Having experienced the versatility, ease of use & programming of the robot, father & son Zeo and Stefano Asioli, who are also Owner & General Manager, at Azeta Zeo Asioli Diffusion, decided to purchase two more units to support the first robot in everyday work, with a clear objective; to improve production efficiencies allowing the company to continue its growth trajectory and keep focusing on innovation and customisation.
Summary
The challenge
Azeta offers its customers a high level of customisation. For this reason the needs within the production line are constantly changing. The company needed highly customisable automation solutions able to provide support whilst adapting quickly to the changing demands.
The solution
A small robot customisable both in terms of programming and functionality that once inserted into the production line, becomes a pillar of support increasing its overall efficiency.
Usage
Precision assembly of mechanical parts according to programming instructions, which relieves employees from repetitive and tedious tasks as well as eliminating associated ergonomic risks.
A solid past laying the foundations for a bright future
Azeta was founded in Correggio in 1967 from the initiative of Zeo Asioli and in its history of more than 50 years has become a leading metal components manufacturer within the hydraulics field. “We strive to develop bespoke custom-made products for our customers” explains Stefano. “We don’t offer pre-packaged prices, but we work with their research and development team to design pieces that meet their needs”. This customer-led focus has defined the Azeta story and has allowed the company to grow over the years, with the opening of new plants, expansion of their targeted markets and the development of products for Chinese industry.
“The mechanics sector is mature” says Stefano. “It’s not easy to come out with new products that stand out from the competition, which is why we have worked on other levers within the market to be able to position our offer as that of a partner, not just a supplier, who continually looks to improve our efficiencies and drive costs down. With this in mind we decided to invest in robotics back in 1990”.
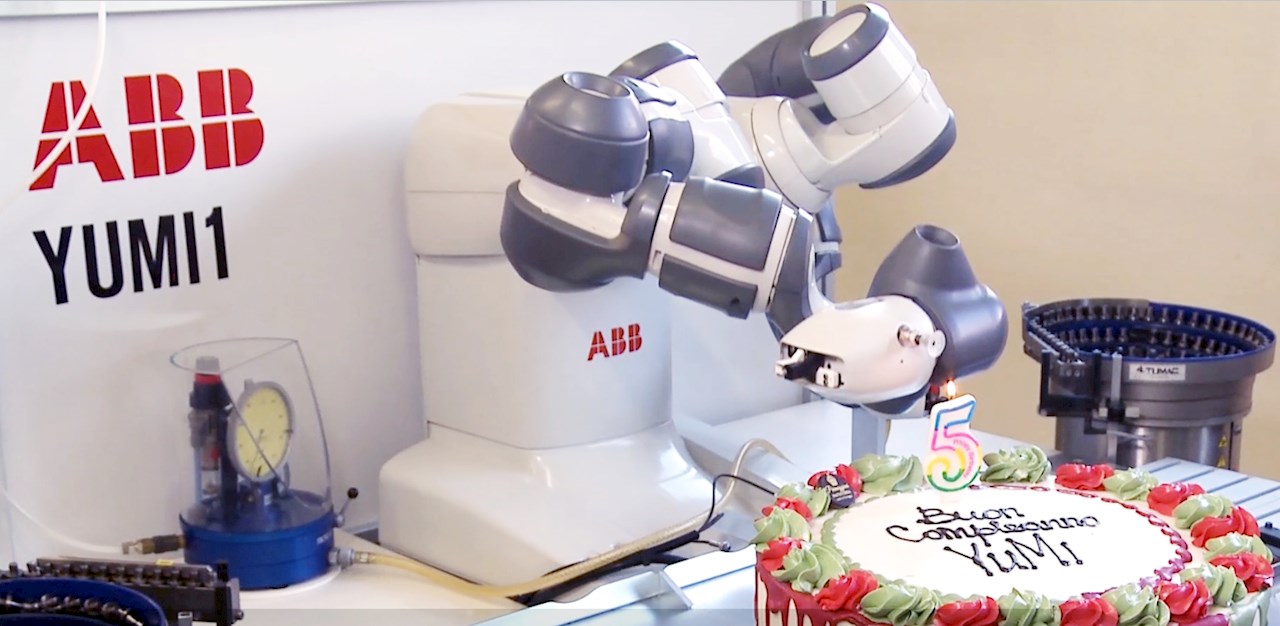
ABB as a partner for growth
Collaboration between Azeta and ABB goes back 20 years with the first purchase of an IRB 140 robot taken to replace another machine. “We chose to make a technological leap forward by choosing an ABB machine that offered numerous improvements including an advanced anti-collision system, which was very important for our type of work” comments Stefano. Over the years a second robot was added to the first IRB 140: “They are robots that really last the distance; both are still in use today” continues Stefano.
In 2015, the partnership was further consolidated with the purchase of YuMi, the first of the collaborative robot range sold in Italy. “As soon as it arrived we presented it to all our workforce, who were all extremely curious” says Stefano. “We were able to experiment extensively with Yumi thanks to the ease of programming the robot which drove us to use it in many different aspects of our work”. The introduction of Yumi into the Azeta production line was a real success, so much so that the company decided to invest in two further machines a couple of years later.
Durability, versatility, ease of programming – How YuMi won hearts at Azeta
When Azeta chose to automate parts of their production they found themselves with a choice of two paths to take: choosing a robot of compact dimensions that would allow an agile integration between man and machine, or the construction of a complex automation system that would have required a much larger floorspace. The first option was the natural choice: “YuMi allowed us to solve the problem of floorspace, taking up relatively little space and allowing people to interact with the robot easily. Other machines have fences and require a lot of management time to keep them operating” explains Stefano.
But it wasn’t only the floorspace savings which won hearts at Azeta: “YuMi’s ease of use and versatility are its two real strengths” continues Stefano. The open-source comms with other protocols has allowed Azeta to interface YuMi with Industry 4.0 helping the company automate the collection of production data to inform and improve performance and efficiency. “Programming YuMi is so easy” says Stefano, “we have a programmer in the company who was able to put the robot into operation without any trouble. More so the user-friendliness encouraged us to not hold back with our imagination and we then went on to programme it to perform functions that we hadn’t even considered possible when we bought it”.
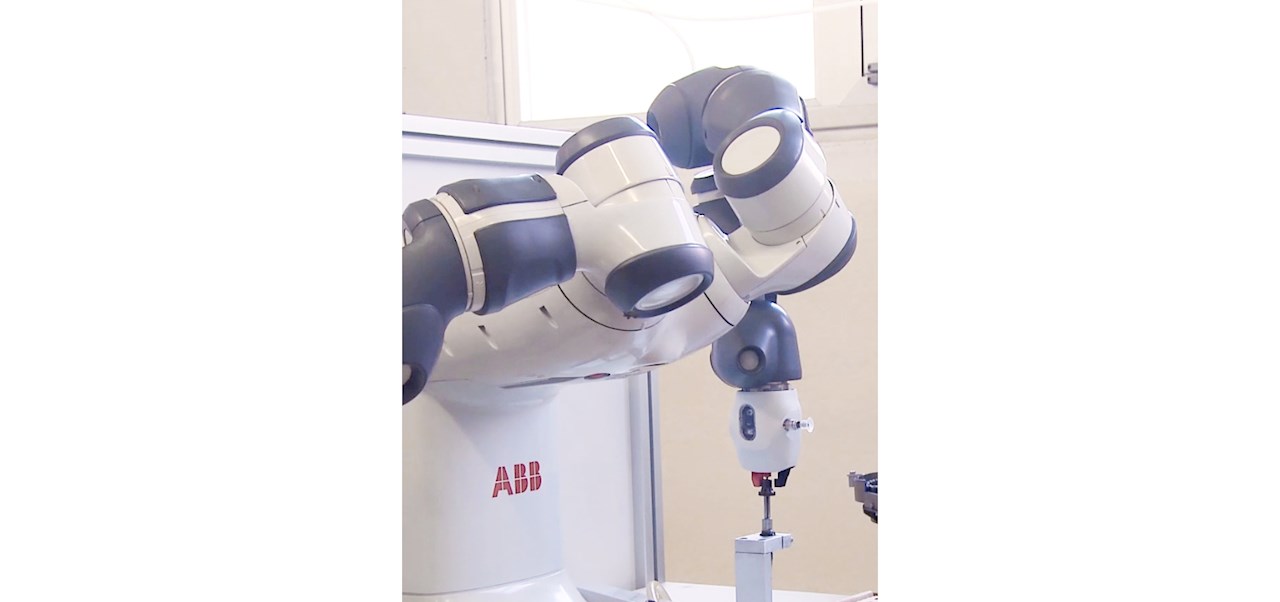
A valuable colleague, a tireless collaborator
The initial apprehension amongst some of Azeta’s workforce when YuMi arrived also didn’t last for long. The robot was up and running in a short space of time, relieving its human colleagues from some of the most boring, repetitive jobs, allowing them the potential to grow within the company and contribute even more of their know-how to Azeta’s successes. “Our employees understood YuMi’s role in the company and quickly appreciated it and were even asking us to buy more of them” explains Stefano
YuMi is also well recognised for its distinctive features making it a very precise instrument. Thanks to YuMi, Azeta has managed to eliminate or significantly reduce the OCRA (Occupational Repetitive Actions) Index on many workstations along the production line. The index is the ratio between the number of daily actions performed using the upper limbs in repetitive tasks and the recommended number of actions. “Safety at work has always been a priority for us and we adopt rules and guidelines that are stricter than those set out by national legislation” continues Stefano, “YuMi is also in line with our commitment to safeguard the health of our employees”.
“Never before have people been able to get so much added value from a machine. YuMi has combined people and technology increasing their overall potential making us all the more ready for new challenges” concludes Stefano.