The United States recently established lofty goals to reduce greenhouse gas pollution. With the technology available today, manufacturers can help the country achieve these goals and improve the sustainability of our own businesses at the same time.
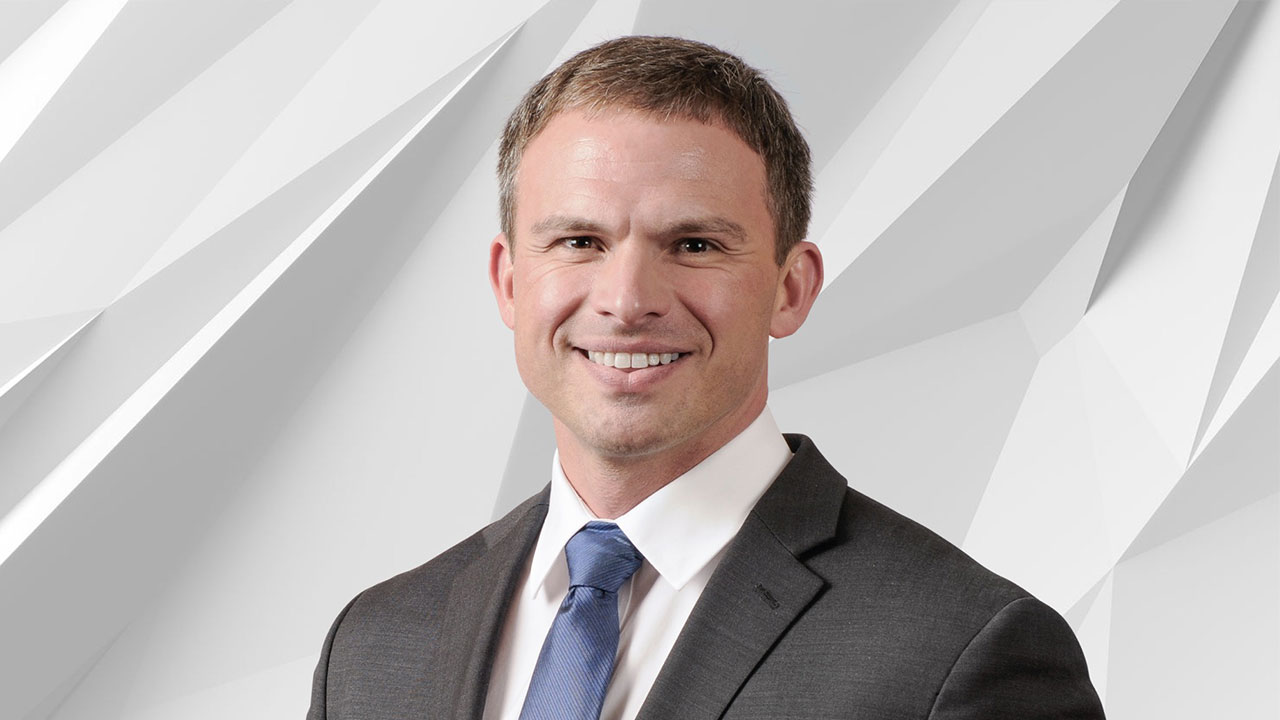
Did you know?
- Motors consume almost 70% of the electricity used in the US manufacturing sector.
- On average, a US manufacturing facility uses 9.5 kWh of electricity per square foot, with an average industrial electricity cost of 6.8 cents per kWh.
- More than 92% of the lifetime cost of an electric motor is the cost of electricity to run it.
- Electric motors, well maintained and kept in clean, dry facilities, can operate for more than 20 years,
Variable speed drives control the speed of the motor. It's not uncommon to oversize a motor in order to meet the highest anticipated load, however, in many applications (especially pumps, fans, and compressors) the full load of the motor is not always required. Adding a drive to a motor-driven pump, fan, or compressor to control the motor speed can typically reduce power consumption by 25%.
Today's highly efficient motors have taken us leaps and bounds beyond NEMA super-premium and IEC IE3 efficiency levels. Today's generation of variable speed motors, based on innovative designs and materials, can now operate up to IE6 levels, efficiencies never before imagined by, let alone available to, industrial operations.
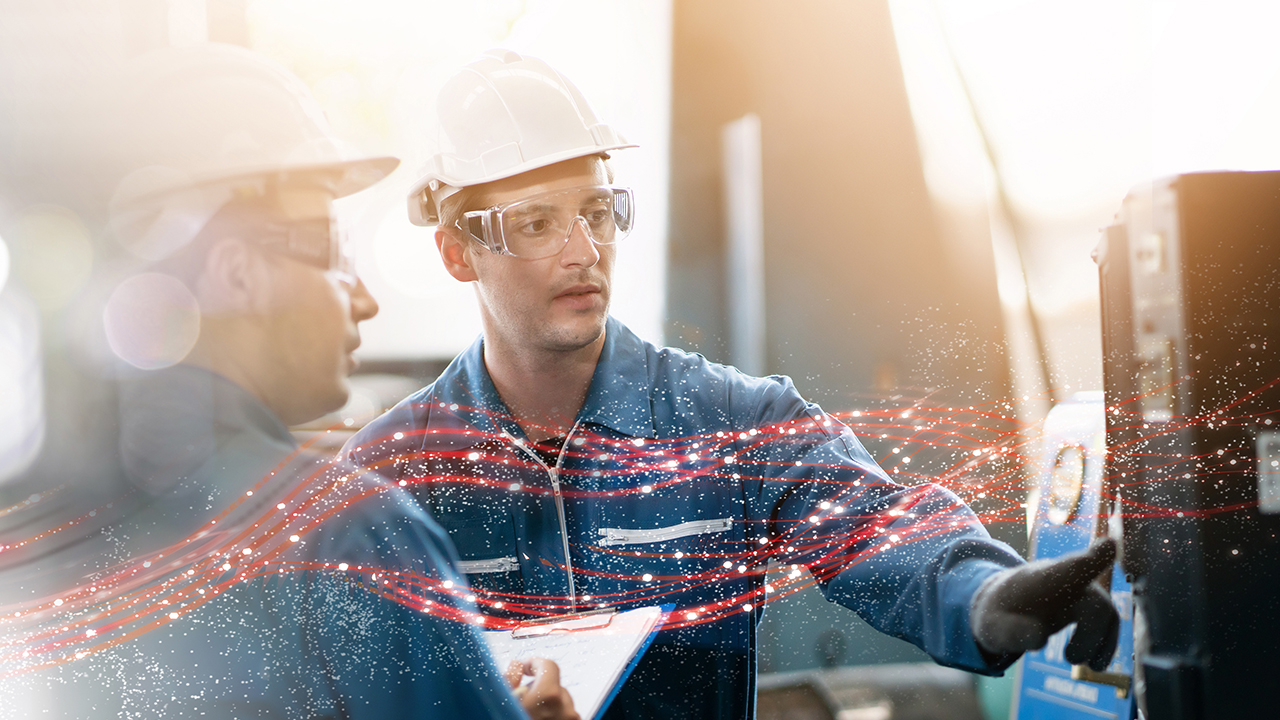
Given these technologies, there are 3 simple ways manufacturers can reduce electricity consumption today:
- Turn off equipment that is idle or doesn't need to run full-time. The fastest way to save on electricity is to not use it at all. Turning off equipment will not only reduce your electricity bill, but it may also extend the life of the equipment itself.
- Use only the amount of electricity you need to get the job done. By applying a drive to the motor-driven equipment, you only use the amount of electricity you actually need. It is estimated that 50% of motor-driven applications would benefit from the use of a variable speed drive. Roughly 25% of the installed base current uses a drive, so we have the opportunity to double the use of drives in manufacturing processes.
- Upgrade installed motors to new, more highly efficient versions. A motor built prior to 1990 is likely to run at 87% efficiency or less. Today's highly efficient motors run at efficiencies closer to 96%. It is estimated that taking out an operating motor and upgrading to a new highly efficient motor can have a payback period of as little as 6 to 24 months.
Energy efficiency is good for our customers, our employees, and our communities. By choosing to invest in existing technologies and reducing the amount of electricity we consume today, US manufacturers can immediately be part of the solution to create a more sustainable environment tomorrow.
Article by:
Smart Industry
Read the original article here