The challenge
Dhp Technology needed a high precision automation solution for its innovative folding solar panel installation which would be the first of its kind in Switzerland.
The solution
The IRB 6700-150 robot by ABB automates the process of joining two layers of solar panels together with great precision and speed. Control and materials handling technology from ABB subsidiary B&R ensures the reliability of the automation process.
The application
Precise placement of solar panel components using robotic automation.
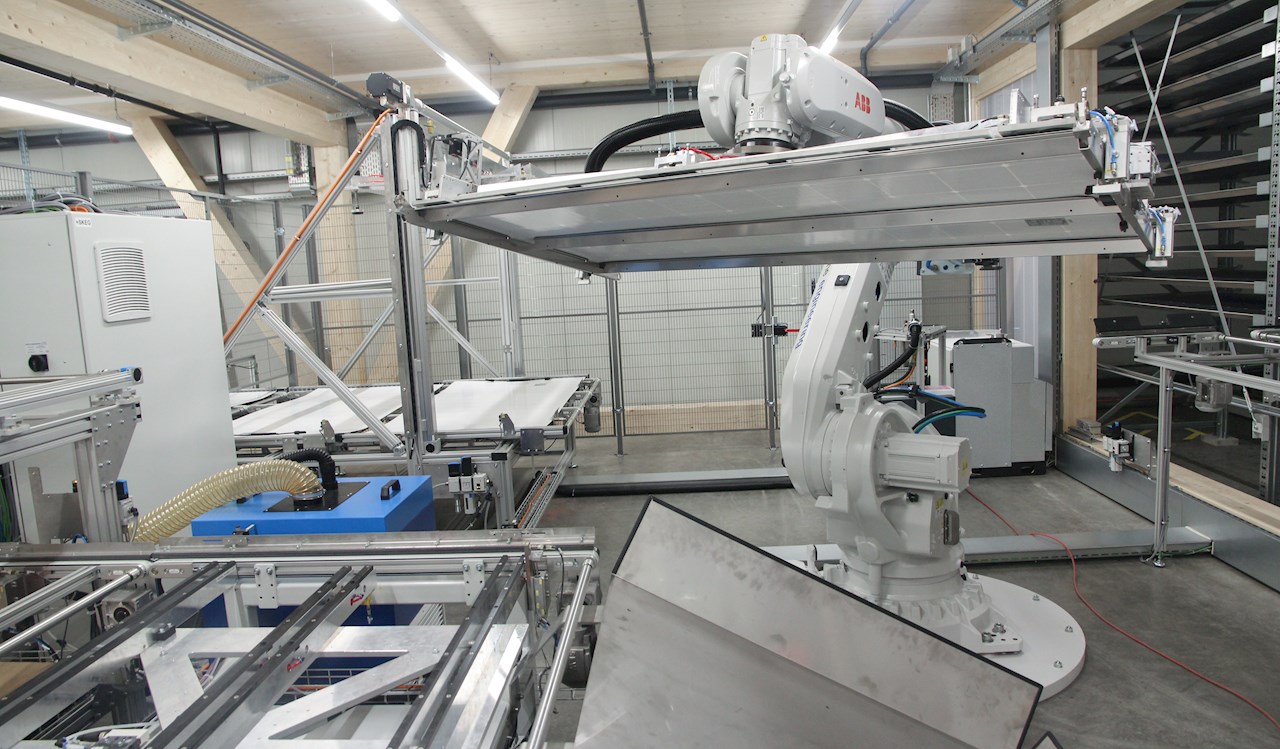
Solar energy plays a decisive role in energy transformation. In Switzerland it has far more potential than wind energy. But, where in our crowded country could enough photovoltaic plants be installed in order to lead the use of solar power out of its current shadowy existence? Solar power constitutes just three percent of the electricity mix generated in the country, presenting an opportunity for innovation.
And that is exactly what Grisons-based dhp Technology set out to do.
While installing solar power systems on rooftops and façades have been explored widely, it is hardly feasible amid Switzerland’s dwindling open spaces. So dhp decided to utilize existing industrial spaces that it could convert into solar power production sites without causing any disruptions.
One of these spaces are clarifying tanks of the waste-water treatment plants (ARA). Over 800 clarifying tanks are installed across Switzerland and being major energy consumers themselves, meant that installing solar power panels over them could be an ideal solution to unburden the power grid. However, installing a permanent solar power system above the clarifying tanks was not feasible as they needed to be accessible by crane systems.
"This is where our patented idea came into play - a folding solar roof with cable technology in lightweight construction", says Gian Andri Diem, a co-founder and managing partner of dhp.
The modules of this solar folding roof, named "Horizon", retract into a storm-proof garage, and back out again at the press of a button. They also automatically take cover if a storm, hail, or heavy snowfall approaches. In order to keep the weight as low as possible, new, glass-free photovoltaic panels were used.
The pilot system was installed at the beginning of 2017 by utility company IBC Energie Wasser Chur and dhp technology above clarifying tanks of the ARA at their main location in Grisons. When fully expanded the solar power panel system covers roughly the same area of a soccer field. This generates 550,000 kWh of solar power every year, which would be sibe equal to the consumption of nearly 120 homes. In this case about 20 percent of the energy is consumed by the ARA itself. The successful pilot project went on to win many awards and soon orders started to pour in.
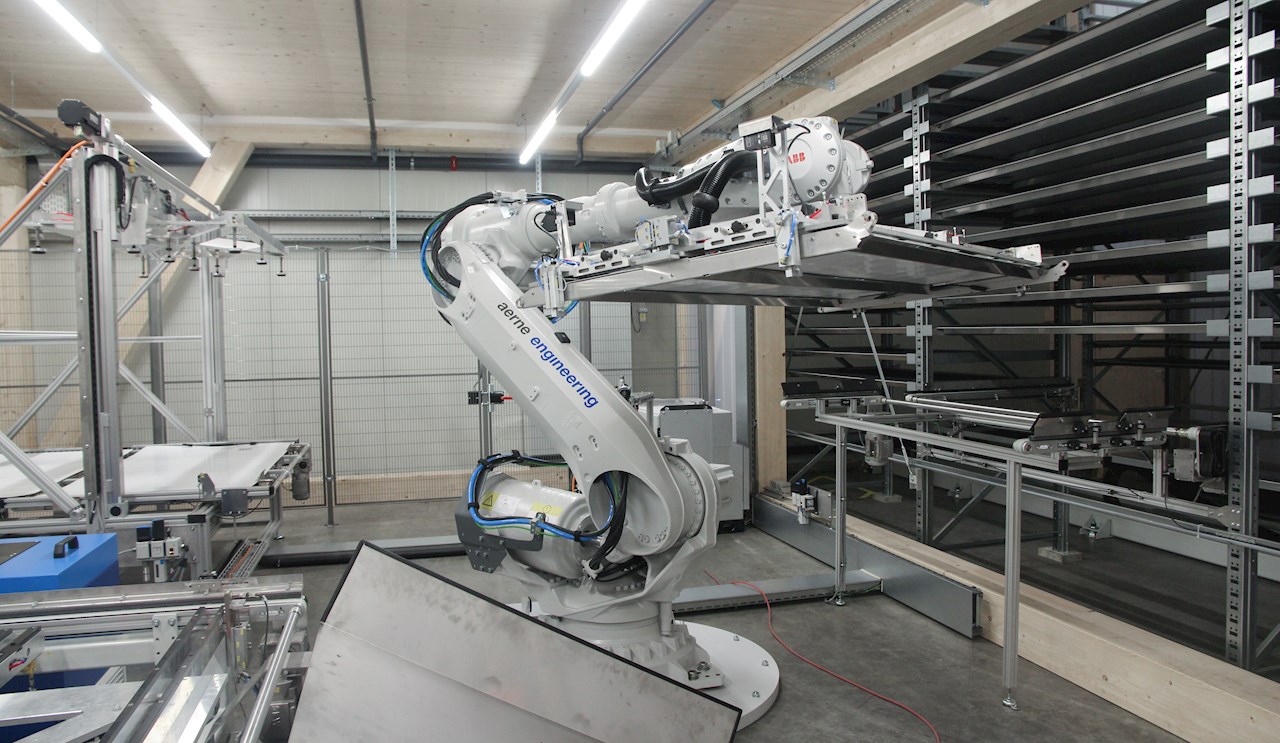
The next step
“It was clear that we wanted to set up series production close to our area to allow our experts to work on the further development of the system, Andreas Hügli, founder and managing partner of dhp technology said. Dhp found a suitable factory building in Zizers near Landquart and collaborated with Aerne Engineering for the design and set up of the production facility.
At the heart of the system is a fully automated production of individual folding solar roof elements in which the photovoltaic modules are glued to the frame. This task is carried out by an IRB 6700-150 robot by ABB. With a reach of 3.2 meters, a load capacity of 150 kg and above all, its high level of precision. The IRB 6700-150 robot is the ideal fit for the job, said Swen Fürer, Director of Sales at Aerne Engineering.
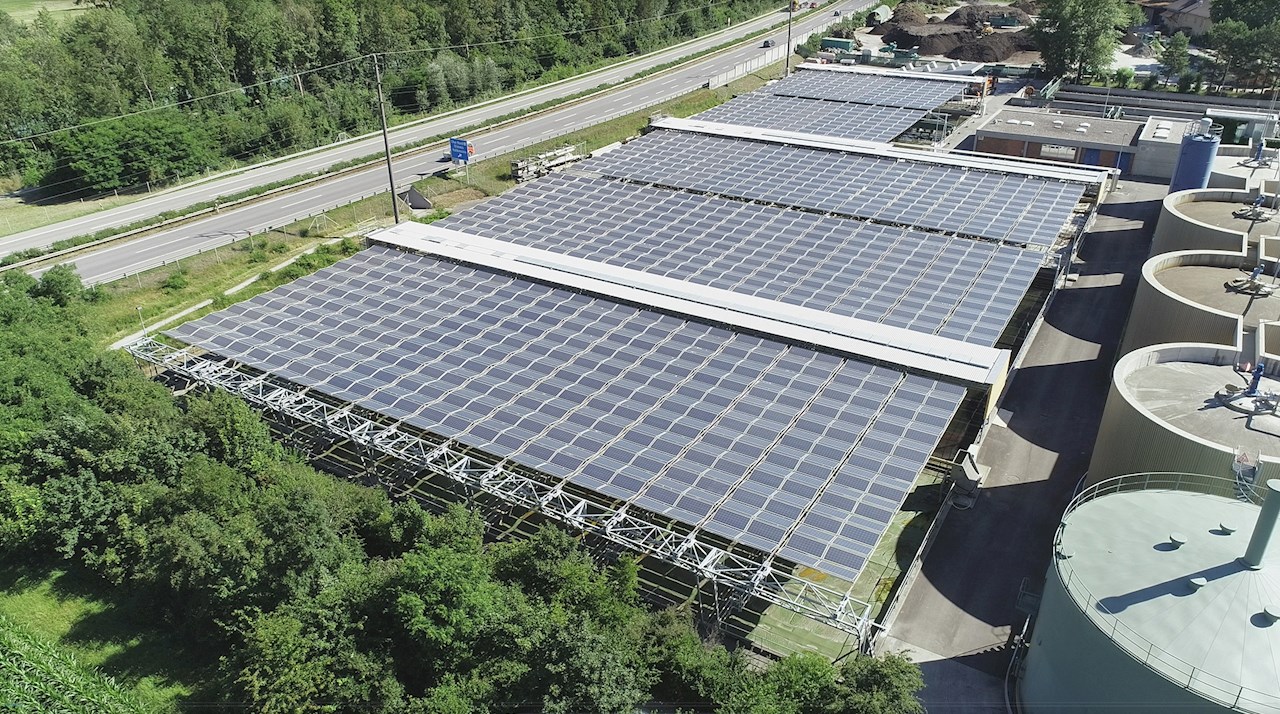
The automation process
The robot picks up a photovoltaic panel using its suction cups and guides the intended adhesive surface with the utmost visually controlled accuracy using a plasma beam in order to significantly increase the bonding strength of the adhesive. Then it presses the panel onto the chrome steel frame which is also automatically pre-treated with plasma and upon whose contact surface the adhesive was applied. Finally, the robot places the glued element into an automated high-bay warehouse where it hardens for eight hours. This adhesive cycle takes around at 160 seconds.
Aerne Engineering used control and conveyor technology including programmable controls, drives and regulators from B&R, a subsidiary of ABB, for the steps to prepare the frame, the solar panel and the control of the whole production cell.
The modules are then attached to assemblies by workers in order to keep the installation work at the final location as low as possible. The manual assembly component of the drive technology was already completed in advance with the towing rope deflection from the cable technology.
"While we received a great deal of specifications, we were also met with openness to define risks together, to proceed on a case by case basis via trial & error in order to implement this complex new system,” said Silas Bühler, Senior Project Manager at Aerne Engineering. Particularly delicate processes such as the plasma pre-treatment were first constructed and tested at Aerne Engineering. The incorporation of the robot could be simulated in advance using the innovative RobotStudio software from ABB.
The serial production in Zizers was put into operation by dhp in September 2019. "The ABB-Robot fully lives up to its expectations as does the integration with the B&R control technology", said Fabian Vogelbacher, Director of Production at dhp.
Meanwhile an initial contract for a solar folding roof over a car park was received from energy company St. Gallisch Appenzellischen Kraftwerke AG (SAK). It will be installed in the spring of 2020 on the car park for the Jakobsbad-Kronberg cableway – marking another milestone for the innovative yet sustainable use of existing infrastructure to promote clean solar energy to power the future of Switzerland.