- ABB’s swift action and reliable support helped in tackling a challenging situation at Xianglu Petrochemicals Zhangzhou’s plant in China.
- The plant reported an outage, after one of the drives tripped due to power fault.
- The situation could have resulted in the company facing a damage of $150k in waste and additionally more, due to cleaning and overall downtime.
Xianglu Petrochemicals Zhangzhou refines and distributes petrochemical products and operates one of China’s biggest petrochemical plants located in eastern Fujian. It produces benzenes, liquefied petroleum gases, and other products.
Condition monitoring, remote support and urgent spare part delivery prevent expensive downtime
Despite the hurdles posed by the COVID-19 outbreak in China, which led to a total shutdown, ABB’s service experts were quick in action and prevented costly downtime for the customer, by providing remote support and facilitating urgent spare part delivery.
For Xianglu Petrochemicals Zhangzhou, three ACS1000 variable speed drives at the Fujian plant play a key role in stirring petrochemical materials. The ACS1000 has been designed as a standard product, using advanced, yet proven motor control technology – known as Direct Torque Control (DTC) - and advanced power semiconductor technology which increases reliability and helps minimize the drives’ footprint. Together with ABB Ability™ Condition Monitoring, the drives enhance the petrochemical mixer’s performance and improve productivity.
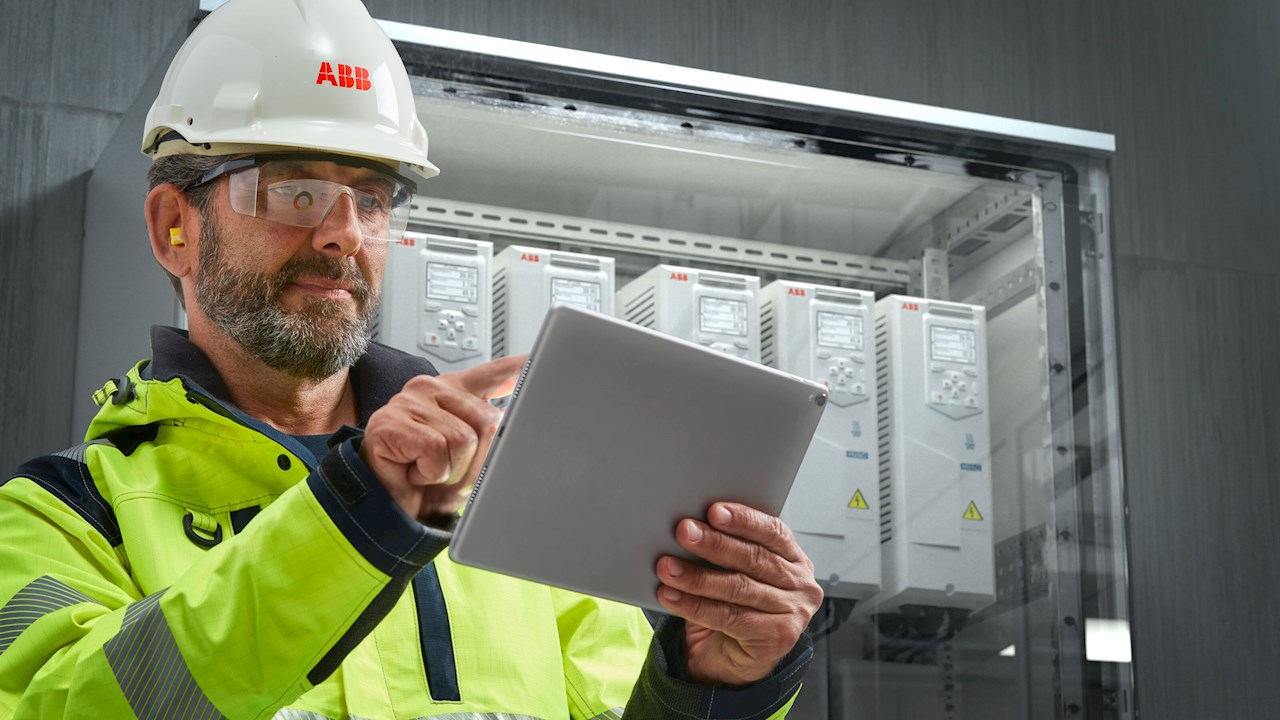
If the downtime of these drives exceeds more than 24 hours, the raw material in the mixer will solidify, impacting the production process. The solidified material must be cleared manually before the mixer can resume production. The customer will have to then clean the mixer, potentially facing a damage of $150k only in waste, but even more so because of the stopped production time.
Part of their running tailored service agreement, Xianglu Petrochemicals Zhangzhou had benefitted since May 2018 of ABB Ability™ Condition Monitoring for drives for their three ACS1000 variable speed drives. ABB Ability™ Condition Monitoring is collecting all the data of the drive performance, enabling monitoring availability, condition, operating parameters, and fault events.
“ABB Ability™ Condition Monitoring for drives is able to monitor the data in real-time. When the drive malfunctions, ABB engineers will instantly receive the fault notification, and they can contact the customer to resolve the problem on site or remote.” said Zhixin Deng, ABB Motion Services Local Division Manager, China
Looking at the data provided by condition monitoring, the ABB experts tracked down the faulty drive that tripped due to a power outage and confirmed the incident at the site with the Chinese refiner. A group of service experts were assigned to deal with the case, which assessed further that the output filter capacitors could have failed. The plant operators helped to measure the capacitor on site and confirmed the failure. The ABB experts were quick in identifying and sourcing the spare parts needed to solve the problem within a turnaround time of only four hours.
Without wasting time, ABB deployed the required capacitors at the Xianglu Petrochemicals Zhangzhou’s plant. After the successful replacement, the drive was back in operation.
“Thanks to ABB’s swift response and support, Xianglu Petrochemicals Zhangzhou decided to continue their ABB Ability™ Condition Monitoring for drives subscription and prevent future malfunction by replacing the same capacitors in the other two drives at its facility. This is a great example of how we have become a trusted service partner for our customers, who approach us for reliable and quality services,” concluded Zhixin Deng, ABB Motion Services Local Division Manager, China.