Although simulation technology is nothing new, it has historically relied on relatively small data sets when making predictions. But with ABB’s Ability™Stockyard Management System (SYMS), which is essentially a digital twin of afacility, operators have access to unfathomably large data sets that allow the customer to combine each cubic meter of material processed with information regarding material quality and location as well as energy consumption in realtime. The result is a technology that has become a business imperative in materials handling and process industries– a vast improvement over competing “boutique” software applications.
Andre Herzog ABB Process Industries / Digital Material Handling in Mining Cottbus, Germany
Andre Herzog holds an advanced degree in electrical engineering. Before joining ABB in 2009, he worked at GE and KSB in senior project management and business development. Today, Andre is product manager, Digital Material Handling for ABB and is responsible for digital applications that optimize materials handling primarily for stockyard operations.
AR How does ABB’s Ability™ Stockyard Management System complement the company’s other customer solutions?
AH ABB has been involved in stockyard management since approximately 2000 when it developed a customized solution for blending different types of coal. From the beginning, the idea was to have a software system that would be an enabler for automation and electrification and that would complement our expertise in managing huge machines, excavators, and stacker/reclaimers. Over the years, ABB reached a whole new level of this technology through its Stockyard Management System (SYMS). Today, the company offers many capabilities that go far beyond blending products for power plants. Its offering now serves not only the mining sector, but also steel foundries, cement producers, fertilizer producers and even port operators. Many customers use SYMS hand in hand with their manufacturing execution systems (MES). This puts ABB in a position to not only provide automation expertise, but expertise in operations management and instrumentation.
AR How does the ABB Ability™ Stockyard Management System compare with competing systems in terms of customer benefits?
AH ABB’s unique selling point is that, rather than looking at an operation in terms of individual machines, it provides a digital twin of an entire bulk yard operation – even for customers who have several sites. Our perspective is tailored mainly to customers who plan to optimize their bulk yard utilization as well as their materials’ quality. We also address customers who are investing in fully automated and / or remotely operated stockyards.
Such customers have two options. They can turn to ‘boutique’ software that only monitors what automated systems are doing and estimates the quantities of raw materials at hand, or they can come to ABB and get the most accurate and validated digital twin of their facility – a digital twin, by the way, that can be upgraded to autonomous machine operation.
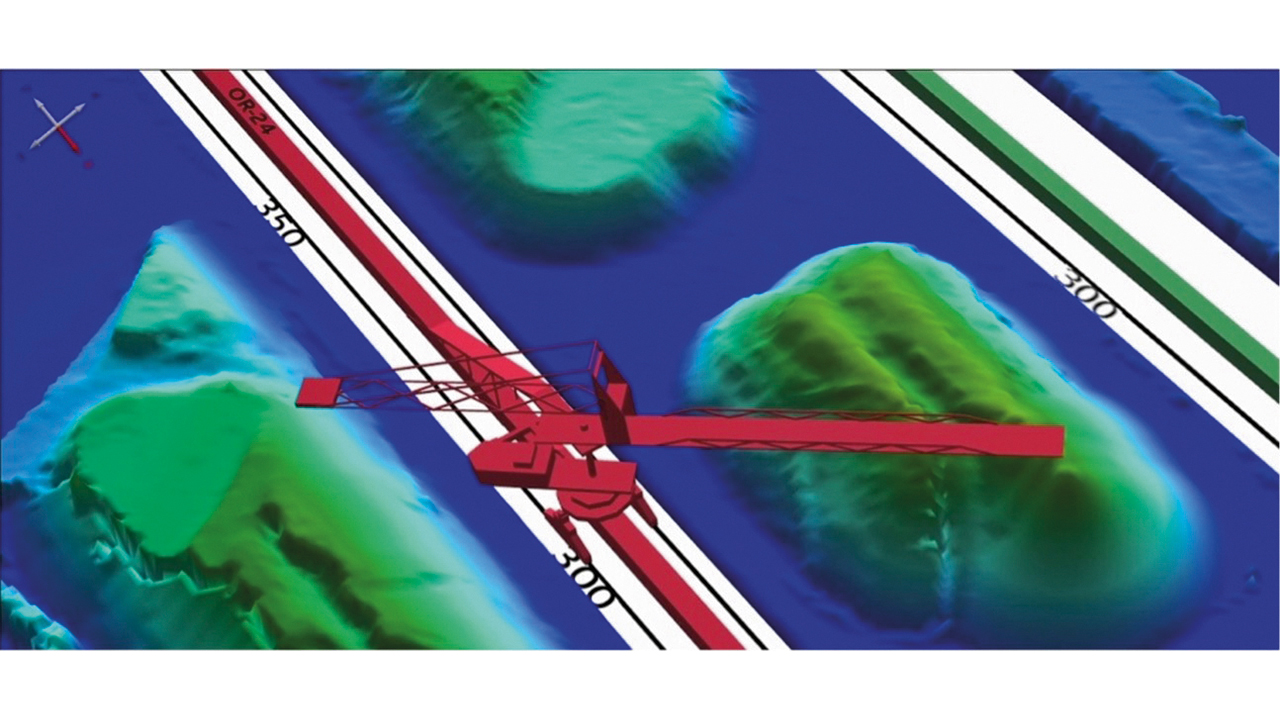
SYMS calculates everything to each cubic meter using a cuboid model and connects this with data generated by connected instrumentation such as, for instance, a highly customized laser scanner. These two data sets are compared, resulting in a high level of accuracy. It is the difference between a checks-and-balances system and a blurry estimate. In addition, with ABB’s solution, the customer can combine each cubic meter with information such as quality of material and energy consumption in real time.
AR Quantifying the energy demand represented by each ton or cubic meter must involve tracking the individual and collective operational efficiency of many machines in real time. Is that what SYMS does?
AH The software is able to track how much energy is needed to move materials around a stockyard. In addition, ABB’s Performance Analyzer can evaluate the efficiency of all the machines at a site. If a machine begins operating below its specs, Maintenance is alerted. The software is autonomous-operations-ready, which means that if the user decides to run machines autonomously, they do not need new software, only some add-ons. This is a huge advantage that will become available this year. New sites will have the option of being fully autonomous from day one. Older sites will be able to upgrade to a level where a computer system runs machinery instead of a person.
AR As increasing levels of stockyard autonomy are reached, can operators expect to see maintenance costs decline?
AH ABB’s autonomous system takes very good care of machines and their movements. Keep in mind that an operator may be handling a $20 million machine, so if he or she has a bad day then the company and its owners may have a bad year. SYMS makes machine movements much smoother and if it recognizes danger a whole sequence of movements will be stopped.
In addition, with ABB Ability™ Performance Optimization, which we mentioned earlier, we can track and evaluate each machine’s operations from a historical perspective. The resulting data allows operators to identify a machine that is not working as it should be. This gives a stockyard a huge advantage because it is like having a doctor constantly tracking patients’ vital signs. KPIs are set and tracked in the Stockyard Management System environment. Furthermore, as more and more historical information is developed, operators will be able to make predictions that support future planning from different perspectives.
AR Speaking of planning, where does ABB’s ‘digital twin’ fit in?
AH ABB’s Stockyard Management System is, in essence, a digital twin of a stockyard. It is an evolving digital profile of the historical and current behavior of a facility and its processes that is based on massive, cumulative, real-time, real-world data measurements across an array of dimensions, all of which is designed to optimize business performance.
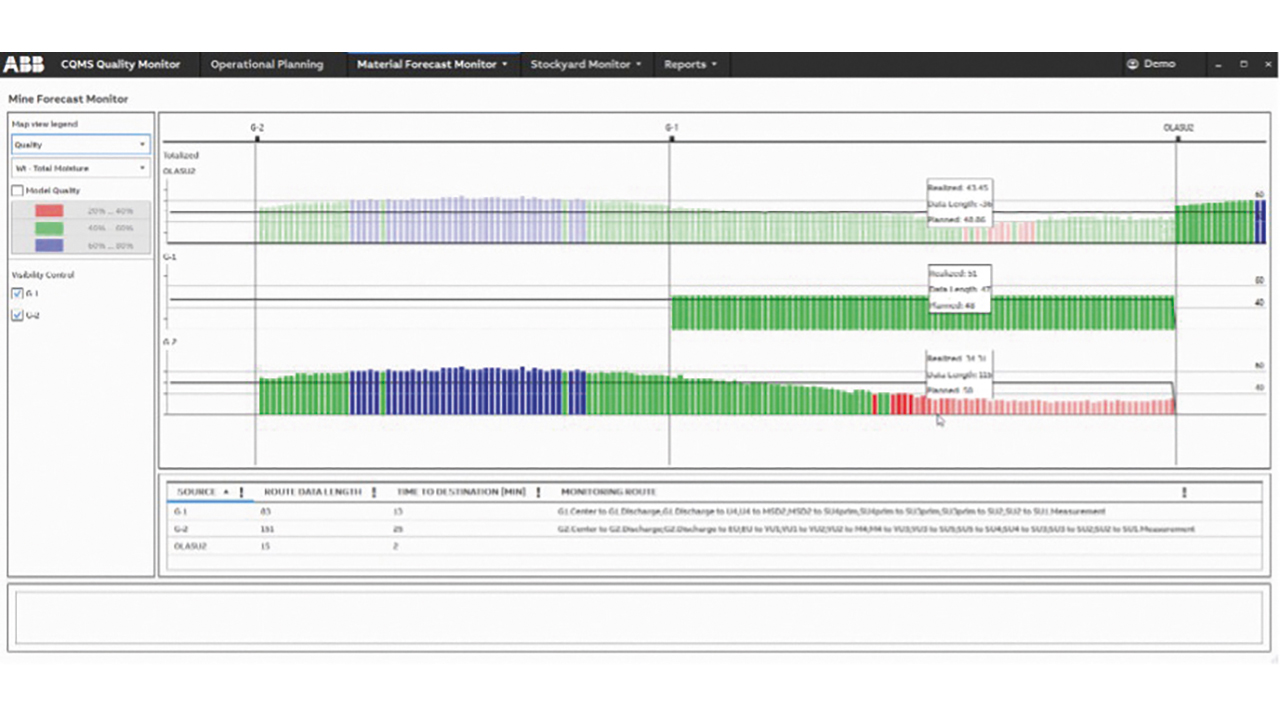
Data stored in different places can be referred to from one common digital twin directory to perform real-time optimization, prevent downtime and plan for the future by using simulations. While simulations are nothing new, they have historically relied on relatively small data sets or assumptions when making predictions. Digital twins, however, have access to unfathomably large data sets thanks to the Industrial Internet of Things (IIoT). They have become a business imperative in the material handling and process industries, including mining and metals.
AR Do you plan to integrate SYMS with upstream or downstream partners?
AH Yes. We develop interfaces where, for example, if there is a rail company and it needs to hand over data, SYMS can provide an interface that connects this information with any vendor. It depends on the project, but we are able to pick up this information and integrate it into the SYMS database. We recently spoke with a European customer that operates multiple stockyards and receives data from different sources – by truck, train, and ship. Thanks to SYMS, we will be able to coordinate this data through a specialized menu that will interconnect the data from several digital logistics solutions.
AR Let us talk for a moment about user experience and digitization. What is ABB doing to simplify the operator’s job?
AH In Asia, for example, we have a customer that was, until recently, filling out nearly 2,000 pages of forms for every vessel unloaded. Now, they can do almost everything digitally. We have made a huge impact on the digitization of their day-to-day operating routines. When it comes to dashboards and reporting, we are improving everything with a view to creating a more user-friendly experience. We have improved our whole reporting system for customers. Everything can be configurated and customized to meet a customer organization’s specific needs.
AR How far are we from fully autonomous operations in the mining and metals area?
AH We have one pilot stockyard that will probably enter fully autonomous operations by the end of this year.