Eva Wadman, Jarl Sobel, Anders Eidenvall Industrial Automation Measurement & Analytics Västerås, Sweden, eva.k.wadman@se.abb.com, jarl.r.sobel@se.abb.com, anders.eidenvall@se.abb.com
Lightweight, strong, highly reflective and recyclable, aluminum is ideal for many consumer and industrial product applications. Its use can lower energy costs and reduce CO₂ emissions that are so crucial in today’s market [1]. It is no wonder that aluminum sheet metal is in high demand, eg, as packaging material and for can production; for transportation vehicles especially for body-in-white for cars, eg, Ford’s F-150 model, etc. [1]. For instance, the North American lightweight material market is estimated to grow dramatically between 2020 and 2025 with aluminum expected to capture the highest market share in terms of value [1]. However, achieving a specific aluminum end-product demands producers to control the chemical composition, work hardening and thermal history of aluminum, or alloy, and its thickness.
To this end, aluminum cold rolling mills require thickness gauging systems that are dependable, safe, robust, compact, and accurate; they must also operate in a harsh and spatially restricted environment. The capability of minimizing thickness deviations during the rolling process is critical. Although this may seem easy to achieve, it is actually dauntingly difficult.
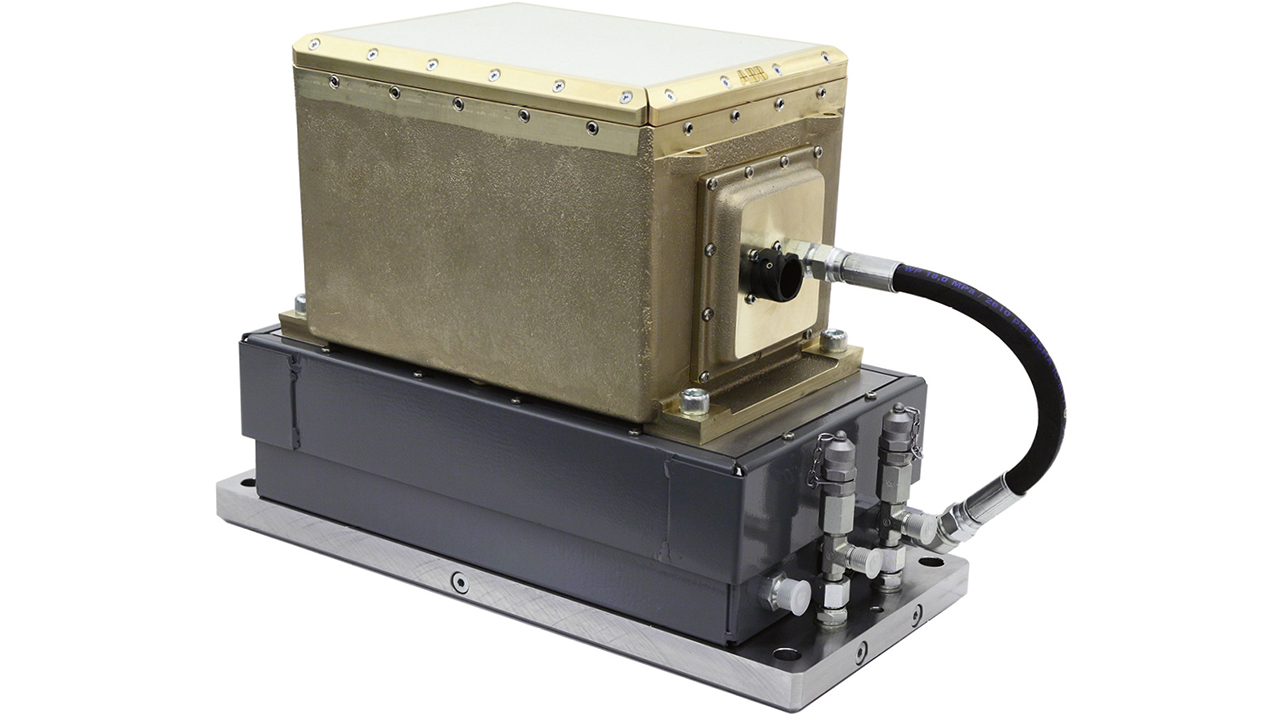
Committed to developing the best possible gauges for measurement and analysis, ABB has engineered the unique gapless MTG Box Gauge system →01 with Pulsed Eddy Current technology (PEC) →02 to determine both resistivity (between 27 nΩm and 65 nΩm) and true strip thicknesses (0.5 mm – 8 mm) for aluminum and clad aluminum [2]. Despite this amazing achievement, ABB continues to push the limits of thickness measurement. With the new High-pass Mode option that calculates thickness variations for thin aluminum strip (between 0.6 mm and 0.1 mm) customers will be able to measure fast thickness variations for use in feed forward control under specific conditions.
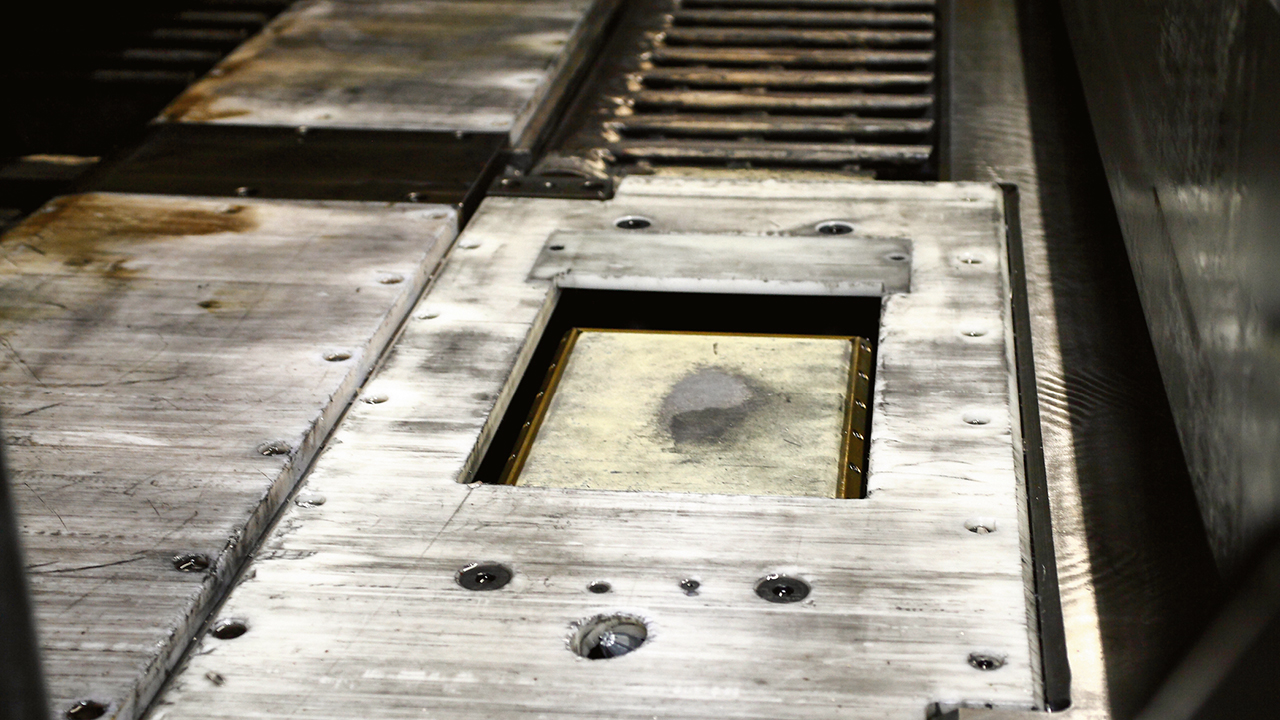
The rolling process and keeping thickness in-line
During rolling, metal is subjected to intense pressure and tension in a harsh environment (in the presence of dust, steam, emulsions or other fluids); shape and thickness are altered through rolling and stretching to reach the final size and thickness. As the metal is rolled, the speed increases to compensate for the change in thickness. Creating the right balance between the reduction due to the force of the mill and the reduction due to extruding the material through the gap is crucial; if the process is off-balance even slightly, the metal strip could break or cobble with disastrous results. Thus, thickness gauge systems must control thickness within tight tolerances while the material moves through at varying speeds; thereby ensuring maximal productivity and minimizing costs associated with non-conforming strip. In cold rolling mills, where aluminum sheet is produced to exacting thicknesses, and production continuing around the clock, tighter thickness tolerances can mean higher efficiency and access to additional markets. For instance, the high-volume production process used for deep drawing cans in the aluminum can market has extremely tight tolerances; producers require a strip thickness deviation of only a few μm for a strip thickness of 200 μm for the entire strip (lengthwise and widthwise).
ABB has developed the MTG, with PEC technology to measure true thickness with outstanding accuracy and dependability in this harsh and challenging mill environment →01.
MTG – gapless gauging for aluminum strip
With many competitive advantages over conventional radiation-based gauges for aluminum thickness measurements, the MTG family of gauges is gaining acceptance worldwide [2]:
• Robust and compact design
The aluminum-bronze gauge housing has superior chemical and mechanical properties that protect the gauge from the harsh mill conditions →01.
• Gapless
The gauge is gapless, with nothing above the pass line that can obstruct the strip passage →02. Consisting of one sensing element box, the MTG Box Gauge head can be installed below the mill table for protection during threading, tail out and strip breaks.
• Alloy independence
Amazingly, the PEC sensing technology measures true thickness independent of material composition →03 with no need for alloy compensation.
• Independent of mill environment
The gauge is insensitive to anything, eg, coolant, steam or dirt, except for the metal strip in the measuring zone and is therefore ideal for interstand applications.
• Tight thickness tolerances
Alloy chemical variations will not influence the alloy independent MTG gauge. The harsh environment (eg, lubricants) will not impact the measurements either. With an accuracy, in the mill, of +1.5 μm ±0.05 percent, metal strip producers can form the desired thickness at the tolerances demanded.
• Safe for humans and the environment
Because the MTG gauge does not rely on radiation-based technology, health and environmental concerns are eliminated. No restricted areas are required, nor is it necessary to dispose of radioactive waste.
• Infrequent and rapid calibration
The gauge arrives calibrated along with 12 calibration plates. Once in use, calibration is performed every six months and can be conducted in only 20 min. The calibration plates ensure that the gauge measures absolute thickness and thickness deviations according to traceable standards.
• Negligible costs for maintenance
Without fragile or aging components, radiation sources or detectors, high voltage transformers or precision mechanics, the MTG gauge is nearly maintenance-free.
• Increased mill production time
Gauge measurements are material-independent so there is less downtime due to reduced need for calibration and maintenance.
• Short and competitive return on investment (ROI)
By reducing mill downtime, non-conforming material, maintenance, need for spare parts, frequent calibration and security requirements for radiation-based technology, the MTG is a cost-effective alternative to radiation-based devices, with a short ROI.
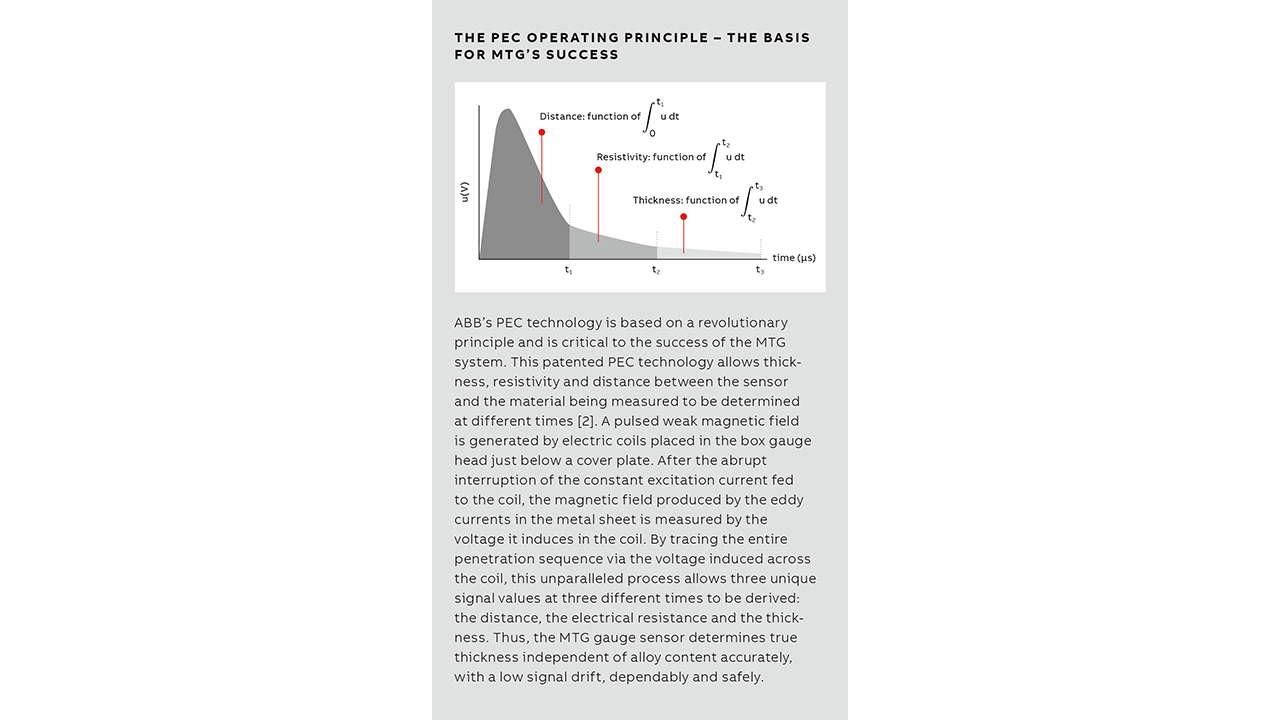
Stretching the limits
In operation for over 15 years, the MTG with PEC technology allows strip producers to meet tight tolerances and replace their X-ray and contact gauges to improve their competitiveness for standard aluminum strip production. But, what if the measured signals of the MTG gauge could be used to measure thickness of very thin standard metal strip (thicknesses as low as 0.1 mm)? Currently, radiation-based gauges, X-ray and Beta-gauges can measure in this range with high speed/low noise. The mechanical contact gauges and the MTG C-frame gauge, with a rather small gauge gap, can also measure accurately in this range but only at the strip edge; no center measurements are possible. Most significantly, the safety and environmental costs associated with radiation-based gauges and the impracticality of mechanical gauges make these methods disadvantageous for aluminum strip producers.
High-pass Mode
Always exploring ways to meet producer’s needs, in 2019, ABB’s researchers began investigating a MTG gauge function for thin strip aluminum measurement. Although absolute thickness cannot be directly measured for thin strip, ABB created an option that will, under specific conditions, determine thickness variations at high frequency (faster than 0.024 Hz), for thicknesses between 0.1 mm and 0.6 mm, and with a high signal-to-noise ratio: the High-pass Mode option [4]→04. Nonetheless, certain conditions must be met for the high pass filtered value of thickness to be calculated:
• Because persistent thickness changes that last more than 10 seconds will be zeroed, this function is only possible for use in feed forward control (interstand or entry side).
• The relative variation in resistivity of the material must be less than the relative variation of the thickness because in High-pass Mode conductance, which is the reciprocal of resistivity, reflects thickness →04.
• For the signal to indicate thickness variations accurately the nominal thickness must be close to the actual average thickness.
• Because only rapid thickness variations are measured, any slow variations will not be detected.
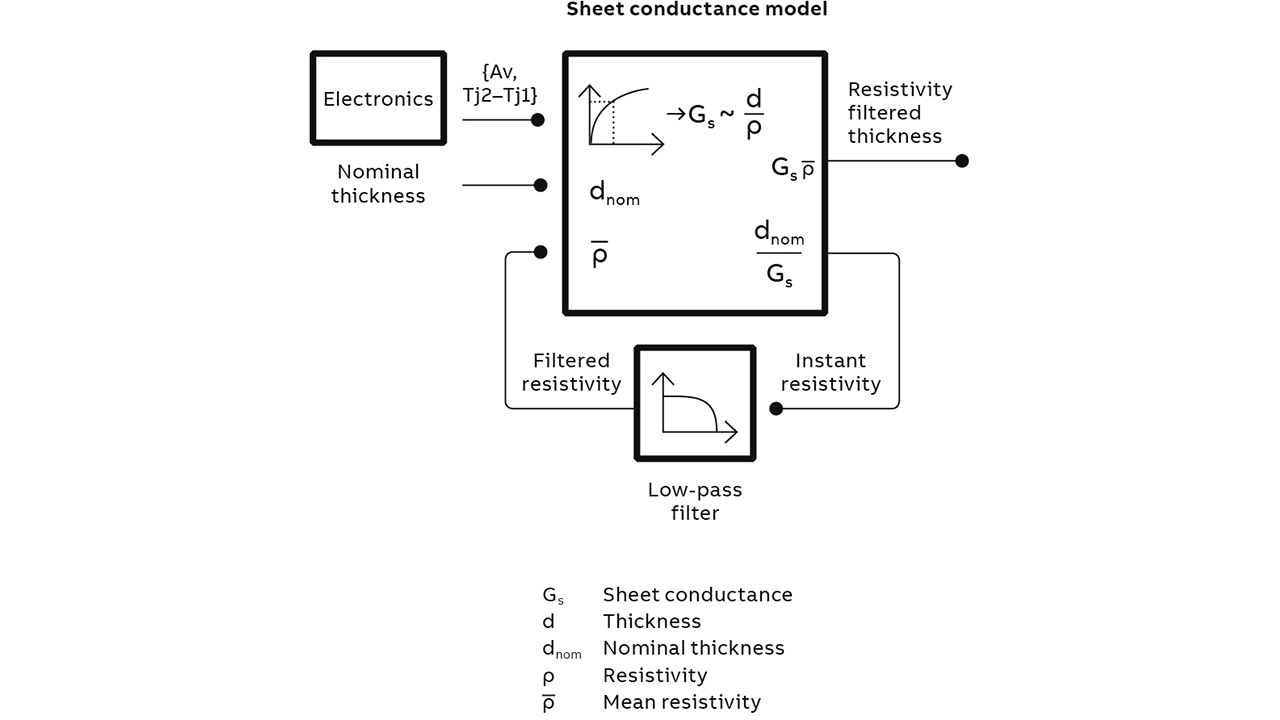
The path to thin strip measurements
ABB’s innovative High-pass Mode will provide customers with a practical measurement option for gapless gauge measurement of deviations in thickness of thin aluminum strip. The signals are insensitive to the environment eg, lubricant, dirt or other non-conductive materials. The sound theoretical basis and rigorous testing demonstrate that slight variations in alloy content have, in practice, a negligible effect on the measured thickness.
A comparison of ABB’s Box gauge thickness variations measured in normal operating mode with those of the High-pass Mode for a thickness of 490 μm was made →05. Although the MTG gauge measures true thickness independent of alloy composition, this becomes increasingly difficult as the strip becomes thinner due to the physics of electromagnetism. In this test case, the MTG gauge measures close to the lower limit of the method, which is slightly less than 0.5 mm, and therefore produces a measurement with greater fluctuations than comparable measurements generated by the High-pass Mode for a strip with a thickness of 490 μm →05a.
Image currently unavailable
Image currently unavailable
Image currently unavailable
Image currently unavailable
Image currently unavailable
Image currently unavailable
Image currently unavailable
Image currently unavailable
Image currently unavailable
05a The input thickness measurement of a cold rolled strip (for 10 s) with a nominal thickness of 490 μm (actual thickness is a few microns less than the nominal thickness) with output signals is shown. 05b The resistivity decrease (0.4 nΩm) leads to an erroneous increase in the thickness measured in High-pass Mode by 3.5 μm (0.7 percent). The High-pass Mode signal has been compensated for the difference in absolute magnitude in order to make the comparison easier. 05c The small resistivity change measured in High-pass Mode also affects an X-ray gauge used to measure strip thickness. The thickness measured by the ABB gauge in normal mode is alloy independent, but not in the High-pass Mode.
05 Results show the efficacy of the High-pass Mode in comparison with the MTG Box gauge and the X-ray gauge.
However, the High-pass Mode does not measure absolute thickness, its signal variations are centered around the nominal thickness of the strip being measured. Nonetheless, a close correlation exists between the thickness variations of the High-pass Mode and the normal MTG Box gauge output when the mean resistivity is filtered using a 10 s running average. Resistivity variations that are faster than 10 s will, however, contribute to a thickness deviation error in High-pass Mode. Here, a drop in resistivity lasting only 0.5 s was noted →05b. Such a decrease, 0.4 nΩm (0.7 percent), causes an erroneous increase in the thickness measured, 3.5 μm (0.7 percent), in High-pass Mode as theoretically expected →05b.
Comparison of the MTG gauge strip thickness measurements with measurements obtained from an X-ray gauge indicate that slight local changes in the alloy composition of the strip will also affect the X-ray gauge measurements →05c.
Such encouraging results not only corroborate the theoretical expectations, they demonstrate that ABB’s High-pass Mode filtered thickness variations are comparable to those obtained from the MTG gauge and X-ray methods as long as the specific conditions are met.
The MTG system – working together for dependability and accuracy
The MTG system (gauge head, control and operator unit, air regulator, hydraulics and the connection unit) have been designed for ease-of-use, optimal function, dependability, connectivity and integration ability →06 and can be connected to Automatic Gauge Control (AGC) systems in mills for feed forward, feedback and mass-flow control. With multiple integration interfaces, eg, Profibus-DP fieldbus communication, network communication via VIP, OPC DA, and Modbus TCP, an operation unit (to adjust set-ups, thickness value and status information), Human Machine Interface (to view thickness deviations as real-time data and trends), diagnostics part for error information, etc. and a service part (for calibration, manual control function, and service–based use case) the systems is flexible and operator friendly and efficient.
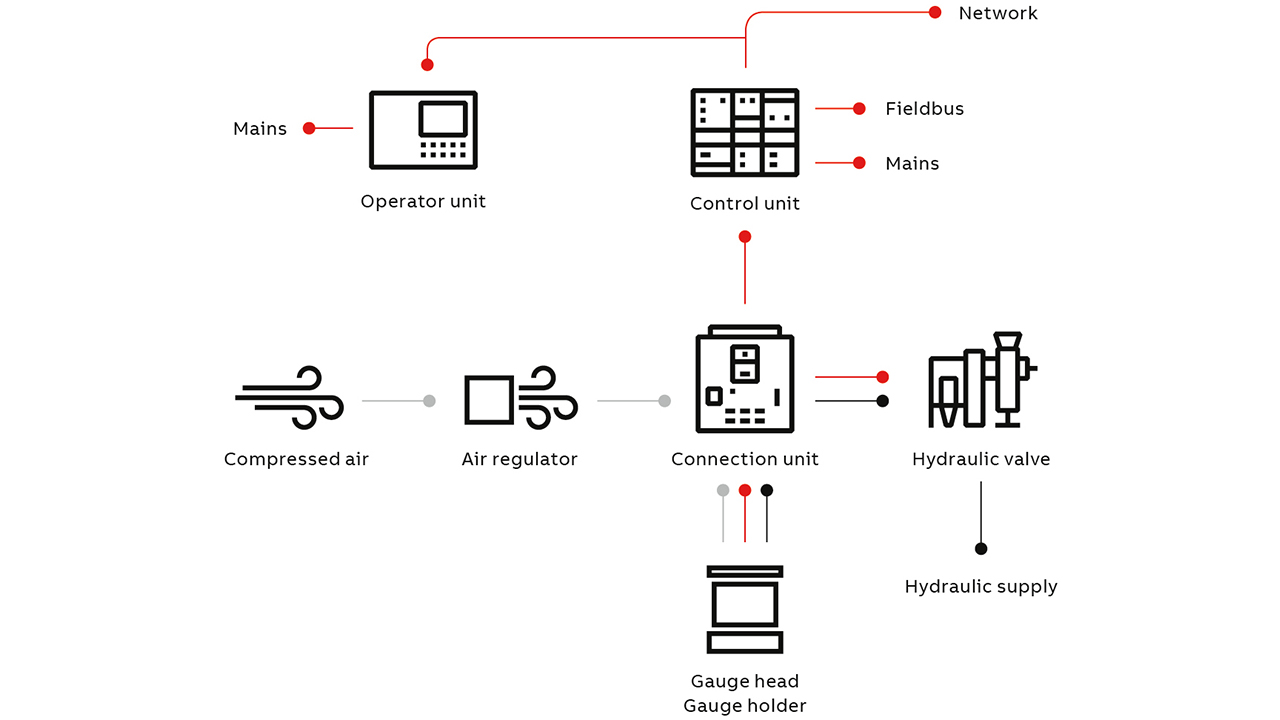
Mounted on a vertically moving frame, the gauge adjusts automatically to the right measuring distance via a hydraulic positioning system; rapid positioning allows measurements to be made almost instantaneously, when tension comes on. In this way the thickness-controlled strip length can be maximized. Changes in the distance caused by small changes in speed or tension are corrected for automatically.
The integration of system components and outstanding capabilities of each device and unit allows metal producers to attain specified thickness within tolerances 24/7, safely, with negligible costs for maintenance. The MTG system with the gapless gauge and PEC technology enables accurate true aluminum thickness measurements. The material independence, environmental and safety benefits, and quick commissioning time results in increased productivity and higher yields for standard metal strip producers in a sustainable process [2,4].
Thanks to ABB’s new High-pass Mode option, producers will soon be able to control thickness deviations of thin aluminum strip in feed forward control, thereby enabling aluminum producers to meet the ever-increasing tolerance requirements and access new markets.
References
[1] Market Watch, “What are the key market trends impacting the growth of the automotive lightweight material market?” in Market Watch, July 16, 2020. Available: https://www.marketwatch.com/press-release/what-are-the-key-market-trends-impacting-the-growth-of-the-automotive-lightweight-material-market-2020-07-16. Accessed July 18, 2020.
[2] L. Thegel and E. Wadman, “Non-ferrous metal thickness gauges”, ABB Review, 1/2017, pp. 40–45.
[3] ABB, Measure IT Pulsed Eddy Current technology: Operating Principle, Automation Technologies, 2004-05, pp. 1–6.
[4] ABB, Millmate thickness gauging systems; imagine outstanding dependability, ABB AB Industrial Automation, 2020, pp. 1-11. Available: www.abb.com/thicknessgauging