clearing the path for operators to swiftly recognize and address the significant alarms.
To accomplish this, the IAM conducts an array of five analyses: deep alarm de-chattering, alarm sequence analysis, critical alarm analysis, masking rules, and alarm flood analysis. All of these methods rely on data mining techniques to identify data patterns.
IAM development
Developed with historical data from oil and gas process plants among others, analysis relies on concepts such as basketization, a process that slices data into appropriate time intervals; and metrics, which enables results to be prioritized.
Image currently unavailable
Image currently unavailable
Image currently unavailable
Image currently unavailable
Image currently unavailable
Image currently unavailable
03a An example of a critical alarm basket created around a specific critical alarm, C; this is used to identify alarm sequences that occur before and after this specific event. Here, four backward and forward baskets were created for the critical alarm C of length t. 03b An example of time slice basketization created with ABB’s newly developed sequence mining algorithm is shown. The algorithm creates three equal time baskets and each basket contains the alarms that are recorded in the alarm log: These are ordered according to time stamps (the time when each alarm was activated).
03 Basketization (time baskets) is important for alarm sequence and critical alarm analyses. Different types of baskets are needed for each type of analysis.
Basketization is used either to store repeating or short duration alarms in the case of chattering alarms, to divide alarm sequences into equal time periods as with alarm sequence analysis, and to identify alarm sequences that occur before or after a specific event as in critical alarm analysis →03. Alarm lifetime – the time between the return to normal Rtnt and the activation time of an alarm Actt – and the time gaps between alarms (TG) – the time between the activation of one alarm and a second later occurring alarm (TGB-A = ActtB – ActtA) are determined by data attributes →04; these are used for the de-chattering analysis of alarm logs by applying two newly developed algorithms: one algorithm is for the life of an alarm and its frequency of repeatability; the other is for the repetitive alarms: those in which the time gap between activation and return to normal is short. The analyst performs the de-chattering analysis first and then can decide to remove these from the alarm log if appropriate.
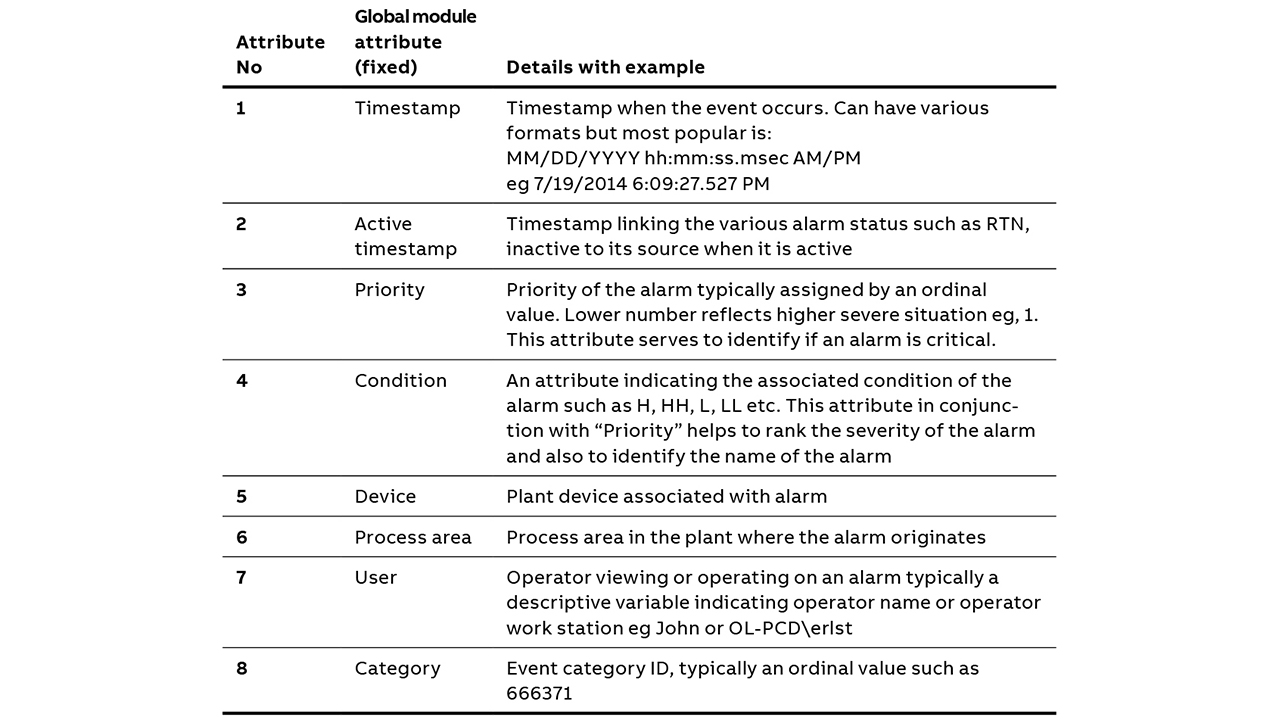
The sequence model analysis
After de-chattering the alarm log, the IAM uses the activations times of historical alarm data to identify and characterize alarms that occur frequently together. Using two measures of significance: support and togetherness, alarm sequences can be ranked according to importance [1]. The algorithm creates four equal time baskets of a specific duration: each basket contains the alarms in the log – ordered according to activation time. The sequence mining algorithm identifies closed sequences of alarms with support – the proportion of observations in the data set that contain the specifically defined item set [1]. Togetherness is then used to rank the sets of closed sequences according to accepted procedures [1].
Critical alarm analysis
Every operator and manager in a process plant not only tries to solve critical events immediately, they try to avoid tripping events at all costs. The IAM facilitates this process by identifying those alarms that occur frequently, before or after a critical alarm (often listed for tracking purposes). Relying on alarm activation times in the historical alarm log, and forward and backward analysis over a specific timespan (usually 60 minutes), the model identifies sequences of alarms around critical alarms. Each event is associated with a level of severity that determines event criticality.
More analysis, better functionality
In addition to de-chattering, sequence, and critical alarm analytic models, ABB employed masking rules analysis and alarm flood analysis to provide operators with better functionality. The masking rules method is used to determine if the lifespan of an alarm is contained within that of another alarm; this suggests whether the contained alarm is redundant or not. As the name states, alarm flood analysis identifies waves of alarms that may occur following certain plant operations: shut-down of equipment for preventive maintenance or cleaning purposes, etc. If no new alarms ensue, then these alarm floods might be “normal” and require no further action from an operator.
Visualizing alarms to boost usability
Following the extensive testing of the analytical models with data from the oil and gas industry, a major contributor to the development of alarm systems, ABB considered a variety of display visualizations concepts. After all, the operator should know what needs to be done and how much time is available to do it. Targeted visualizations reduce the operator load, enable better event predictions and improve alarm system configurations. [2]. Along the way, some well-known challenges surfaced: limited space and too much data on the screen; and color confusion. By developing concepts simultaneously to represent alarm analysis, allow for data filtering and grouping of visualizations: conventional list view →05a, sunburst diagrams →05b, and parallel coordinates →05b; criteria such as practicality, readability, and grouping efficacy was evaluated and the best views for specific analysis types were developed [2].
Image currently unavailable
Image currently unavailable
Image currently unavailable
Image currently unavailable
Image currently unavailable
Image currently unavailable
05a A prototype of the UI: a list view for critical event analysis is shown on the right side while a parallel coordinates filter is displayed on the left side. 05b The sunburst visualization display includes the sunburst (right side) and the parallel coordinates filter (left side): the bigger the sunburst segment, the greater is the number of sequences that start with the alarm in question. The size of the circle segment represents the amount of alarms. The bigger the segment the more alarms of this name appear. Detailed information about the sequences that contain the hierarchy that has been selected is obtained by mouse-hovering.
05 The GUI views were chosen to enable maximal readability and usability.
ABB’s alarm portfolio and vision
The IAM system has been productized and is currently being incorporated into the ABB Ability™ Symphony® Plus software [3]. Basically, to perform alarm analysis, historical data is imported into the IAM as text files of various formats; data is transformed with the help of a mapping file, either created or imported, to a global alarm model (GLAM), which gives the least common multiple of historical alarm data and provides for storage →06. The software currently defines 10 different alarm aspects; however, up to 52 different individual aspects can be set depending on the needs of the customer.
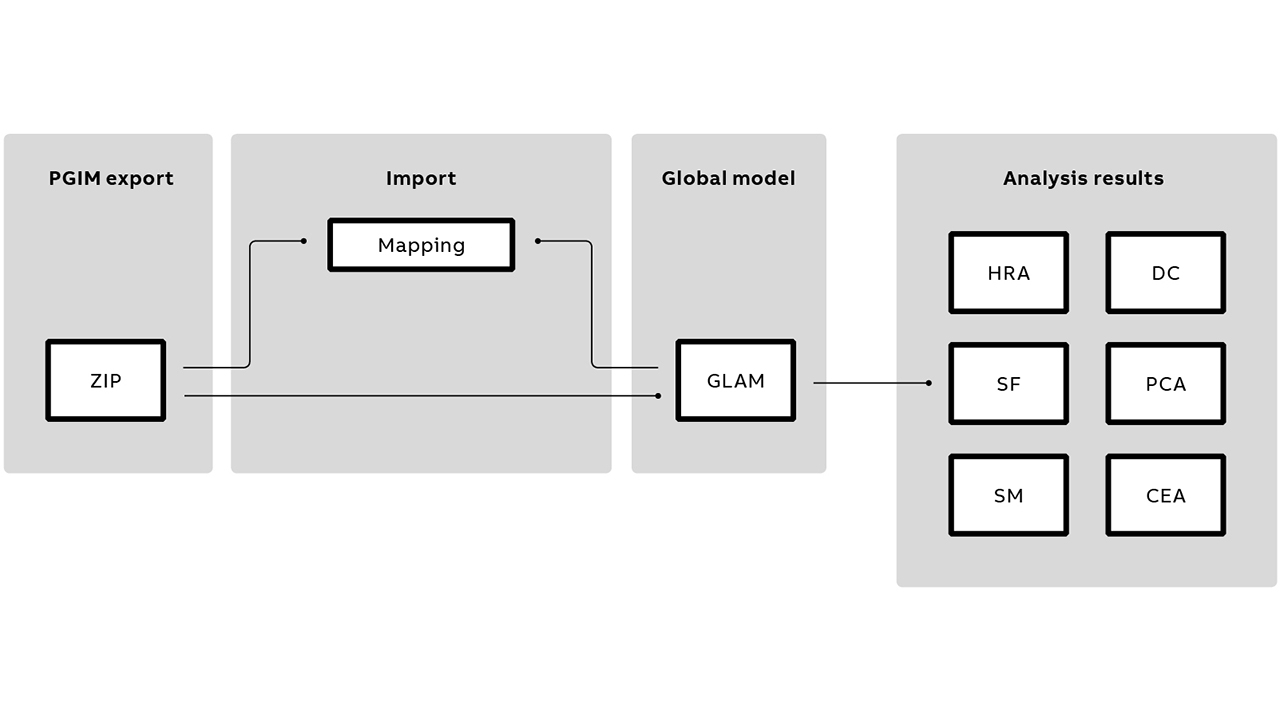
The new system, ABB’s AlarmInsight® and Safetyinsight™, has been designed to help achieve safe and reliable operations in the process automation industry throughout the lifecycle of a plant and covers the initial engineering phase and the subsequent operational phase.
The engineering phase relies on digitalized engineering data for tools to document hazards, define appropriate barriers, and design the “instrumented” safety and alarm system. The second, or operational phase, relies on contextualized operational data (IT/OT). This serves to assist with monitoring alarm and safety system performance; transforming data into actionable insights to enable informed decision making.
The use of advanced alarm analysis takes the “guesswork” out of alarm rationalization. The deep-learning gained from analysis can be incorporated back into the engineering tools and used to optimize or maintain the automation and safety systems. ABB’s holistic process completes the alarm lifecycle management support.
ABB’s vision for alarm management is derived from the company’s extended involvement with, and demonstrated commitment to, standards like EEMUA 191 and ISA SP 18.2 that address the importance of a robust alarm management capability in process plants, and their vast experience with power generation plants. Each alarm should alert, inform and guide; alarms should be presented at a rate that operators can deal with, detectable problems should be alarmed as early as possible, and the cost/benefit of alarm engineering should be reasonable. The Ability® Symphony™ Plus HMI, S+ Operations, implements ABB’s newest IAM technologies to make this vision a reality.
ABB’s intelligent alarm system consists of two critical yet distinguishable parts that cannot be separated: the technical optimization of the alarm system and the optimization of the human machine interface. This approach to alarm development not only leads operators to greater awareness, faster response times, and better decisions, it provides process industries with the potential for prediction. ABB’s Symphony Plus HMI, S+ Operations with IAM has abilities that are leaps-and-bounds beyond the descriptive capabilities of currently available alarm management systems.
Acknowledgements
Special thanks are extended to the original IAM team members: Jinendra Gugaliya, Marcel Dix, Veronika Domova, and Mithun Acharya for their valuable contribution to the IAM project. Also, Roland Weiss and Alf Isaksson are thanked for their support as program research managers during the project.
References
[1] A. Dagnino, “Data Mining Methods to Analyze Alarm Logs in IoT Processes”, in IEEE 15th International Conference on Automation Science and Engineering, August 22-26, Vancouver, Canada, 2019, pp. 1-14.
[2] V. Domova, “Intelligent Alarms Management: Sequences analysis visualization: Guided report on implementation”. ABB Internal Report, 2018, pp. 1-37.
[3] ABB Ability™ Symphony ® Plus, “Intelligent Alarm Management Technical Preview 1: Release Notes in Power Generation & Water”, ABB Internal Report, 2018, pp. 1-57.