The ABB Ability™ Smart Sensors are installed across three plants in Singapore operated by Japanese chemical giant, Denka, as part of a service agreement signed with ABB in 2018. Under the service agreement, ABB manages equipment failure risk and conducts or advises on preventive maintenance and repairs using a reliability index and urgency level. If a motor develops a fault, it is repaired at an ABB workshop. If repair is not an option, ABB will replace the motor.
On Singapore’s Jurong Island, Denka operates one of the world’s largest styrenic resin production chains. Here hundreds of motors, from 0.75 kilowatt (kW) to 160 kW, operate pumps, compressors, blowers and pelletizers. Hundreds of Smart Sensors enable ABB to provide Denka with continuous monitoring of the operating and health parameters of process-critical motors, pumps and bearings, to keep production running 24/7.
The sensors reduce the hours spent manually checking performance and gathering data while bringing new insight into the operating performance of the assets. A manual inspection would previously be carried out at three-month intervals. The trends that indicate a potential risk would be missed, with the possibility of catastrophic failure, a long downtime and expensive loss of production.
The Smart Sensors proved their worth after only a few days in operation when one detected a higher than normal vibration in a motor on a feed roller. ABB’s engineers, who were monitoring the motors, alerted the Denka maintenance team. Upon inspection they found a heavy build-up of sticky polymer and were able to clean it before it damaged the motor.
In another instance, a sensor picked up an abnormal temperature increase caused by an absorbent pad stuck on the fan cover, which obstructed the motor’s cooling.
Similarly, a bearing started performing abnormally. It was regreased and the condition improved with a slight increase of levels within the alert range but was still monitored closely. Two months later, the bearing started crossing the alarm zone continuously, and it was replaced during the next scheduled maintenance shutdown before it could cause any problems.
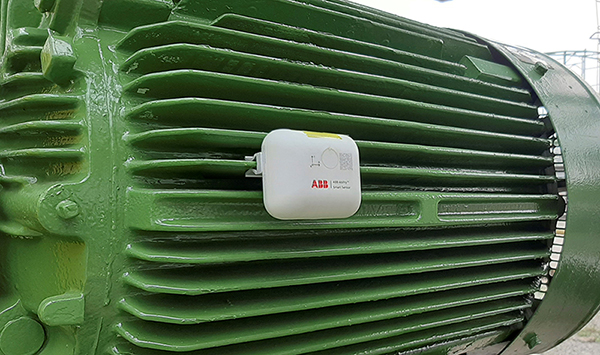
As part of the service agreement, Denka is embracing ABB’s newest Smart Sensor for hazardous areas. The new high-performance sensor carries ATEX, IECEx and NEC 500 certifications and features an extended battery life and a robust sealed-for-life design. It has an IP66/67 rating and can withstand high levels of vibration, corrosion and physical impact.
Denka has approved the installation of bearing and motor sensors in hazardous areas at its Merbau plant, a production base for carbon black. For the Tuas plant, which produces fused silica filler, Denka has ordered motor, bearing and pump sensors, with the motors being fully covered by ABB’s service agreement.
H.C. Ng, Denka Singapore’s Plant Maintenance Manager, says: “Many of our process-critical motors are exposed to harsh operating conditions that can result in premature failure, causing costly downtime. Denka was an early adopter of the Internet of Things (IoT), and we wanted a plug-and-play solution that could perform condition monitoring of our critical motors and bearings with little to no involvement from our workforce.”
“The Smart Sensors are proven to extend our motor lifetime, save energy and reduce maintenance costs. Combined with the support of the service agreement, they enable our maintenance engineers to focus on other critical tasks. The project has been an overwhelming success, both for Denka and ABB.”