Linde’s air gas factory in Kilpilahti, located in Porvoo, Finland, produces nitrogen, oxygen, and argon 24/7, save for a short annual service break. The Kilpilahti factory also supplies liquefied medical oxygen to hospitals around the country. The main product of the factory is gaseous nitrogen, and tens of millions of cubic meters of this gas is delivered every year to customers in the Kilpilahti industrial area.
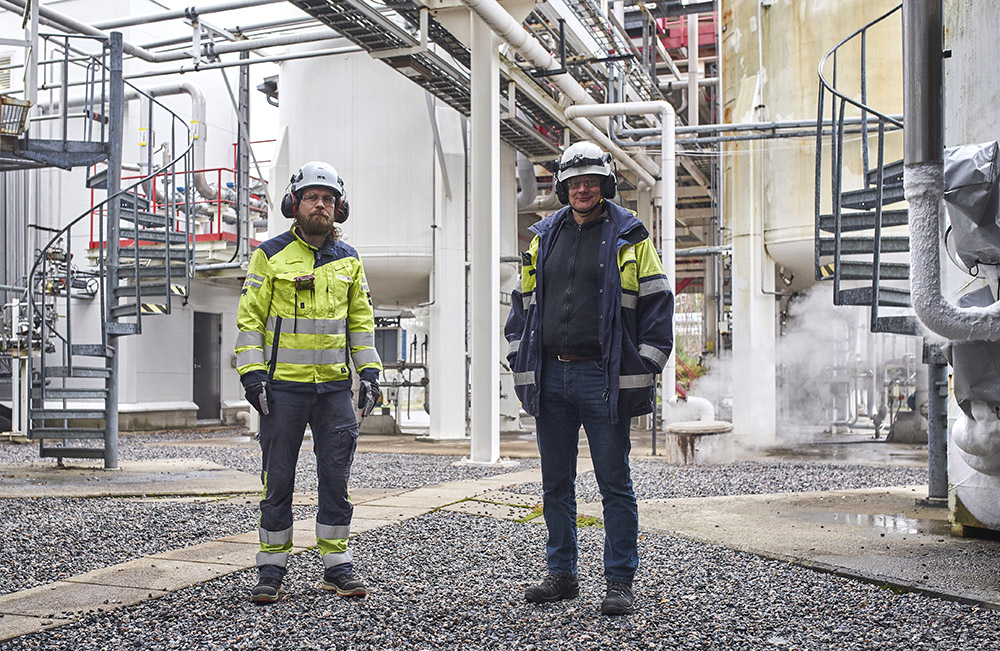
Two years ago, it became clear that the I/O cards that control the factory’s valves and pumps and send measurement data to the control room had to be replaced. “They had been in operation for 30 years and were at the end of their life cycle,” says Linde’s automation engineer Jarmo Turtio.
There were several options: the most expensive one was to update the entire automation system, including the hardware and the software. Another option was to update the lowest level of the automation system and replace all the original components from the 1980s.
Nitrogen and oxygen around the clock
“Due to the nature of our operations, the automation update of the factory was very time-critical. We only had ten days to complete the update,” Jarmo Turtio says. After careful consideration, Linde decided to have all the original parts, i.e. nearly all the factory’s I/O cards and old automation centers, replaced. “The plan we prepared with ABB indicated that this would be the best way to guarantee a successful update.”
“All the analog and digital I/O cards in the factory were replaced, which meant 1,912 I/O points in total,” describes ABB’s project manager Jarkko Räikkönen.
The project group consisted of representatives of Linde, ABB, and Bilfinger, which was in charge of the installation work. Since the service break would only last ten days, the group opted for a creative solution. The new automation centers were located in a new place inside Linde’s factory hall, and they were fitted with new I/O cards in advance. In addition, new cables were installed for the old automation centers, so that they would be ready when the service break started.
Image currently unavailable
Image currently unavailable
Image currently unavailable
Image currently unavailable
Image currently unavailable
Image currently unavailable
Image currently unavailable
Image currently unavailable
Image currently unavailable
Image currently unavailable
Image currently unavailable
Image currently unavailable
Image currently unavailable
Image currently unavailable
Image currently unavailable
ABB’s new automation centers ensure the continuous operation of the plant. All the analog and digital I/O cards in the factory were replaced, which meant the replacement of 1,912 I/O points. In order to disassemble the old I/O cards and establish connections to the terminal blocks linked to the new centers, thousands of wires had to be reconnected. ABB’s duplicate power units ensure uninterrupted power supply to the new automation centers. Preparations in production were started months before the service break. Preparations for the automation system update were made with the help of circuit diagram plans of the factory. ABB created a “digital twin” of the existing system, which could be used to test all the changes and additions in advance.
Careful preparation crucial for success
While it was not necessary to reprogram the entire factory, Turtio was concerned about the changes to be made to the automation software. His concerns were dissolved when the new centers and their wiring could be tested in advance with the help of ABB’s Advant testing system. “We could test the software side already during the summer, long before the factory was shut down,” Turtio says.
ABB created a “digital twin” of the existing system, which could be used to test all the changes and additions in advance. This advance testing can also be carried out while the factory is in operation. In addition, the control room software was updated as part of the project. This was completed well in advance, because 800xA updates can be done while the factory is running.
In production, preparations were started months before the service break. “We have two large liquid nitrogen storage tanks,” Turtio says. They were both filled to the brim in September 2019 when the factory was shut down. At the same time, ABB’s hardware engineer updated the factory’s circuit diagram plans and reviewed them with Bilfinger’s installation team. “Everything was scheduled very carefully, all the disassemblies and connections,” ABB’s Räikkönen describes.
September 23, 2019 was the project’s D-Day, and the factory was shut down. Despite the careful planning, there was no way round the arduous and time-consuming task of reconnecting thousands of wires in order to disassemble the old I/O cards and establish connections to the terminal blocks linked to the new centers. Räikkönen and his hardware engineer colleague were on permanent standby or present at the factory, monitoring the installation work. Any problems were resolved immediately. “We also removed old circuits that were no longer in use. There were no mistakes,” says Jarkko Räikkönen.
The service break was scheduled to last ten days. The work was completed in seven days.
A new boost from a perfect performance
“It was a first-rate performance,” says Jarmo Turtio praising the project. “We sat down a few times with our colleagues from ABB and Bilfinger to plan this. And everything went just as we planned—only faster!”
Turtio gives a simple explanation for why the project was a perfect success: “We had the chance to do all the difficult parts in advance.” And this is exactly what they did. When the actual service break started, the risk of errors had been reduced to a minimum. The functionality of the software and wiring had been ensured through testing, and only the new terminal block connections were yet to be tested.
The automation in Linde’s air gas factory is now in top condition. Now that the parts that posed a risk have been replaced, the plant’s reliability has been restored to a high level. “For some of the old I/O cards, there were no longer spare parts available. If one of them had broken down, the shutdown period might have been much longer. The old automation cabinets were also full of old electronic components. Those have also been replaced,” Turtio describes.
According to Turtio, the next time Linde must consider updates will be in six to seven years’ time when the control room might need to be updated. However, the factory’s existing automation hardware will last longer than that. “ABB guarantees 15 more years of support for it.” Therefore, the automation of the more than 30-year-old factory has many more years of life ahead.
The modernized factory has now been in operation for a year without problems. “If I think of the factory as a whole, this was absolutely the best possible solution at this moment. And everything has worked as it should.”
Image currently unavailable
Image currently unavailable
Image currently unavailable
Image currently unavailable
Image currently unavailable
Image currently unavailable
Linde’s automation solution was given at least 15 more years of life thanks to a factory automation update implemented in cooperation with ABB, completed in only seven days. “It was a first-rate performance,” says Linde’s automation engineer Jarmo Turtio. The chemical industry center in Kilpilahti, the largest in the Nordic countries, relies on an uninterrupted supply of gas from Linde. In 2020, the company formerly known in Finland as AGA changed its name to Linde, but it has been part of a leading international industrial gas company already since 2000.

The service life of industrial automation is counted in decades
Oy Linde Gas Ab’s (formerly AGA) automation system
1989 AGA’s air gas factory in Kilpilahti is started up with ABB’s Advant factory automation.
2004 The automation control system is updated to ABB’s 800xA.
2018 AGA enters into an agreement with ABB to update the automation system in Kilpilahti.
April 2019 Four new automation centers with I/O cards are delivered to Linde.
Summer 2019 Trunk cables are built between the new centers and the old ones in production, the new centers are connected, terminal block fields are built for the old centers to enable cross-connection, all the cables and software are tested in advance. The control room’s 800xA software is updated from version 5 to version 6.
September 2019 During the ten-day service break, the I/O cards of the old centers are disassembled and the field devices behind them are connected to the terminal blocks linked to the new centers. This work is completed in seven days, and the gas factory is restarted earlier than planned.
2034 The availability of spare parts for the updated system is guaranteed for the next 15 years.

Text: Petja Partanen
Photographs: Olli Urpela