ABB is enhancing its collaborative robot family with a new industrial cobot which combines enhanced collaborative safety measures and ease of use with the speed, robustness and precision of an industrial robot.
Based on ABB’s class-leading IRB 1100 industrial robot, which offers best in class speed and accuracy, the CRB (Collaborative Robot) 1100 SWIFTI combines a payload of 4 kg and reach of up to 580mm with the benefits of safe collaborative operation and ease of use. This will open new possibilities for enhanced productivity in a wide range of applications, from manufacturing to logistics and beyond, and enable more businesses to embrace automation.
SWIFTI offers a maximum Tool Center Point (TCP) speed of more than five meters per second, which is more than five times higher than other cobots in its class and comparable with industrial robots.
Designed to support intermittent collaboration between human and robot, SWIFTI can move at high speed for maximum productivity, without jeopardizing safety when a human worker needs to approach the cobot.
SWIFTI is aimed at tasks including assembly and polishing where human operators need to be present to carry out duties such as supervision and repositioning of parts. Such applications have traditionally used extensive physical safety measures such as fencing to minimize the risk of people coming into contact with robots moving at high speeds, increasing the cost and size of the installation, and disrupting line speed and productivity as the robots have to be stopped so a human can enter the workspace.
Integrating a safety laser scanner with ABB’s SafeMove Collaborative safety software, SWIFTI ensures that contact between a moving robot and a human will not occur, thus preventing injury. Working together, the technologies allow safe collaboration to be achieved without the need for physical fencing, by ensuring that an operator is not present within the robot’s working envelope while it is moving.
If an operator is detected within SWIFTI’s working area, the cobot’s movements will automatically slow down or stop completely to allow the operator to approach safely. As the worker moves away, the cobot will restart, returning to full speed and movement for full productivity once it senses that its working envelope is completely clear. As an added safeguard, SWIFTI also features an interaction status light that provides a visual indication of the cobot’s status when the operator is in the cobot’s workspace.
Image currently unavailable
Image currently unavailable
Image currently unavailable
Image currently unavailable
Image currently unavailable
Image currently unavailable
Image currently unavailable
Image currently unavailable
Image currently unavailable
Image currently unavailable
Image currently unavailable
Image currently unavailable
Image currently unavailable
Image currently unavailable
Image currently unavailable
“By enabling safe collaborative operation at higher speeds with its speed and separation monitoring, SWIFTI bridges the gap between collaborative and industrial robots,” said Andie Zhang, Global Product Manager, Collaborative Robotics for ABB Robotics. “By utilizing the expanded capabilities offered by next-generation cobots like SWIFTI, companies will be able to transform their productivity by automating repetitive, mundane and dangerous processes, while leaving employees free to perform more rewarding activities.”
Another aspect of SWIFTI’s collaborative design is its ease of use and installation. The robot’s safe working zones can be set using SafeMove’s easy-to-use fast setup tools, including the SafeMove Configurator App on the ABB FlexPendant.
When it comes to programming the robot itself, SWIFTI offers users a choice of both lead-through programming via a clip-on lead through programming device, and ABB’s new Wizard easy programming software. Based on simple graphical blocks, Wizard Easy Programming makes it easy for non-specialists to automate their applications. The blocks represent actions such as ‘move to location’, ‘pick up an object’, and ‘repeat movements’, making it easy and intuitive to build a series of simple processes for the robot to perform. There are also functions for error handling, allowing novice programmers to resolve errors such as collisions.
Removing the need for operators to learn complex programming languages, these features greatly reduce the time, effort and scope for error that have deterred many companies, especially SMEs, from investing in robotic automation.
Every ABB cobot installation includes a start-up package that provides ABB Ability™ condition monitoring & diagnostics as well as a support hotline free for the first six months to access ABB’s expert technical assistance, which is offering support across all industry segments.
SWIFTI, and the new GoFa™ CRB 15000 cobot, will both be available from February 24 2021, and together they are the next generation of cobots from ABB, joining YuMi® and Single Arm YuMi® to create an industry-leading cobot portfolio for applications ranging from less than 0.5 to 5kg.
Key features CRB 1100
- 4kg payload and 475mm or 580mm reach.
- Fast performance – industrial robot speed of up to 5 meters per second (the exact safe collaborative speed may be lower, as it will depend on the specific application, tooling, payload etc. Users can refer to the SafeMove Configurator App for a recommendation. Users should always carry out a risk assessment of their application).
- Accuracy / position repeatability of 10 microns.
- Small footprint, lightweight manipulator and ability to mount in any direction.
- Powered by OmniCore™ controller and FlexPendant.
- Four integrated air supplies.
- ISO flange for easy mounting of tooling.
- Cobot label and white/gray color scheme to differentiate CRB 1100 and IRB 1100.
- Safety laser scanner and SafeMove Collaborative software (a safety PLC may be required for connection with the laser scanner)
- Interaction status light to communicate cobot status
- SafeMove Configurator App on the ABB FlexPendant.
- Safety certified PL d Cat 3.
- IP40 protection.
- Ease of use: quick calibration and configuration.
- Ease of use: Wizard Easy Programming.
- Ease of use: Clip-on lead-through programming device.
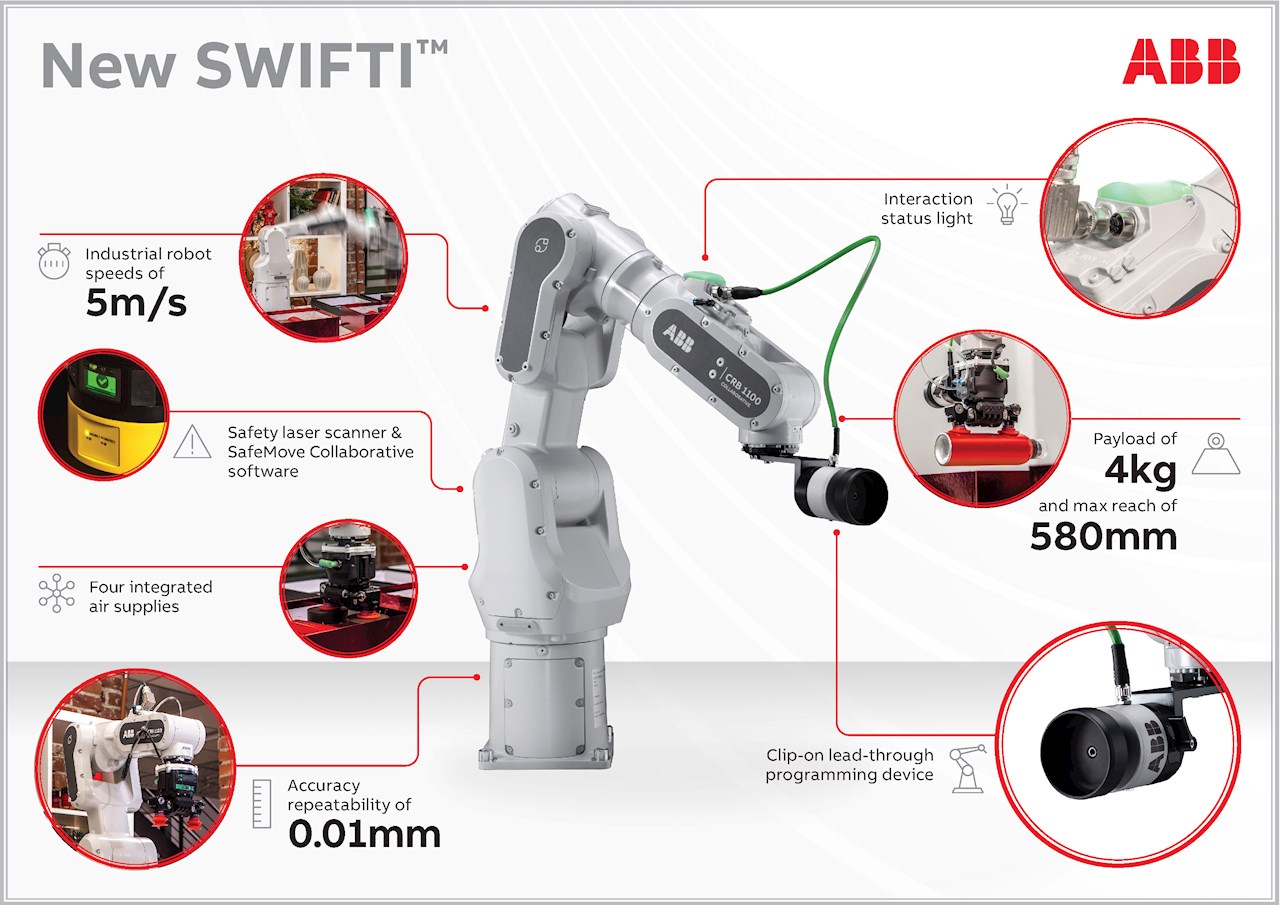
1. Design and engineering
SWIFTI has been specifically designed to close the gap between collaborative and industrial robots, enabling fully safe collaborative operation to be achieved in applications demanding industrial performance in terms of speed, accuracy and robustness.
“Combining the capabilities of a collaborative robot with the higher speed, accuracy and robustness of an industrial robot helps to address many of the barriers that have prevented many companies from fully realizing the potential benefits of robotic automation,” said Andie Zhang. “By coupling the safety features and ease of use and installation of a collaborative robot with the high speed, precision, performance and compact design of the IRB 1100 industrial robot, SWIFTI provides the best of both worlds. With collaborative safety and high speed and accuracy on a par with an industrial robot, it will help companies transform their productivity by enabling greater co-operation between their robotic and human workers across a wide range of applications.”
Using the same platform as ABB’s class-leading IRB 1100 industrial robot, SWIFTI provides the ideal solution for applications including loading and unloading or assembly where workers intermittently need to operate in the same workspace as a robot, as well as kitting, material handling, and screwdriving to insertion and polishing tasks.
SWIFTI is designed to work with ABB’s OmniCore robot controller family. Offering high levels of flexibility, connectivity and performance, OmniCore features a 50 per cent reduction in footprint compared with previous robot controllers, together with best-in-class motion control and path accuracy. OmniCore can be easily integrated with the latest digital production technologies, including a wide variety of fieldbuses and advanced vision systems.
SWIFTI’s exterior design stands out, with the same distinctive white and gray color scheme as ABB’s other new collaborative robots, as well as ABB’s new collaborative robot signifier icon, which features a stylized depiction of a robot and human hand working together.
2. Speed and performance
As the collaborative version of the IRB 1100 industrial robot, SWIFTI offers the same class leading speed and repeatability. Moving at up to five meters per second, SWIFTI is more than five times faster than other 4kg payload collaborative robots, enabling users to combine the benefits of collaborative operation and greatly enhanced productivity with a single robot.
With a best-in-class repeatability of 10 microns that exceeds both other cobots and industrial robots, SWIFTI can be relied on to accurately pick, transfer and place payloads time after time.
This superior performance is achieved by the speed and safety separation concept outlined below, with human workers fully protected against the risk of accidental contact with the moving robot by SWIFTI’s integrated safety measures.
Another benefit of SWIFTI’s speed and separation safety concept is the removal of the need for specialized collaborative tooling. As there is no potential for contact between human workers when SWIFTI is moving, it can be used with the same tooling as a standard IRB 1100 industrial robot, presenting scope for potential cost savings and removing the need to hold two separate sets of tooling. An example is the inclusion of a vacuum pack, which features four integrated air supplies that can be used to enable simultaneous picking of multiple items using suction. Normally used on ABB’s IRB 1100 industrial robots, the same vacuum pack can be fitted to SWIFTI to offer the same functionality with no need for any modifications.
3. Safe by design
SWIFTI combines the proven performance of ABB’s SafeMove safety certified robot safety software, which is integrated directly into the cobot controller, with a safety laser scanner, to create a speed and separation safety concept, where the goal is to avoid any contact between human and robot that could potentially result in injury.
This enables safe collaboration at higher speeds and payloads without the need for containment measures such as fences. This makes SWIFTI ideally suited for applications characterized by intermittent collaboration, with infrequent sharing of the workspace.
Using a ‘green, yellow, red’ zone approach, the robot reacts according to which zone a human worker is in. If the worker is detected in the green zone, then the robot will carry on working at its full speed and range of movement. If the yellow zone is entered, the robot restricts its movement and speed to a safe limit. Entry into the red zone will bring the robot to a complete halt, allowing the worker to safely approach the robot to perform a task such as loading or unloading.
The robot will remain stopped until the red zone is cleared and will only return to full movement and speed once the worker is back in the green safety zone.
SWIFTI’s design also includes an interaction status light that allows users to easily see the status of the robot, with the light changing color from green to yellow to red according to the proximity of the user.
“As well as helping to reduce the overall cost of an installation through reduced spending on additional safety measures such as fences, being able to remove physical separation between people and robots saves space and makes for more open workspaces. This helps people operate and carry out their tasks freely, which minimizes potential disruption and interruption of production processes caused by having to stop the robot to allow operators to enter a cell to sort out issues in the event of a problem,” added Andie Zhang.
4. Ease of use
Every effort has been made to help make SWIFTI as easy to use as possible, with ABB’s latest easy programming technologies designed to remove the need for users to learn specialist programming skills.
Initially developed and launched in 2020 for ABB’s single-arm YuMi collaborative robot, ABB’s Wizard easy programming software can be used to set up SWIFTI in a matter of minutes. With Wizard, the programming process is reduced to simply dragging and dropping the required block on the screen of the ABB FlexPendant, with the user able to see the results immediately and adjust the cobot’s actions if required. By linking these blocks together, complete programs can be built for applications such as machine tending or assembly, with no need for any knowledge of robot programming languages.
“Reducing the time and complexity of programming robots is one of the key opportunity areas for driving the growth of robotic automation, especially at the SME level,” said Andie Zhang. “People have become accustomed to the easy user interfaces in smartphones and other consumer technology. Our Wizard Easy Programming tool uses this concept to take the effort out of programming industrial robots and brings us a significant step closer to enabling anyone and everyone to use robots.”
For companies with more specialized programming needs, new blocks can also be created to perform specific tasks. This is achieved through ABB’s Skill Creator software which is available for free for anyone to use to turn standard RAPID programming routines into Wizard blocks and make them ready for use by non-programmers. The custom blocks, known as skills, can be produced to control grippers or create actions for specific applications such as screwdriving and polishing.
Users can also program SWIFTI using lead-through programming. A clip-on lead-through device that can be attached to the robot’s end effector allows users to move the robot arm into the required positions, which can then be set using the FlexPendant. Once the positions have been set, the device can be removed and re-used to program other SWIFTI robots.
SWIFTI users will also be able to use RobotStudio®, ABB's simulation and offline programming software. This is the industry’s leading PC-based solution for programming, configuration and virtual commissioning before installation.
To help support SWIFTI, ABB has also created a series of online tutorials covering a range of topics, from set- up and programming through to operation and troubleshooting. Please click here for more information.
5. Cobot portfolio
The new SWIFTI cobot builds on the success of ABB’s YuMi family, which has been helping businesses safely automate key tasks since YuMi, the world’s first truly collaborative robot, was launched in 2015. ABB’s portfolio of collaborative robots now offers three different families – YuMi, GoFa and SWIFTI, with payload options ranging from less than 0.5kg to 5kg, to support the most diverse range of collaborative applications.
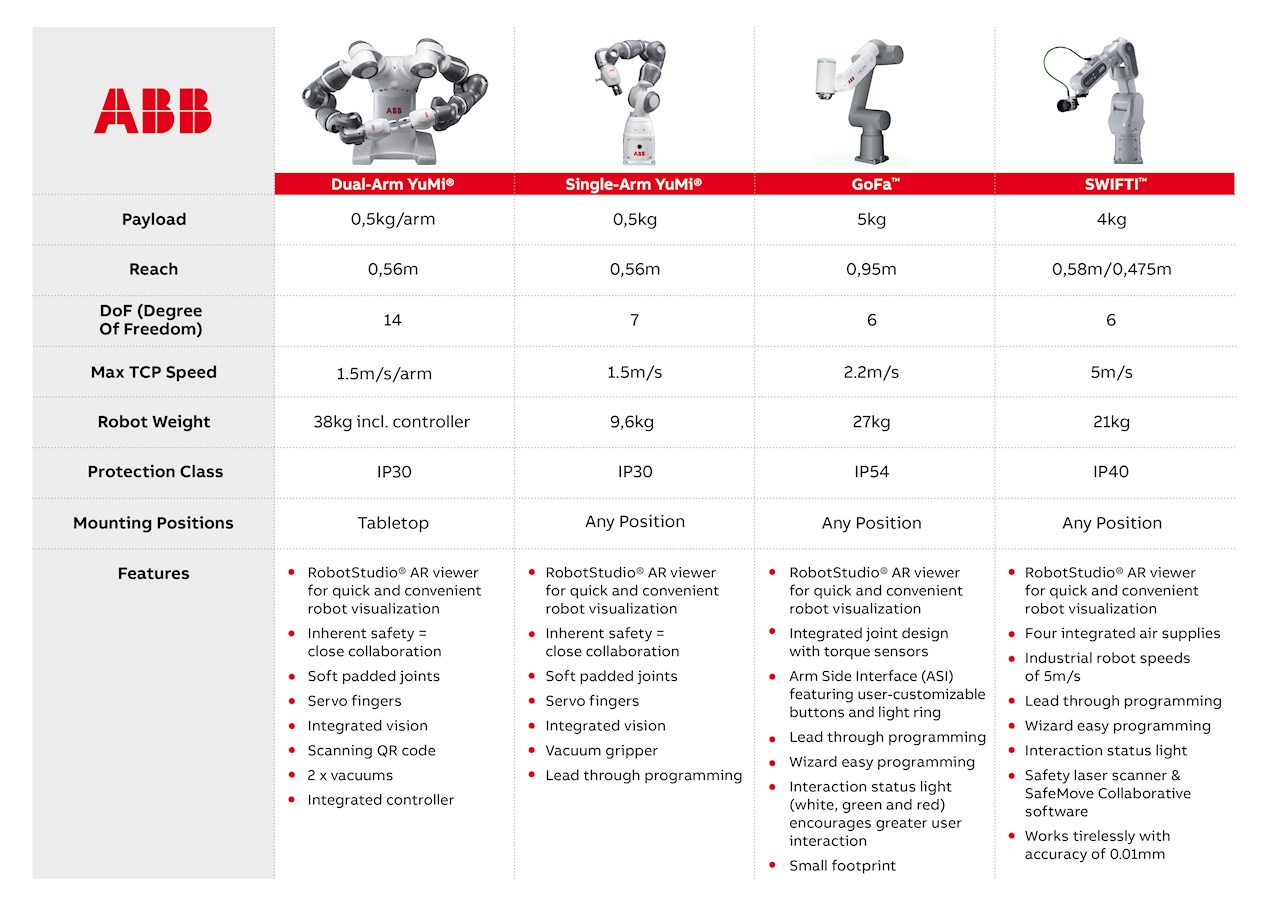