Marc Mustard Content & Robotics Manchester, UK, marc.mustard@gb.abb.com
Robots are on the move. Once fenced off from workers, they are increasingly migrating into the comparatively open spaces →01 – 02 that characterize small- to mid-scale manufacturing environments, collaborating with humans in material handling, machine tending, and component assembly, and offering welcome support in laboratories →03, logistics centers, warehouses, and workshops.
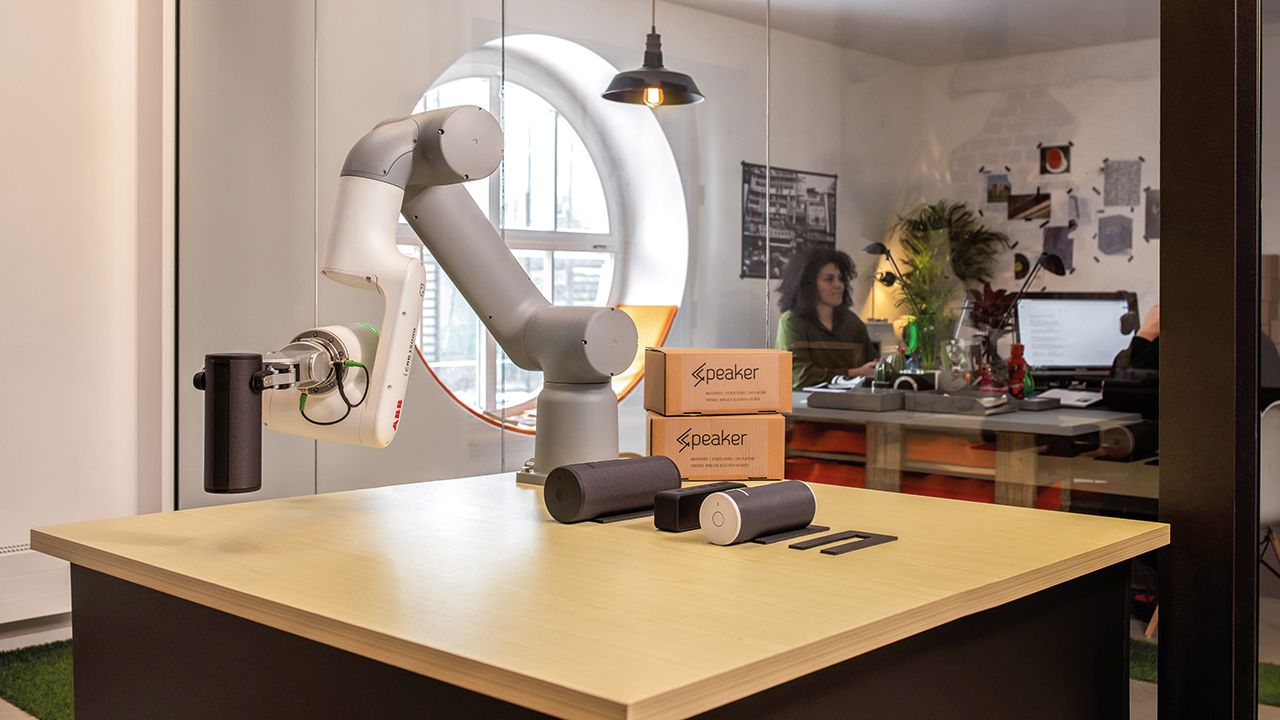
Essentially robots designed to operate in the presence of human workers without the need for safety measures such as fences, this new class of helpers known as cobots supports businesses as they struggle to recruit and retain staff for a wide range of dull, dirty, repetitive, dangerous, or ergonomically challenging tasks. Indeed, according to a 2020 McKinsey report on the Future of work [1], Europe may face a shortage of workers as the economy recovers following the Covid-19 crisis: “Europe’s working-age population will likely shrink by 13.5 million (or 4 percent) due to aging by 2030,” says the report.
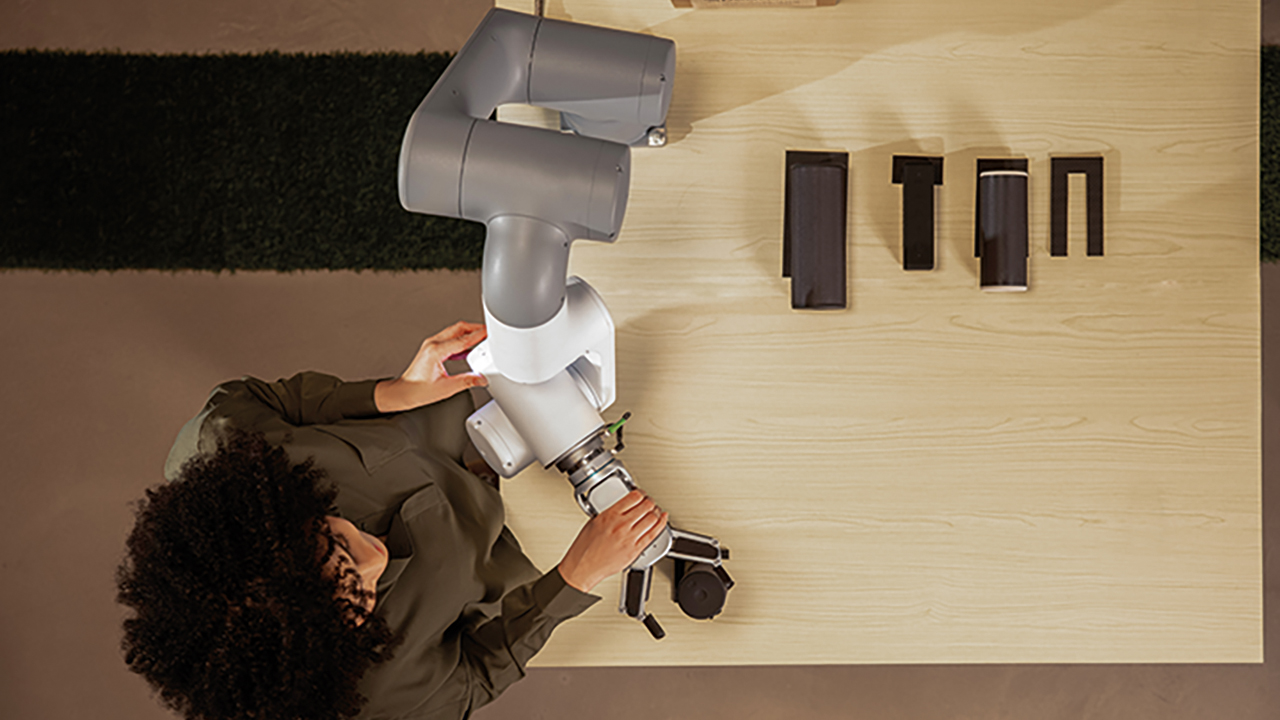
Bot benefits
For businesses, automating processes without requiring physical fencing not only reduces the overall cost of an installation, it saves space and creates a more open work environment. This allows people to carry out their tasks freely, and minimizes interruptions caused by having to physically stop and restart production to access a robot.
Installing robots can also help a business to reduce its operating costs, improve product quality and consistency, enhance production output and manufacturing flexibility, and improve the use of facilities. As well as helping managers to offset labor shortages, automation can improve workplace health and safety because robots support workers with heavy lifting and repetitive tasks.
Adding automation to a process or production line has also been shown to improve job satisfaction, with employees able to upskill and focus on value-added and more rewarding tasks.
In view of these trends, ABB recently expanded its collaborative robot portfolio with the introduction of GoFa™ and SWIFTI™, which complement its YuMi® and Single Arm YuMi® industry-leading cobot line-up.
GoFa™ – the go-anywhere cobot
Capable of handling a payload of up to 5 kg and operating at 2.2 meters per second, which is significantly faster than other cobots in its class, GoFa →04 can perform more operations in a set period than competing cobots. These capabilities make it ideal for assembly or picking-and-packaging tasks where items need to be quickly and accurately transferred from place to place. GoFa’s performance is further enhanced by its micron-level positioning repeatability, allowing objects to be precisely picked, moved and placed time after time.
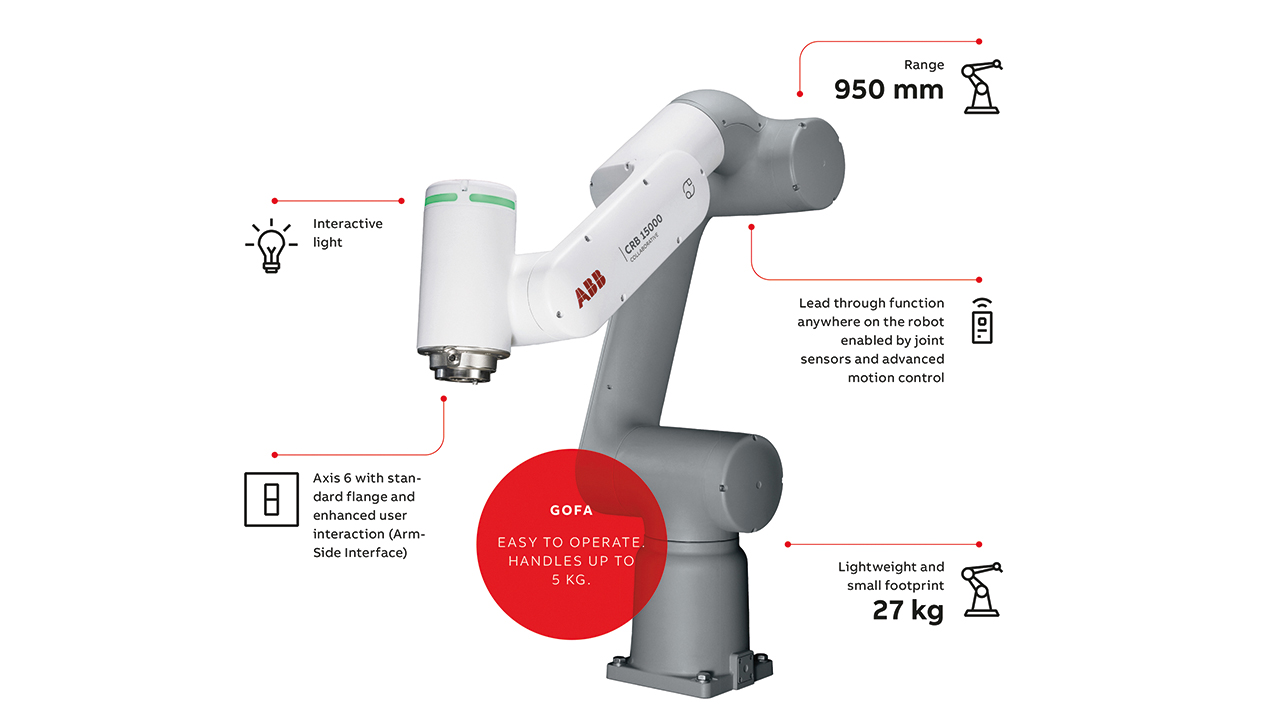
Furthermore, at 950 mm, GoFa’s reach outperforms other 5 kg cobots by around 12 percent. And with a 70 percent longer reach than ABB’s YuMi single arm robot, GoFa can help to reduce the number of cobots that may be needed in a single space.
GoFa incorporates a passive safety system, enabling it to work alongside humans without any safety barriers. Integrated torque and positioning sensors in each of its six joints allow GoFa to come to a complete stop in milliseconds if it comes into contact with a human.
And GoFa can go wherever it is needed. Weighing a manageable 27 kg, with a footprint of just 165 mm2 and able to be mounted in any direction, GoFa, like ABB’s YuMi and Single Arm YuMi, offers the flexibility to be used when and where it is needed, to support short-term process changes, or to fill gaps in production lines wherever and whenever needed. These capabilities give users the flexibility to quickly adapt to changing circumstances or customer demands.
GoFa is designed to work with ABB’s OmniCore robot controller family. Offering high levels of flexibility, connectivity and performance, OmniCore features a 50 percent reduction in footprint compared with previous robot controllers, together with best-in-class motion control and path accuracy. OmniCore can be easily integrated with the latest digital production technologies, including a wide variety of fieldbuses, advanced vision systems and force control.
SWIFTI: high-speed partner
Substantially faster than GoFa, SWIFTI →05 is a collaborative industrial robot aimed at tasks such as assembly and polishing. Capable of speeds exceeding five meters per second, which is five times faster than most other machines in its class, SWIFTI is designed for intermittent collaboration with humans while handling a payload of up to 4 kg. SWIFTI is equipped with an active safety system, which is based on a laser scanner. If a human worker approaches, for example to load, unload or reposition parts, SWIFTI slows and stops, then automatically restarts as the person exits the robot’s sensory safety zone, allowing production to resume as quickly as possible.
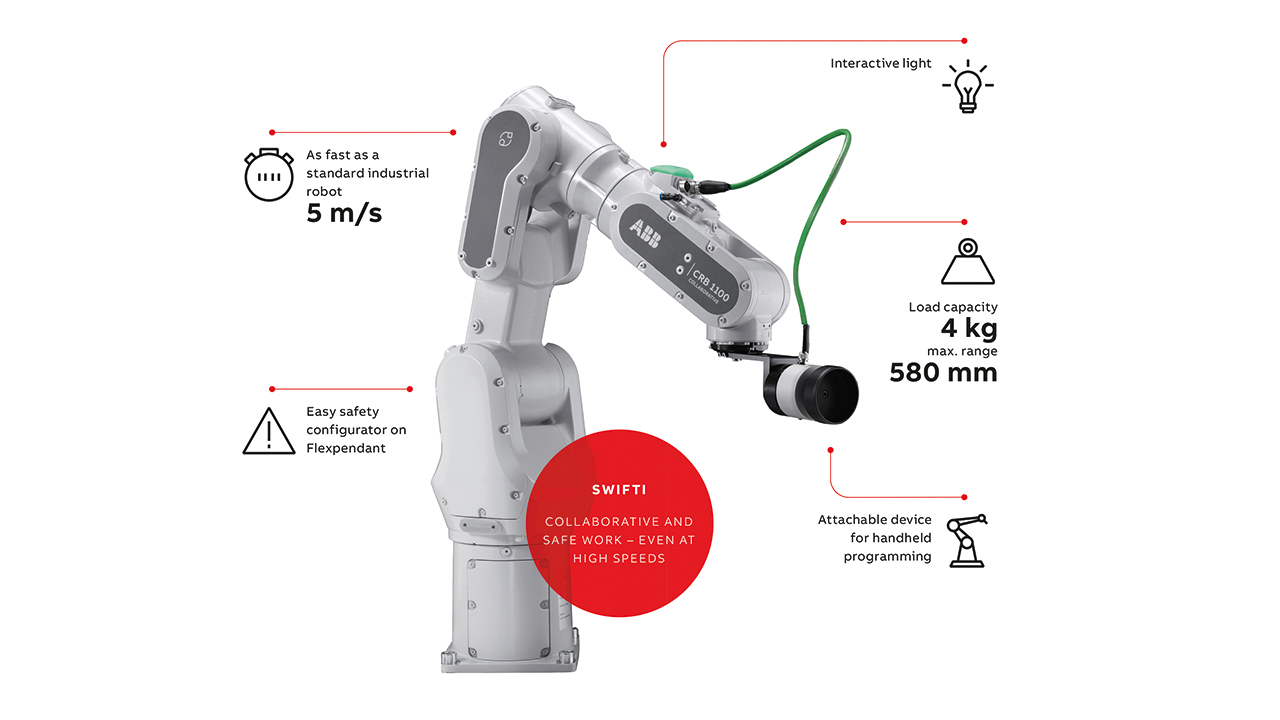
Designed specifically to close the gap between collaborative and industrial robots, SWIFTI addresses many of the barriers that have prevented companies from fully realizing the potential benefits of robotic automation. By coupling the safety features and ease of use and installation of a collaborative robot with the high speed, precision, performance, and compact design of ABB’s IRB 1100 industrial robot, SWIFTI provides the best of both worlds. With collaborative safety, speed and accuracy on a par with an industrial robot, it will help companies transform their productivity by enabling greater cooperation between their robotic and human workers across a wide range of applications.
Another SWIFTI advantage is that it can be used with the same tooling as a standard IRB 1100 industrial robot, thus opening the door to cost savings. An example is the inclusion of a vacuum pack, which features four integrated air supplies that can be used to enable simultaneous picking of multiple items using suction. Normally used on ABB’s IRB 1100 industrial robots, the same vacuum pack can be fitted to SWIFTI to offer identical functionality with no need for modifications.
In addition, since SWIFTI uses the same platform as the IRB 1100, it provides the ideal solution for applications such as loading and unloading, assembly where workers intermittently need to operate in the same workspace as a robot, as well as kitting, materials handling, screwdriving, insertion and polishing tasks.
Painless programming
Although GoFa and SWIFTI are highly sophisticated machines, operators do not need to learn complex programming languages to train them. Lead-through programming anywhere on the cobots’ arms allows users to move the machines into various positions to create tailored programs using ABB’s Wizard drag and drop easy-programming software. With Wizard, the programming process is reduced to simply dragging and dropping graphical blocks on an ABB FlexPendant screen →06. This allows the user to see the results immediately and adjust a cobot’s actions as needed. By linking these blocks, complete programs can be assembled for a wide range of applications.
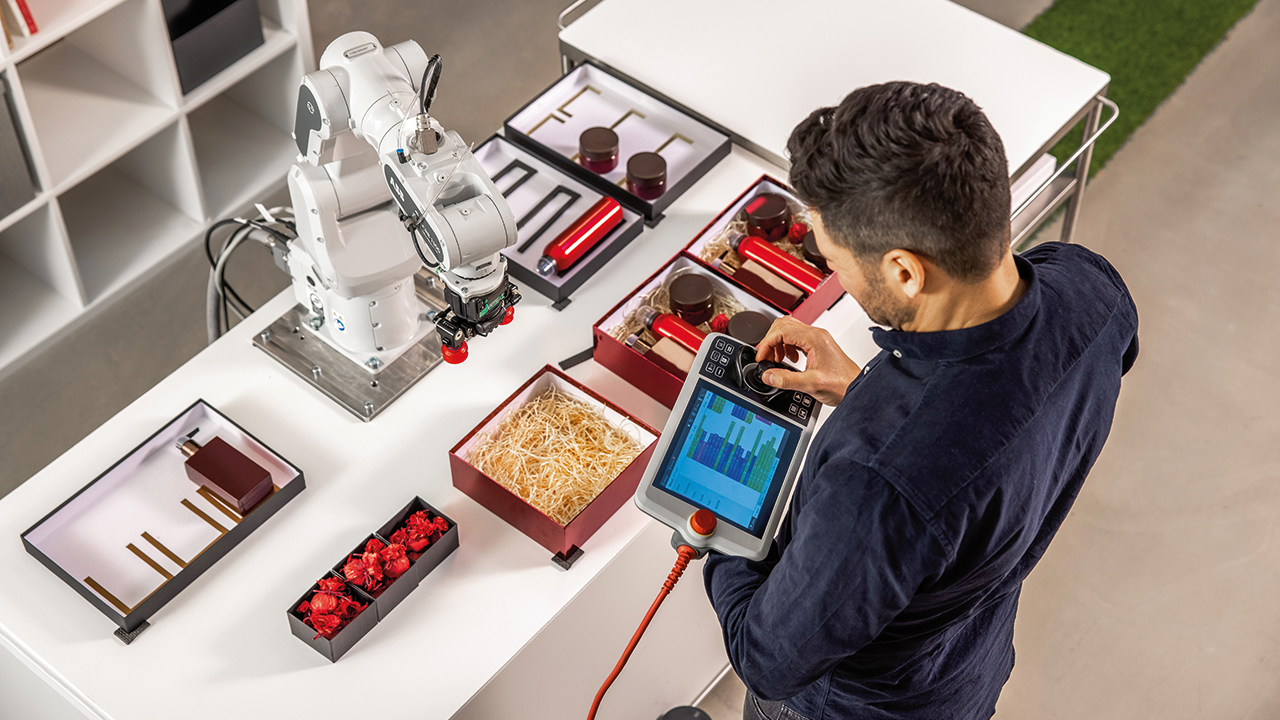
For companies with more specialized programming needs, new blocks can be created to perform specific tasks. This is achieved through ABB’s Skill Creator software, which can turn standard RAPID programming routines into Wizard blocks and make them ready for use by non-programmers. The custom blocks, known as skills, can be produced to control grippers or create actions for specific applications such as laboratory automation.
Users can also use RobotStudio®, ABB’s simulation and offline programming software. This is the industry’s leading PC-based solution for programming, configuration, and virtual commissioning before installation. In addition, when preparing SWIFTI for service, users can establish safe working zones with SafeMove Visualizer, which puts safety configurations directly onto the ABB FlexPendant.
References
[1] McKinsey, The Future of Work in Europe, 2020, page iv. Available: https://www.mckinsey.com/~/media/McKinsey/Featured Insights/Future
ofOrganizations/ThefutureofworkinEurope/MGI-The-future-of-work-in-Europe-discussion-paper.pdf [Accessed May 22, 2021].
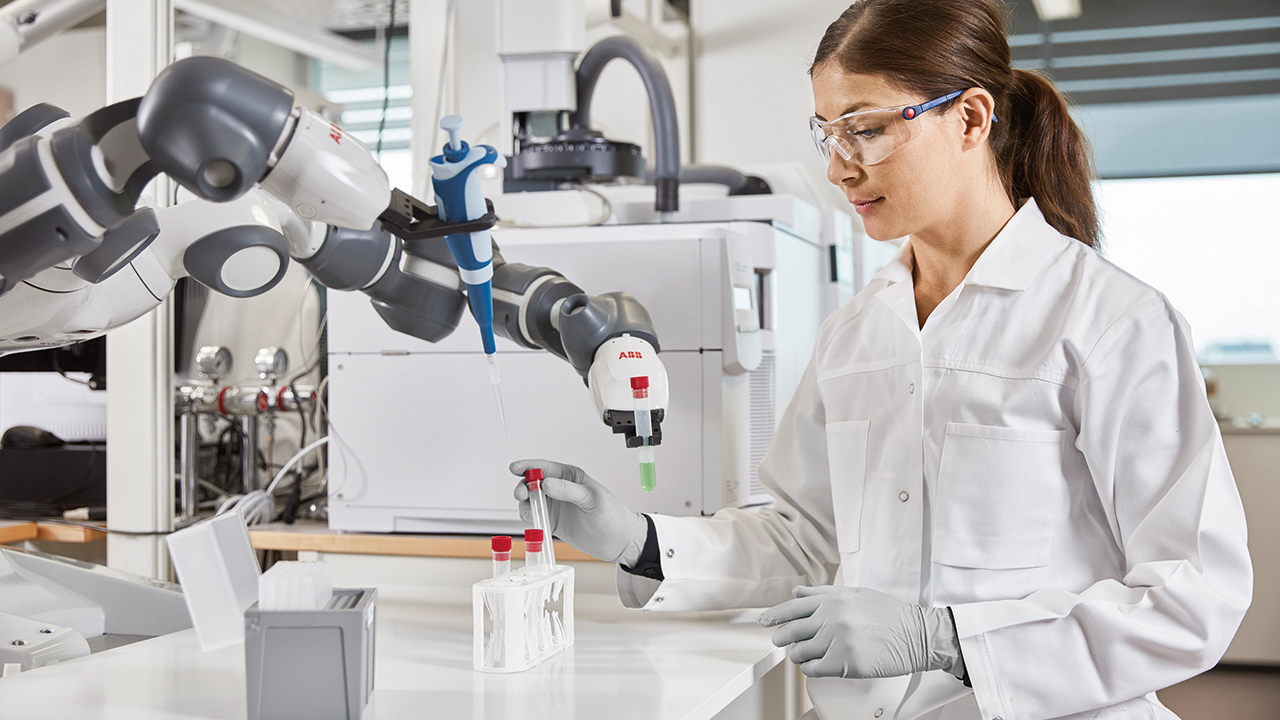
A cobot for lab technicians
At Sweden’s Karolinska University Hospital, adding an ABB collaborative robot to the laboratory team to take over laborious manual tasks has created a better working environment and increased efficiency [1].
Robot solutions are nothing new in healthcare. As pressure grows across the healthcare sector, from vaccine development and testing to patient care, the search has intensified for new ways to utilize robots to fill gaps in production capacity and staff availability.
With its own dedicated innovation center, Karolinska University Hospital in Sweden has been searching for ways to provide improved levels of performance through automation.
Working in collaboration with various organizations, including ABB, the hospital has been exploring ways to use robotic technology in areas ranging from surgery and pediatric care to transporting instruments, laundry, and food.
One area where automation has been deployed is the Karolinska University Laboratory. The lab processes millions of medical samples every year, and although fixed sorting automation helps to handle the large volumes, it was clear that many manual steps involving laborious repetitive tasks might benefit from robot assistants. One such area is scanning test tubes and opening transport sleeves. Today, thanks to an ABB collaborative robot that has taken over this function, lab technicians have been freed from this monotonous and exhausting task, resulting in reduced strain on wrists, improved workflows, and greater efficiency.
References
[1] ABB, ABB’s collaborative robot at Karolinska University Laboratory, November 12, 2020. Available: https://new.abb.com/news/detail/70465/abbs-collaborative-robot-at-karolinska-university-laboratory laboratory [Accessed May 19, 2021]. — 03 ABB is exploring ways to use robotic technology to support hospitals and their staffs. — 04 Weighing only 27 kg, GoFa can go wherever it is needed. — 05 SWIFTI is designed to close the gap between collaborative and industrial robots. — 06 Programming is as simple as dragging and dropping blocks on the screen of an ABB FlexPendant.