Ondrej Frantisek, Sebastian Breisch ABB Process Automation, Corporate Research, Ladenburg, Germany, sebastian.breisch@de.abb.com, ondrej.frantisek@de.abb.com; Alessandro Stucchi ABB SpA Dalmine, Italy, alessandro.stucchi@it.abb.com
Multibody simulation is a tool for the analysis of motion and forces in mechanical systems →01. Often confused with the finite element method (FEM), multibody methodology provides information on motion and forces, whereas the FEM deals with deformation and strength. A basic slider-crank mechanism – as found in the internal combustion engine – transforms the rotation of a motor’s crank into a vertical movement of the piston and thus provides a simple example of a multibody system. For given loads, multibody simulation can evaluate the motion of this system and all the reaction forces in the joints. Conversely, the simulation can also tell how loads react to a given motion.
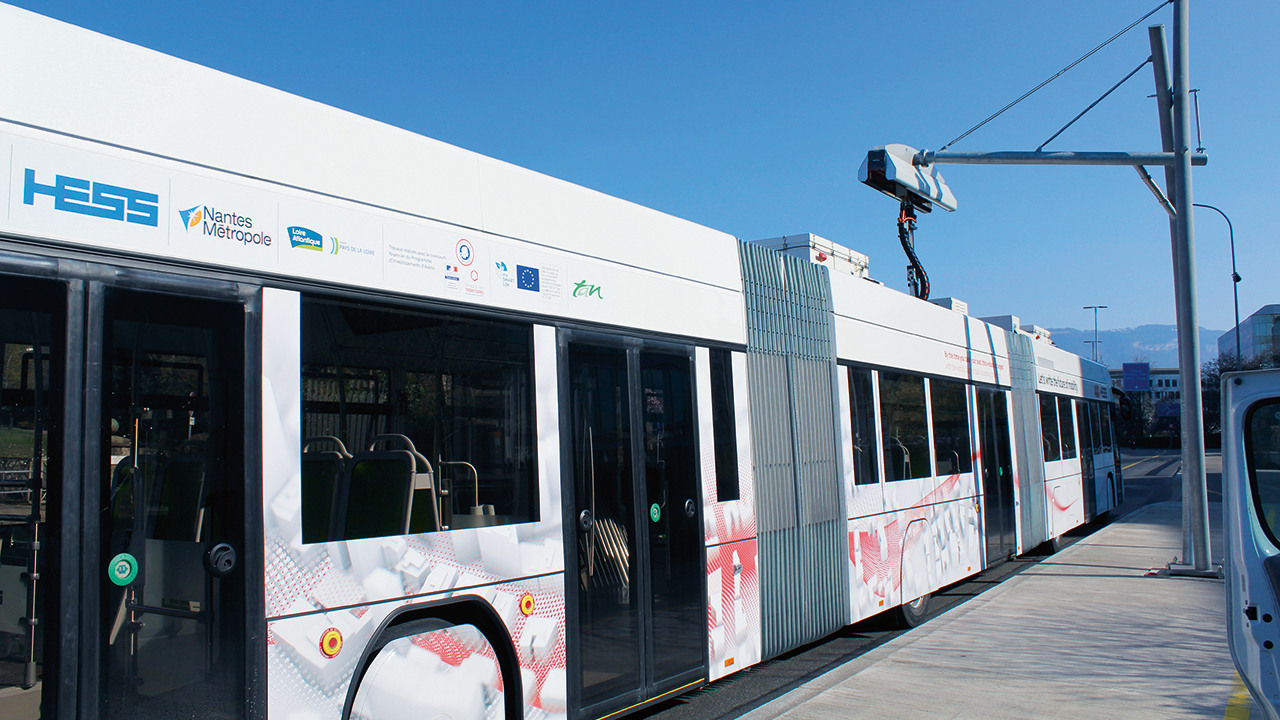
Moreover, the mechanism model can be built parametrically and the influence of these parameters on system dynamics can be investigated →02. This feature is vital in the first stages of product development, in which different dimensions of mechanism are simulated until the required performance is reached. Later in the development, parametric analysis is used to define the influence of production and assembly tolerances and, thus, answer the critical question: “will the mechanism perform as required even with the imperfections introduced during production?”
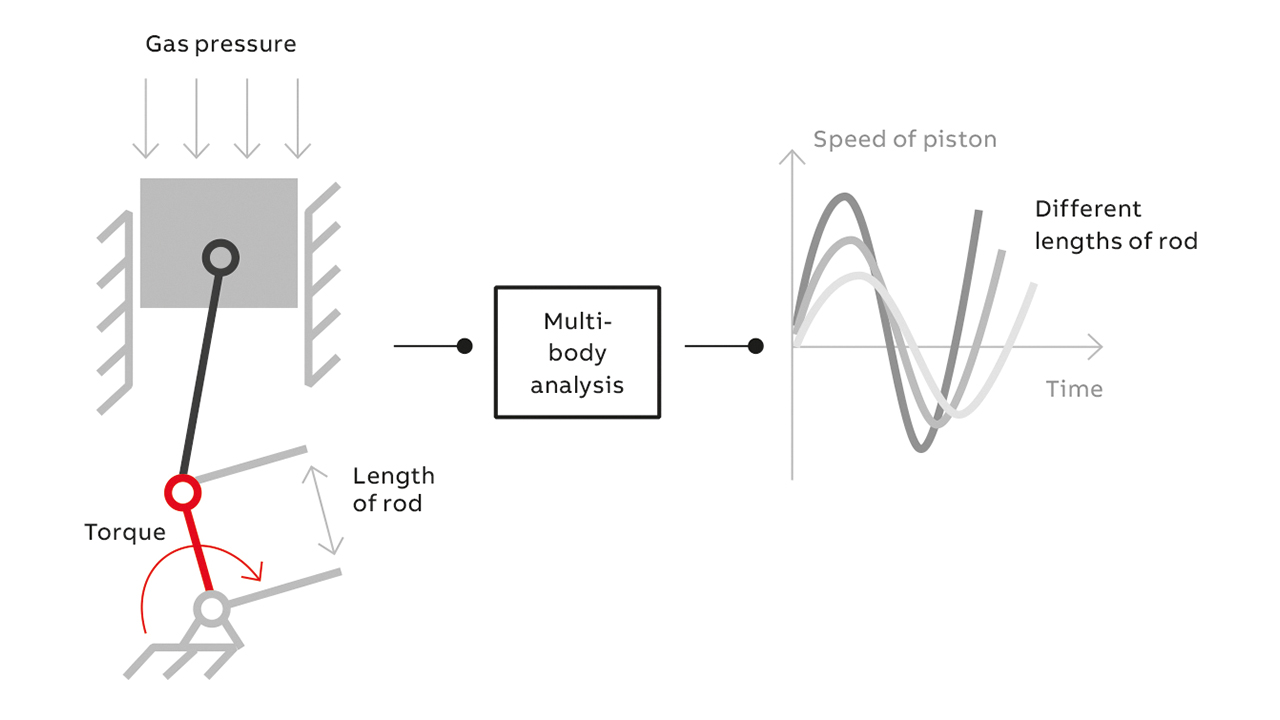
A very important – and usually unavoidable – mechanical parameter studied using multibody simulation is play in joints. Play often has a significant influence on product performance and, because of its nonlinearity, cannot be modeled by simple analytics.
So far, the assumption was made that the mechanism’s links were rigid – ie, they cannot deform. So, what about the deformation and strength of mechanical links? Nowadays, multibody tools can describe well the behavior of mechanisms with flexible parts – if the parts are simple. More complicated parts yield less precise results, so FEM tools must be deployed if precise deformation or strength information is sought. FEM set-up and simulation can be expensive and time-consuming, but there is a smart and fast option: Simulate the mechanism in a multibody tool and simulate only the critical part in the FEM tool, with input from the multibody simulation.
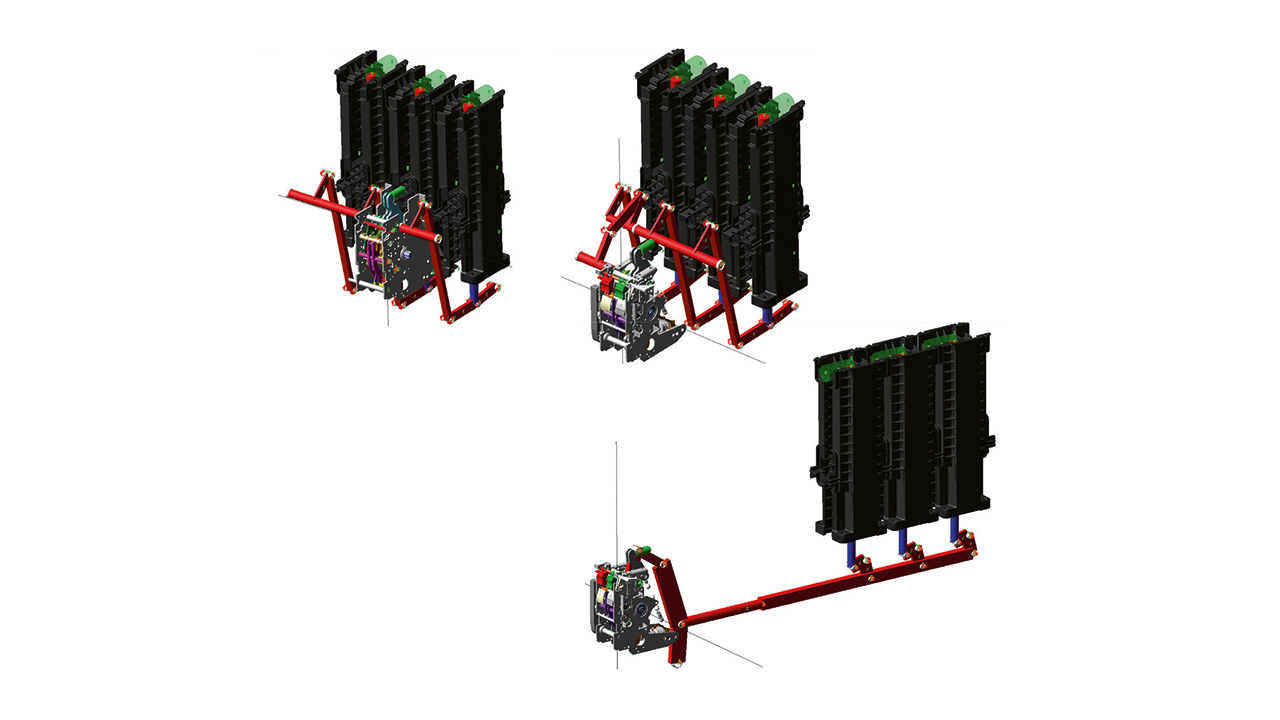
Circuit-breaker design is one area where ABB puts multibody simulation to good use. Circuit breakers are very complex mechanical systems that can be described by analytic formulas only in a limited way. A multibody tool is a must if the dynamics of such a complex system need to be analyzed →03. Using a multibody tool, it was possible to compare three circuit-breaker topologies within two months. Without the tool, three demonstrators would have had to be built – a costly and lengthy process.
Multibody simulation tools provide valuable support during the development of complicated mechanical systems. The tools accelerate the development process significantly and help avoid any unpleasant surprises during production by characterizing the influence of production tolerances.